222 S Oakley Progress
06/16/25
We are largely wrapped up as of today! The intercom and security system that Bryan designed has been installed and looks very slick. And sod, backsplash tiles, glass railings and garage doors have been installed. We used a 3D printer to create beauty covers as needed throughout the project — pictured here is a vanity drawer modified to accommodate the drain piping.
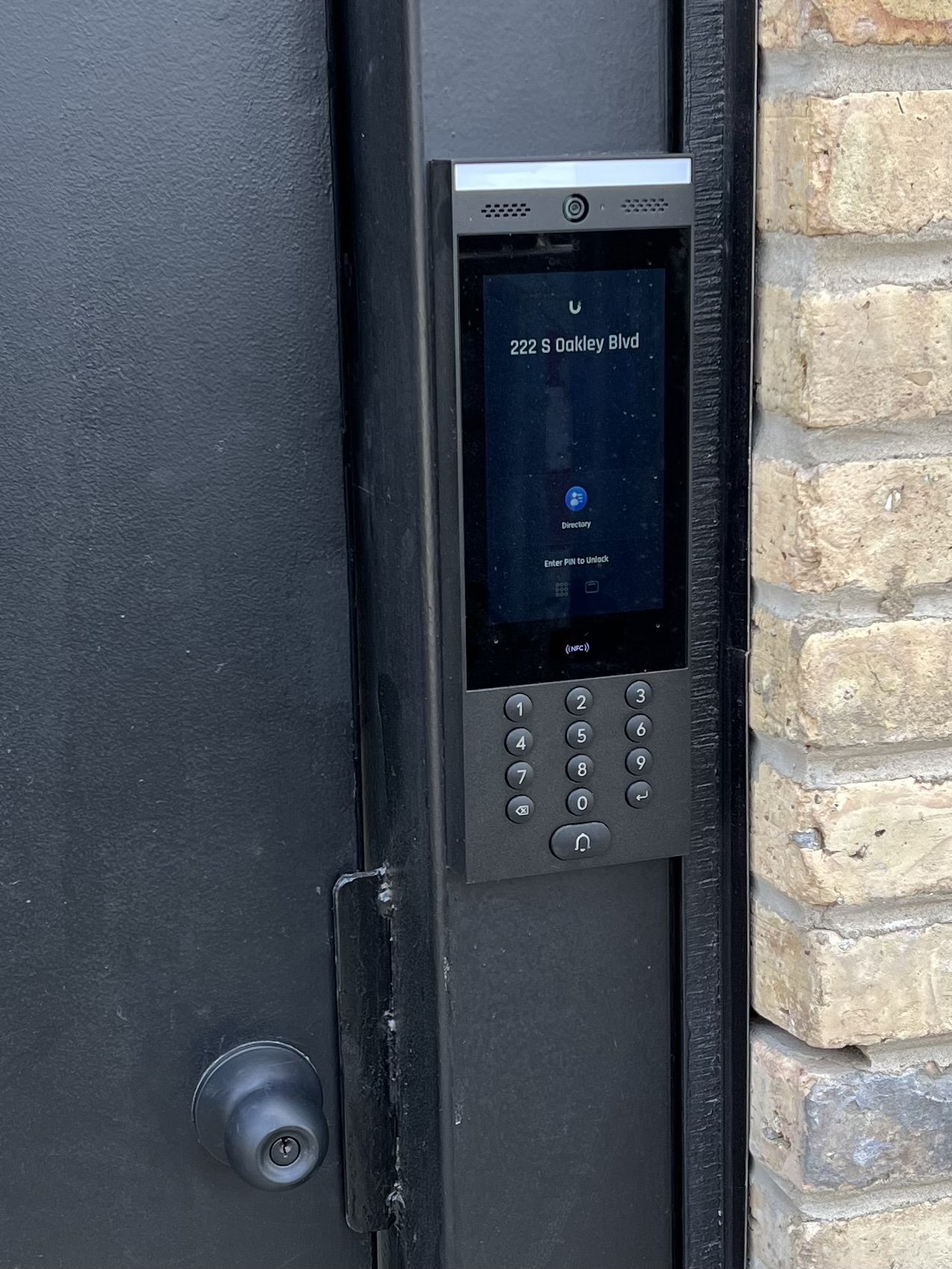
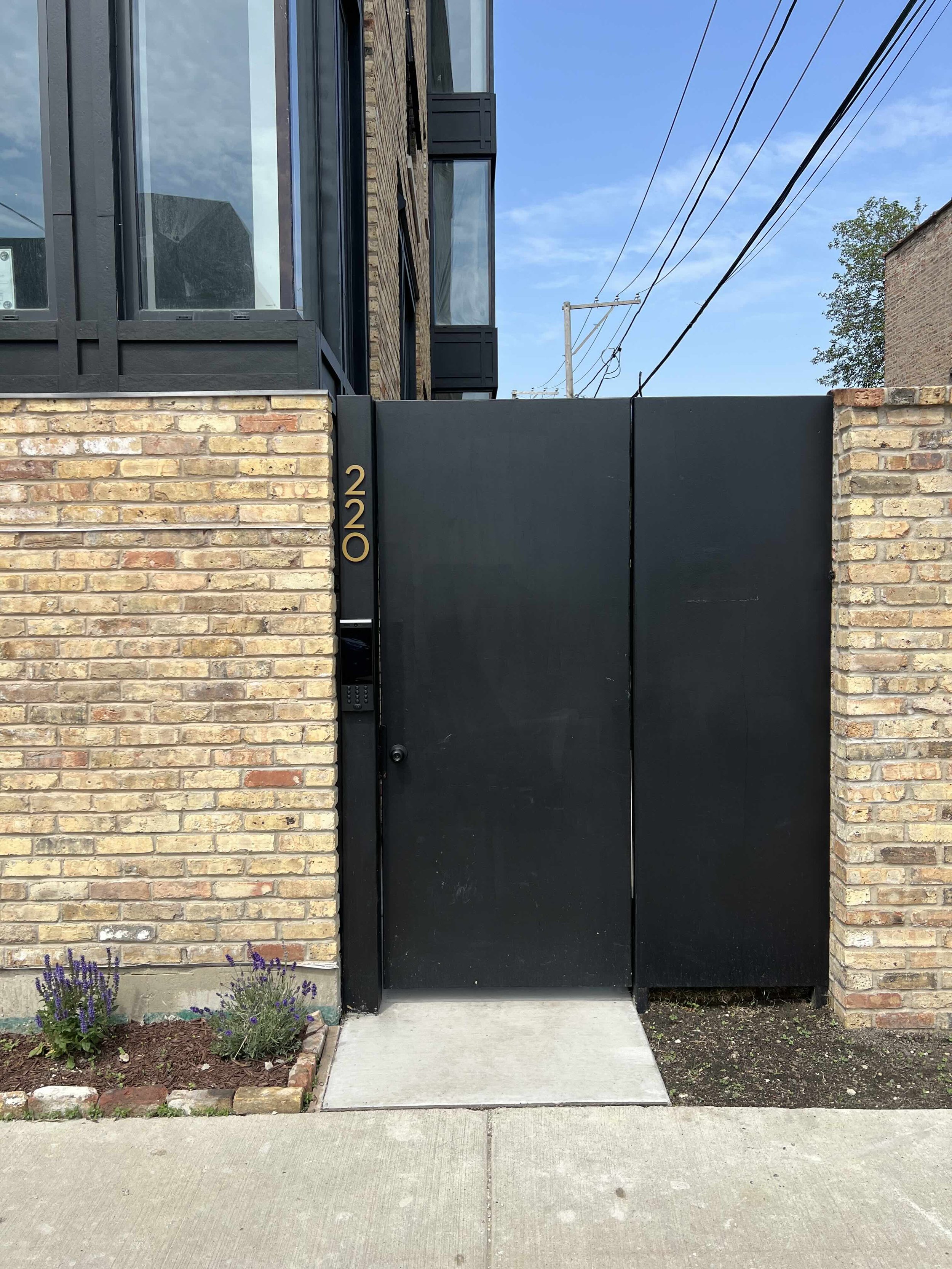
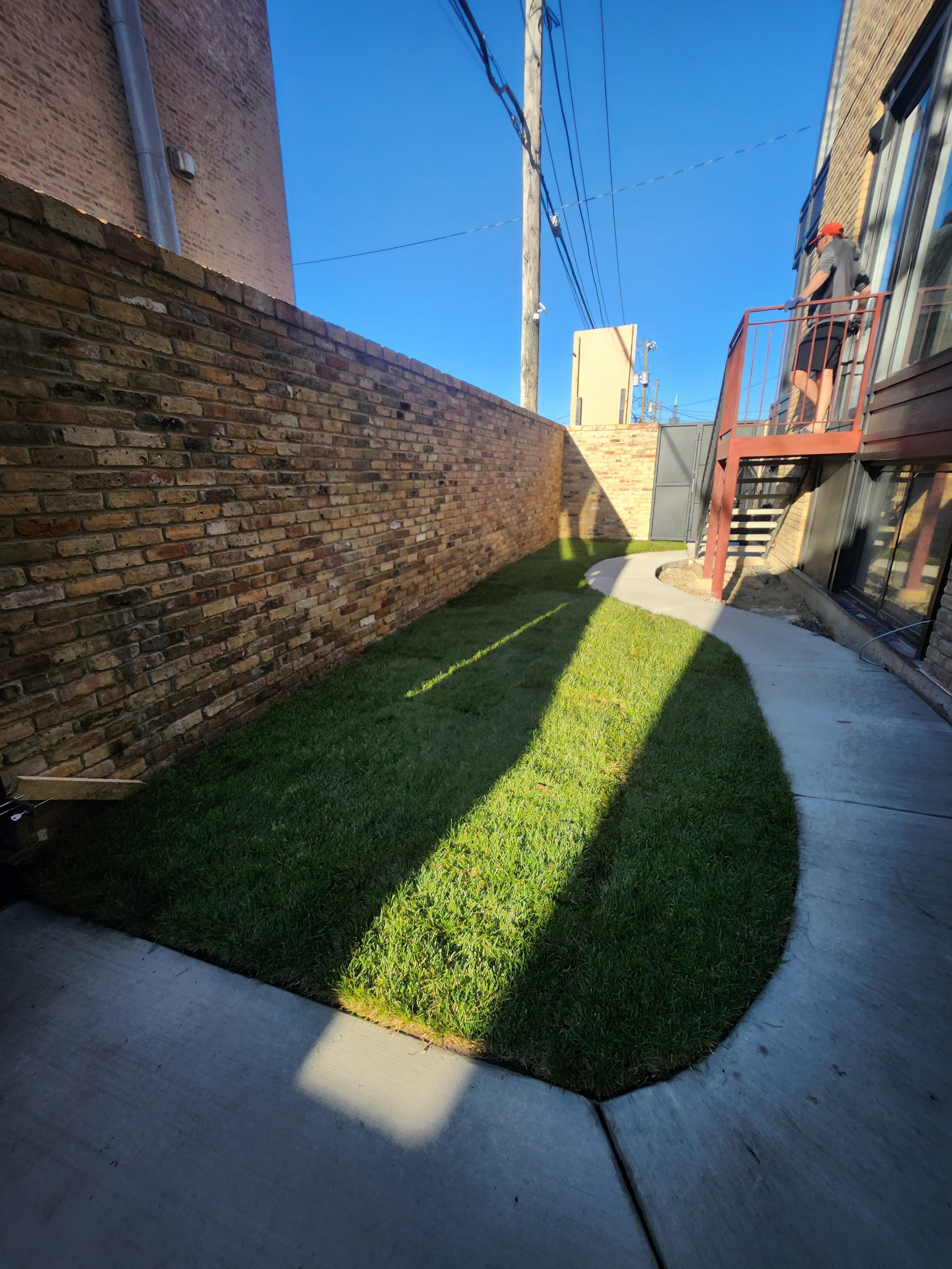
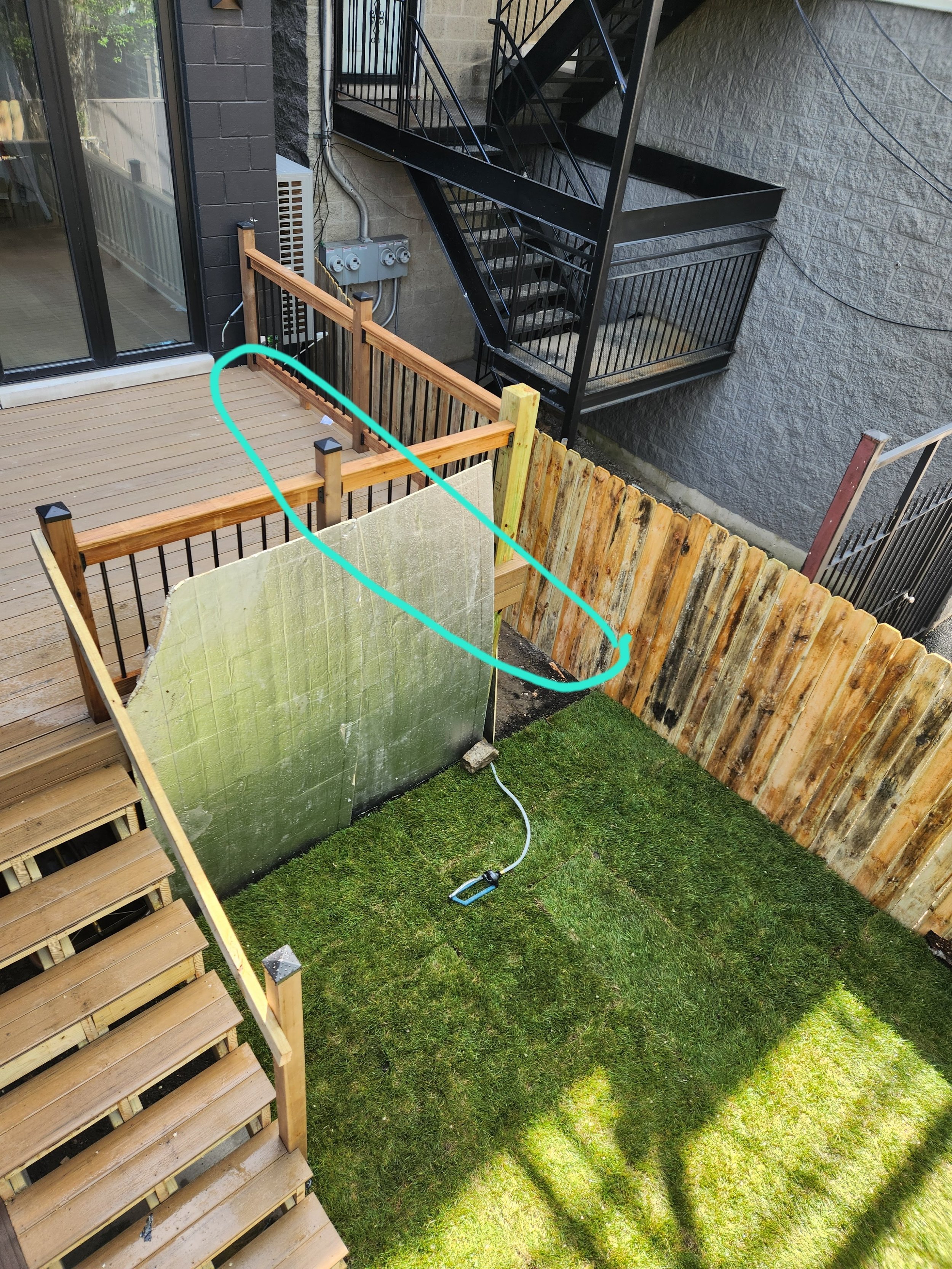
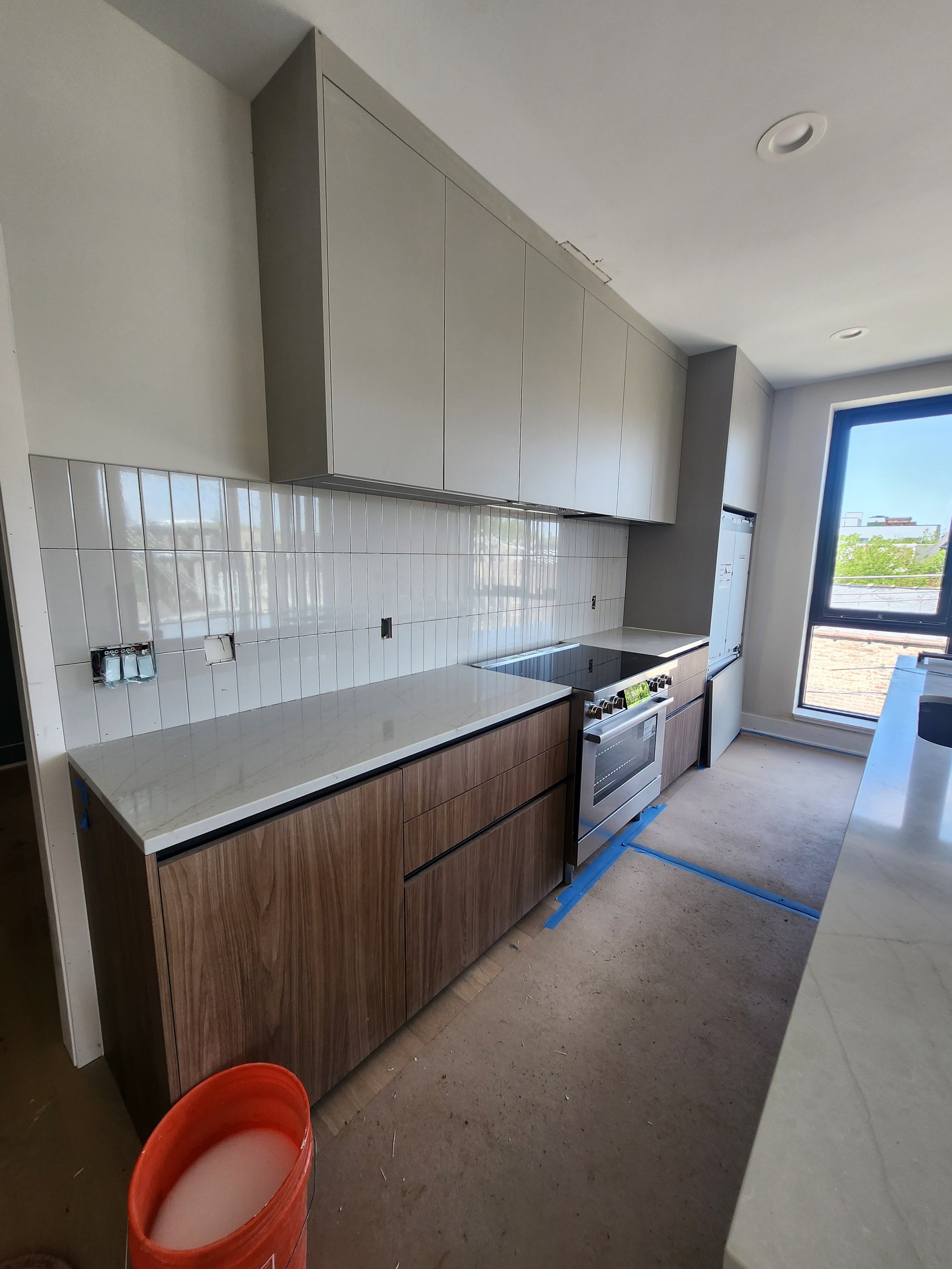
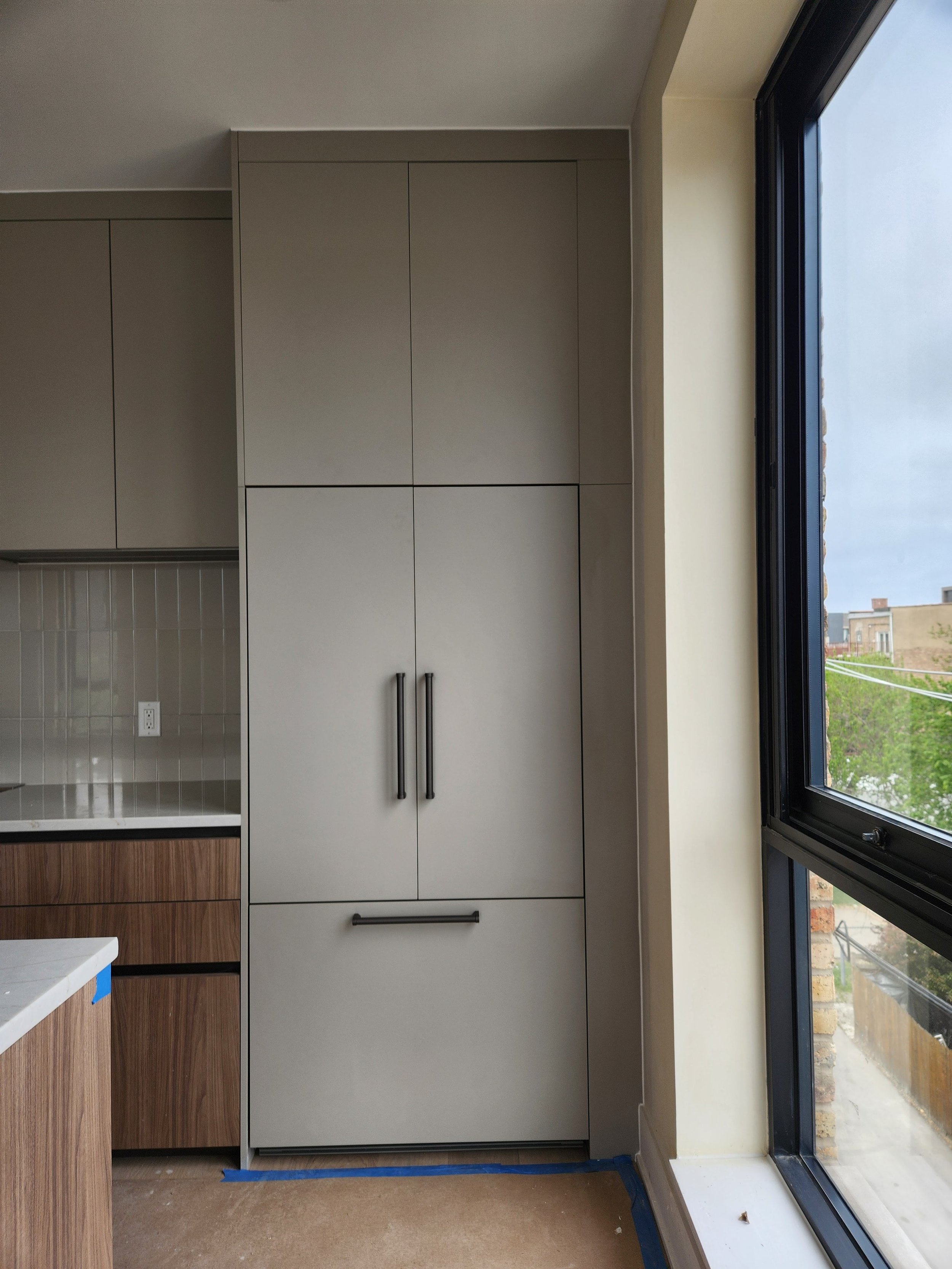
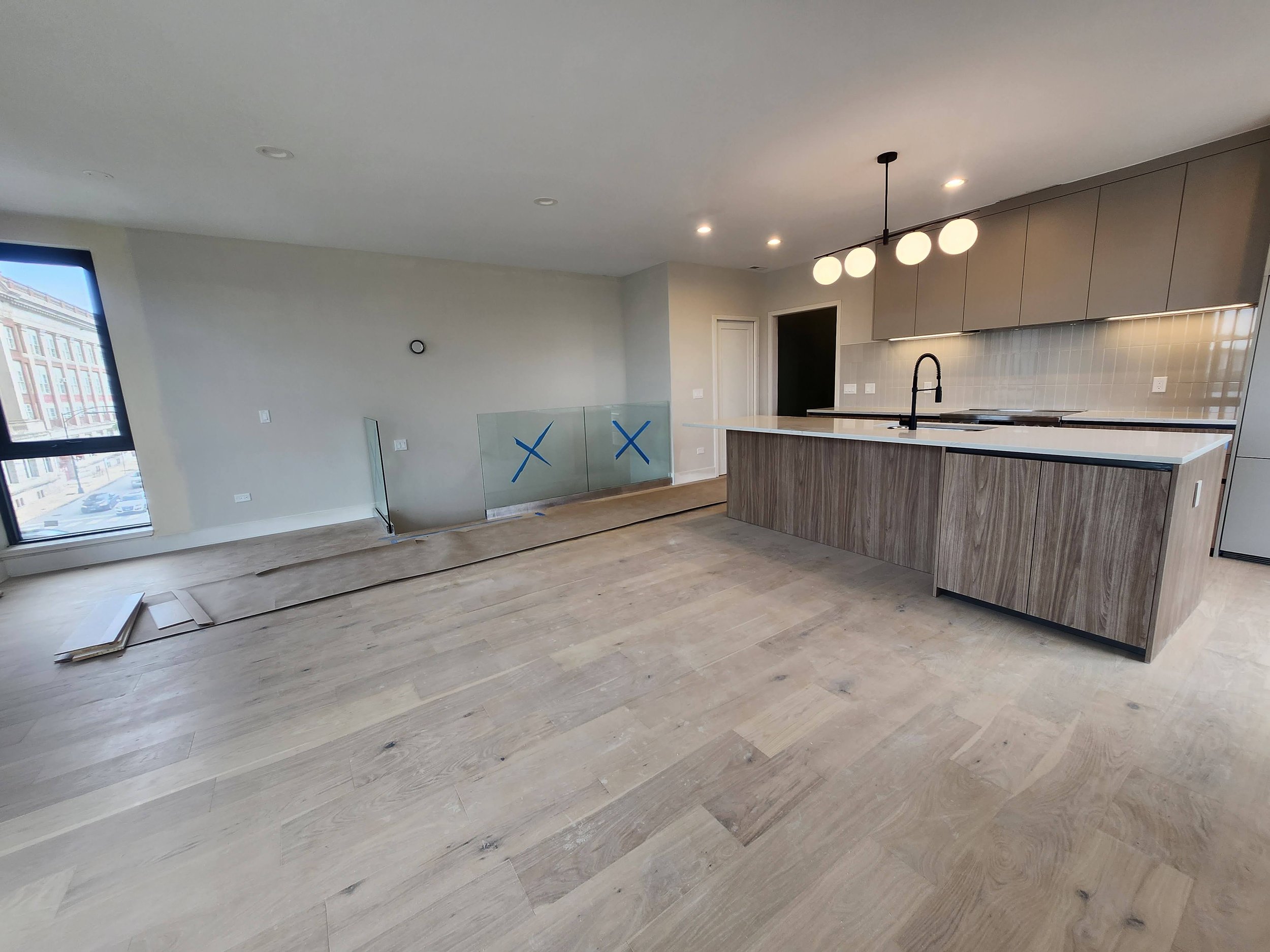
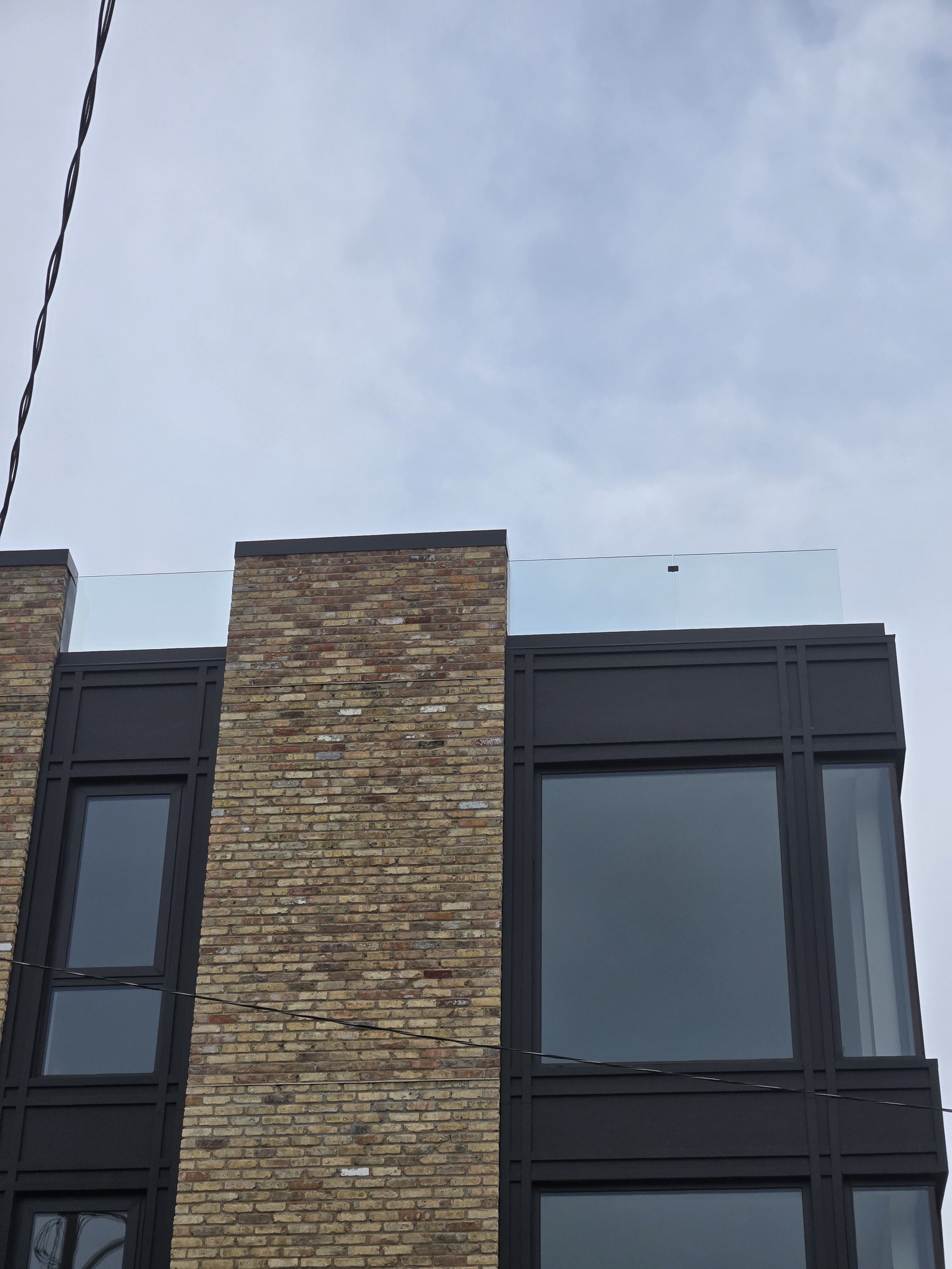
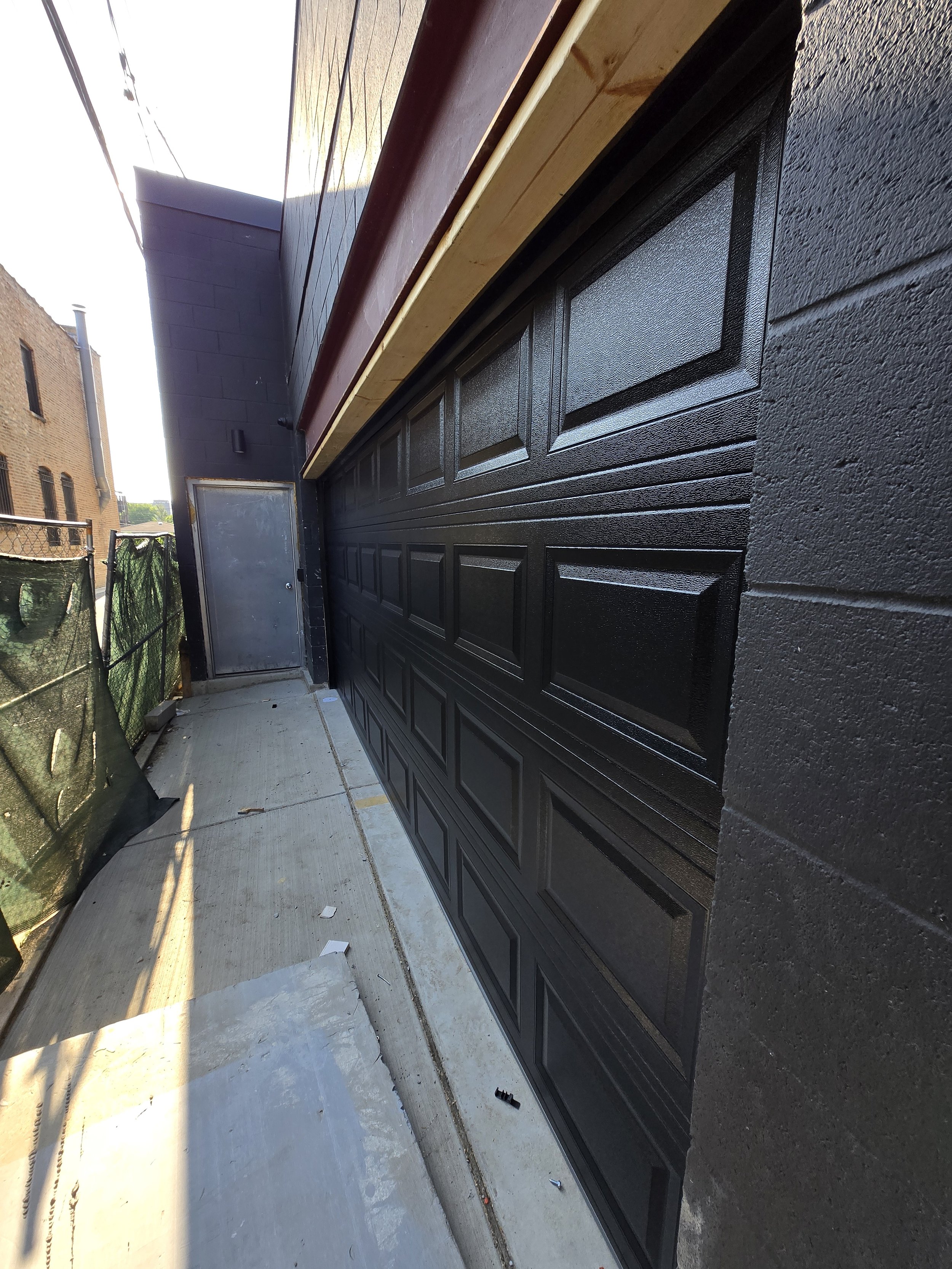
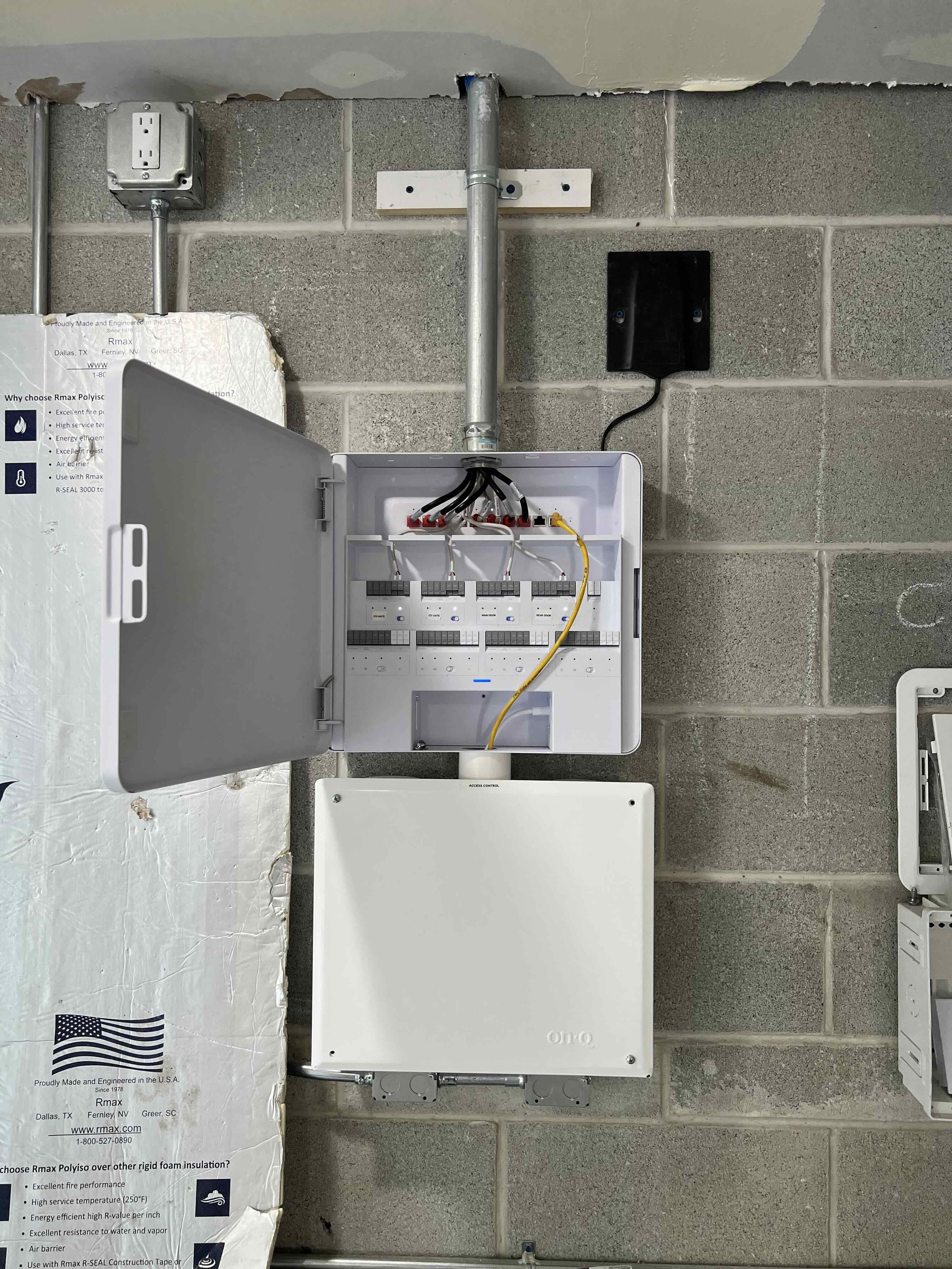
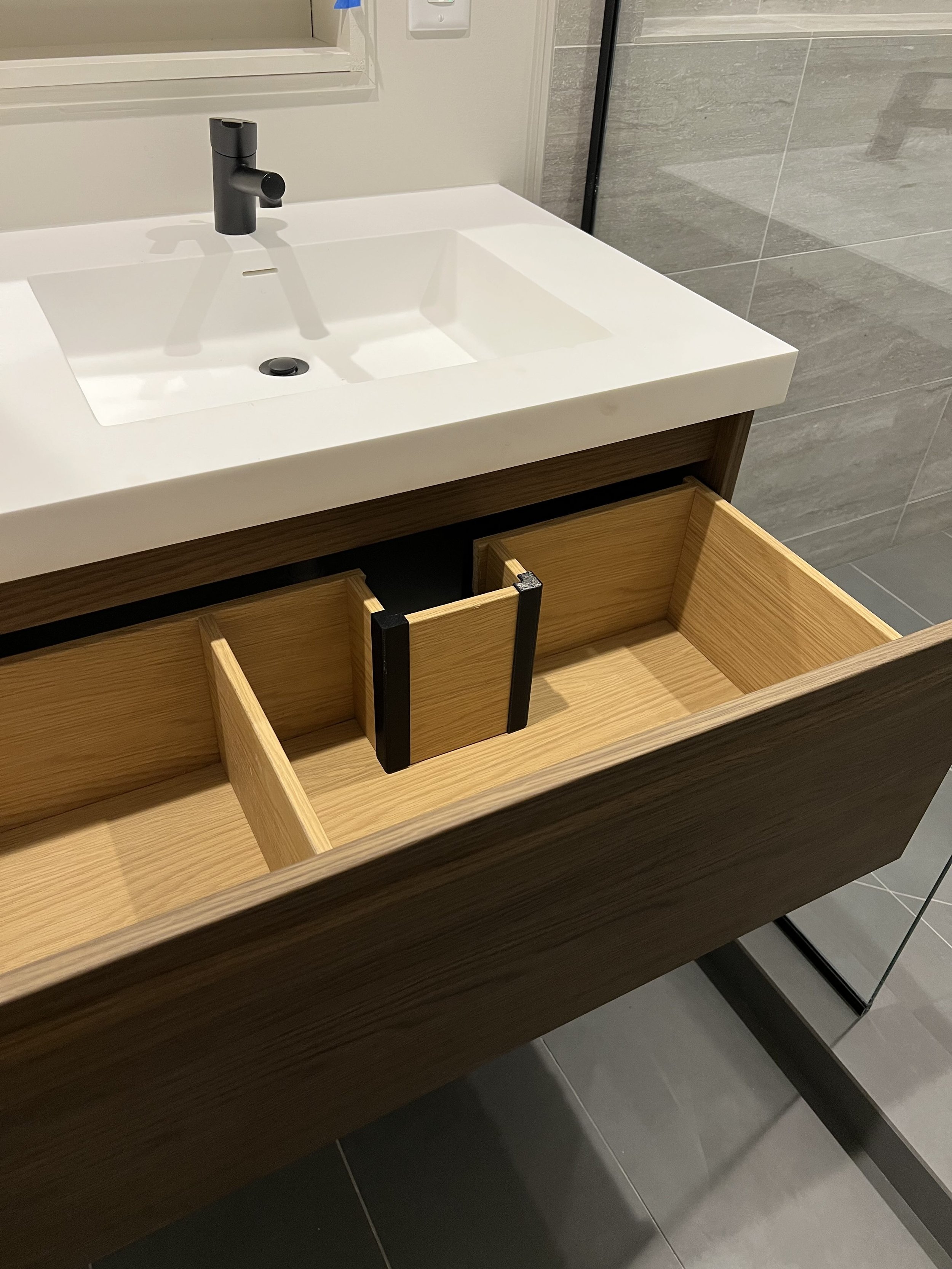
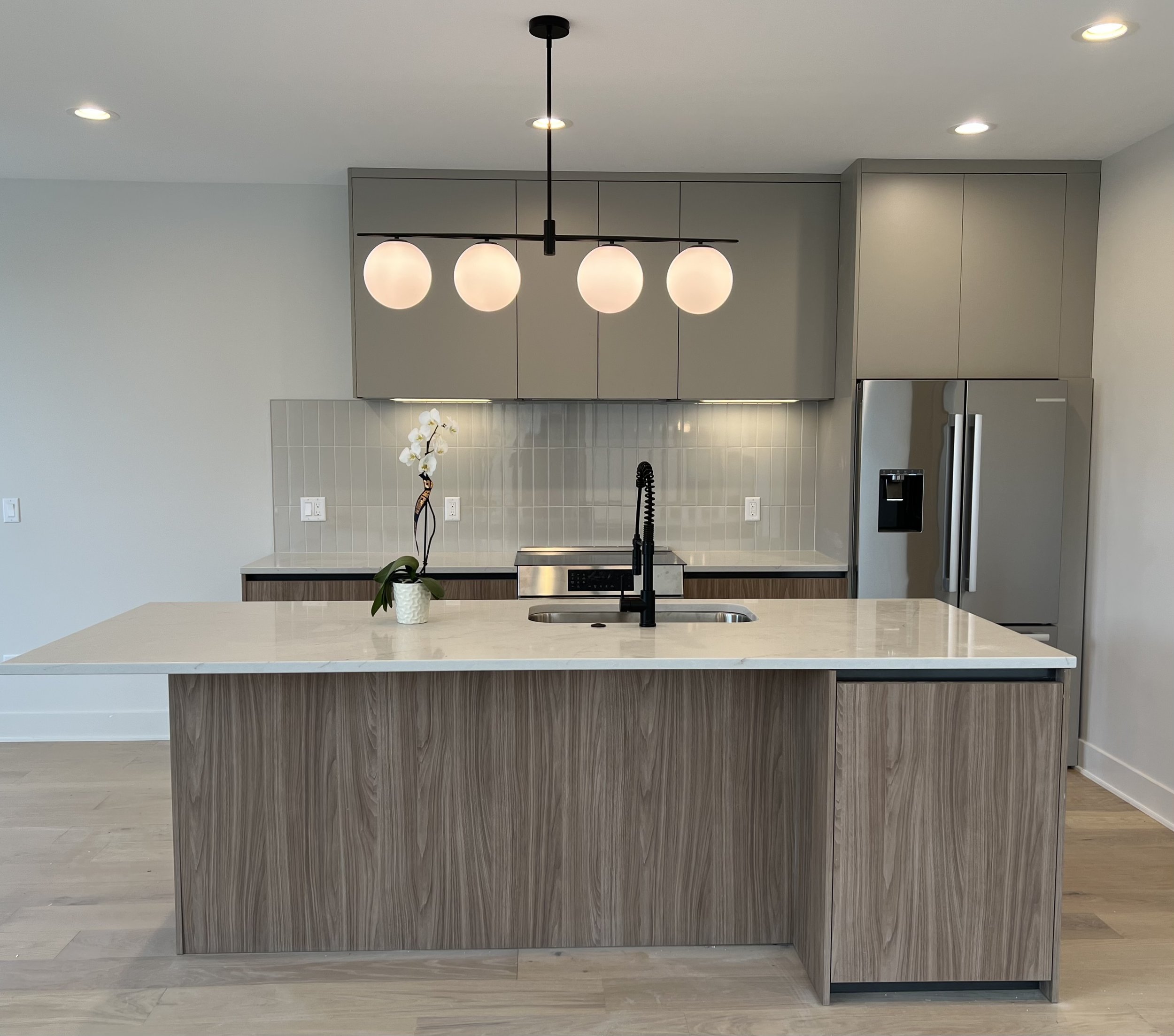
05/08/25
Flooring, countertops, appliances, closets and concrete sidewalks have been installed
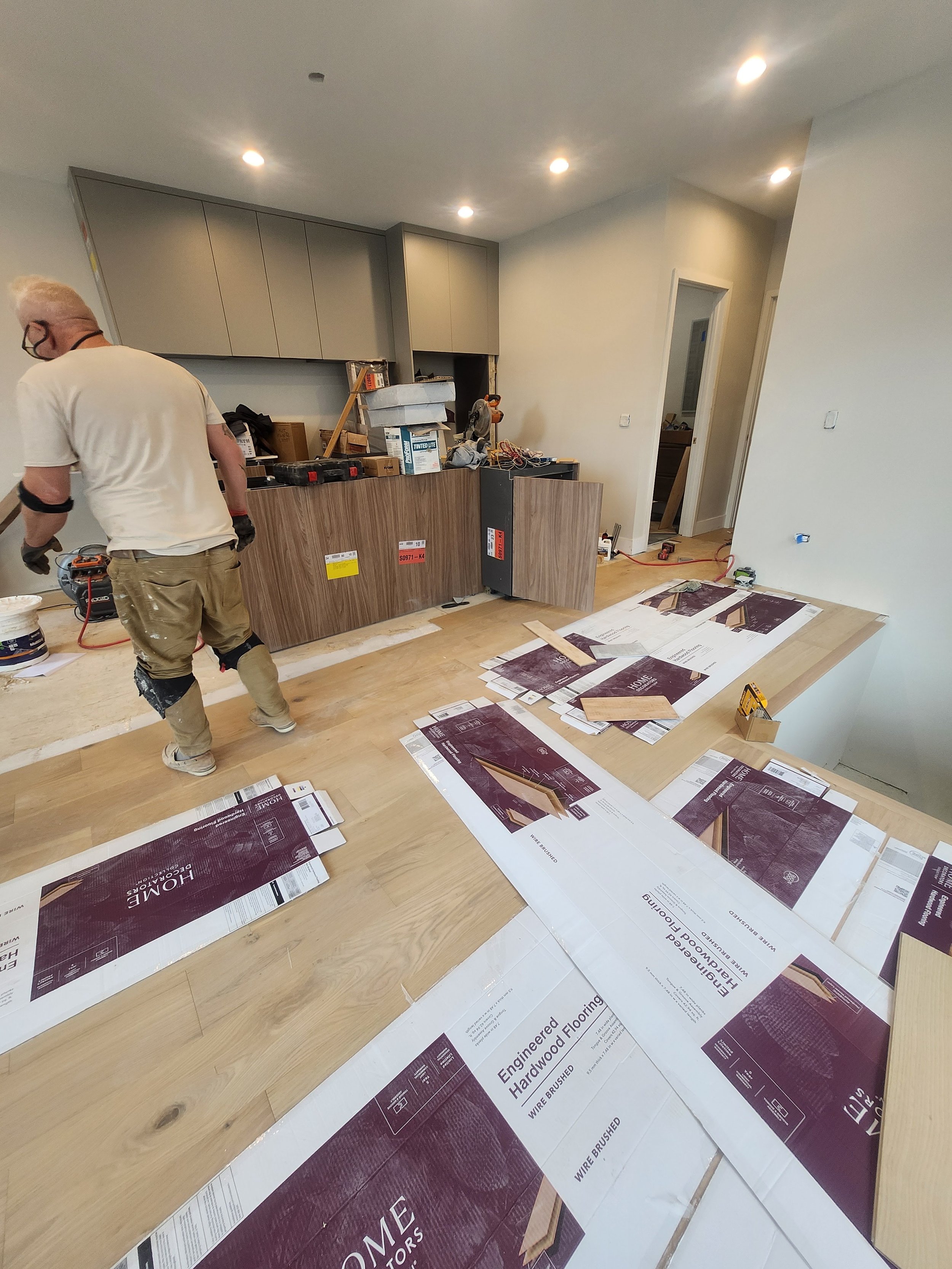
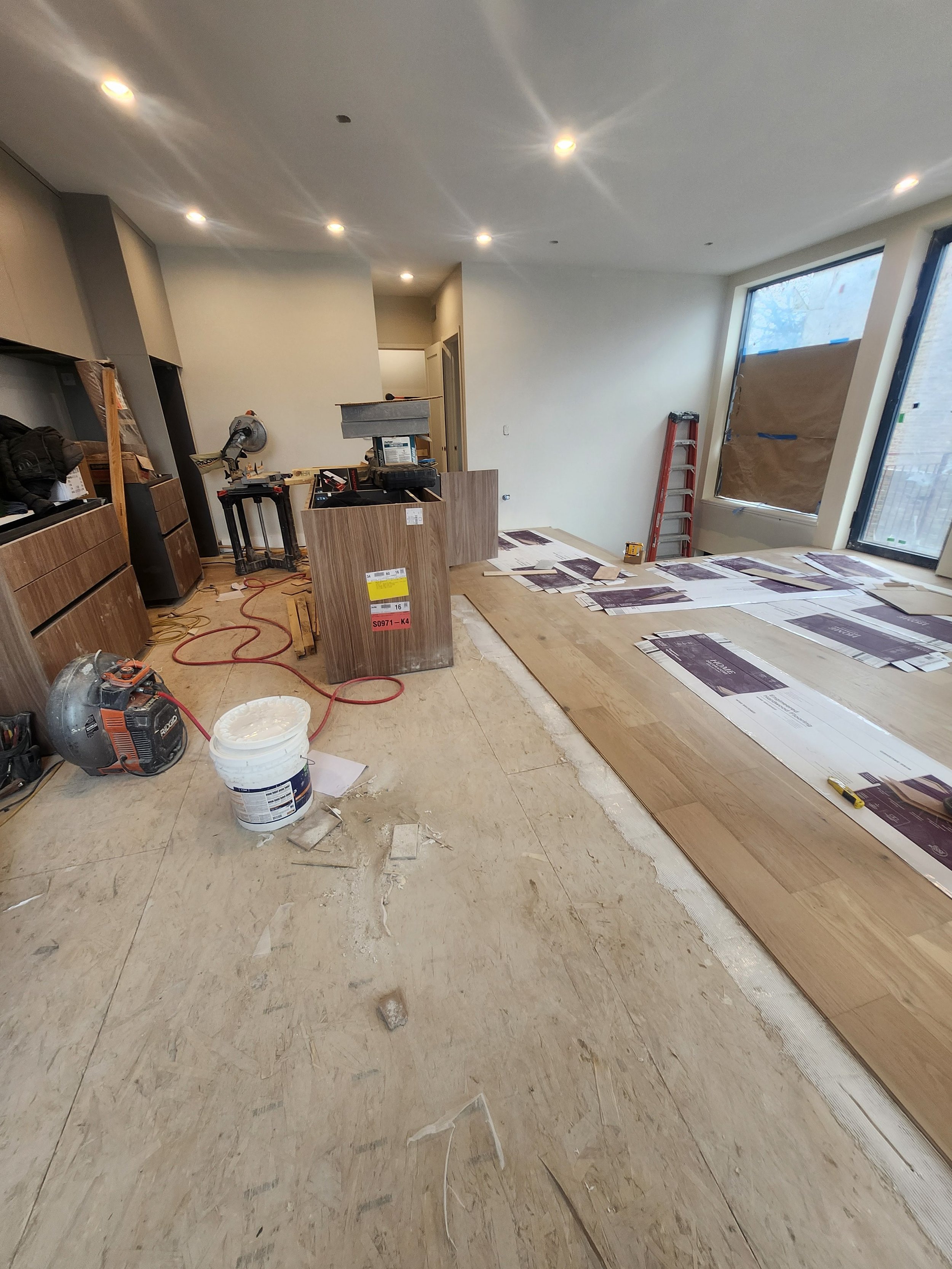
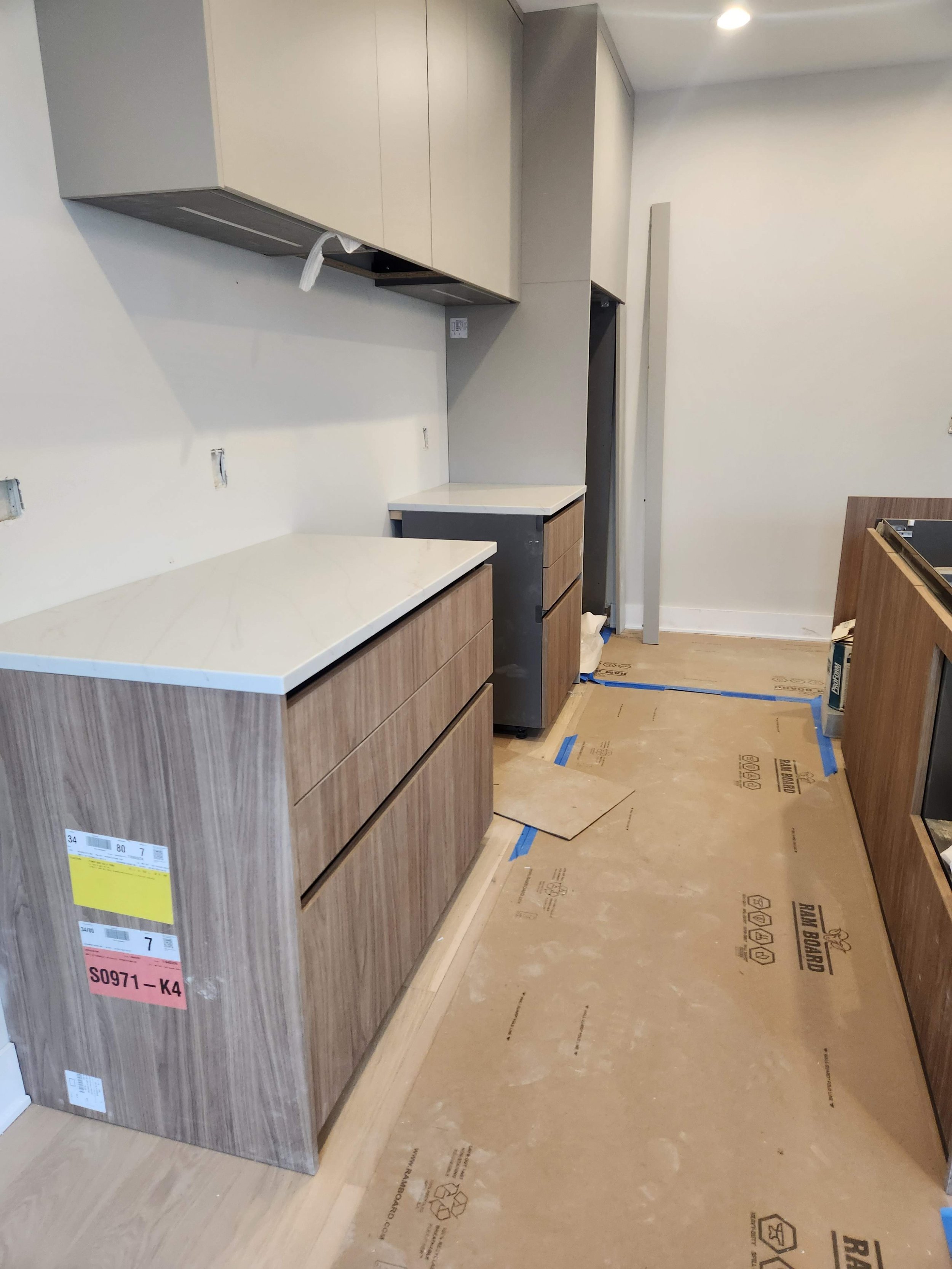
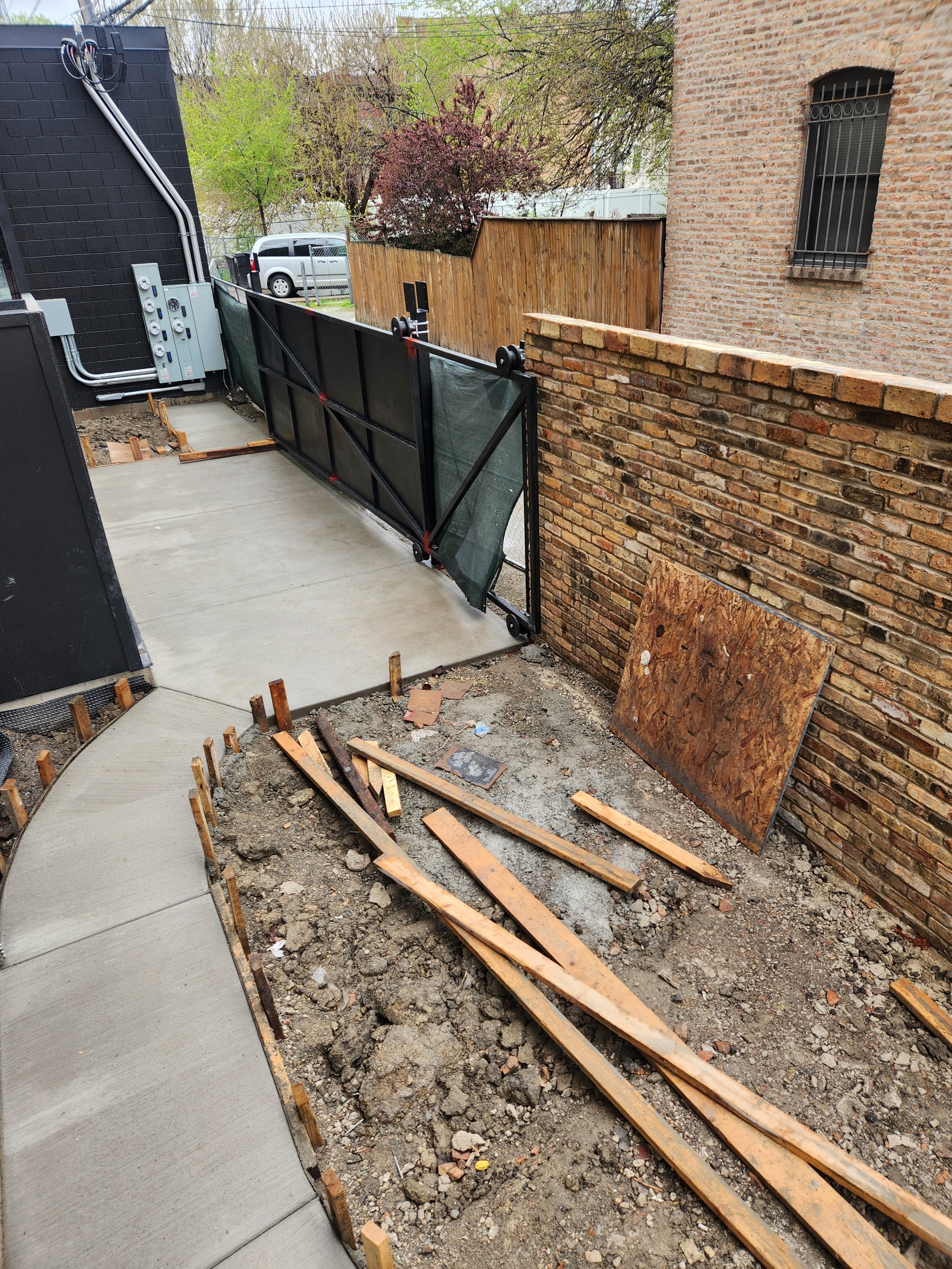
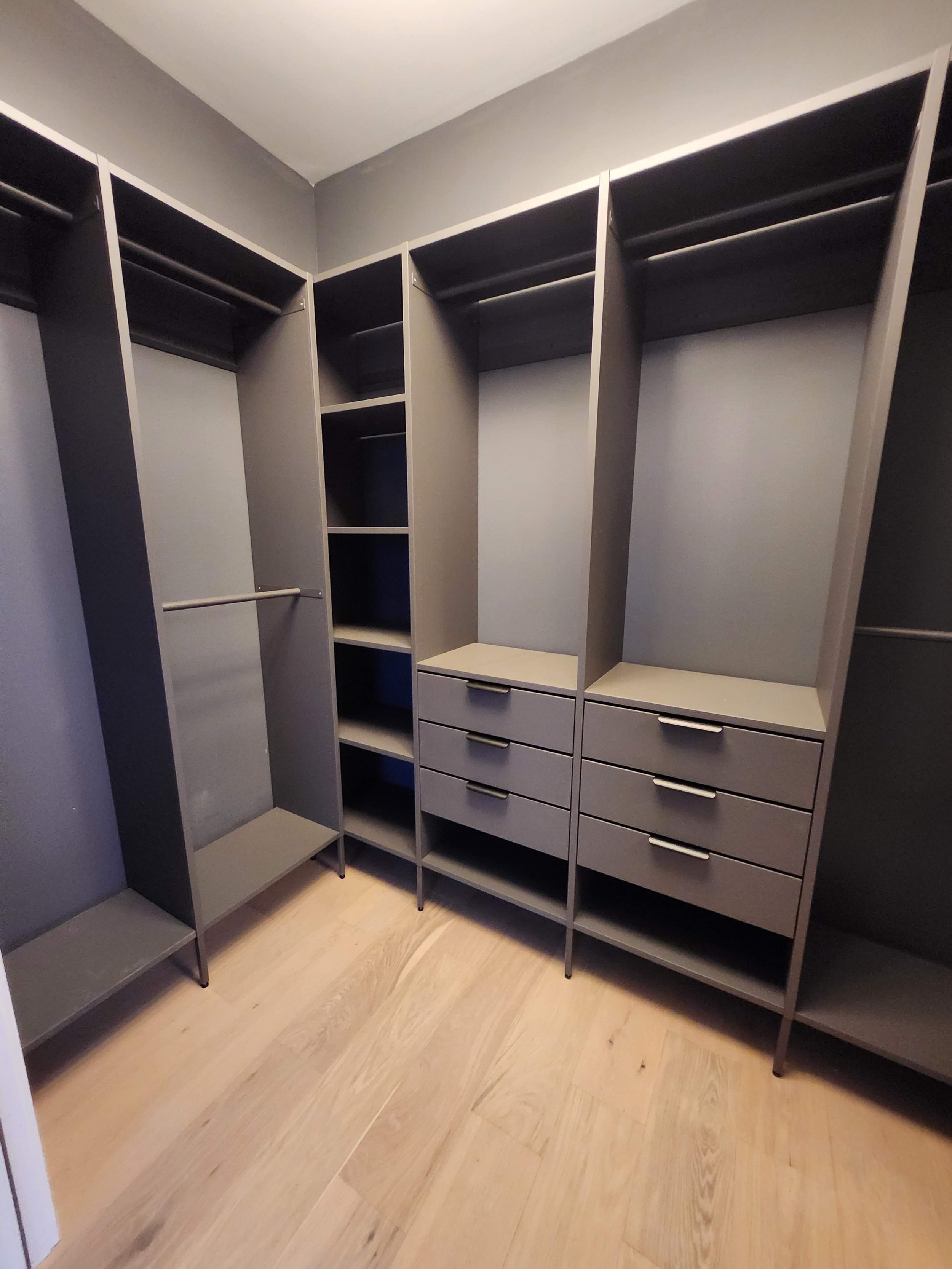
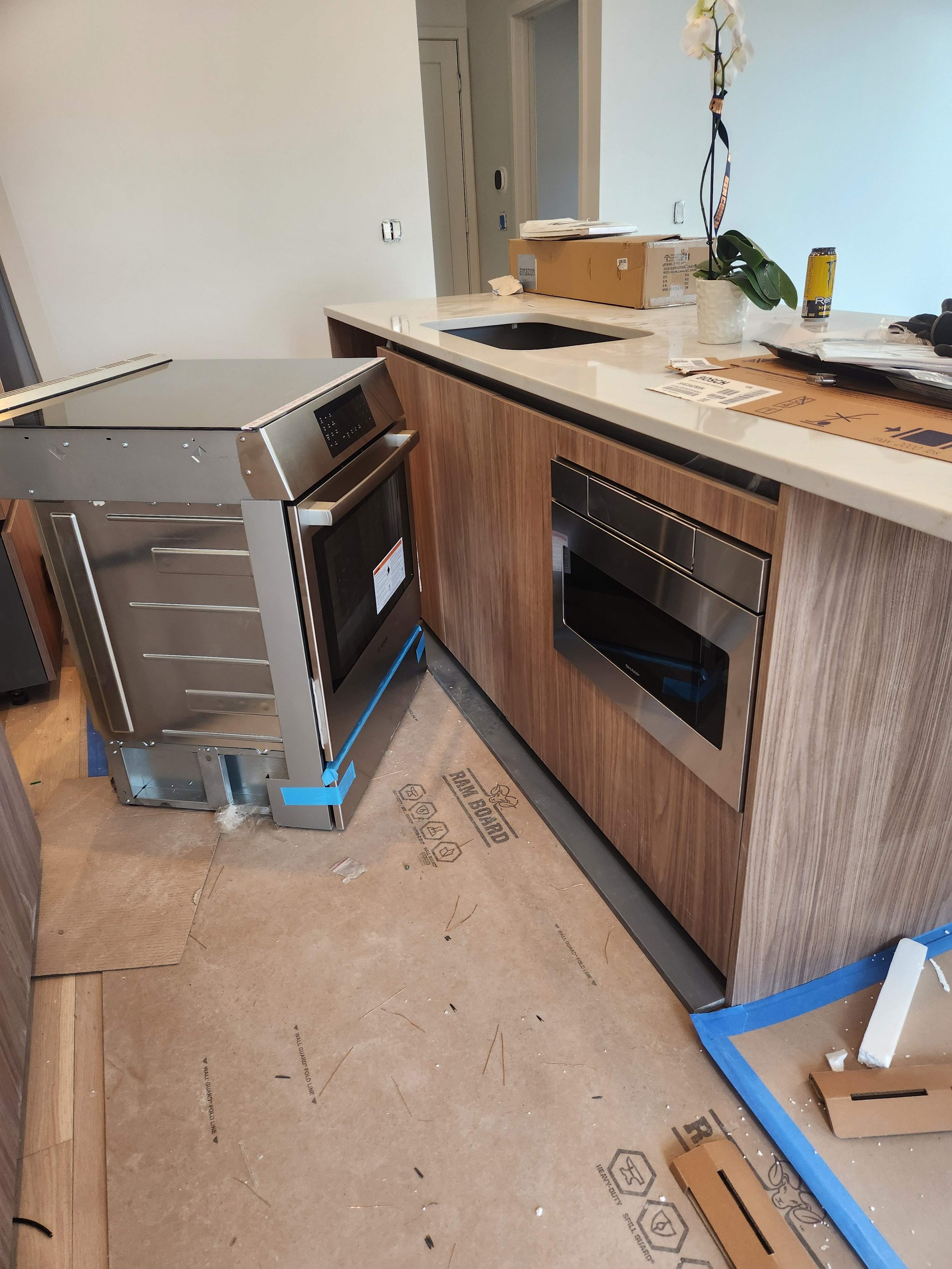
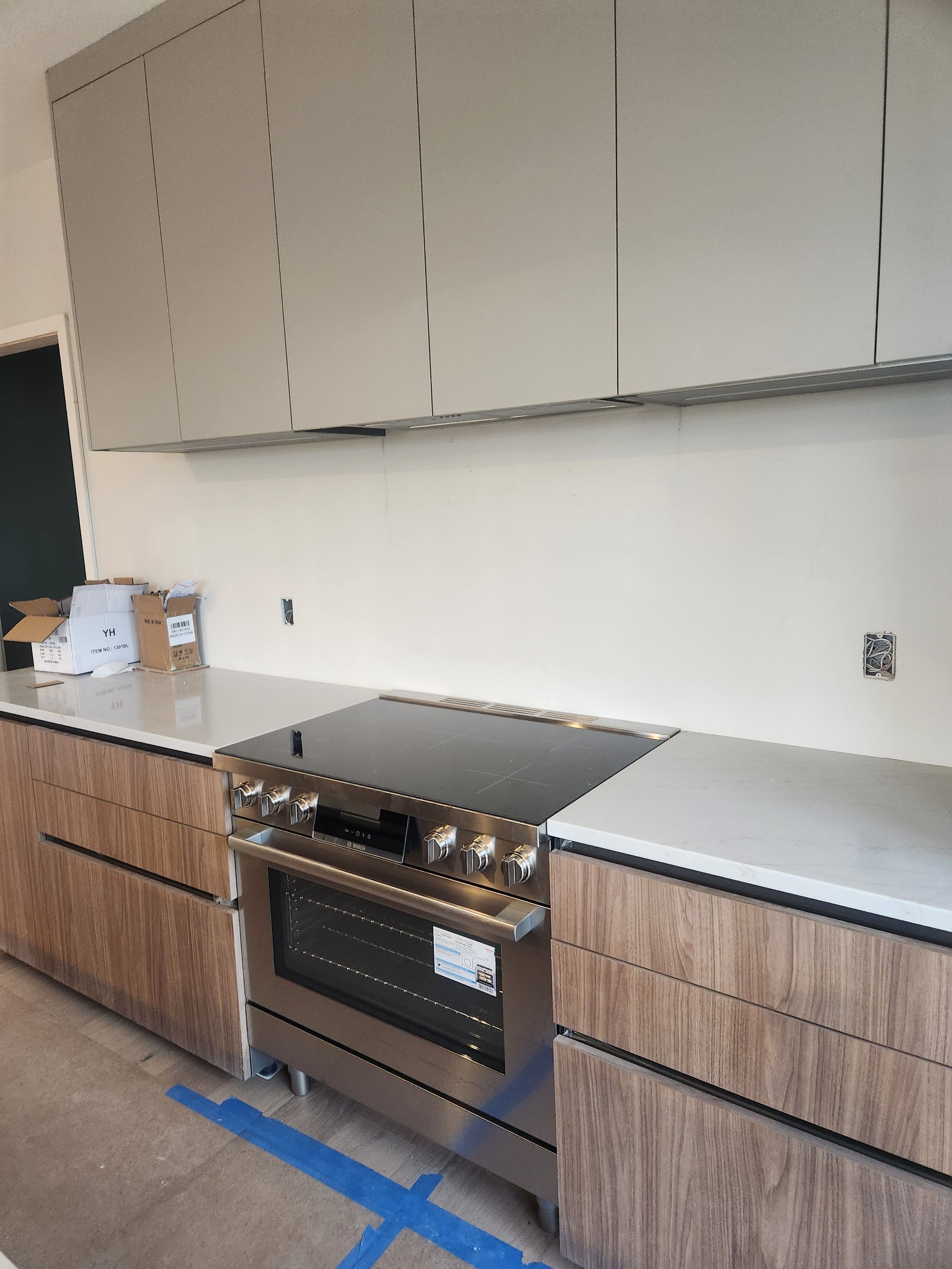
04/10/25
Exterior work has made good progress these past few weeks now that the weather is a bit warmer. The siding and coping was finally completely finished this week! The brick garden wall for unit 1E was finished this week as well! And we also started decking installation for units 2 and 3.
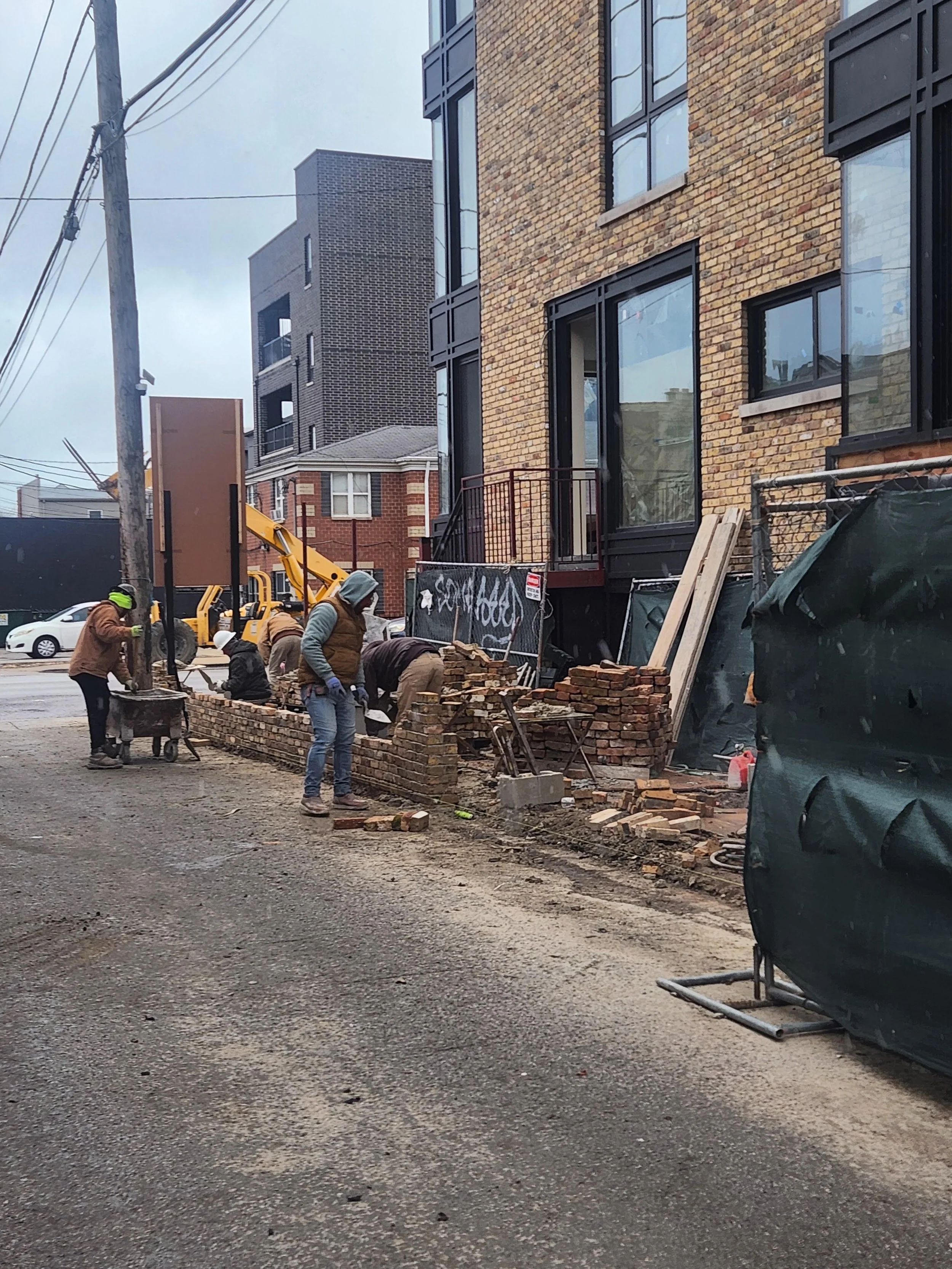

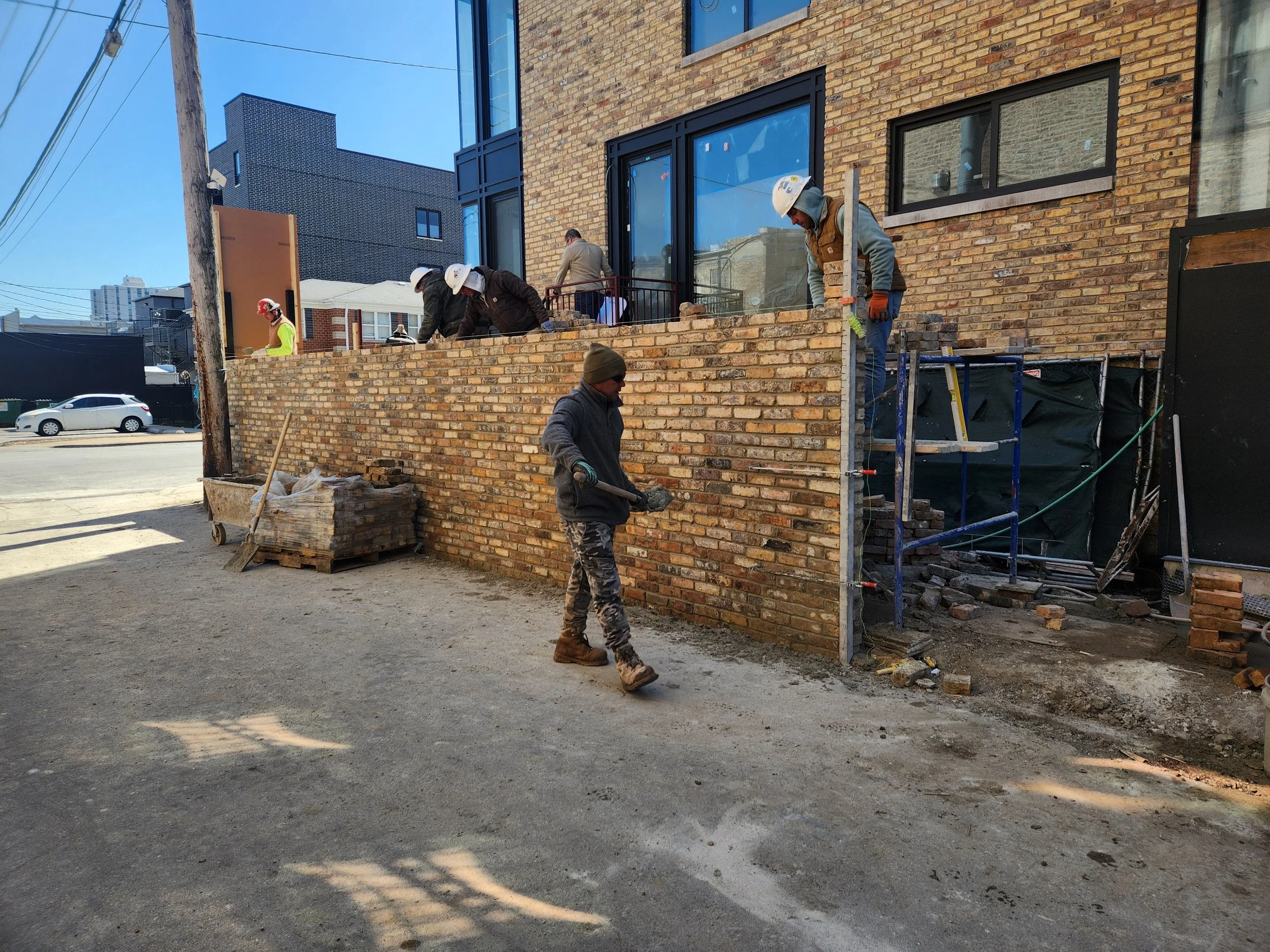
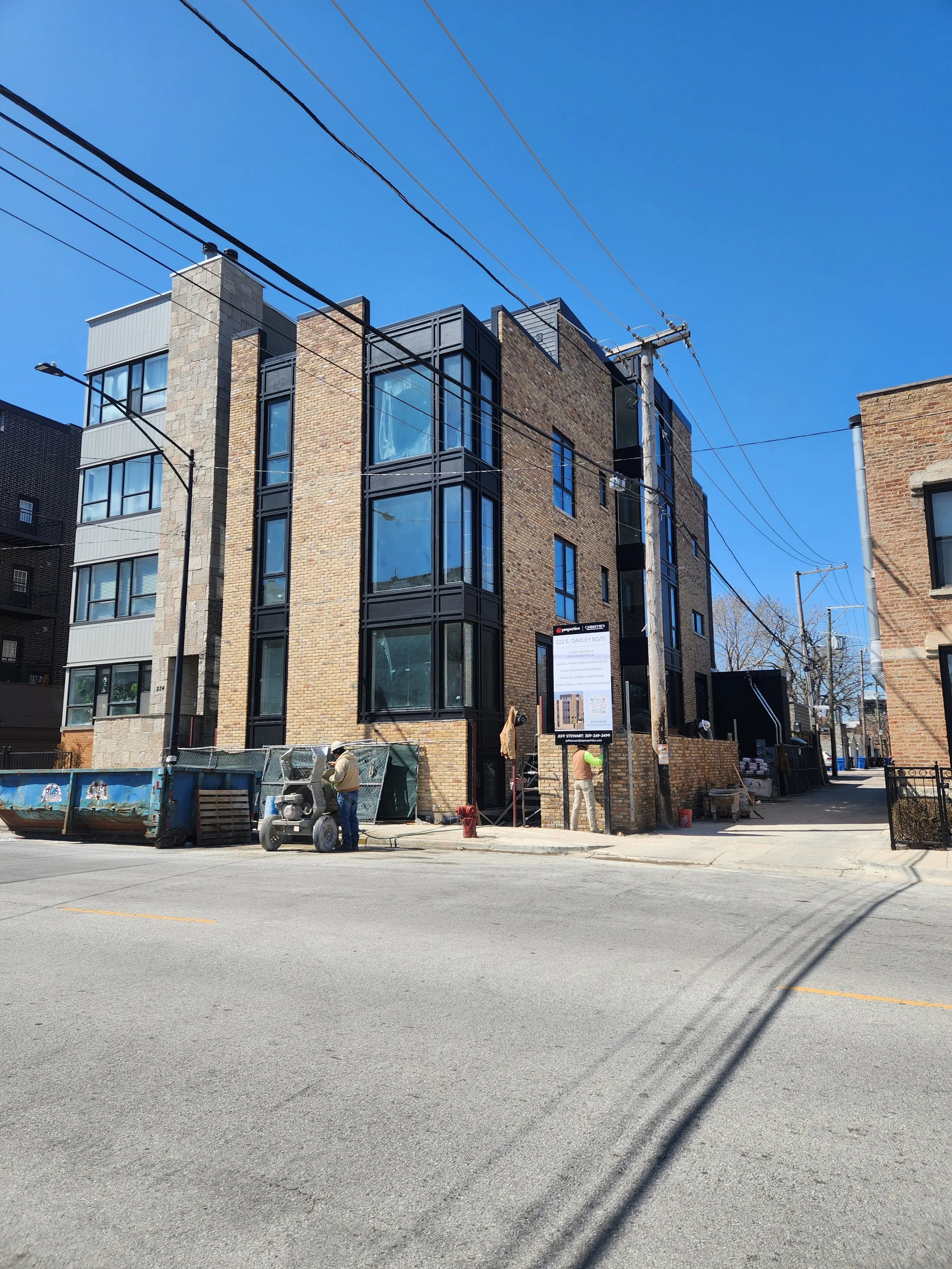
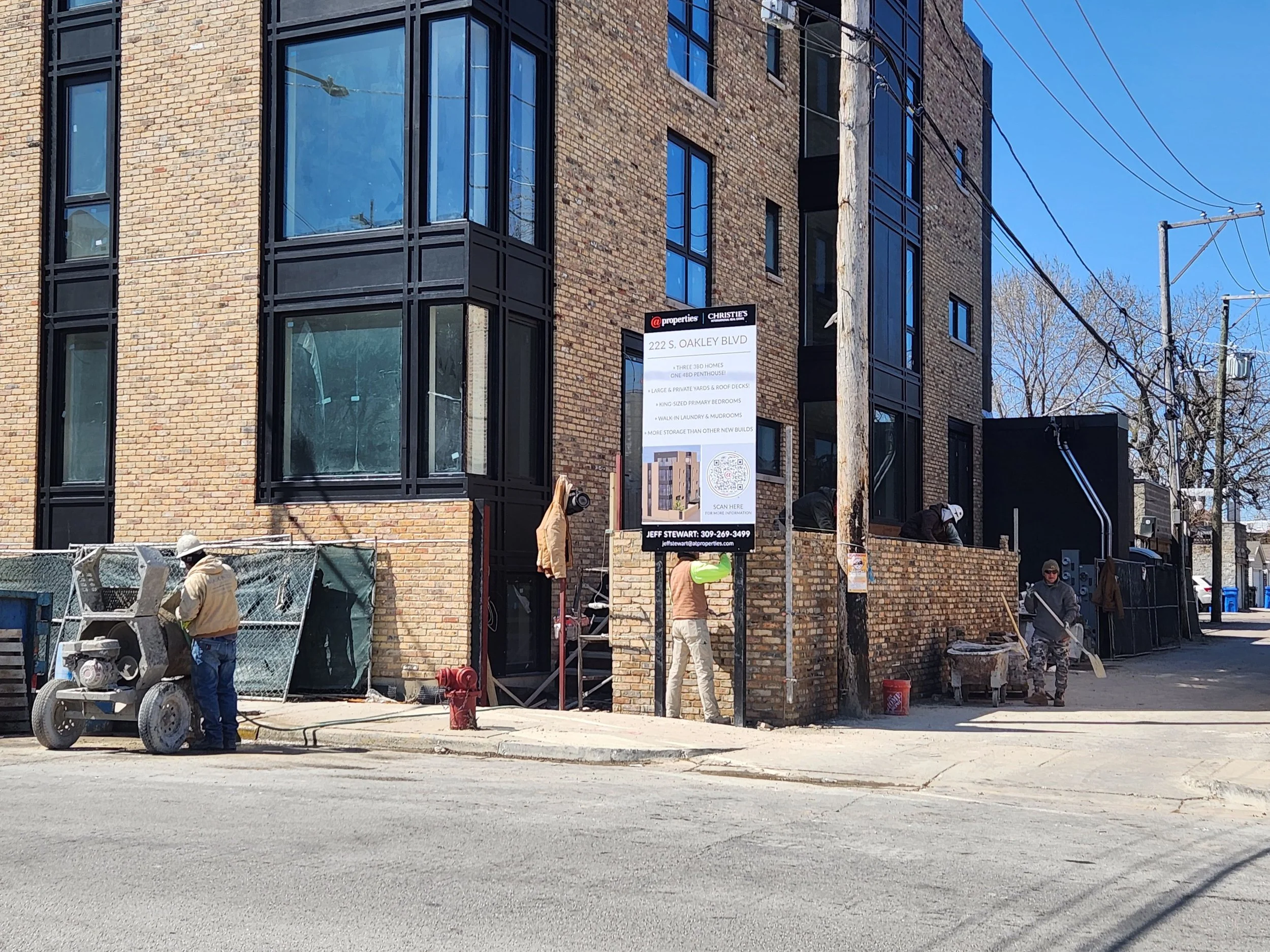

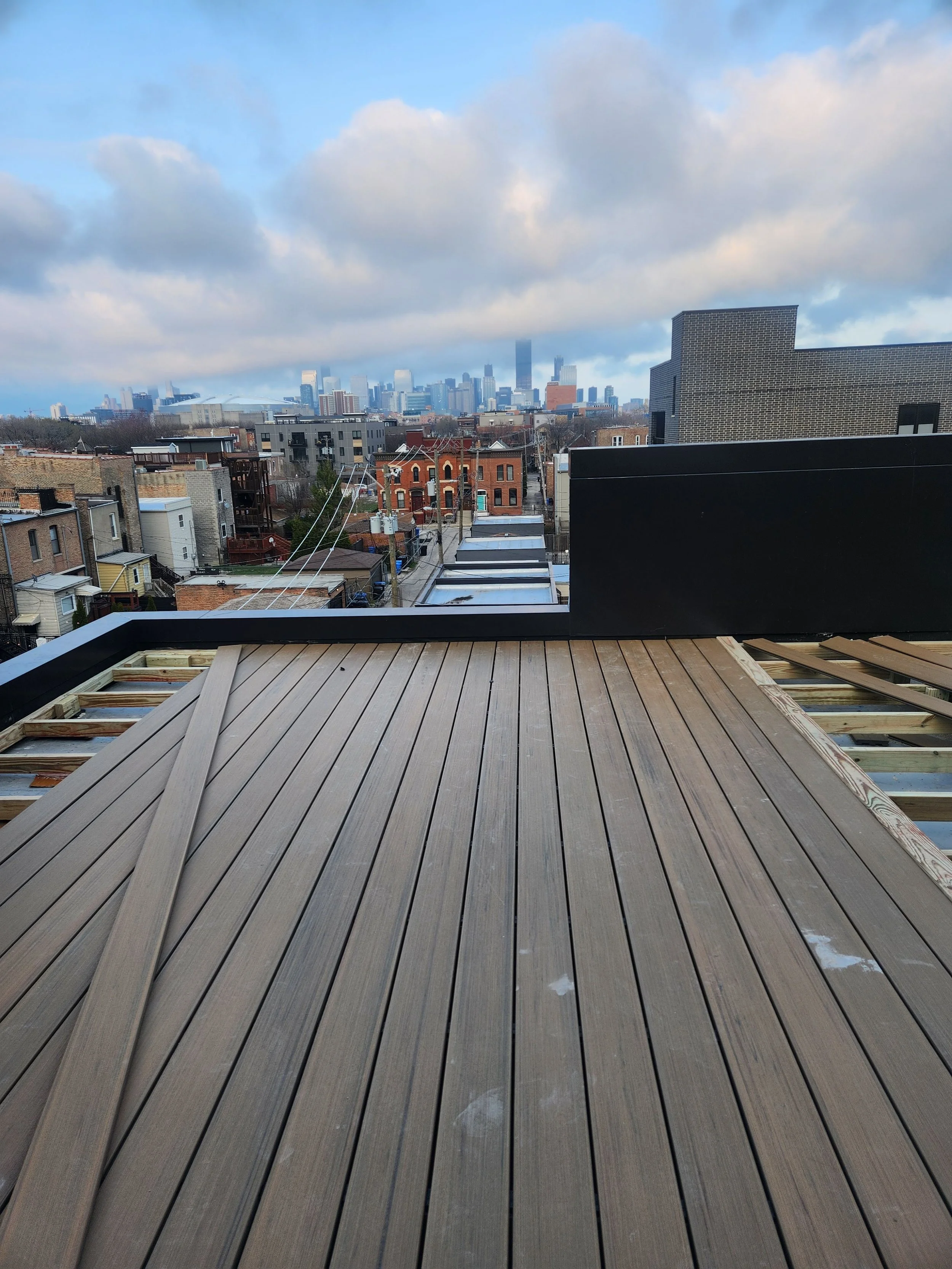
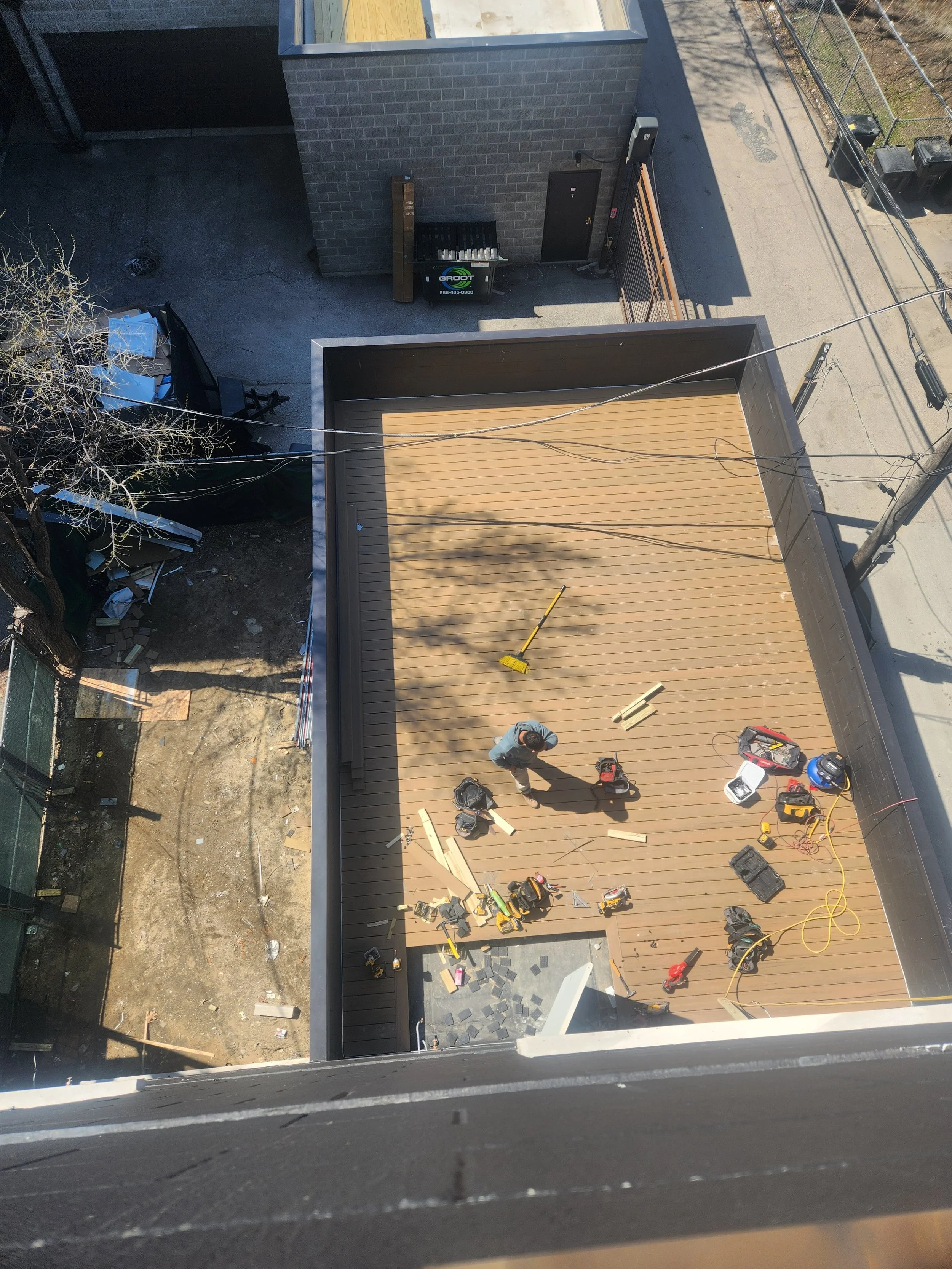
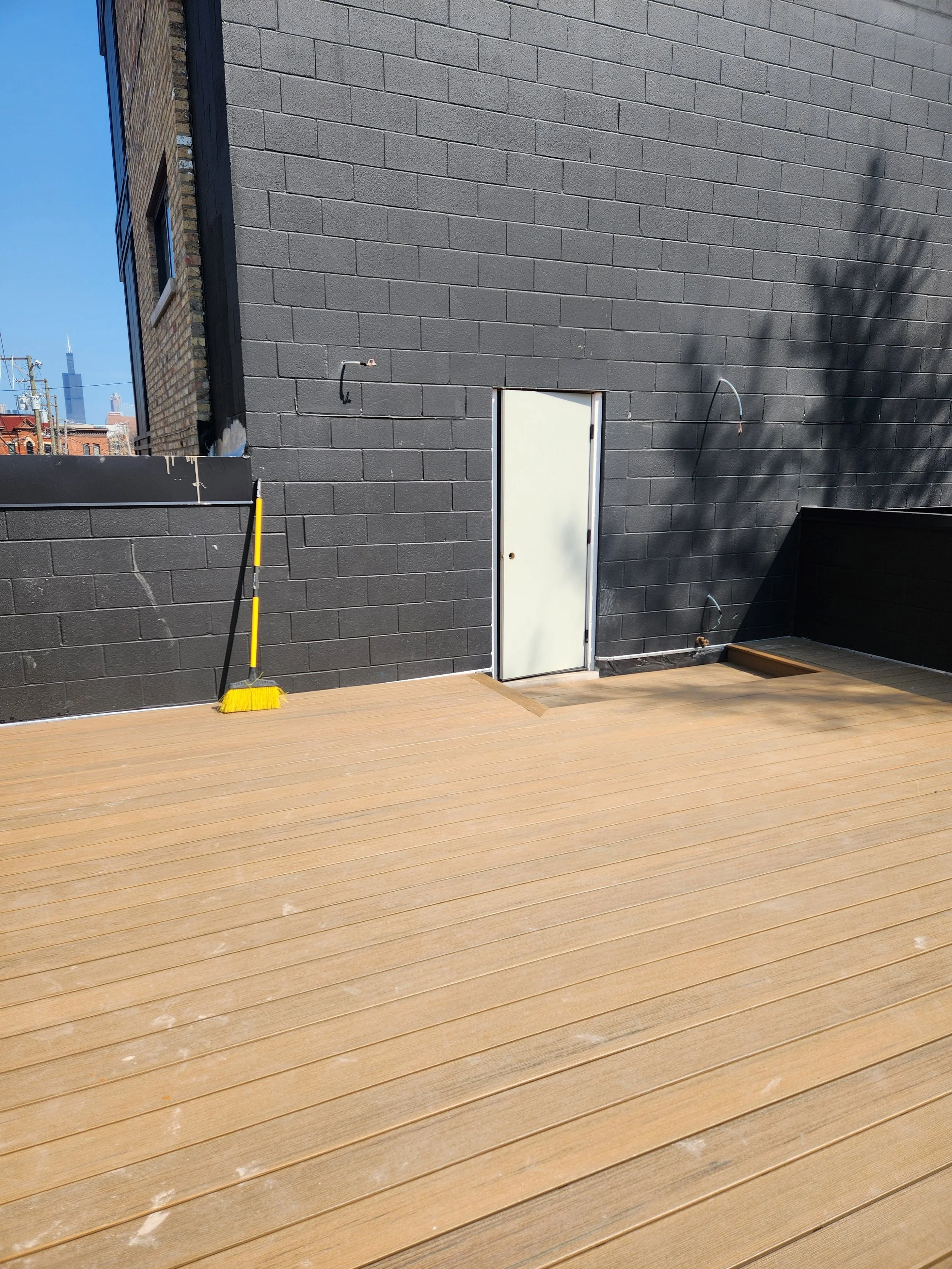
03/25/25
We’ve started installation of our super sleek Italian kitchen cabinets and our bathroom vanities. Plus, the stone guys have measured for our countertops, which are now in production.


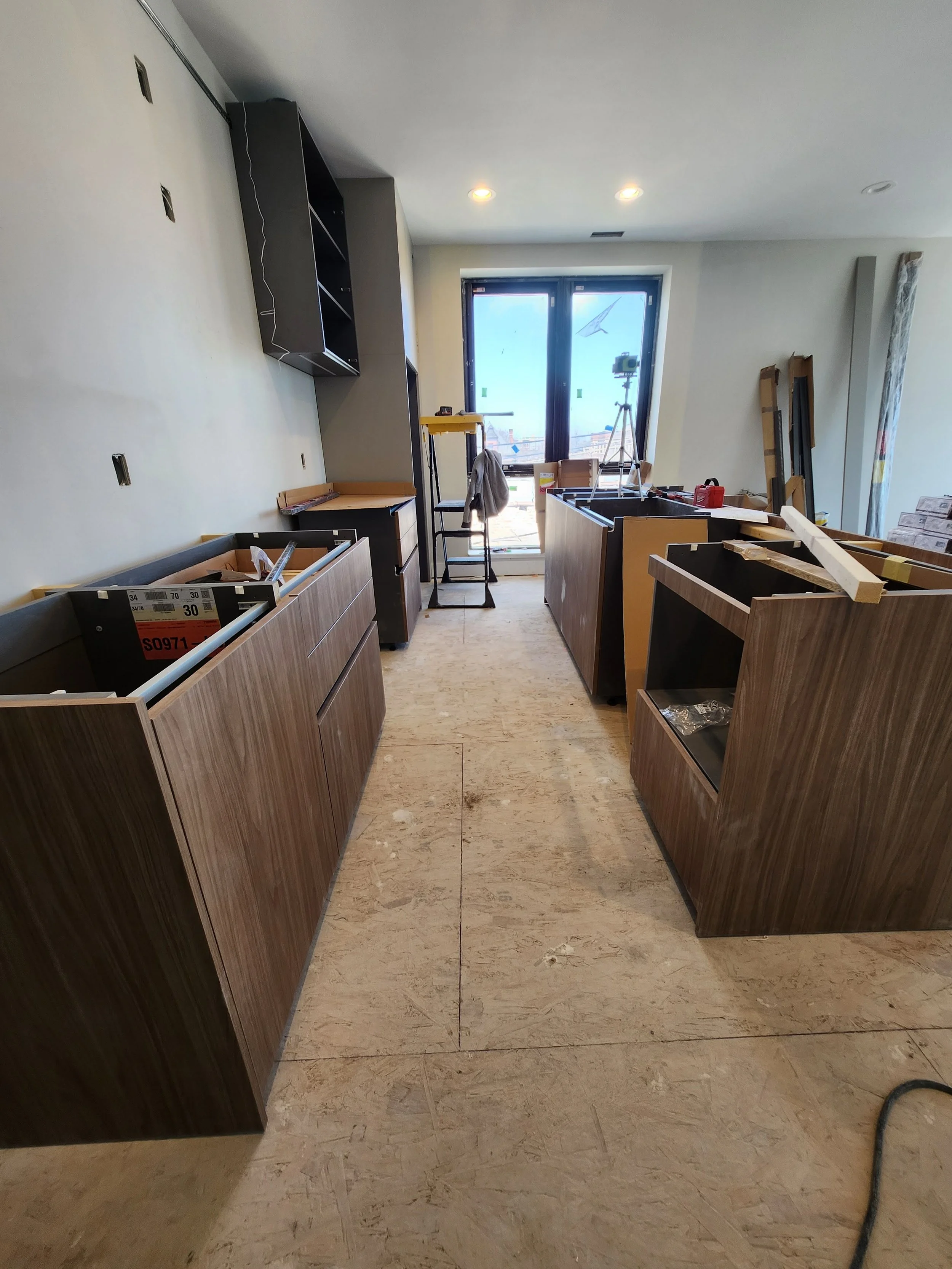



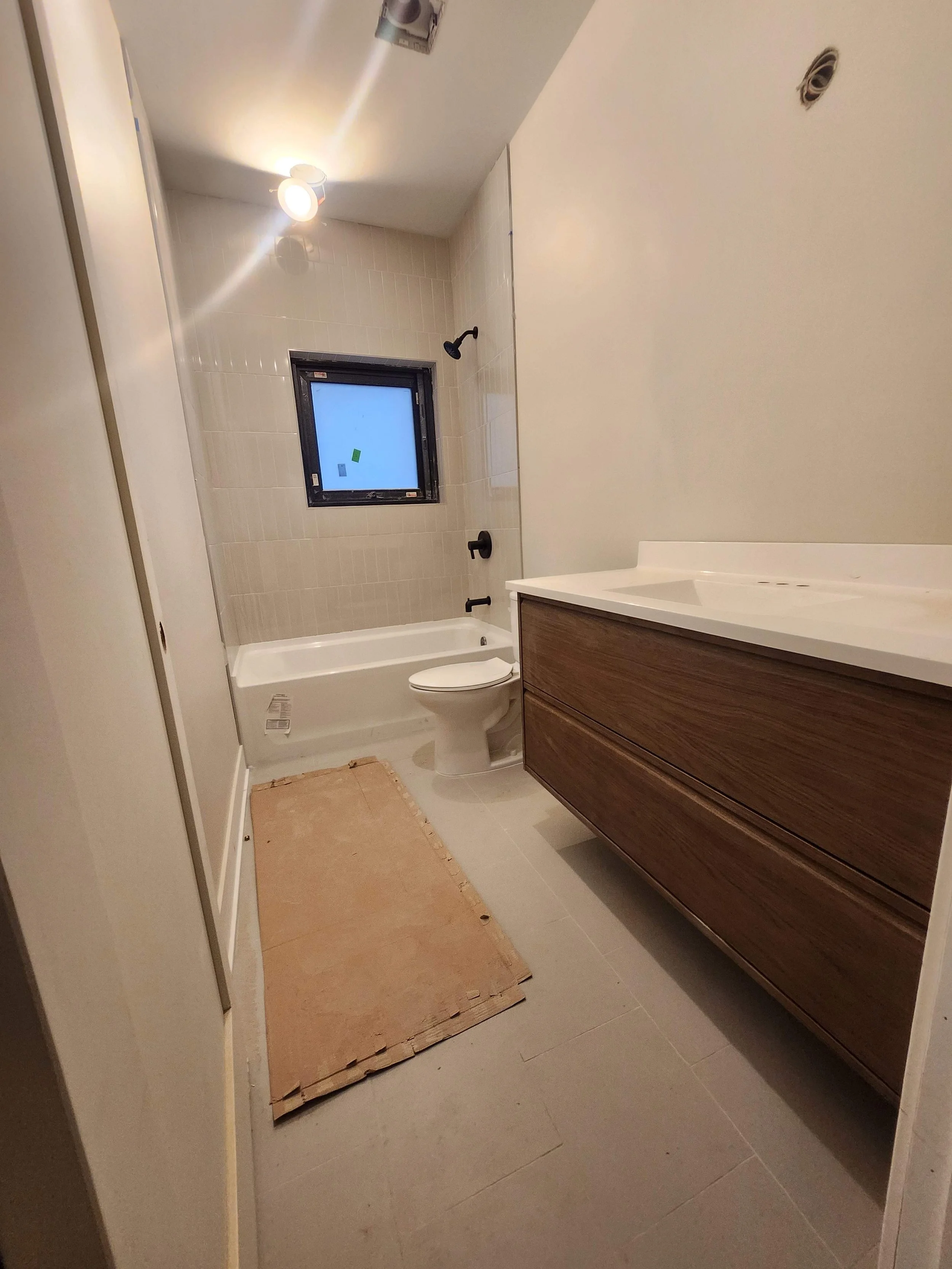
03/14/25
Tile work has been continuous since February, and is finally close to completion.
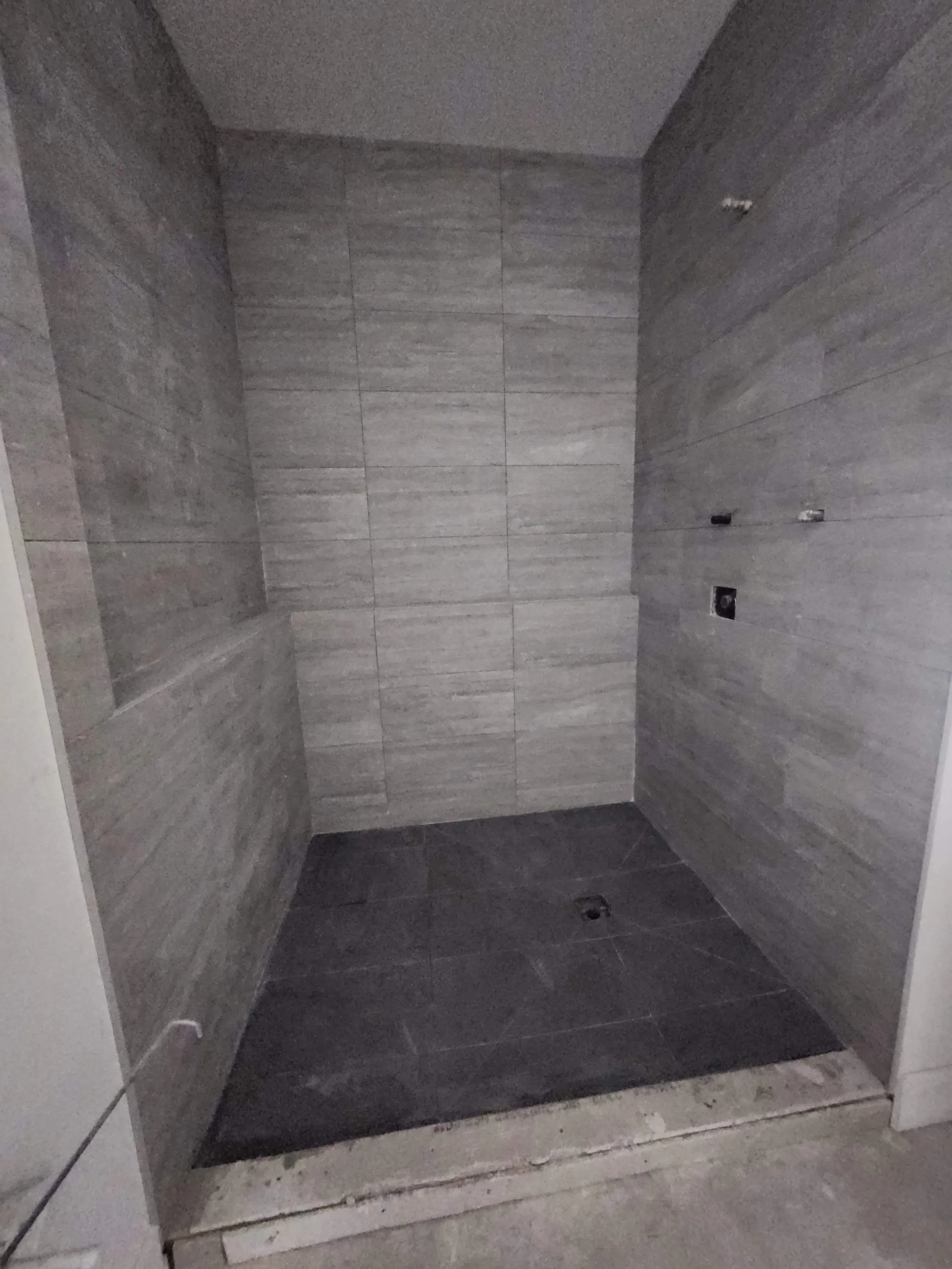

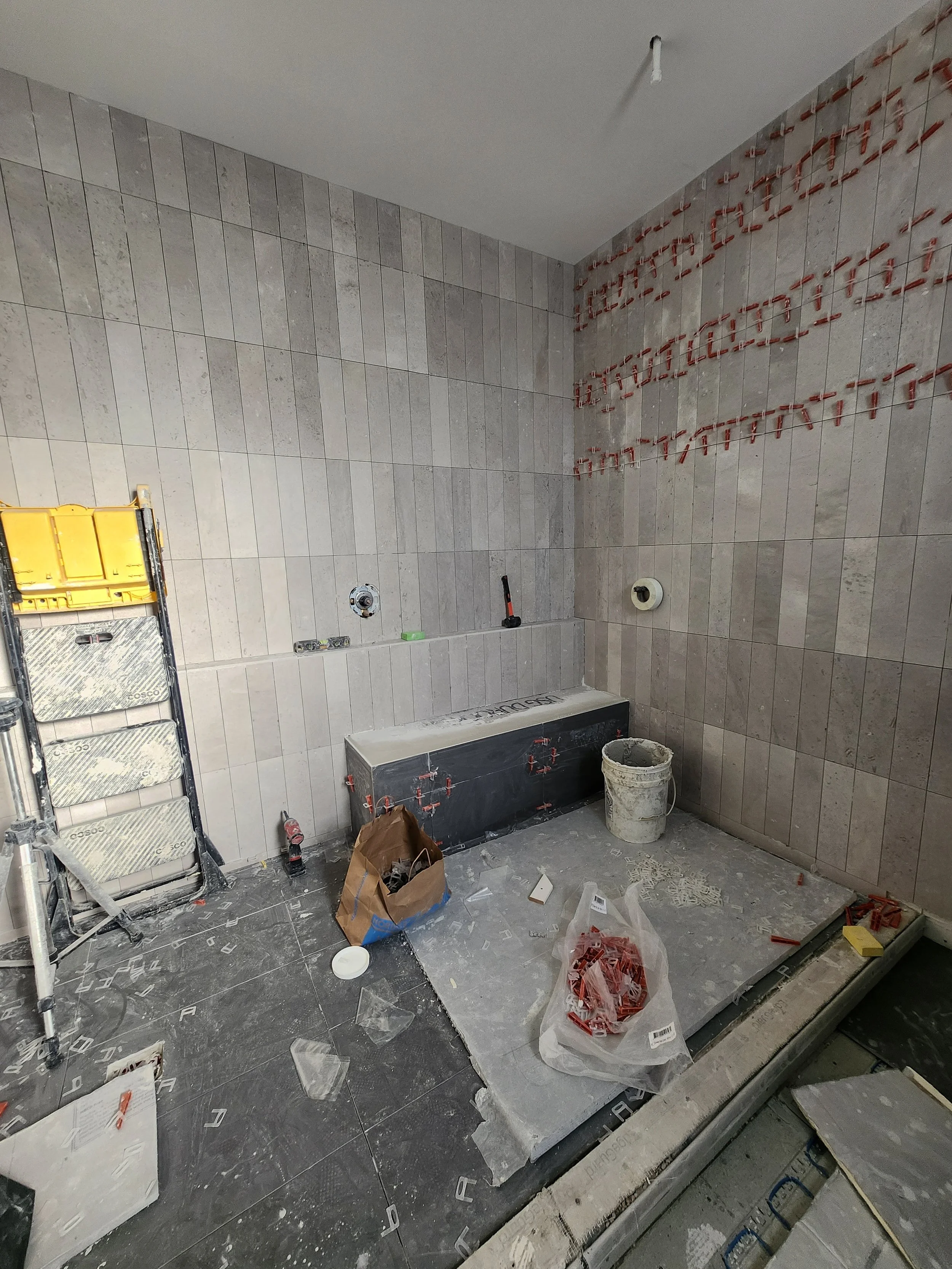
03/10/25
We’e finally made some good progress on the siding, and it’s looking sharp! The idea was to mimic the pattern of the steel beams of a Mies van der Rohe building.
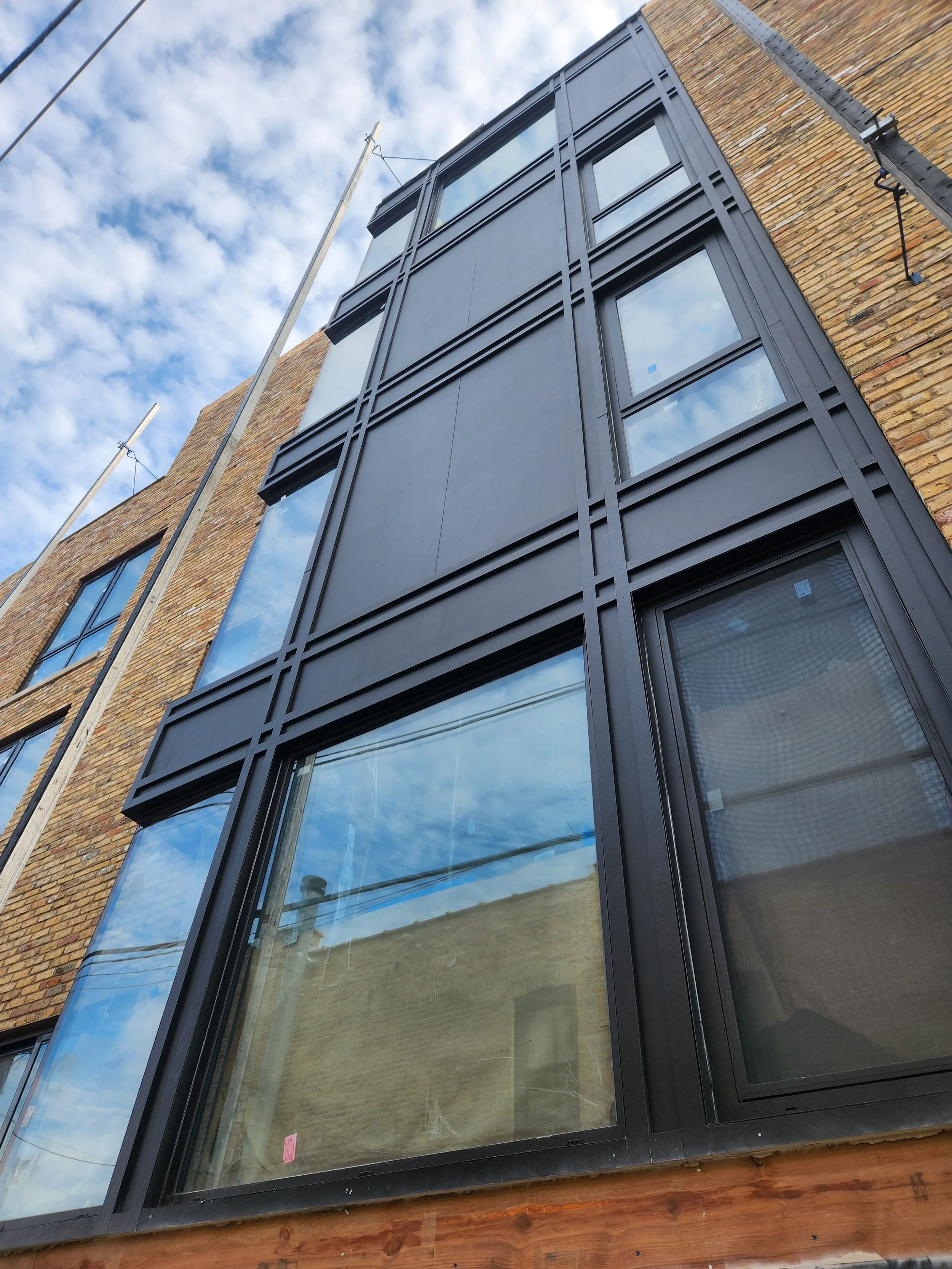

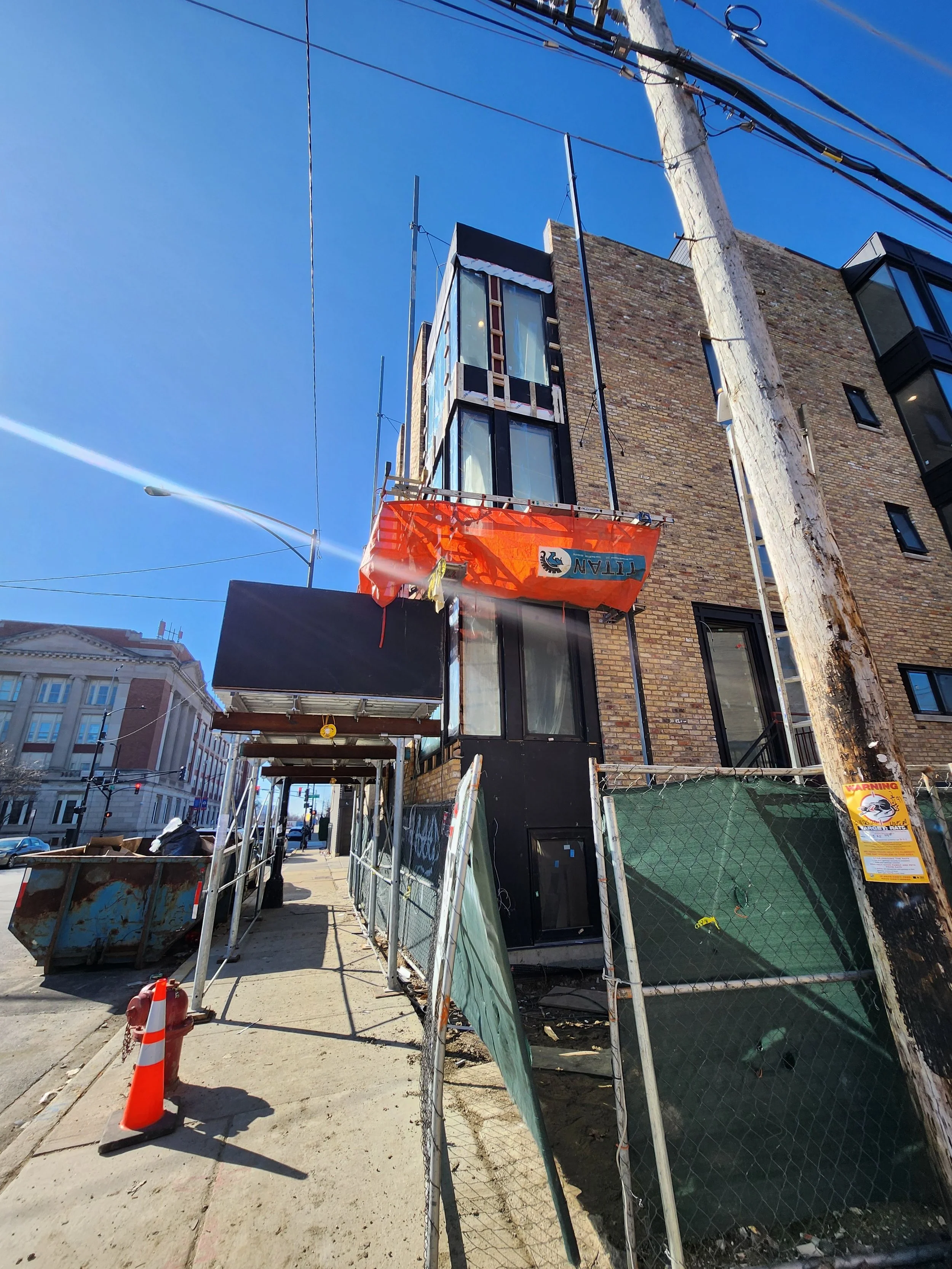

03/03/25
WE HAVE POWER!!!
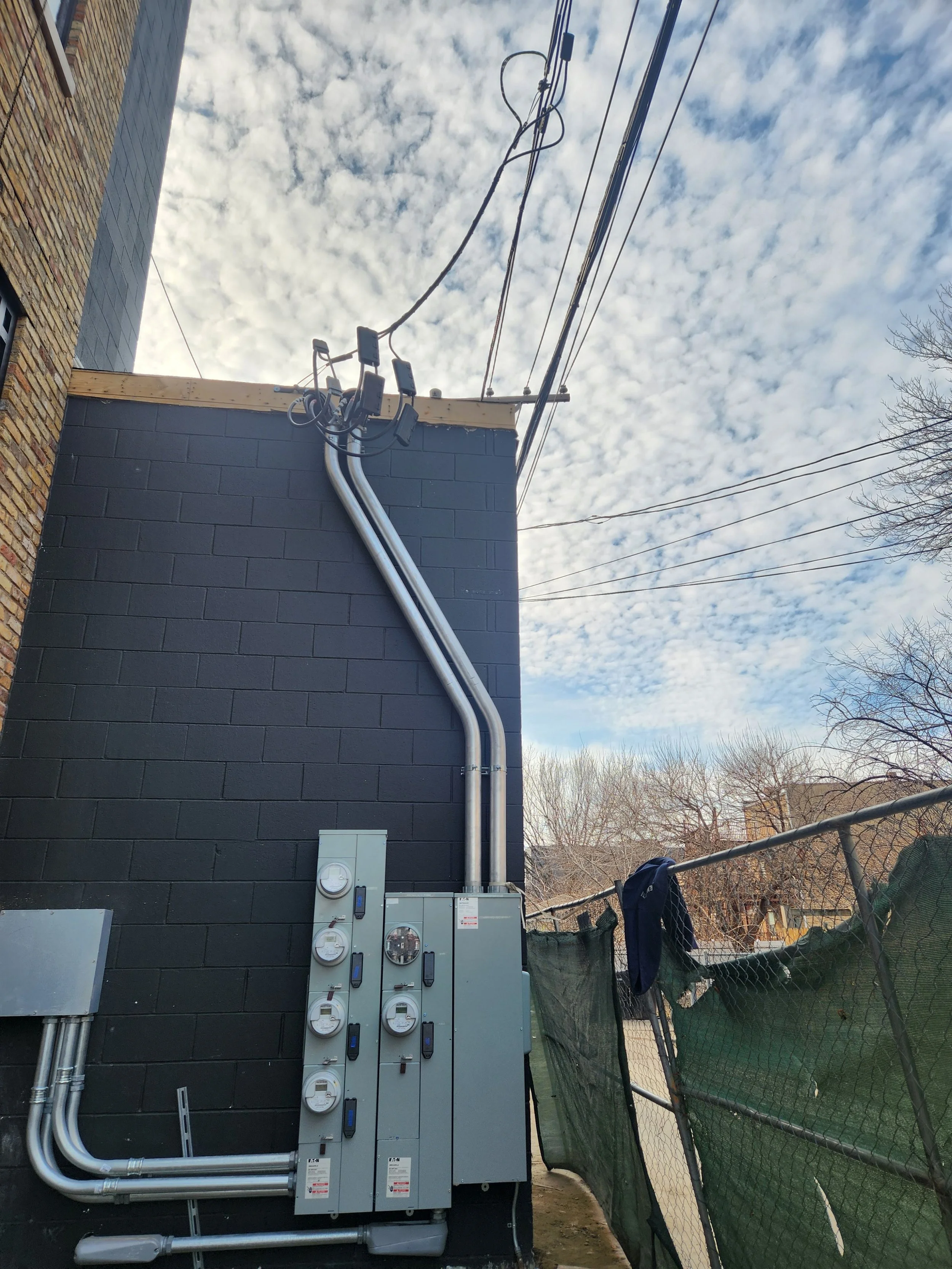
02/26/25
We started to install the cable for the heated bathroom floors. During installation a special device - the “loudmouth” - is attached to the cable to alert us of any damage during installation. Thankfully the cable remained fully intact by the completion of the job - phew!
Tile work continued on the showers, and the trim carpenters started making progress on door, casing and base trim installation.
ComEd ALMOST gave just power on Monday. But they only finished the overhead cable run. They’ve promised we’ll have our service connected by the end of the week……fingers crossed!
The siding is finally starting to come together as well - it’s nice to see the exterior of the building progress after being paused by all the cold weather we’ve had.
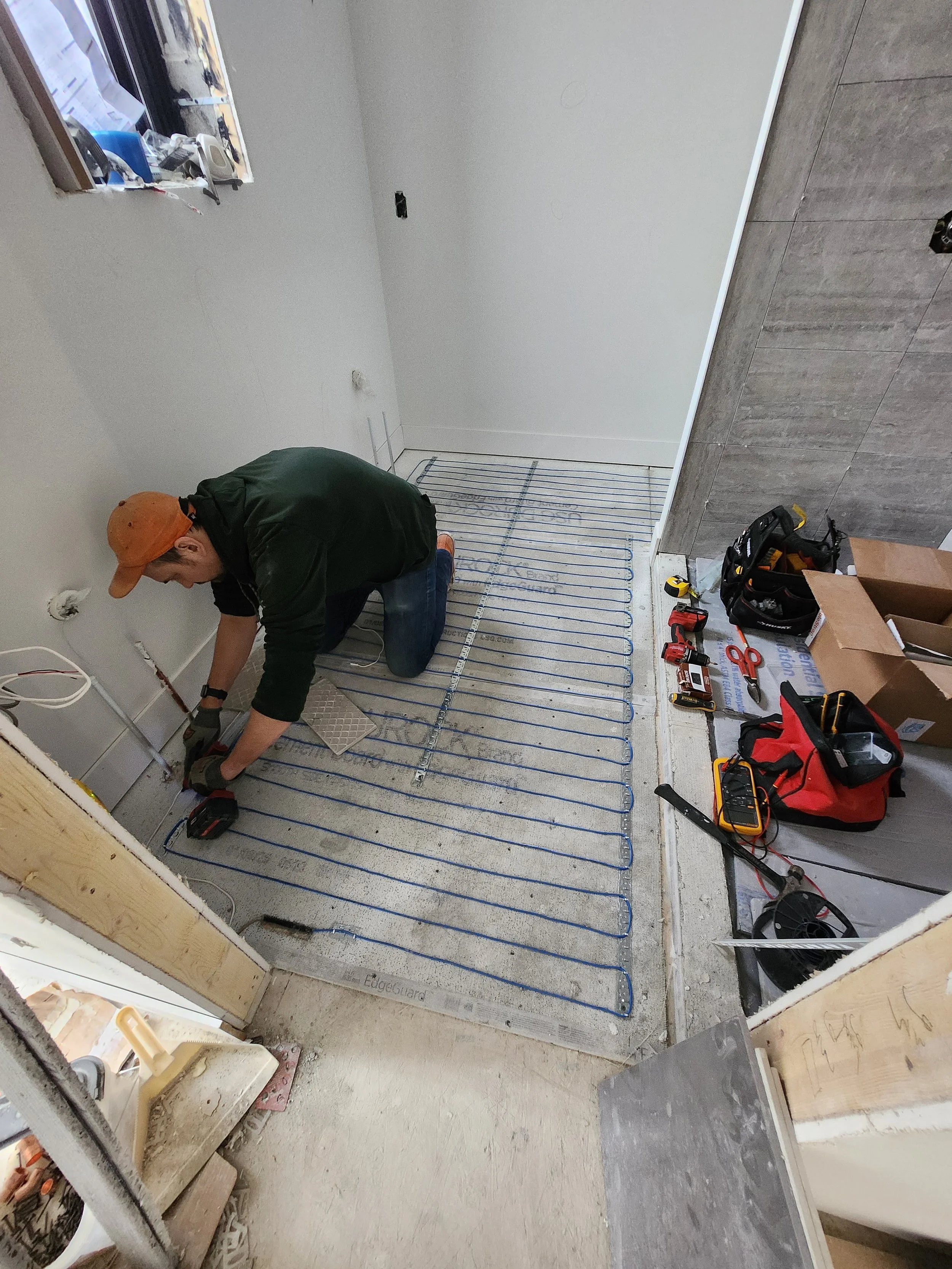
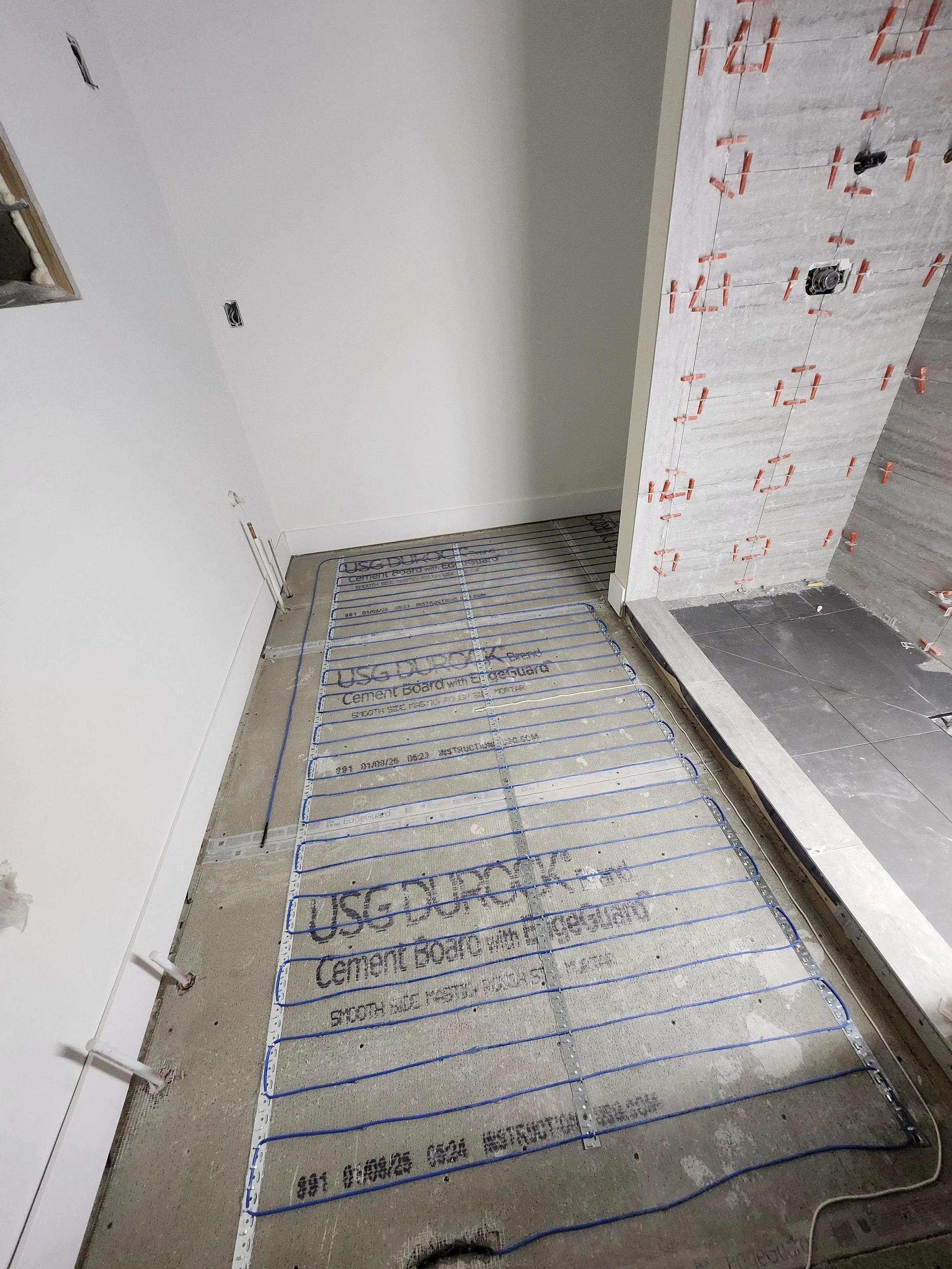
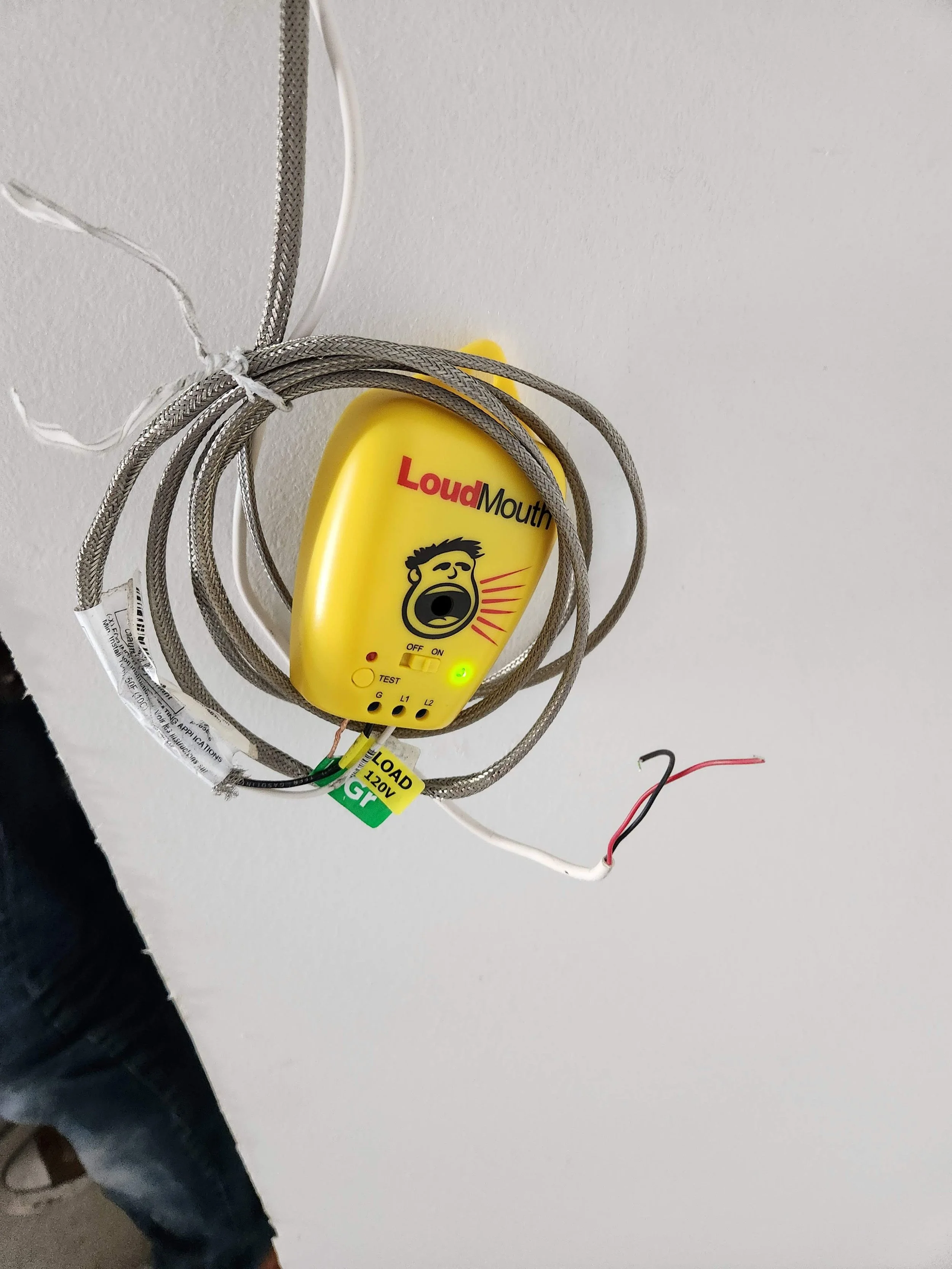
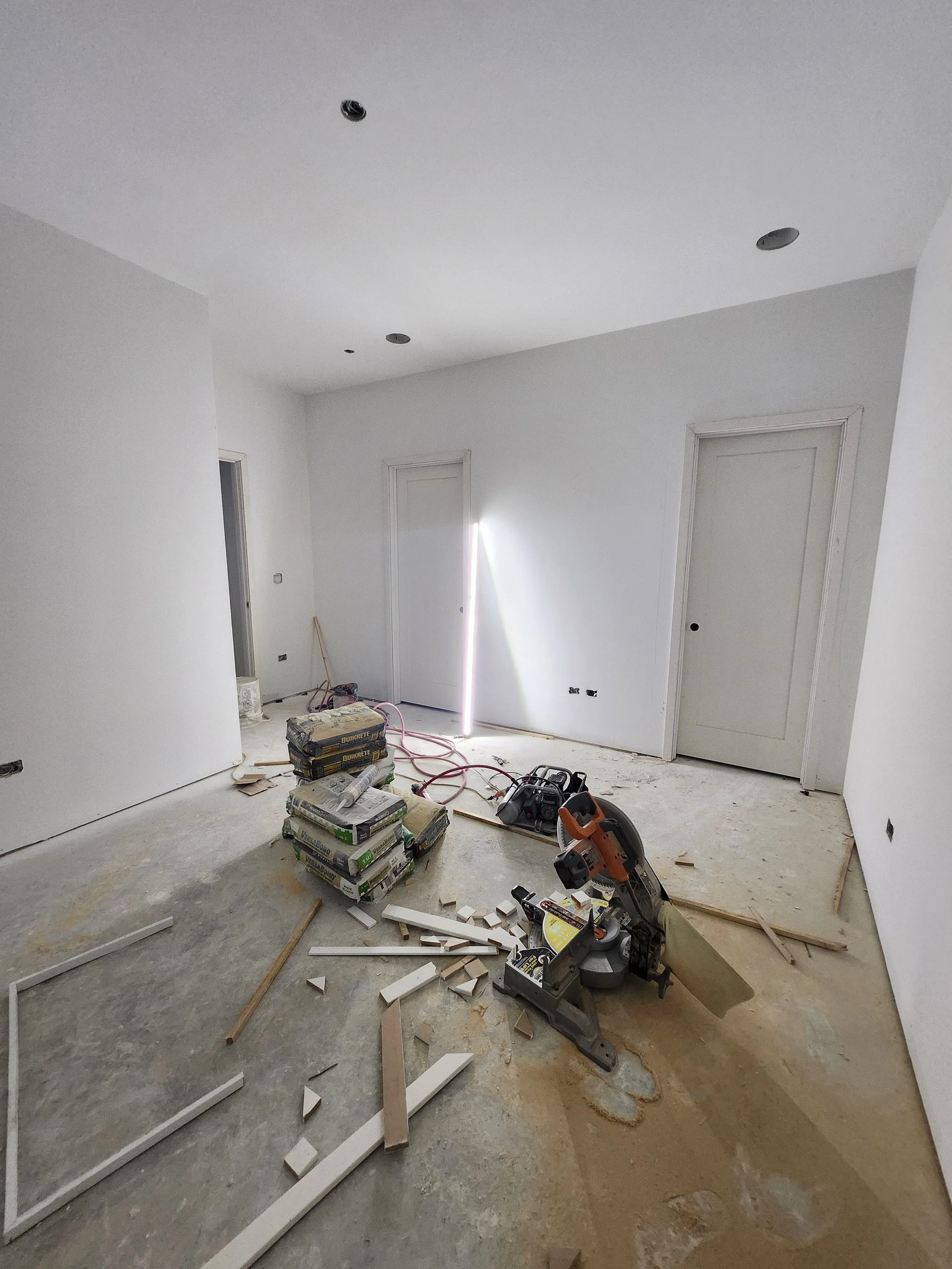
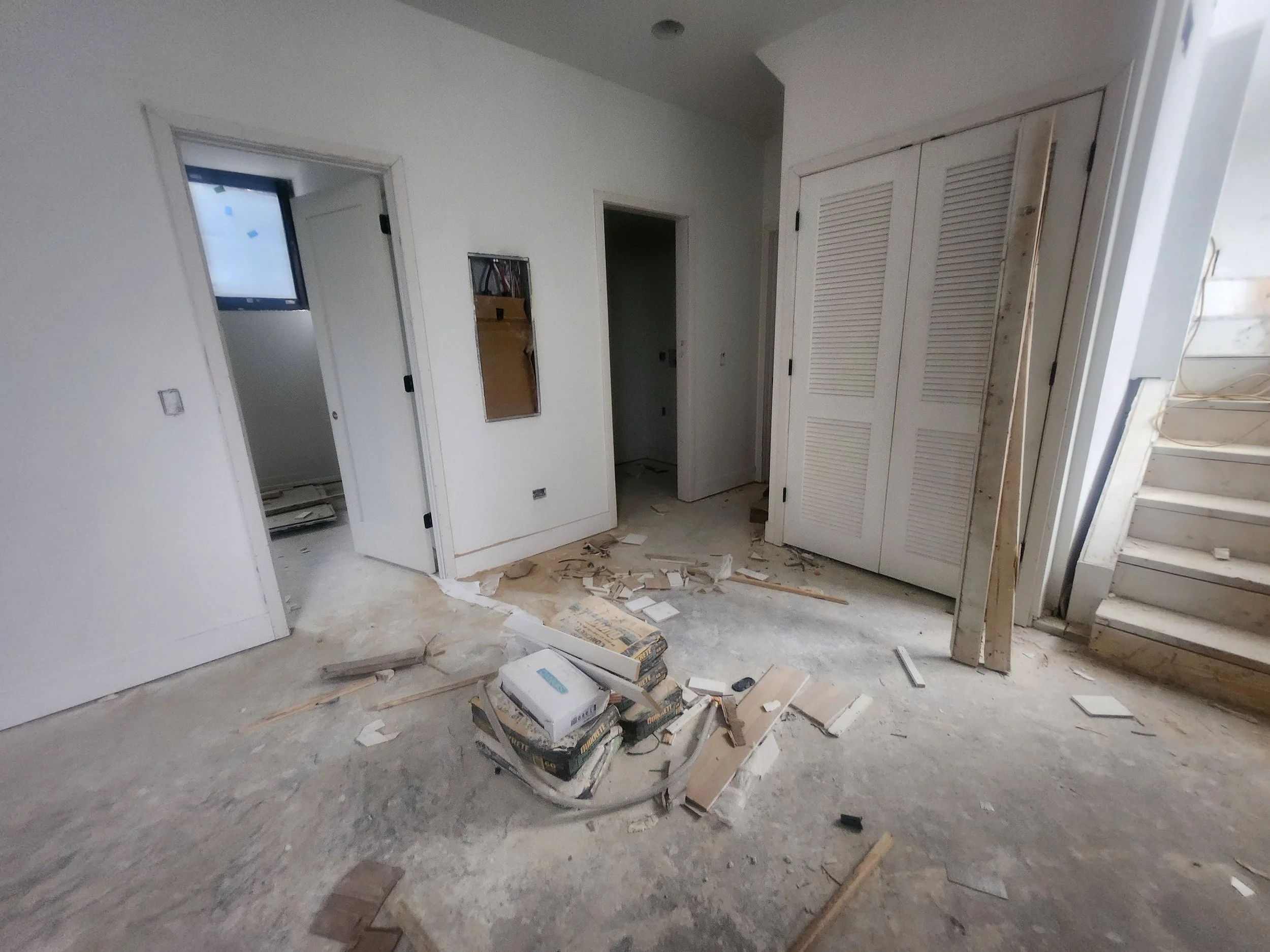
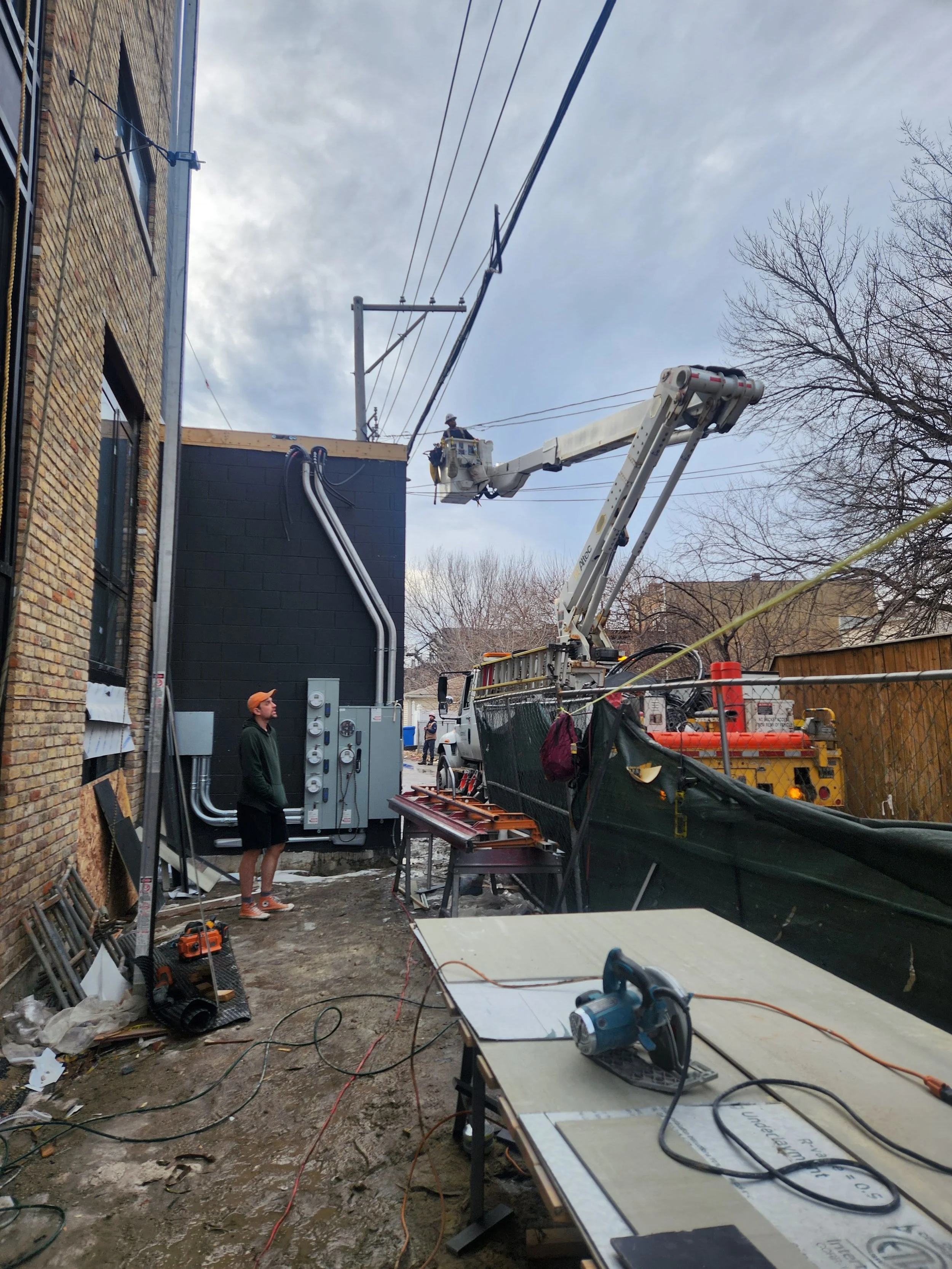


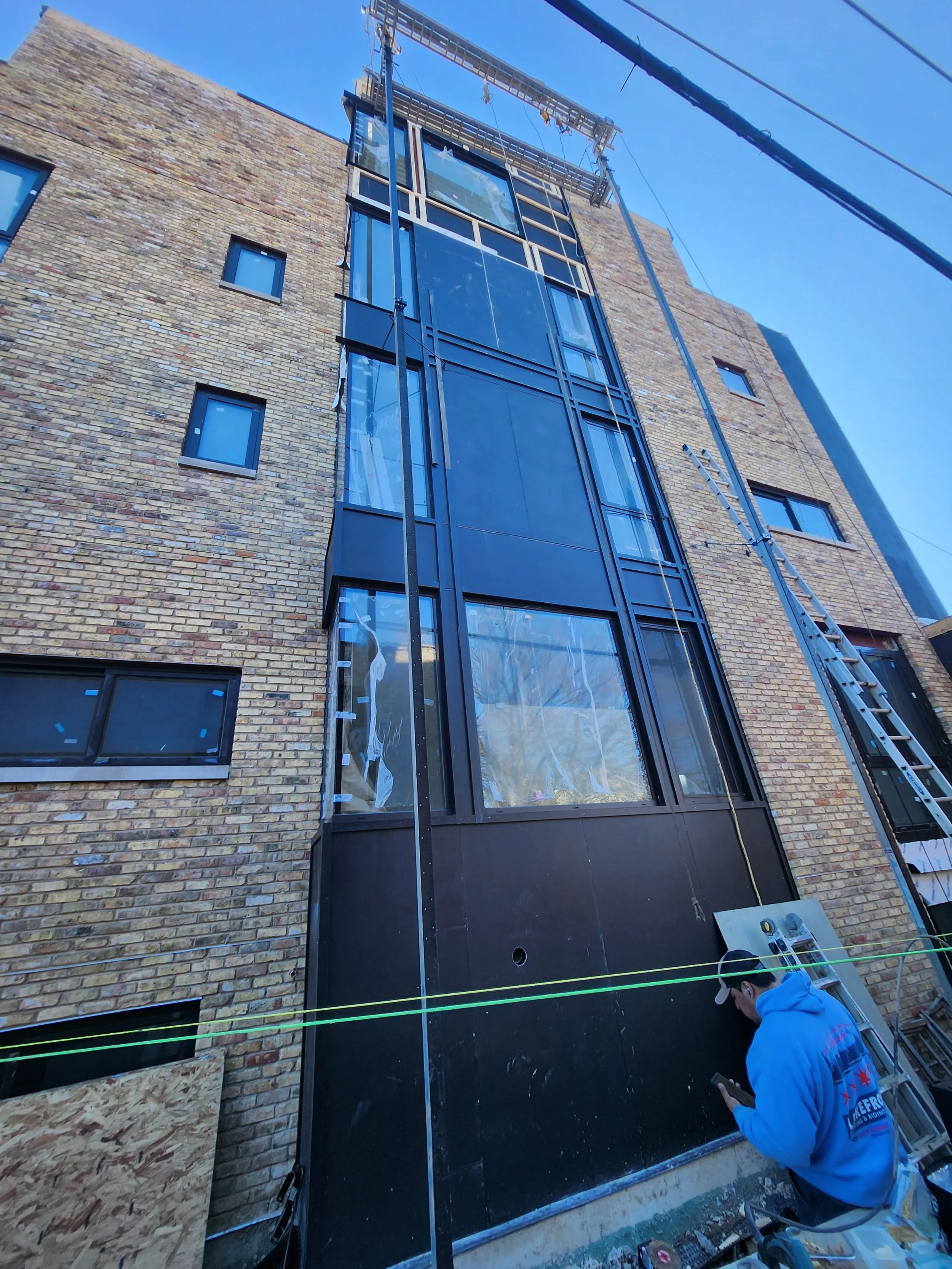
02/11/25
Drywall is finished! They’ve hung, mudded, sanded and primed all walls and ceilings. We’ve started tile work and siding this week. And ComEd installed our meters. Still no power, but we are one step closer. The HVAC guys have installed the furnaces and heat pumps in anticipation of our power service connection later this month. And we caught a cool pic of the city view in the gloaming :).

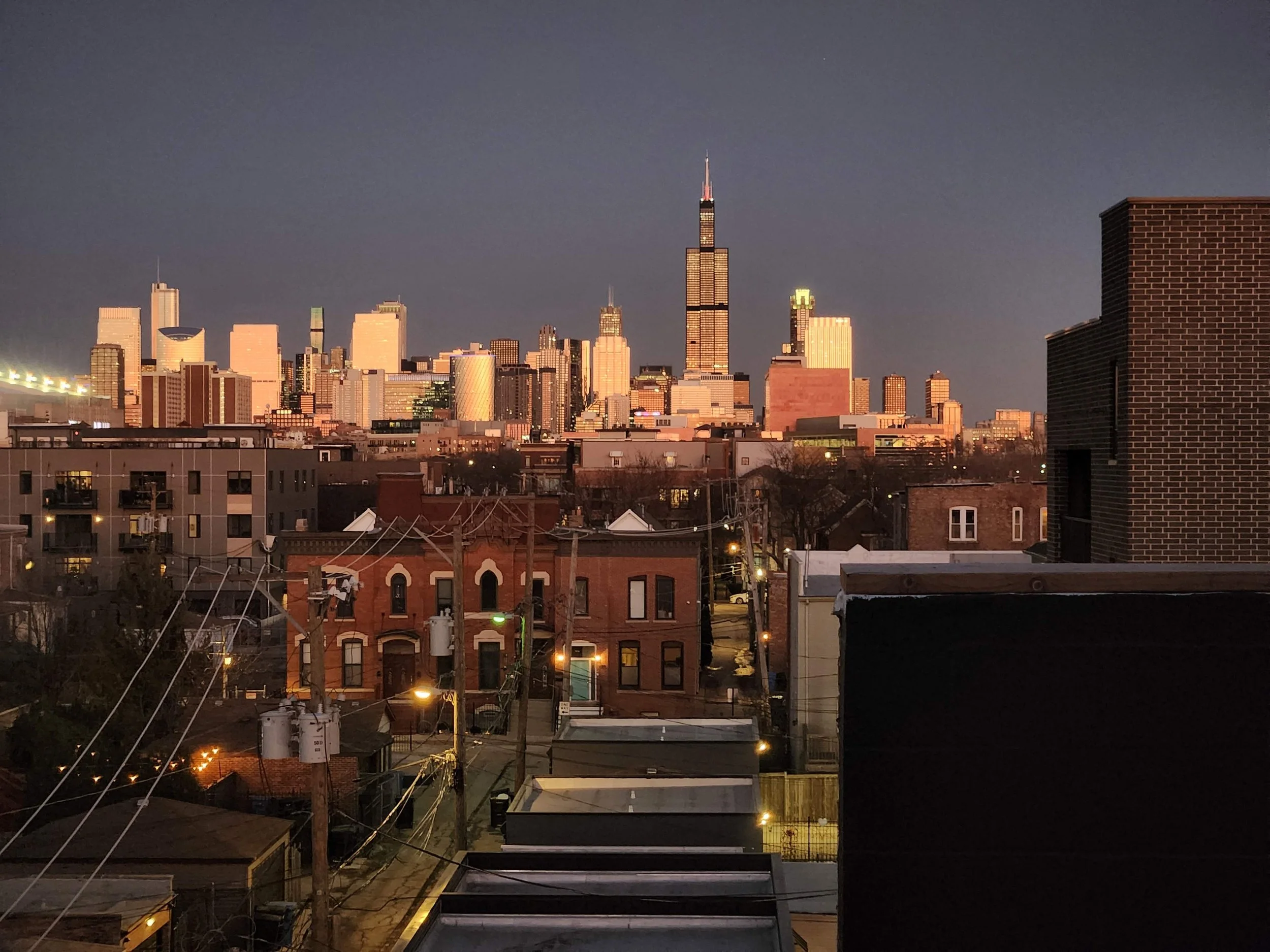



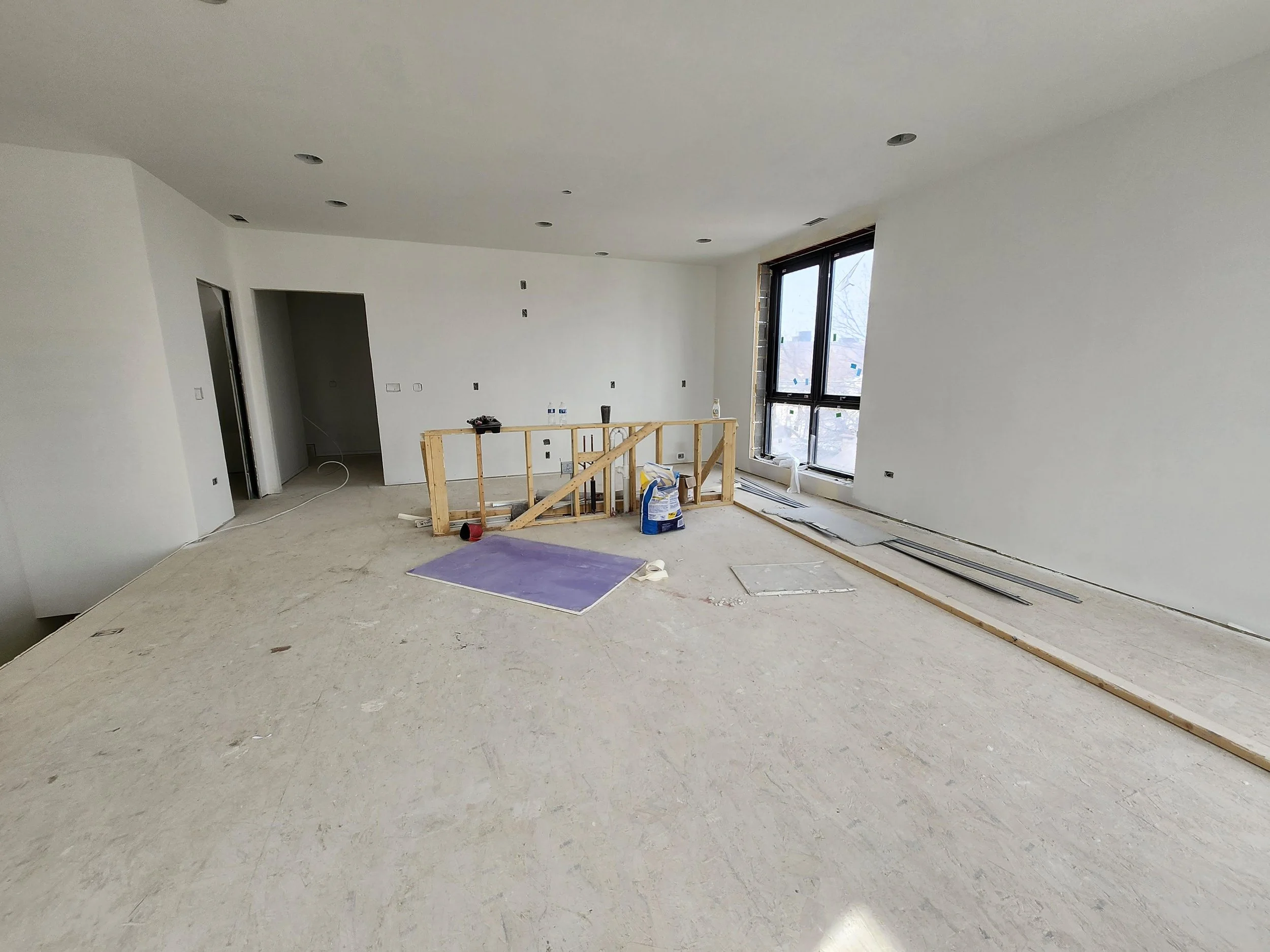


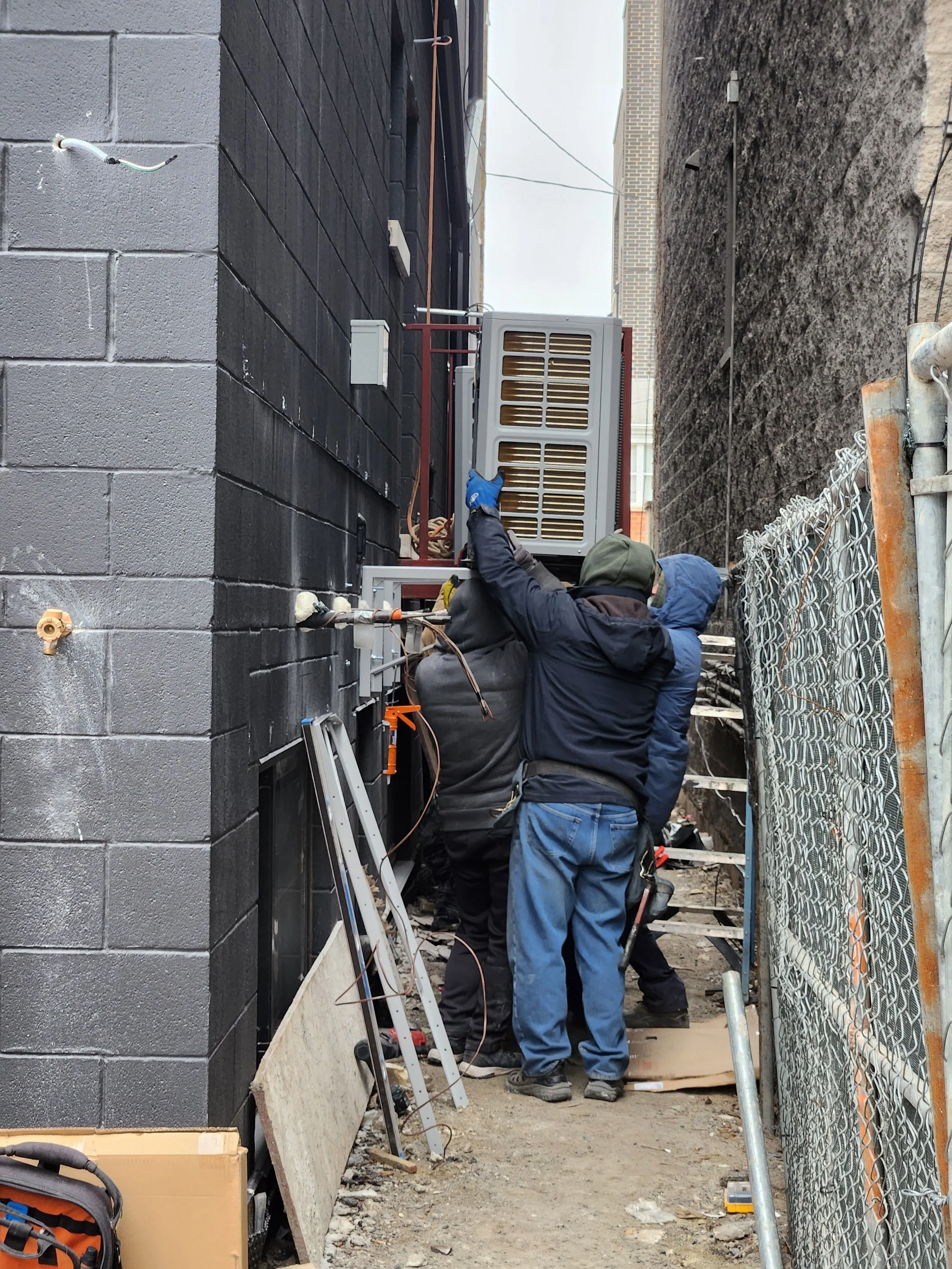
01/09/25
Happy New Year! The insulators have finished the closed-cell spray foam on the exterior walls, the sound batts at unit demising and bathroom walls, and the blown-in cellulose in the floors for sound mitigation between units. This week, the drywallers have been hanging drywall. They’ve been super fast and will be done by the end of the week! Next week they will start to mud and tape the drywall.
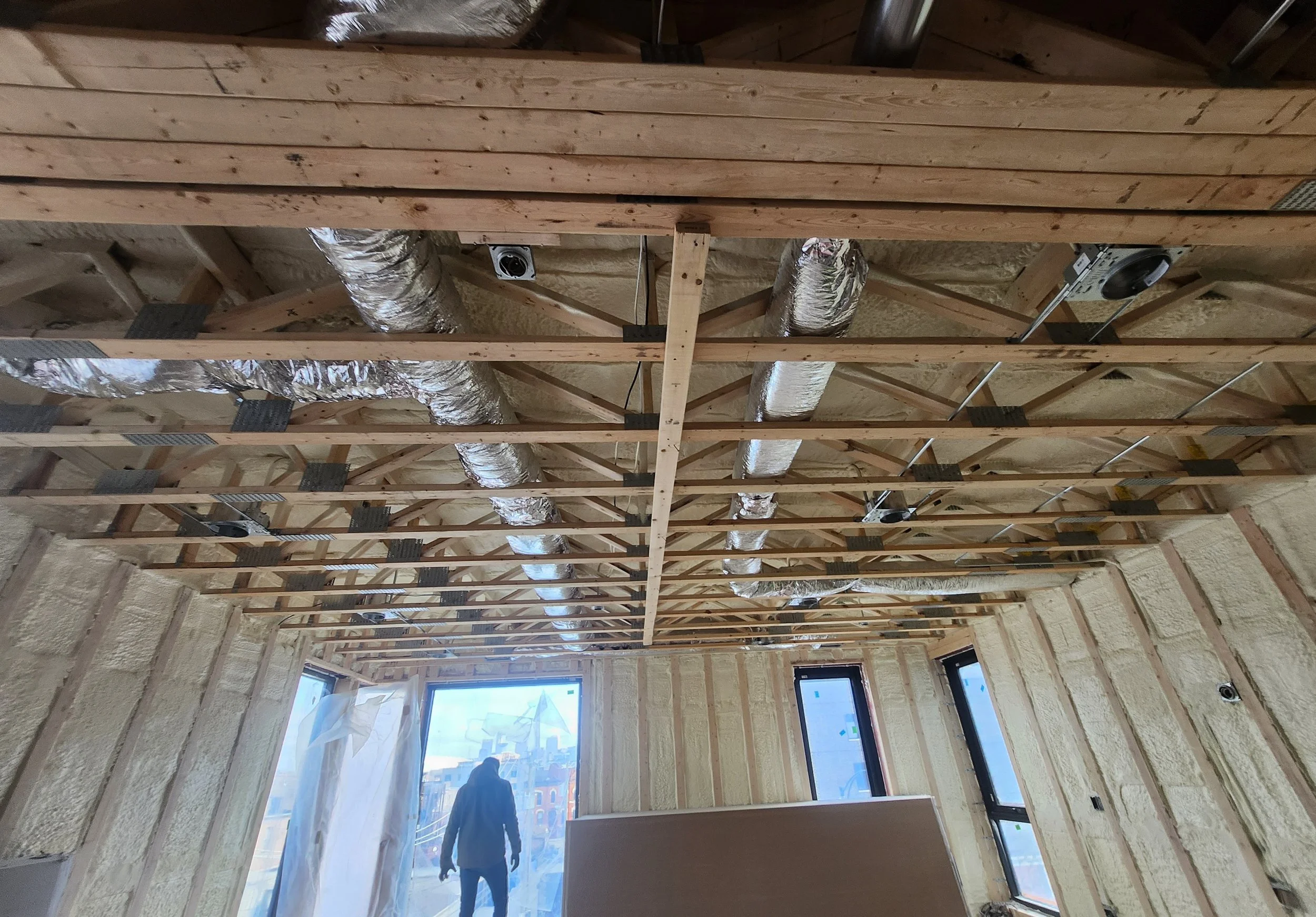


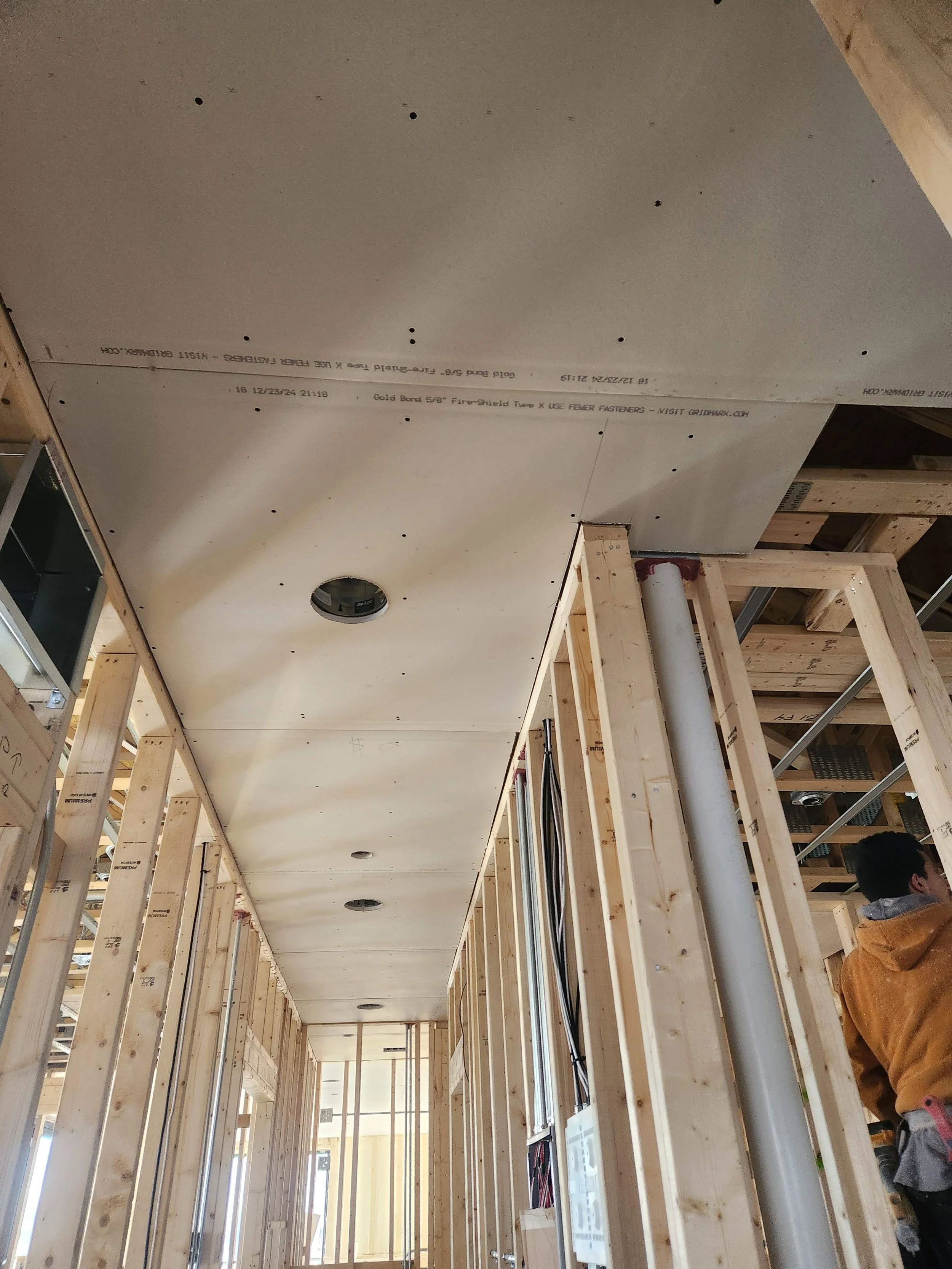

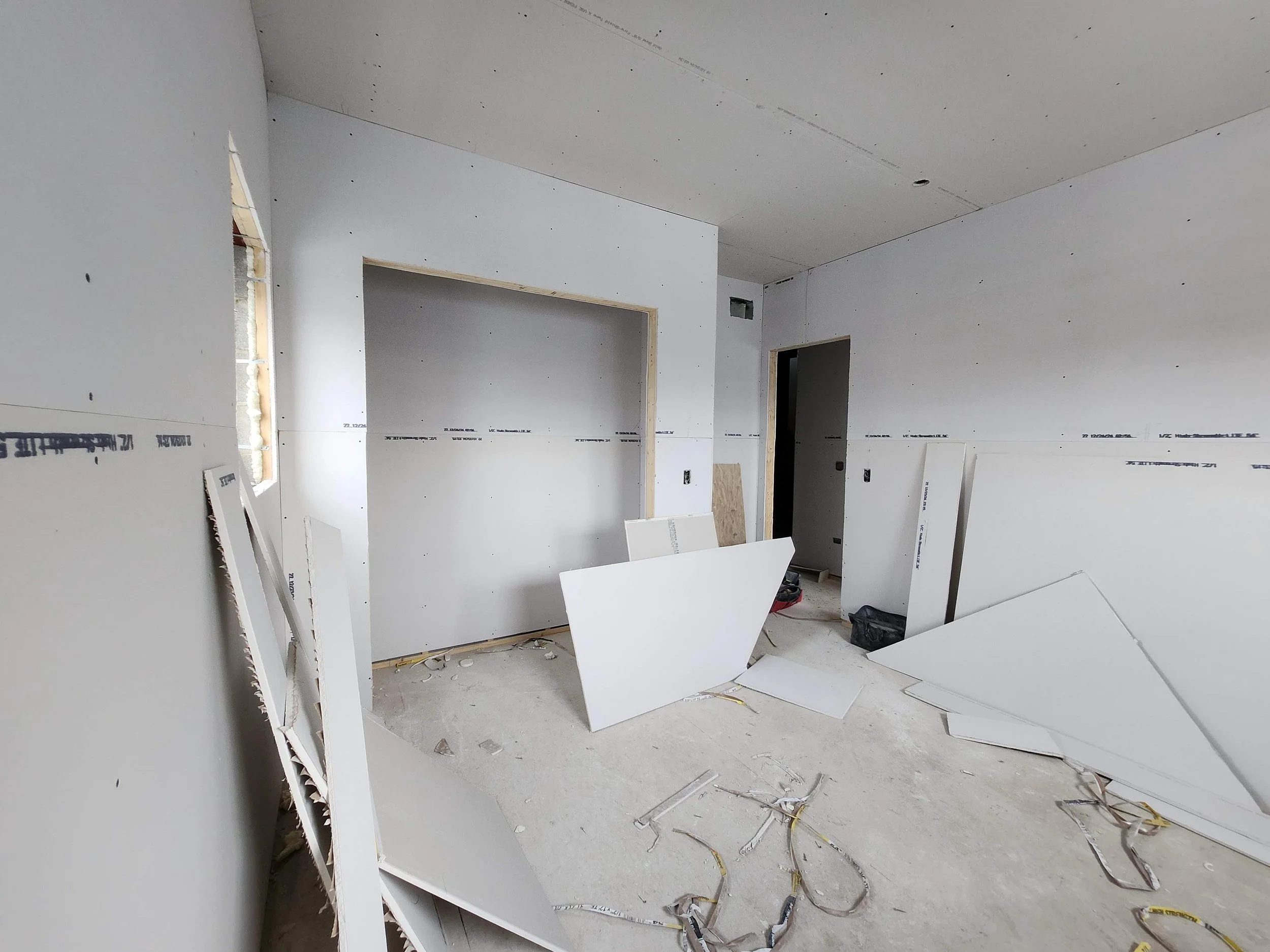
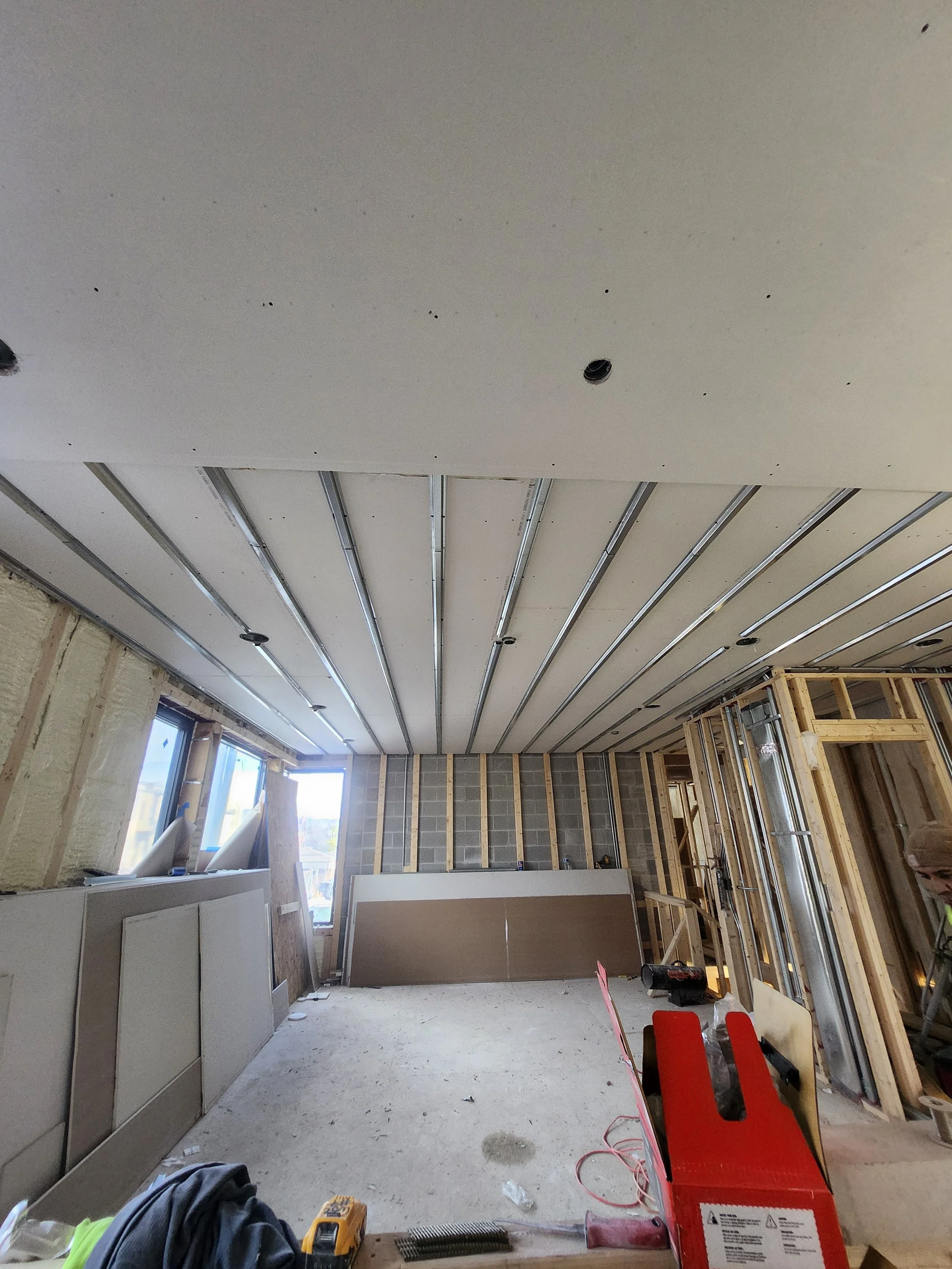

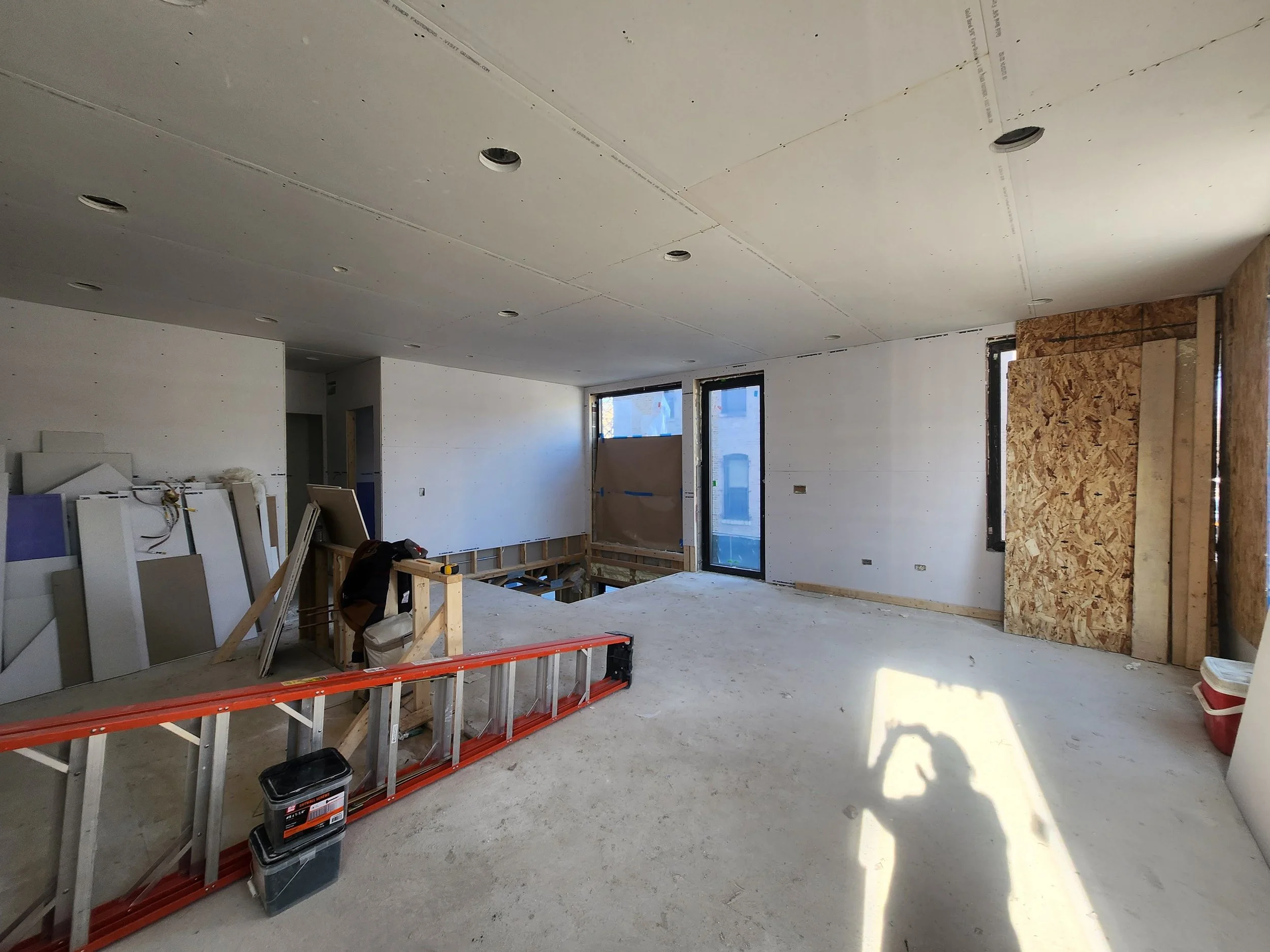
12/19/24
We passed all of our rough inspections!!! We are cleared to begin insulation and drywall. We also got our fire-stopping done today (the red putty), which provides fire resistance where there are penetrations by pipes and ducts in fire-rated walls and floors.


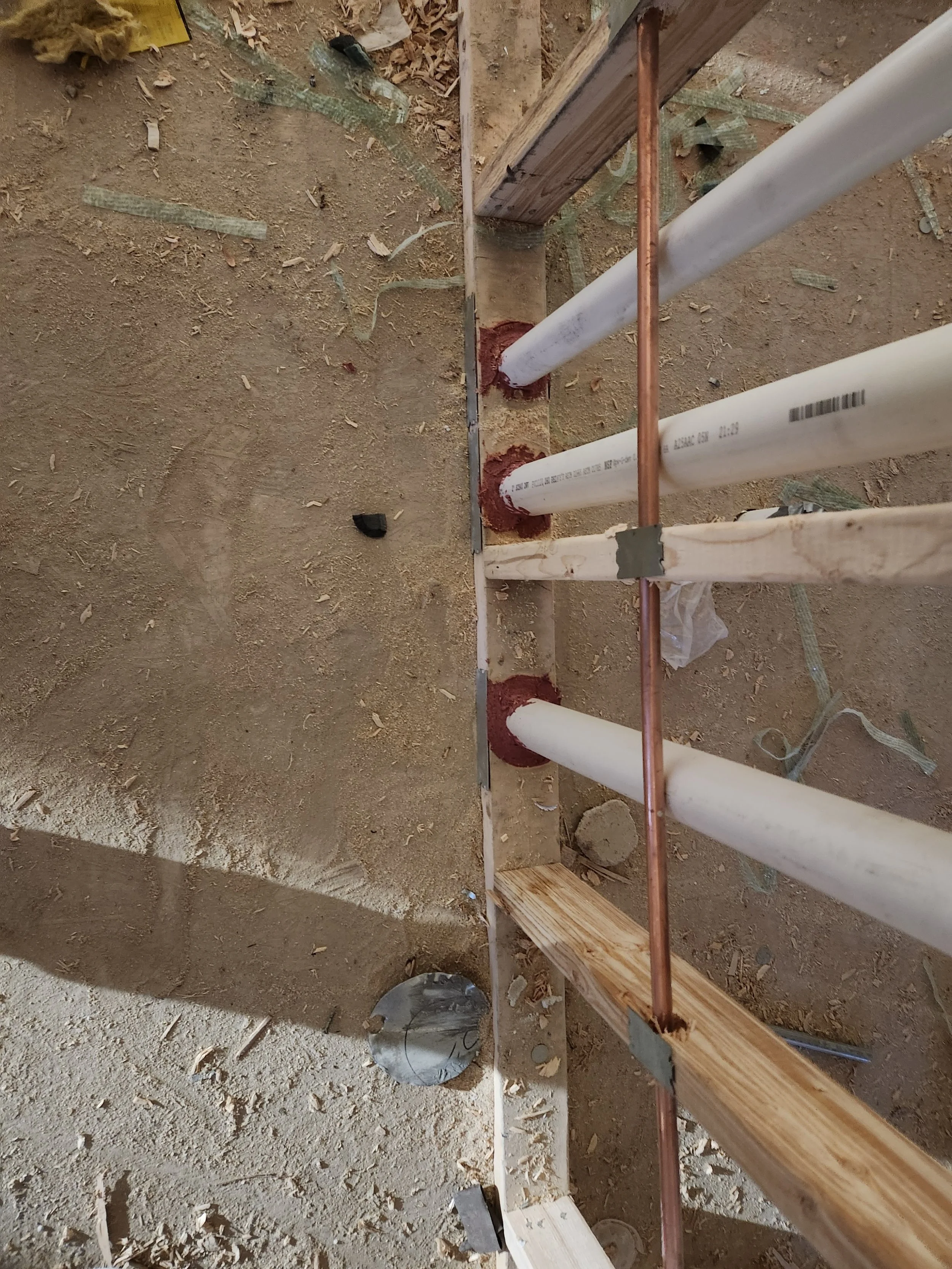
12/17/24
Our specialty windows are being installed this week - we’ve got accordion patio doors and corner windows. And the rough plumbing, electrical and HVAC installation is ongoing and will be ready for inspection this week! Look at those beefy cables bringing power to each unit! It was a feat getting those things through the conduit!

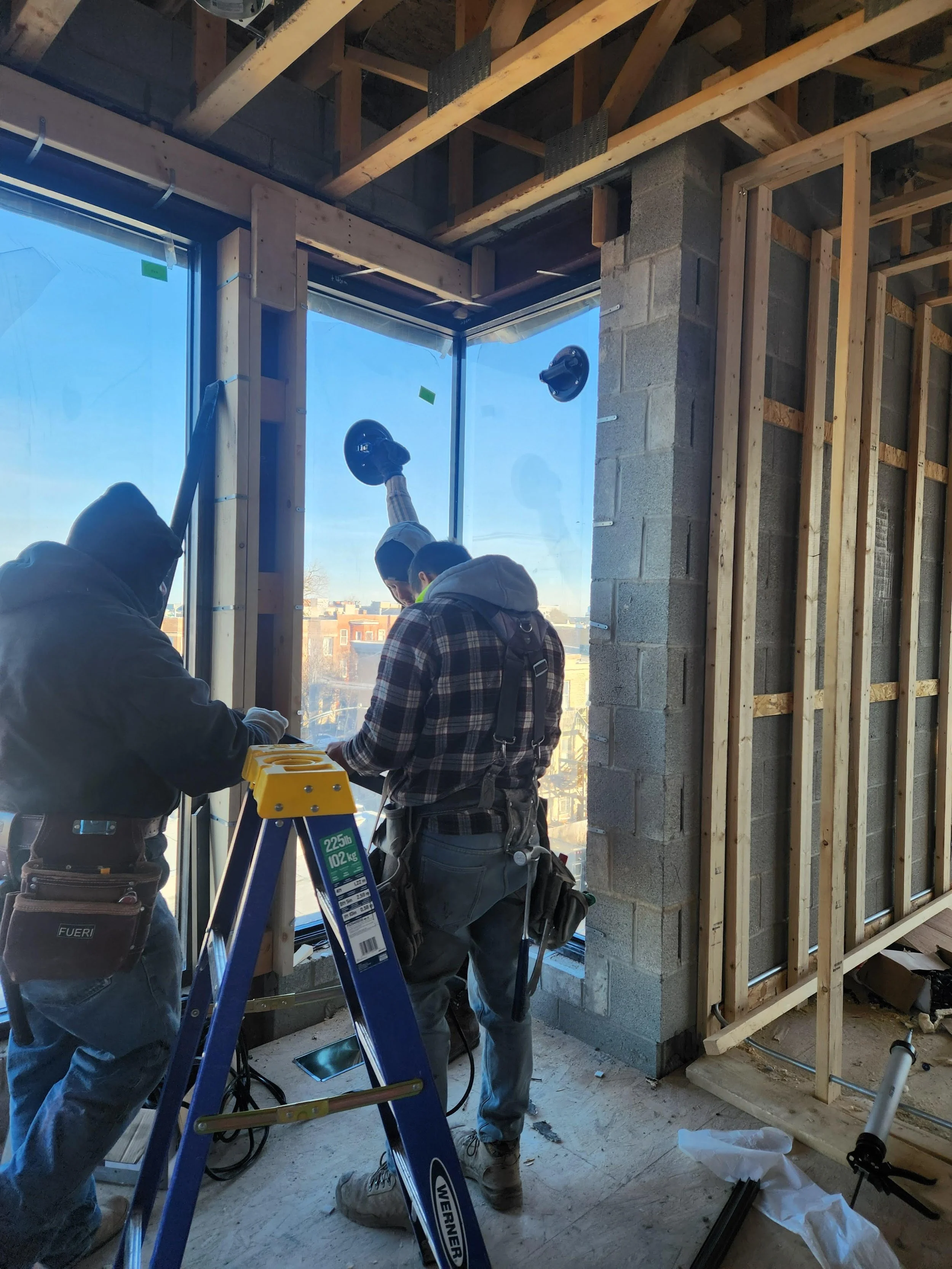

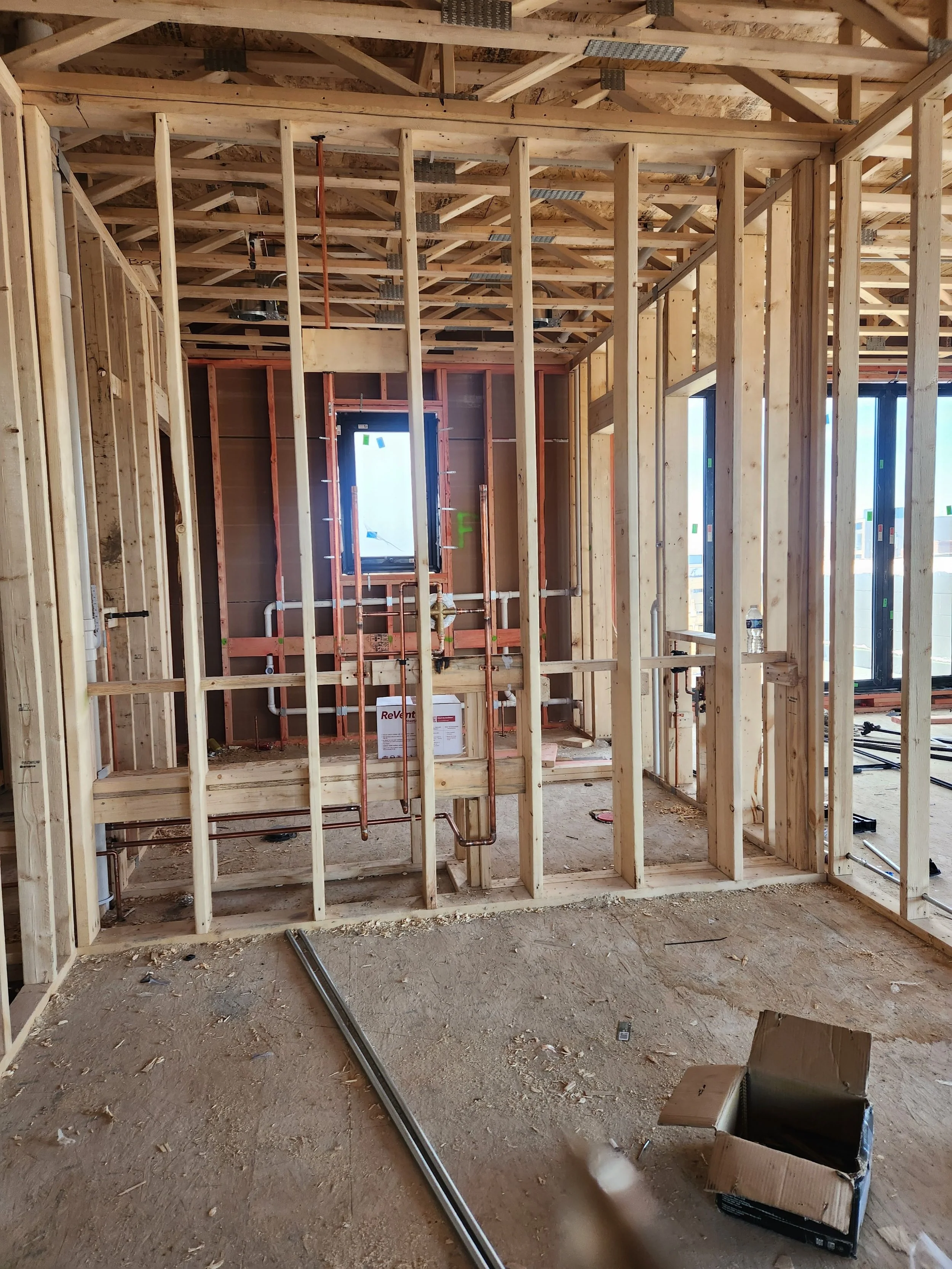



11/27/24
Our windows were delivered from China through the port of Los Angeles, and installation is going smoothly so far. Next week, the corner windows and folding doors will be assembled and installed.







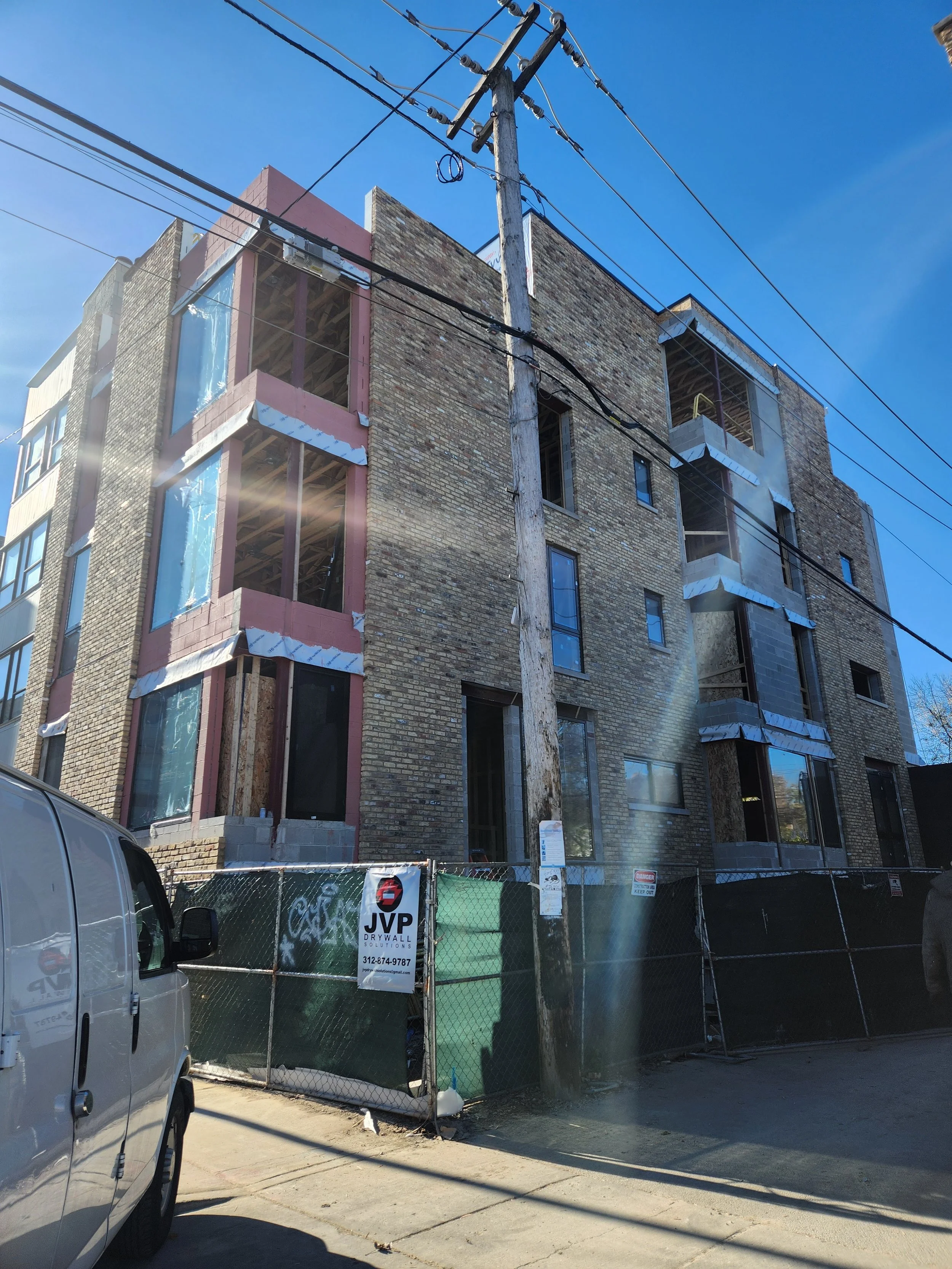
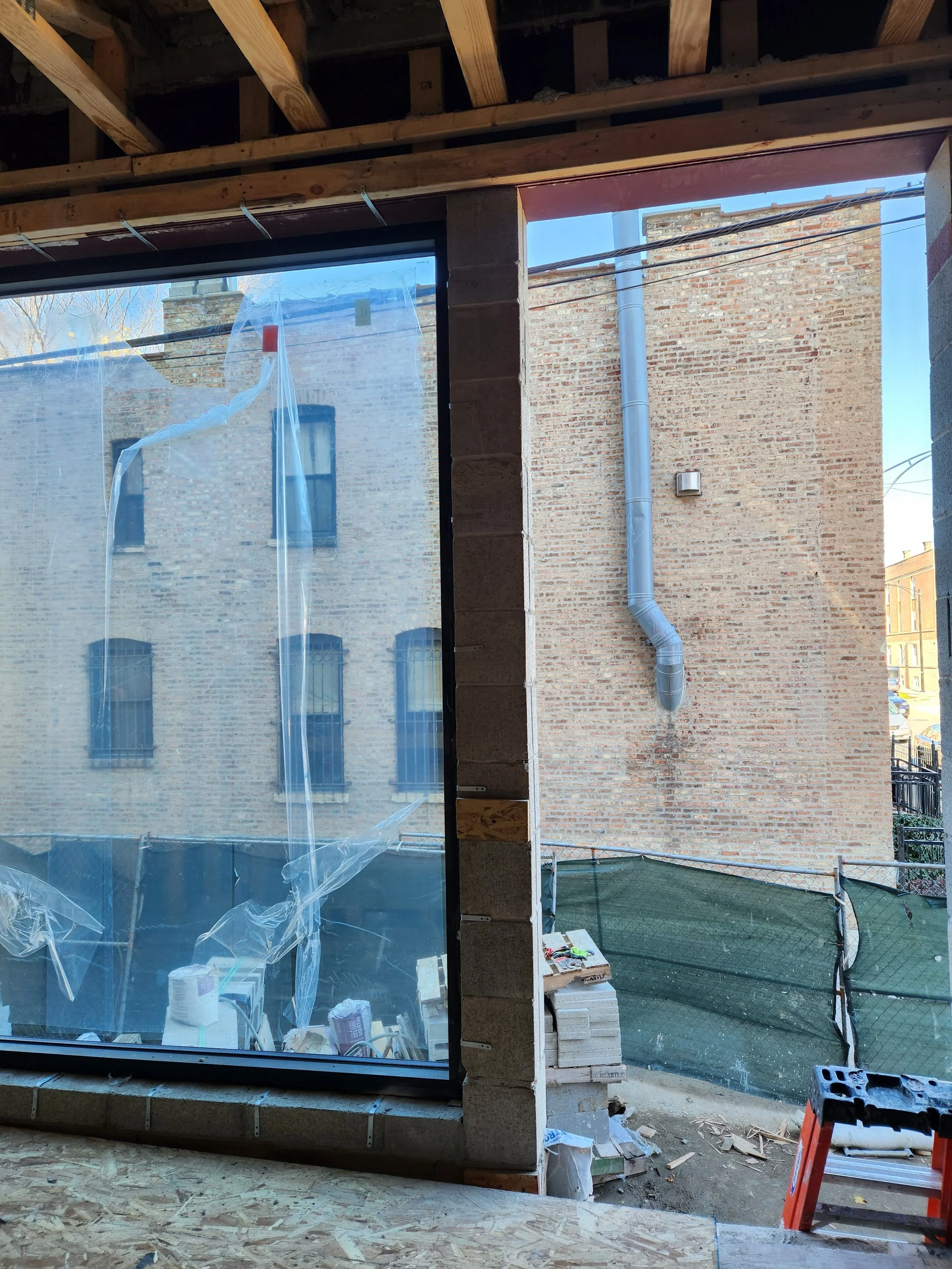
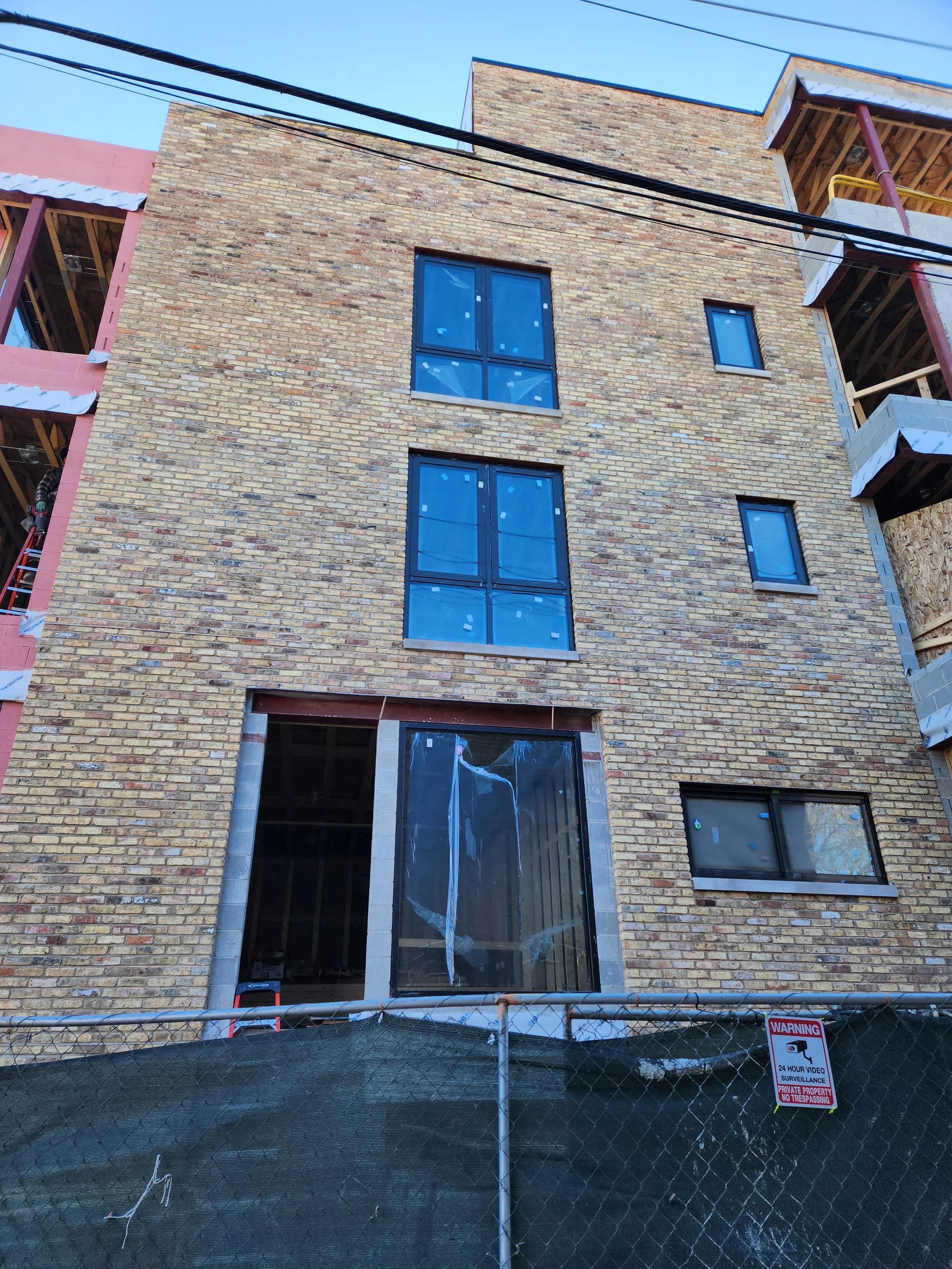
11/25/24
Now that the main part of the building has been built, we’ve moved on to the garage. The roof of the garage will have a deck for exclusive use by Unit 2. Even the garage deck has a bit of a view!

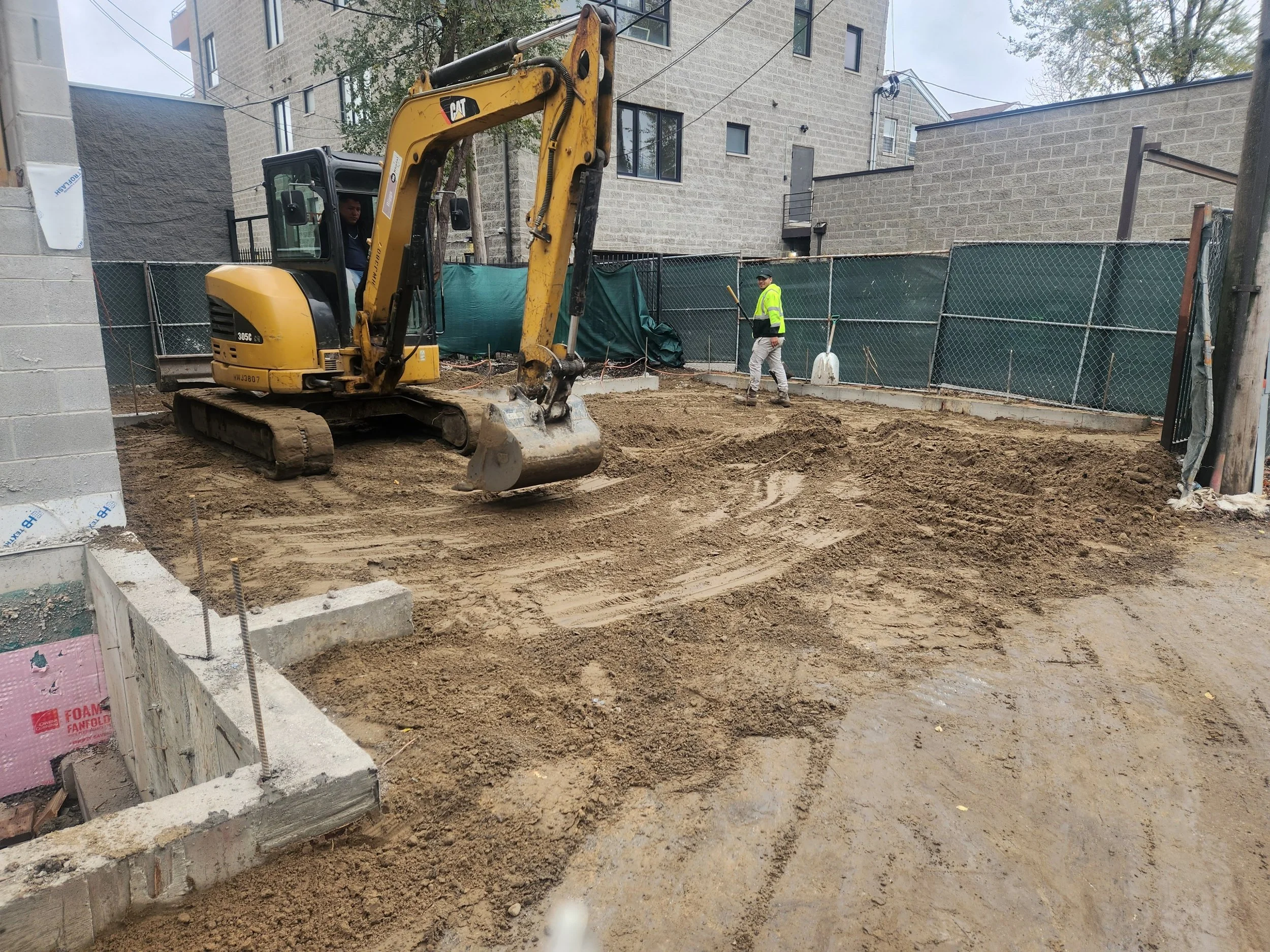


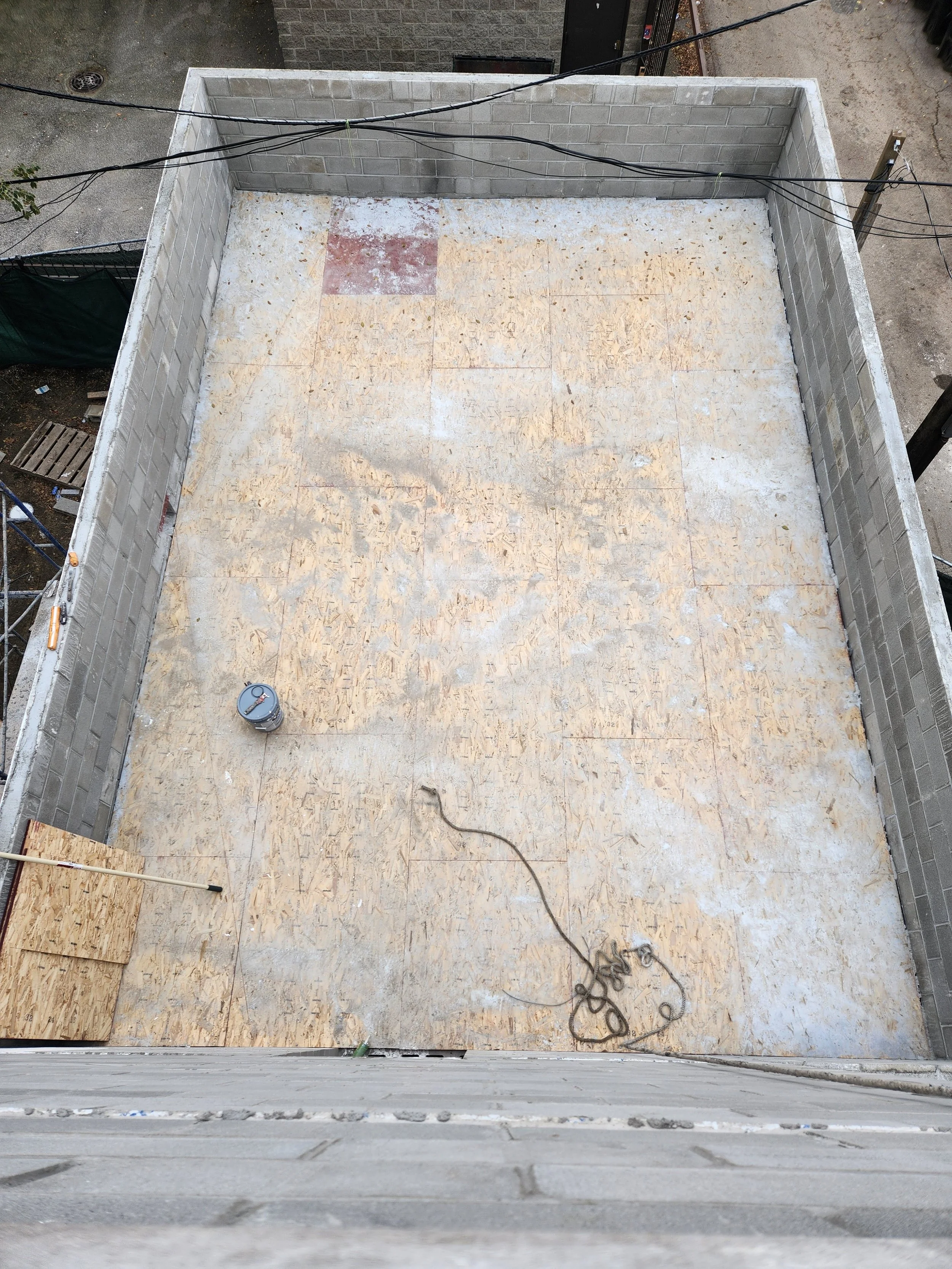
11/21/24
The plumbers have finished their waste piping, and are now working on copper. The HVAC guys have gotten ductwork installed for two of the units. The electricians have started installing conduit, and they’ve finished the service installation. We are ready for ComEd to connect us and give us meters! We’ll see how long that takes :)
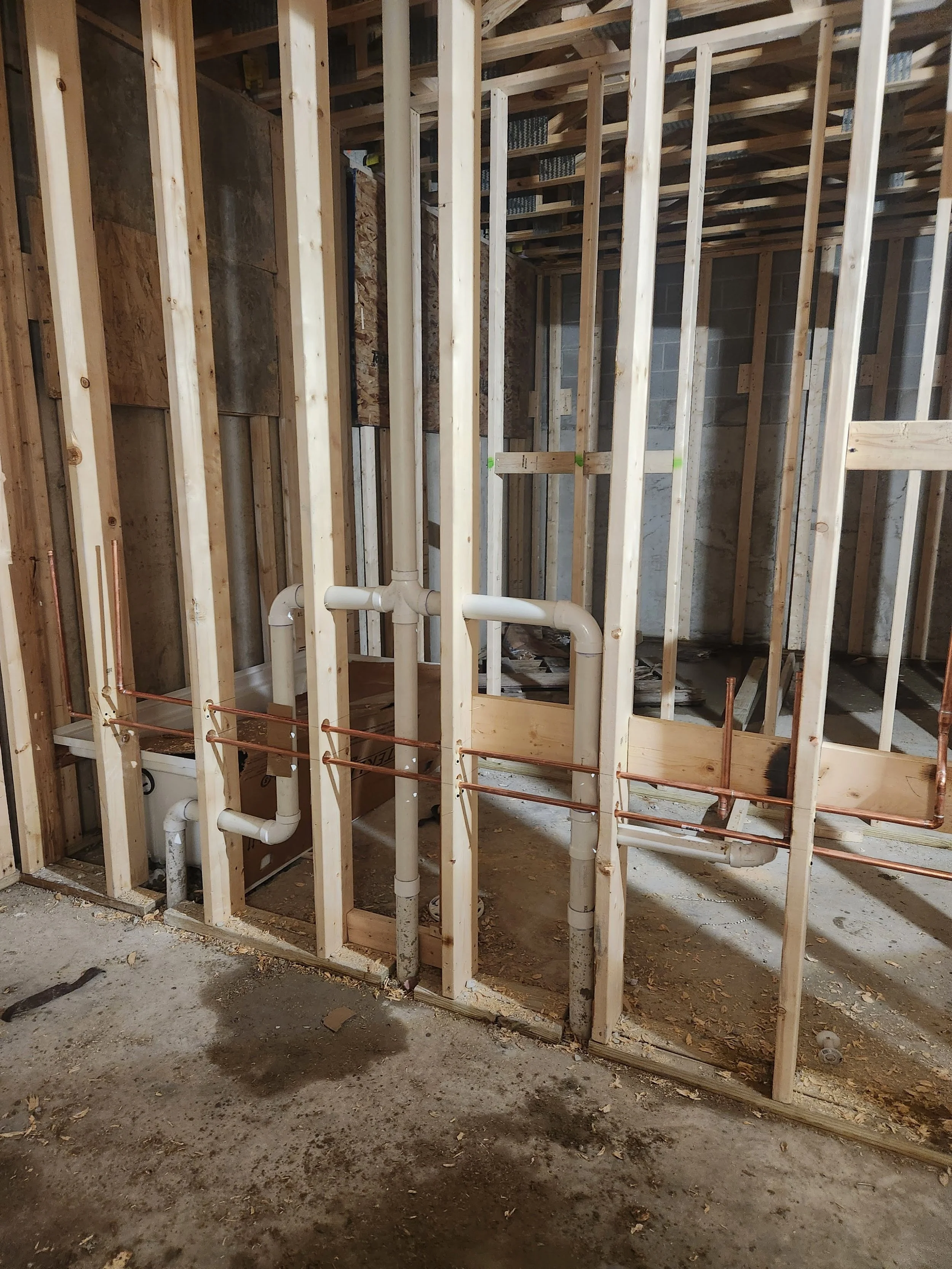

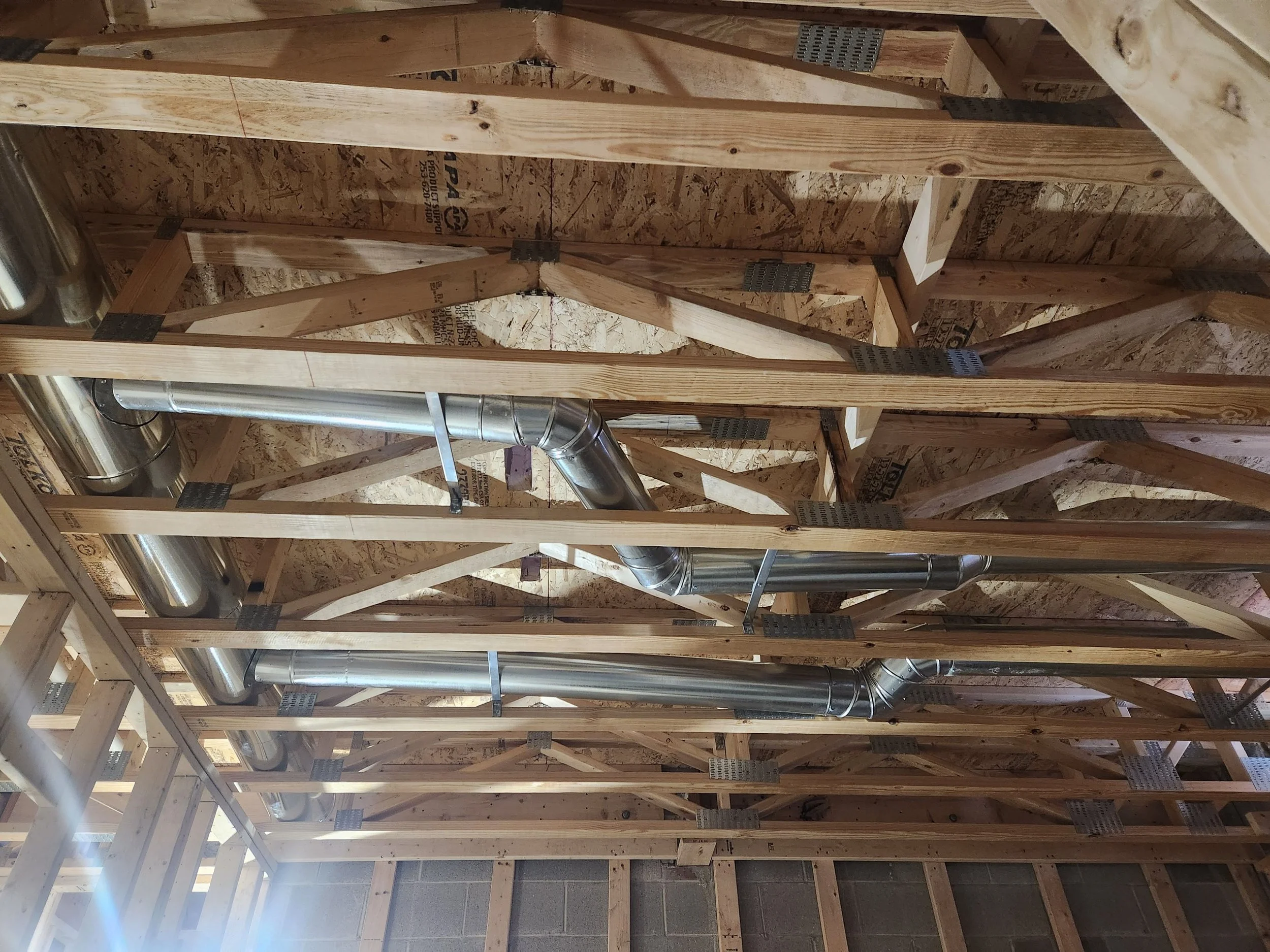


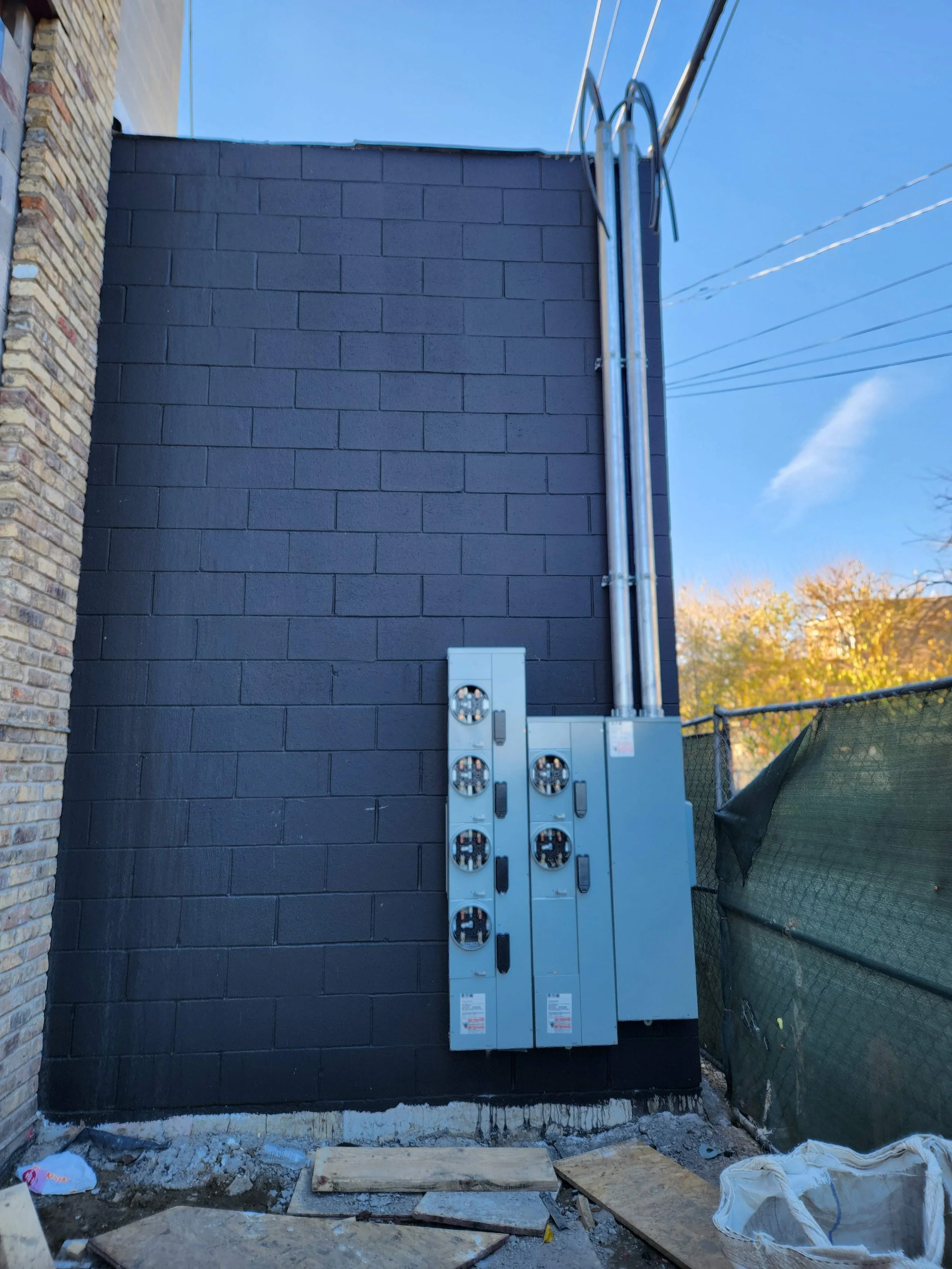
11/07/24
The roofing on the main building has been installed. Decking will be installed over the lower section of roof to create two private outdoor areas for unit 3.


11/05/24
We are topped out and interior framing is complete!

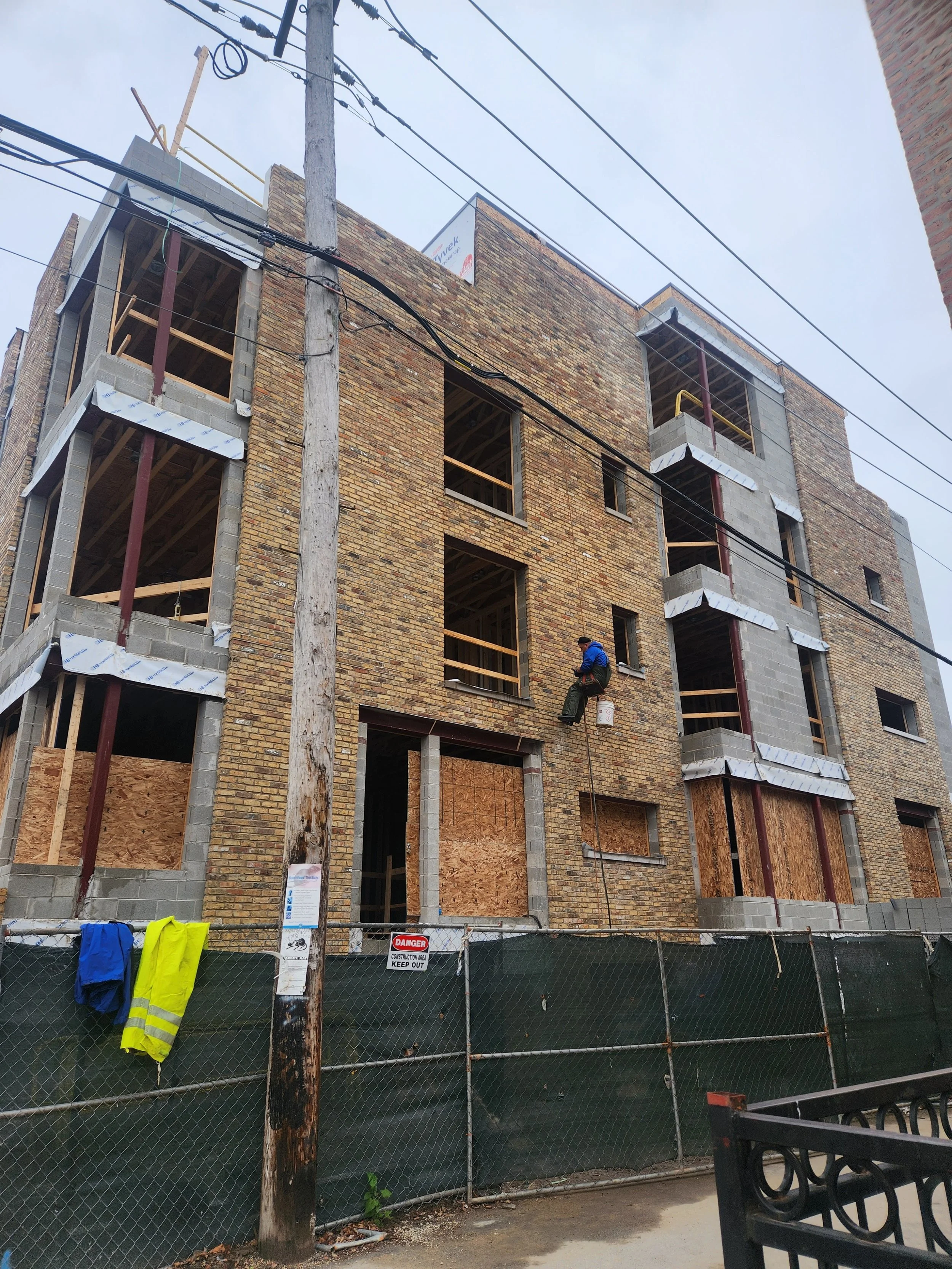

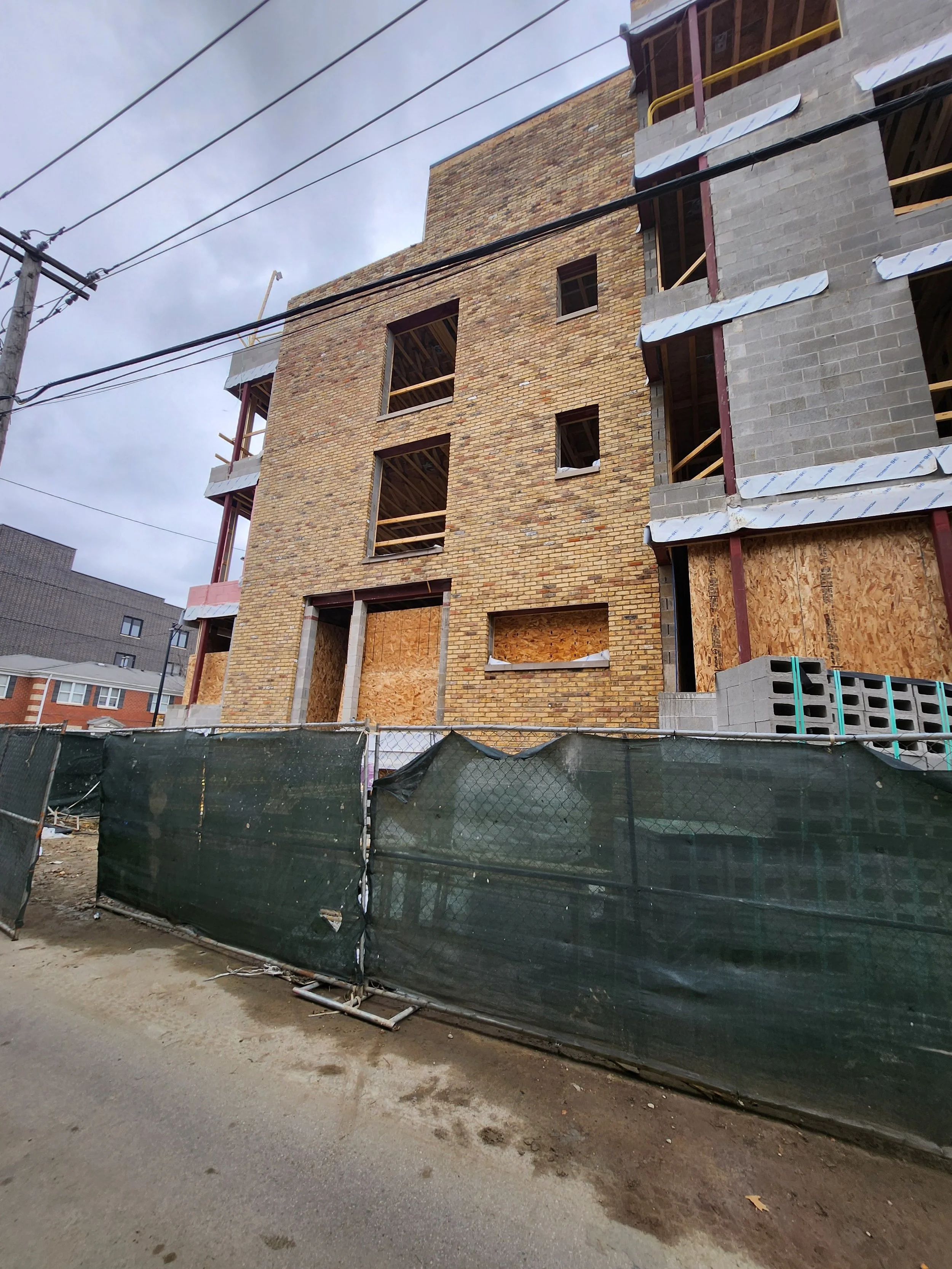

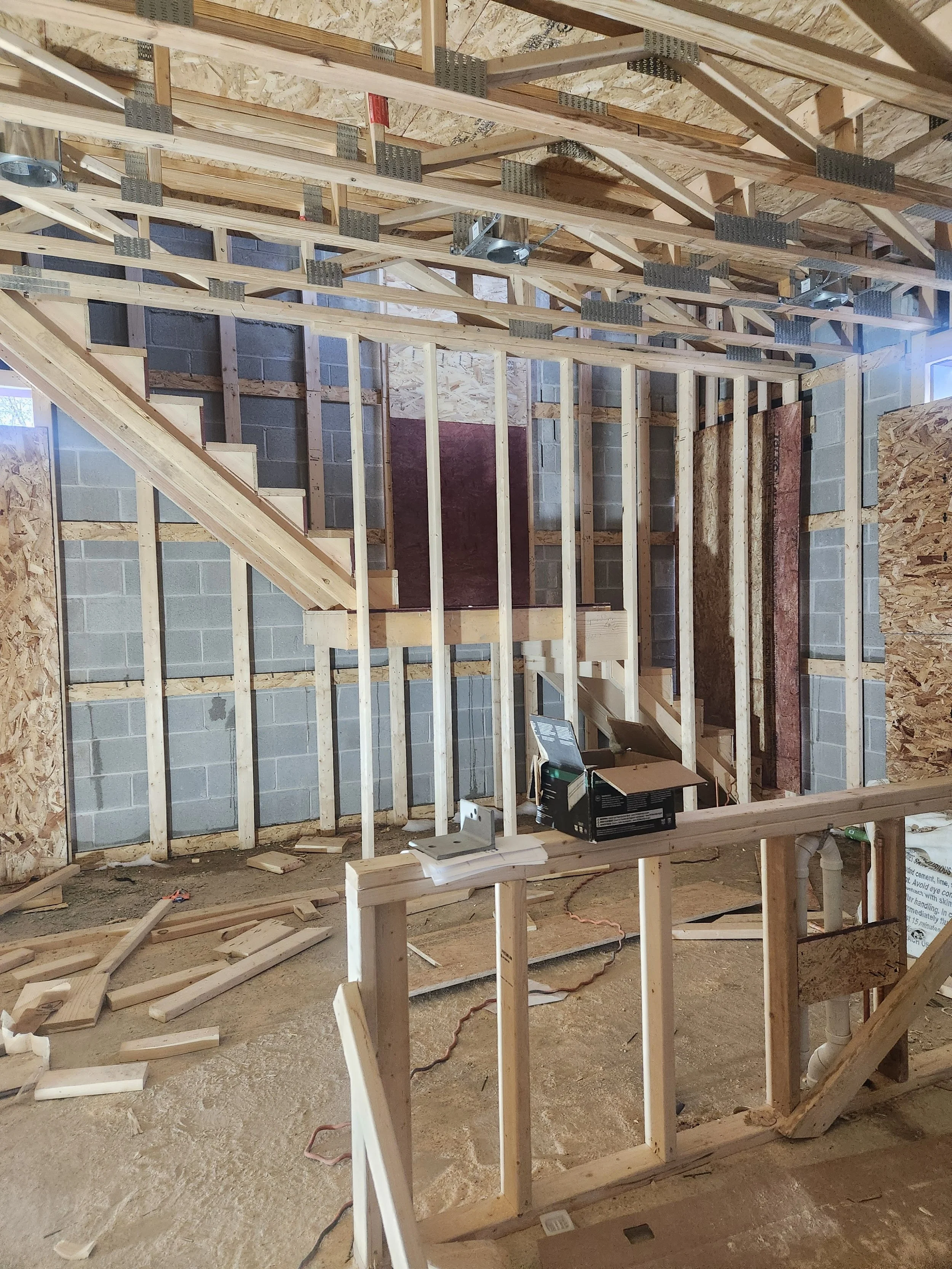
10/23/24
Mom, Dad and Dianna came in for a site visit over the weekend while the 4th floor trusses went in. The masons continued from 4th floor to roof and the carpenters are about finished with two floors of interior framing. The views from Unit 3’s roof deck on the 4th floor are incredible! This week we are finalizing cabinet and plumbing fixture selections so we are ready for the plumber and the electrician to start roughing-in.
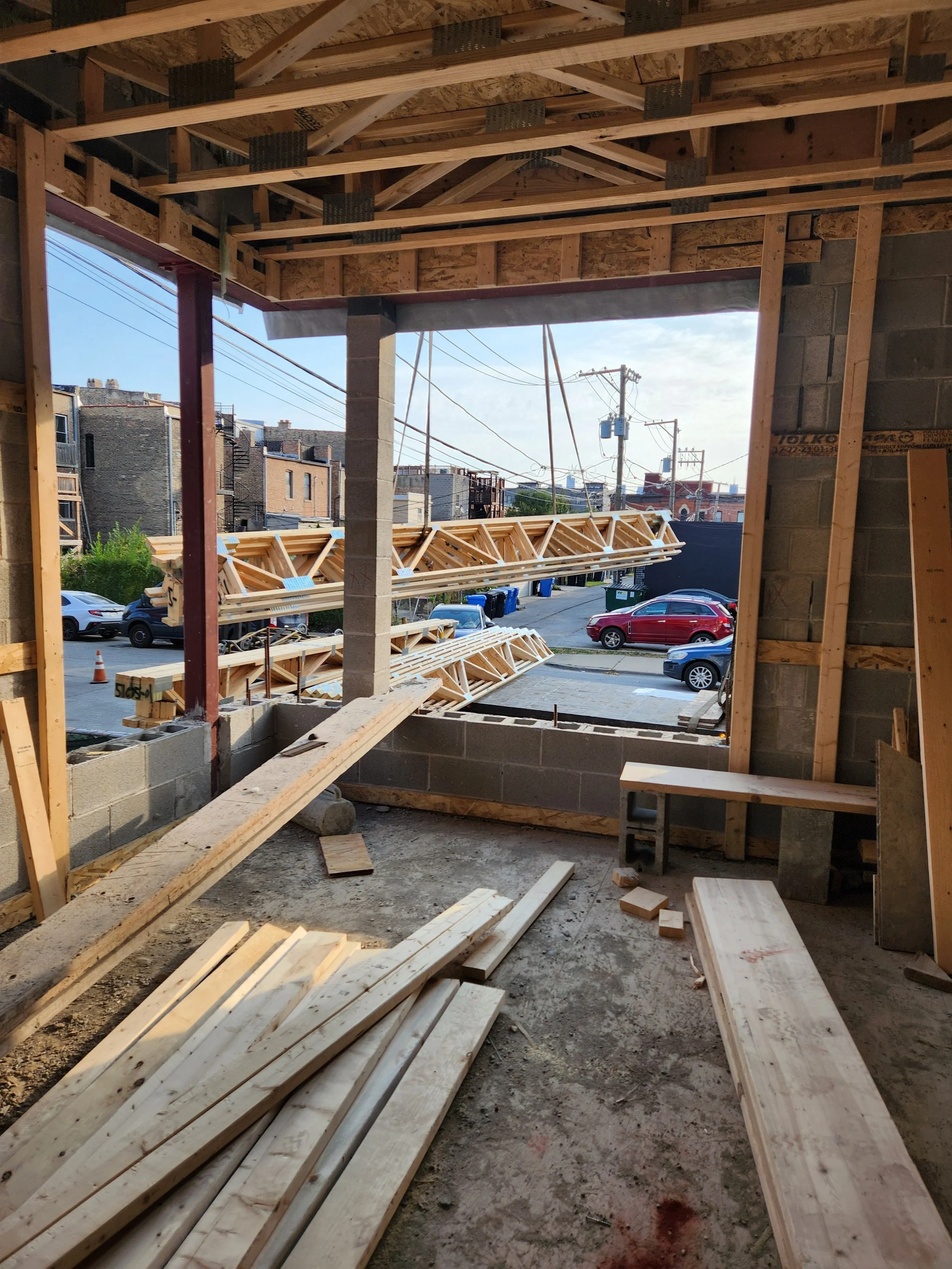
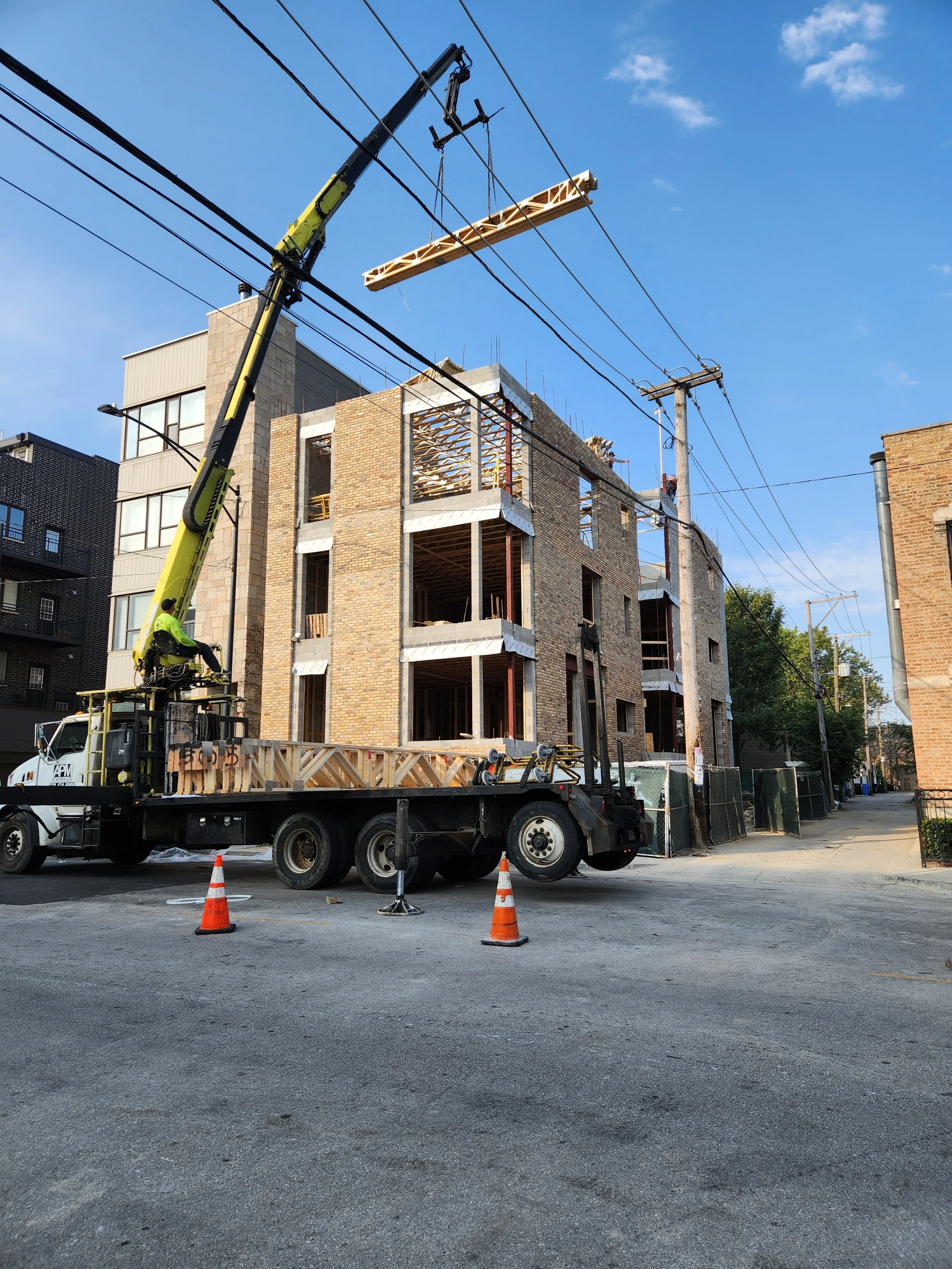




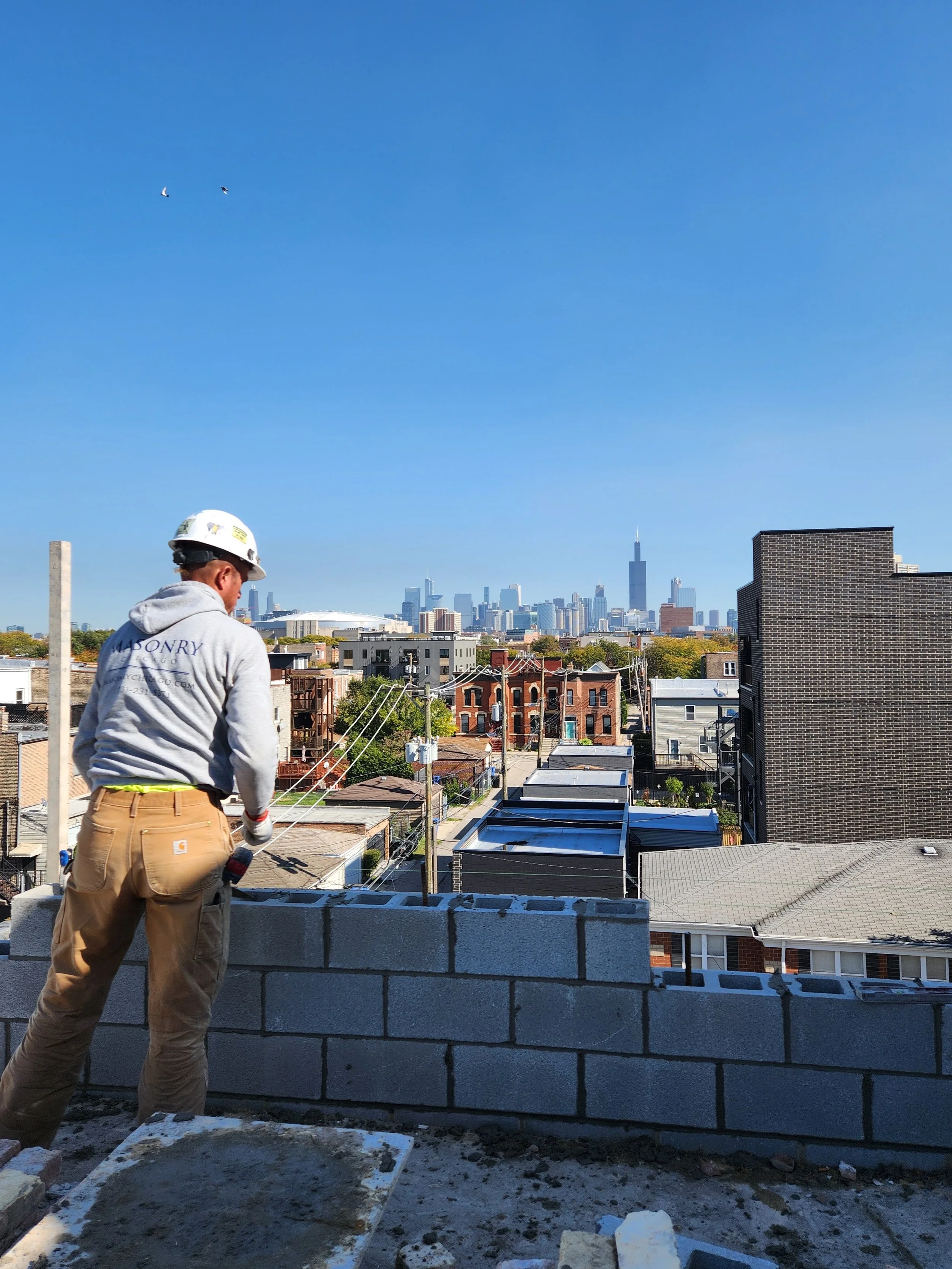




10/04/24
Masons and carpenters continued their work from the 2nd to the 3rd floor. We are very happy with the way the brick is turning out — all saved from the old building!
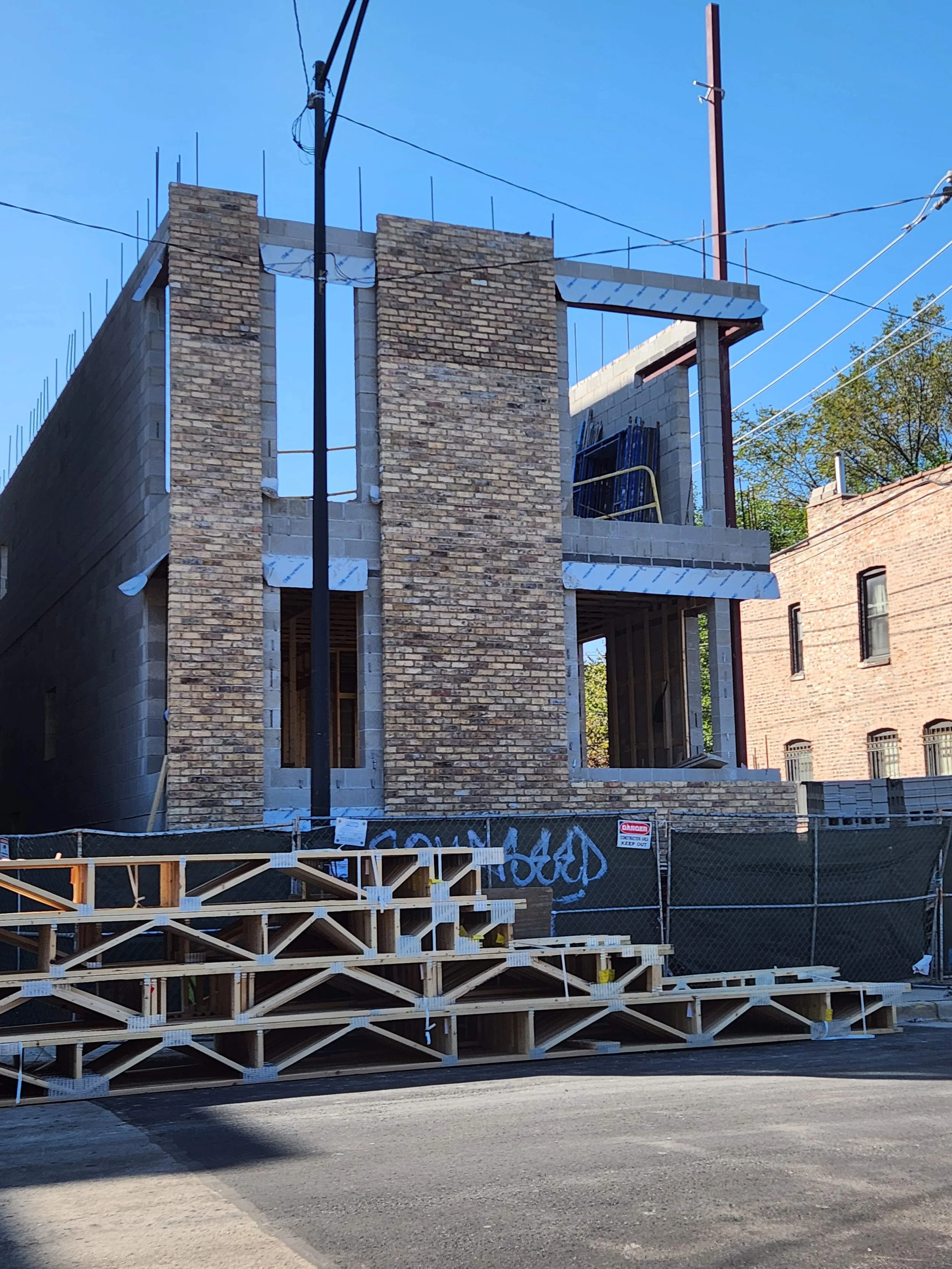
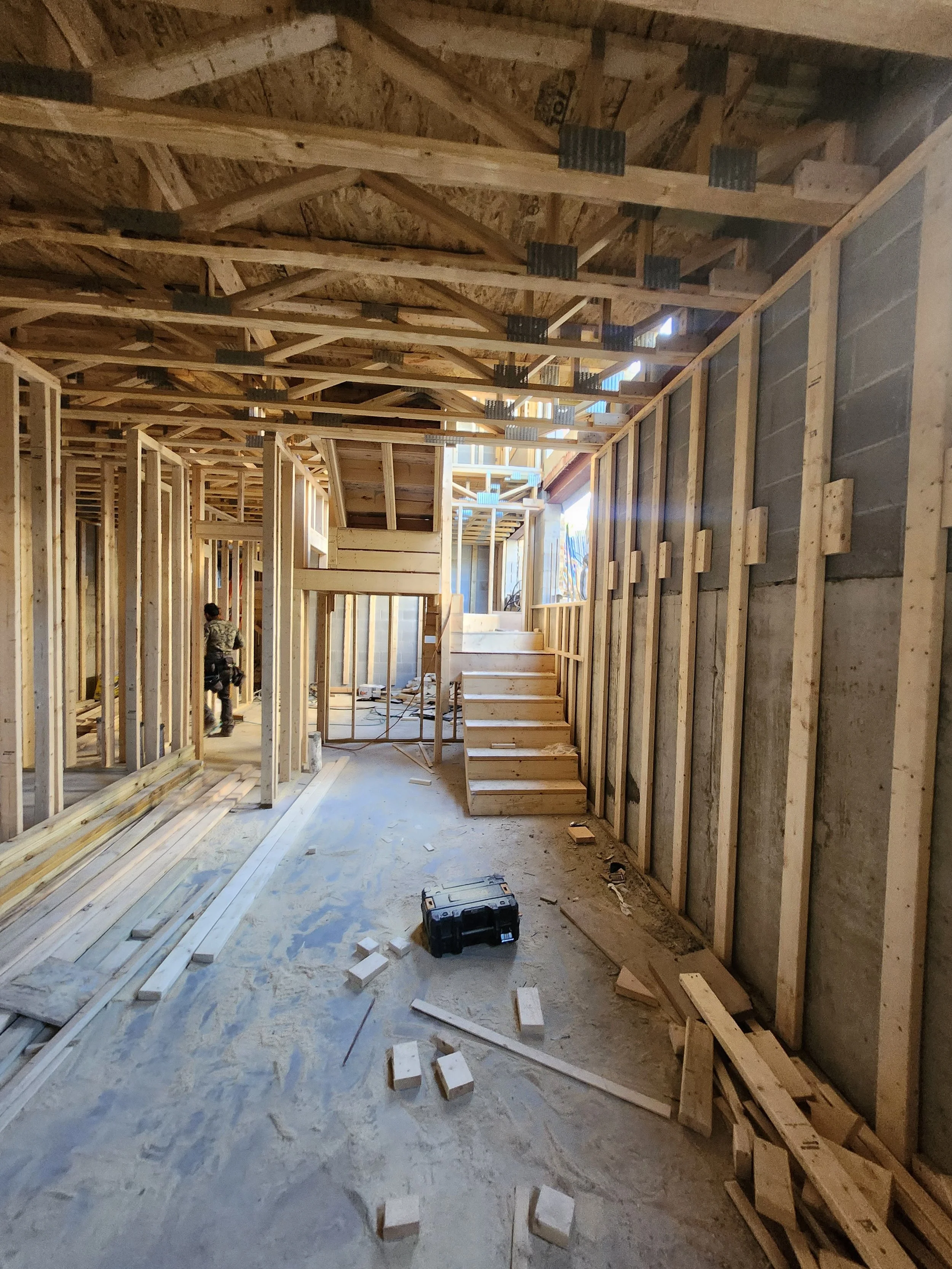
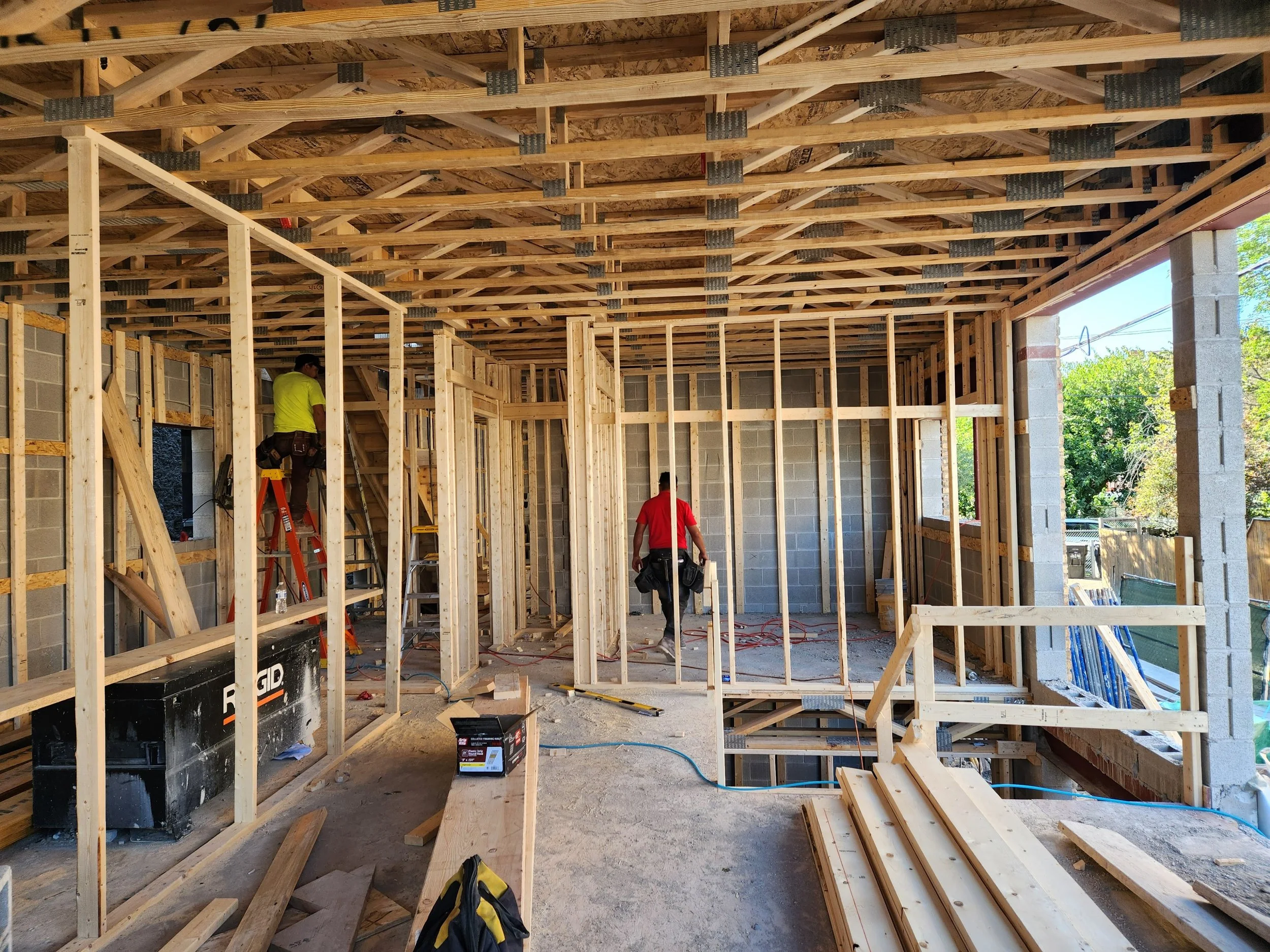

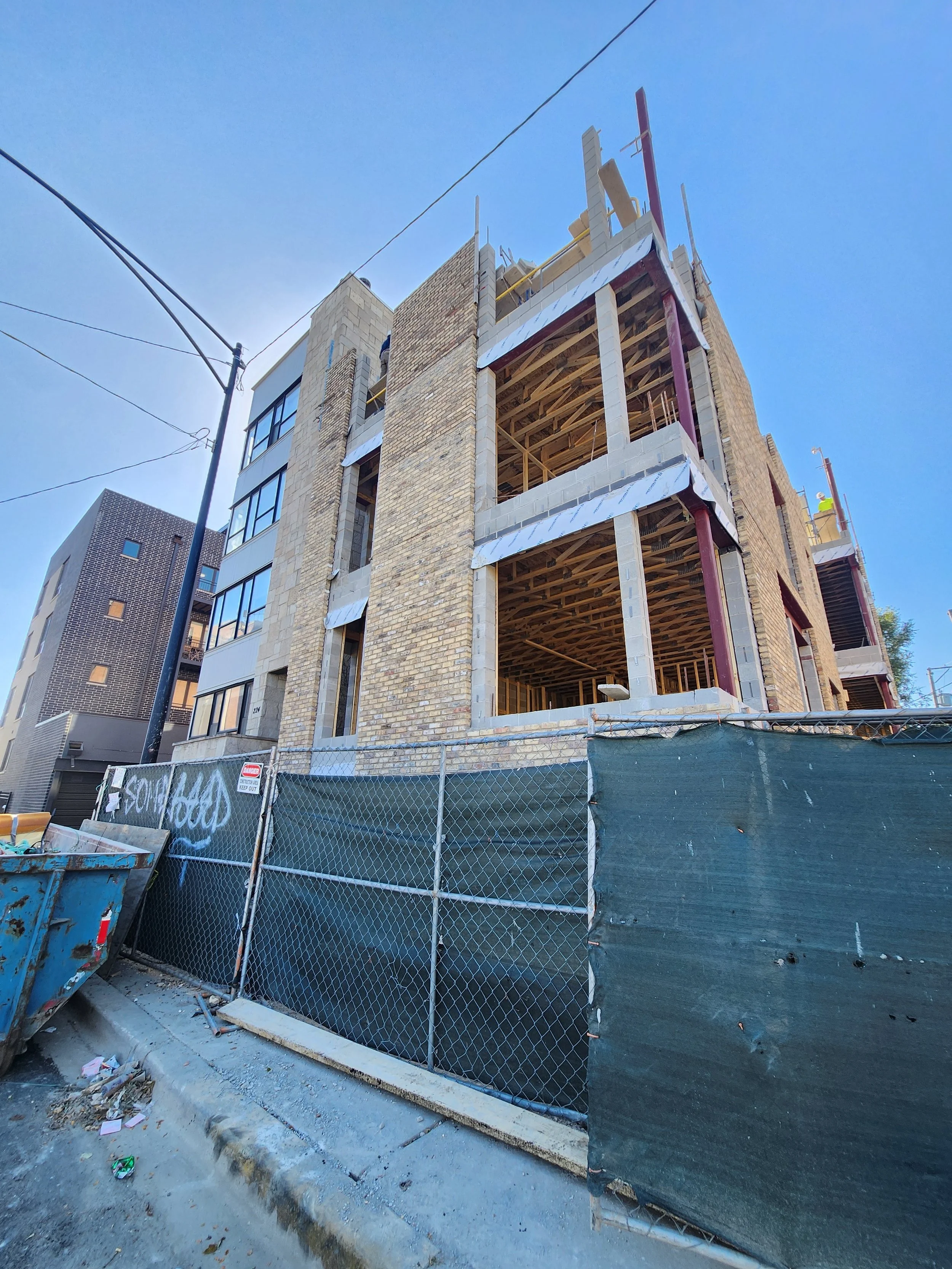
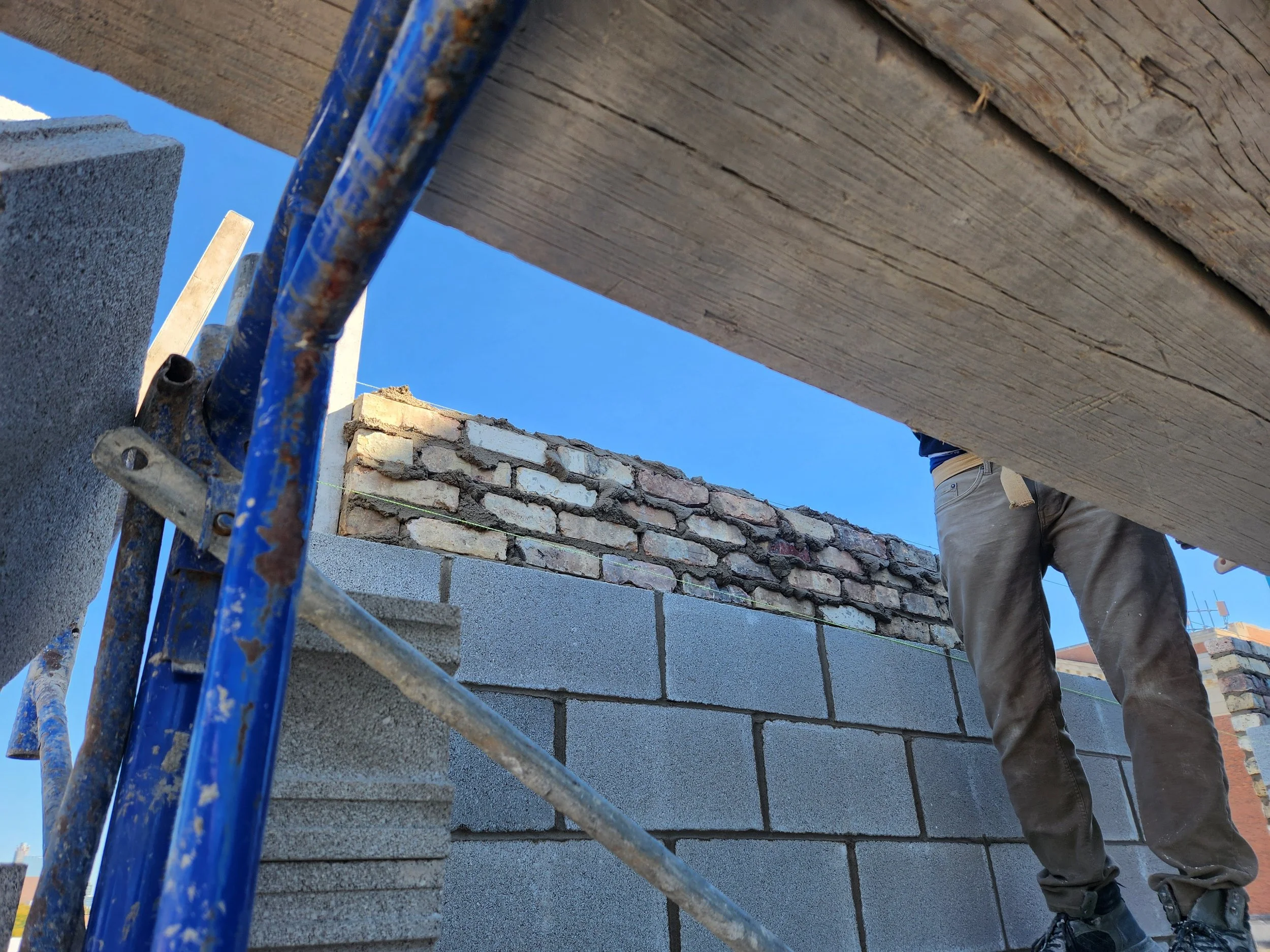
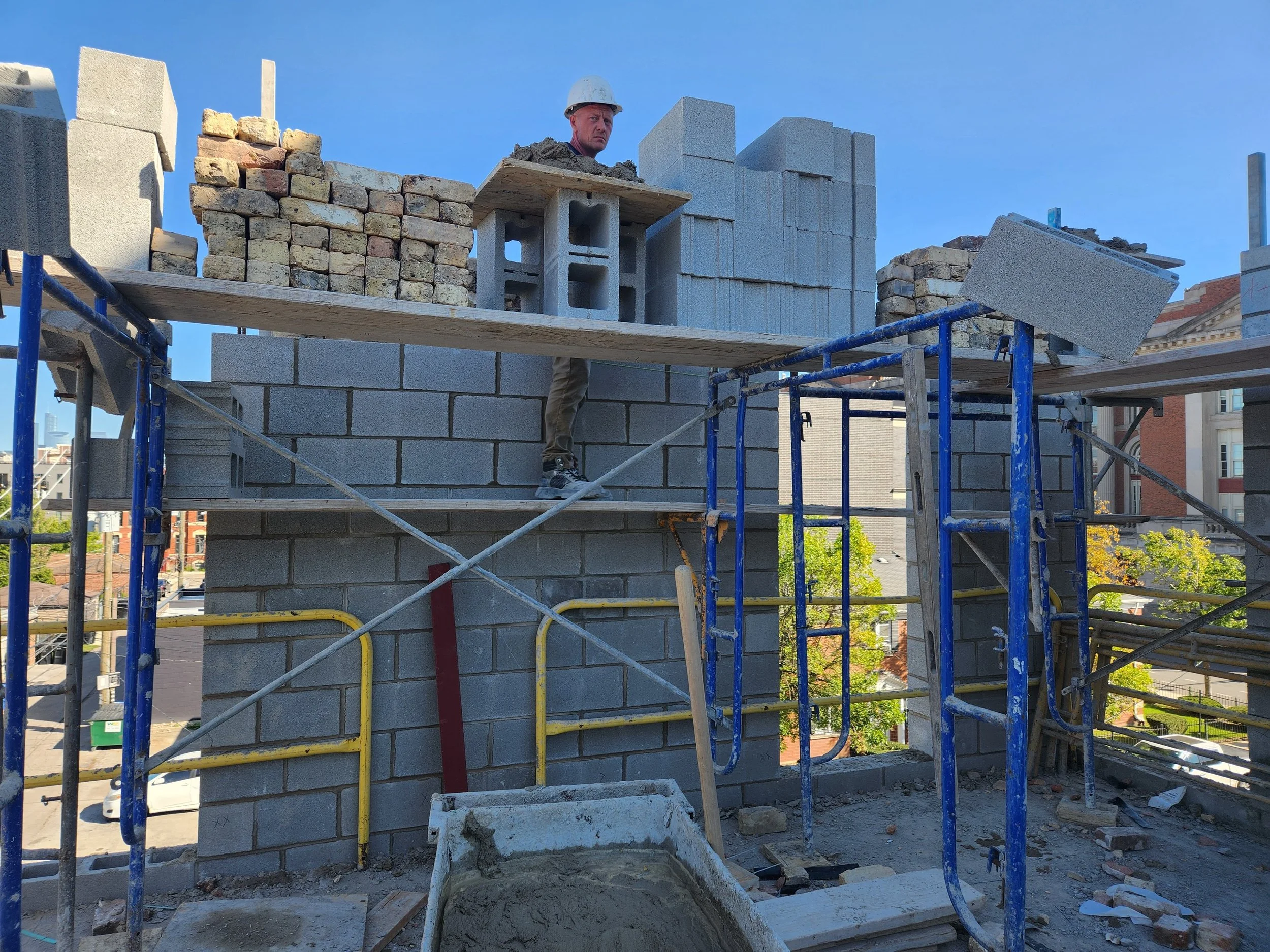

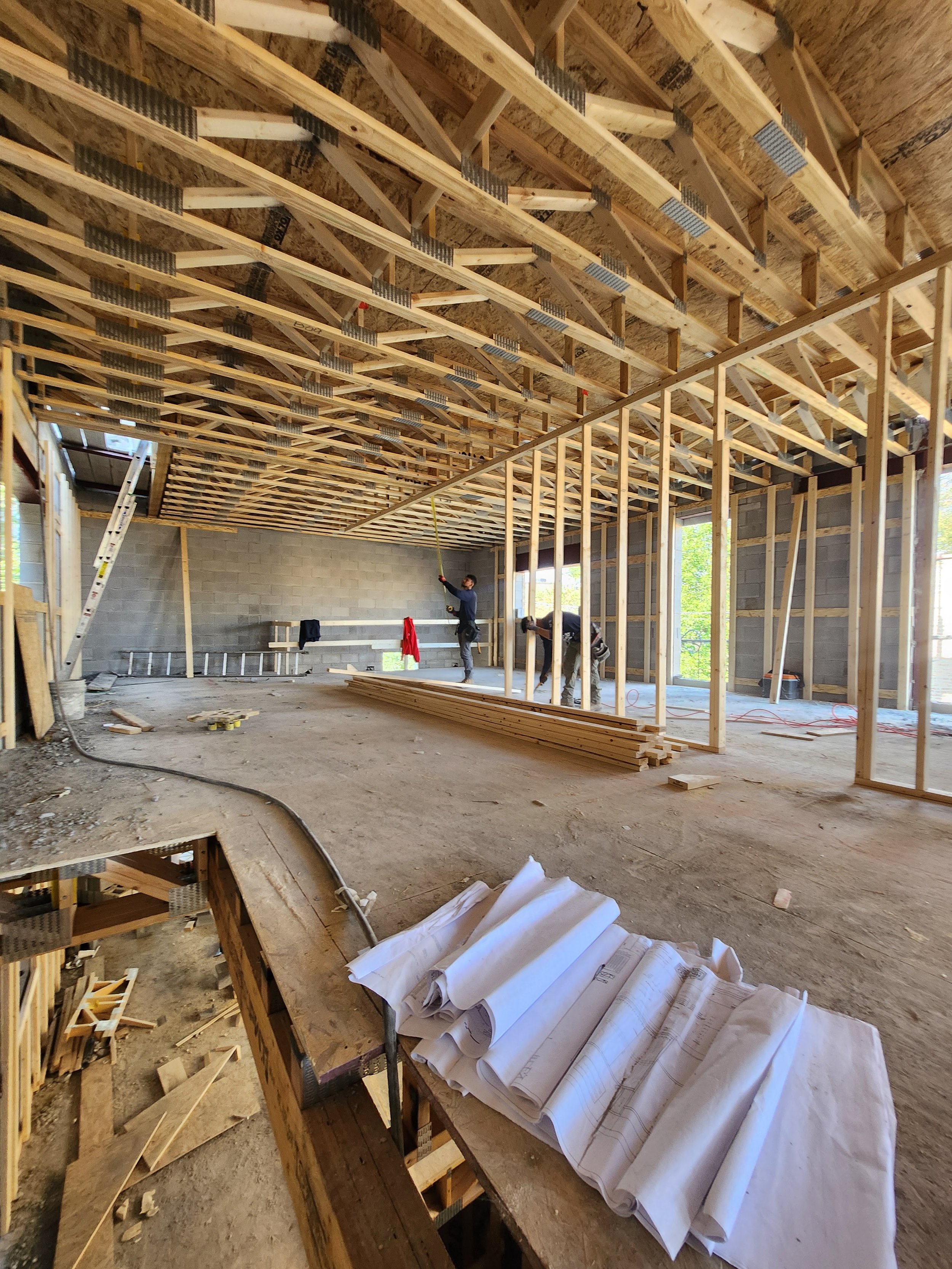

10/01/24
Masonry progress continues from second to third floor.



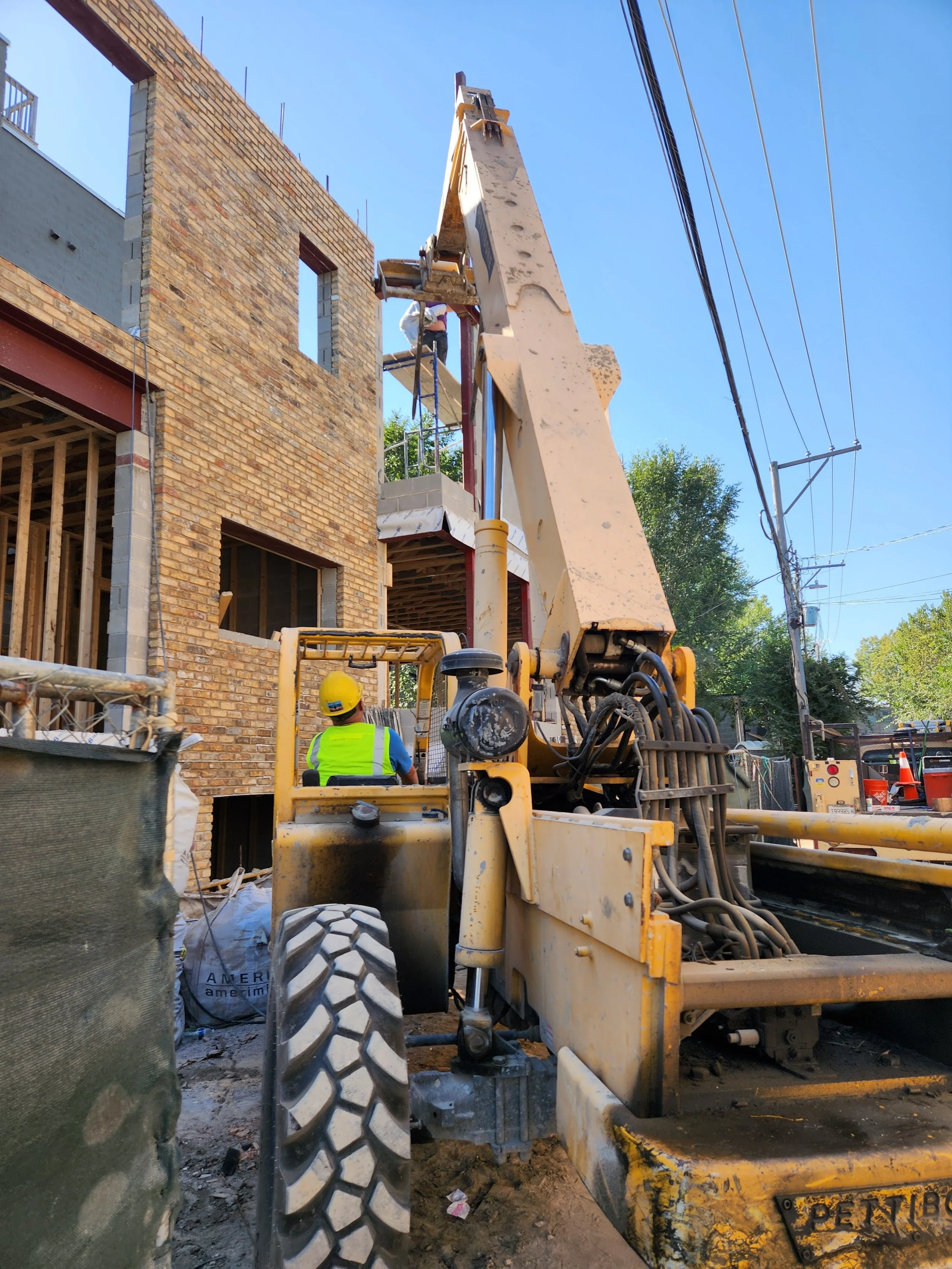


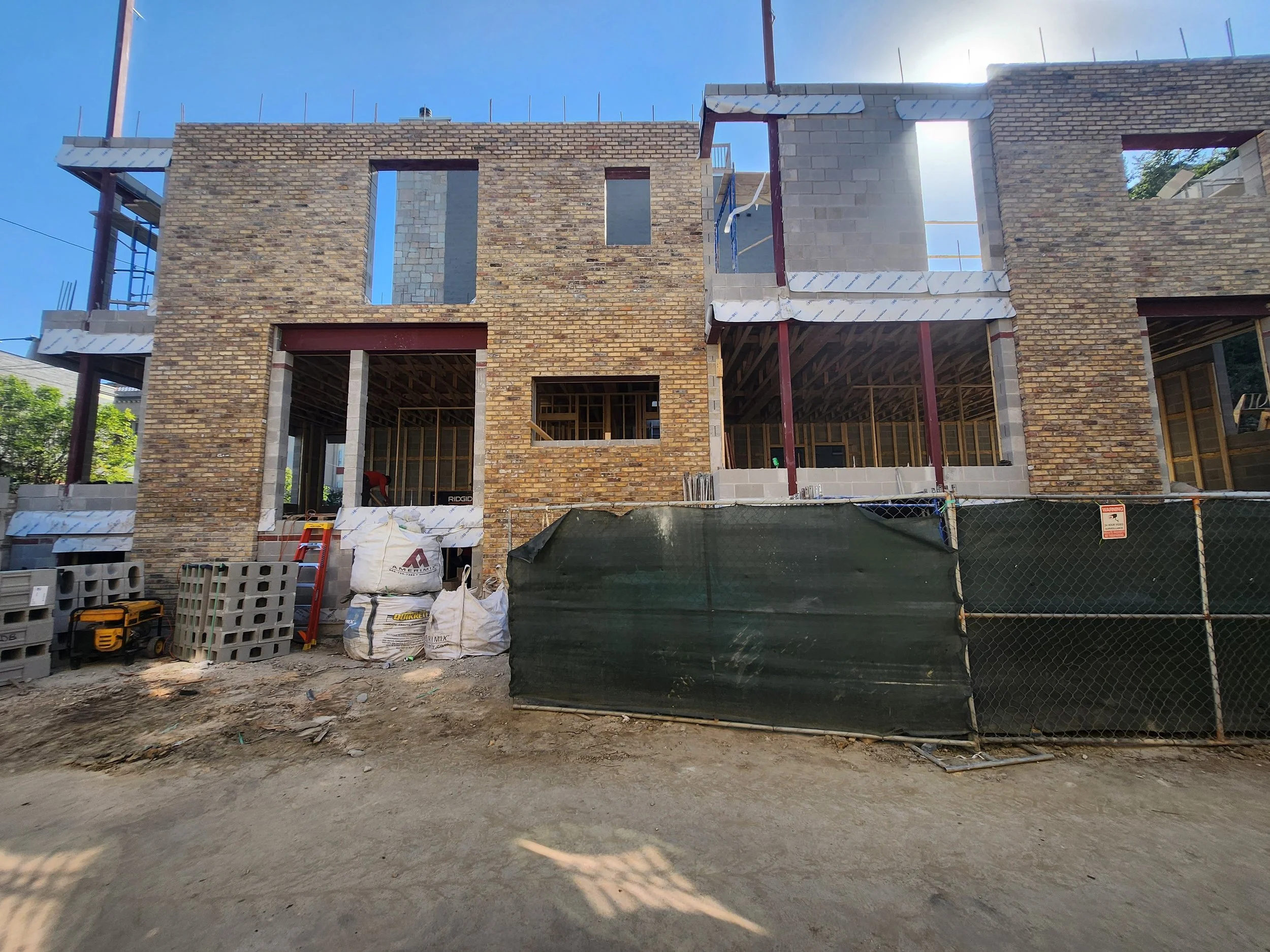
9/27/24
The 2nd deck went in this week and the masons are working on the 2nd floor walls and the exterior brick. The carpenters are continuing to frame interior walls for basement and 1st floors. Due to some rain, the basement collected a fair bit of water — we spent the morning getting the water out so the carpenters could work.

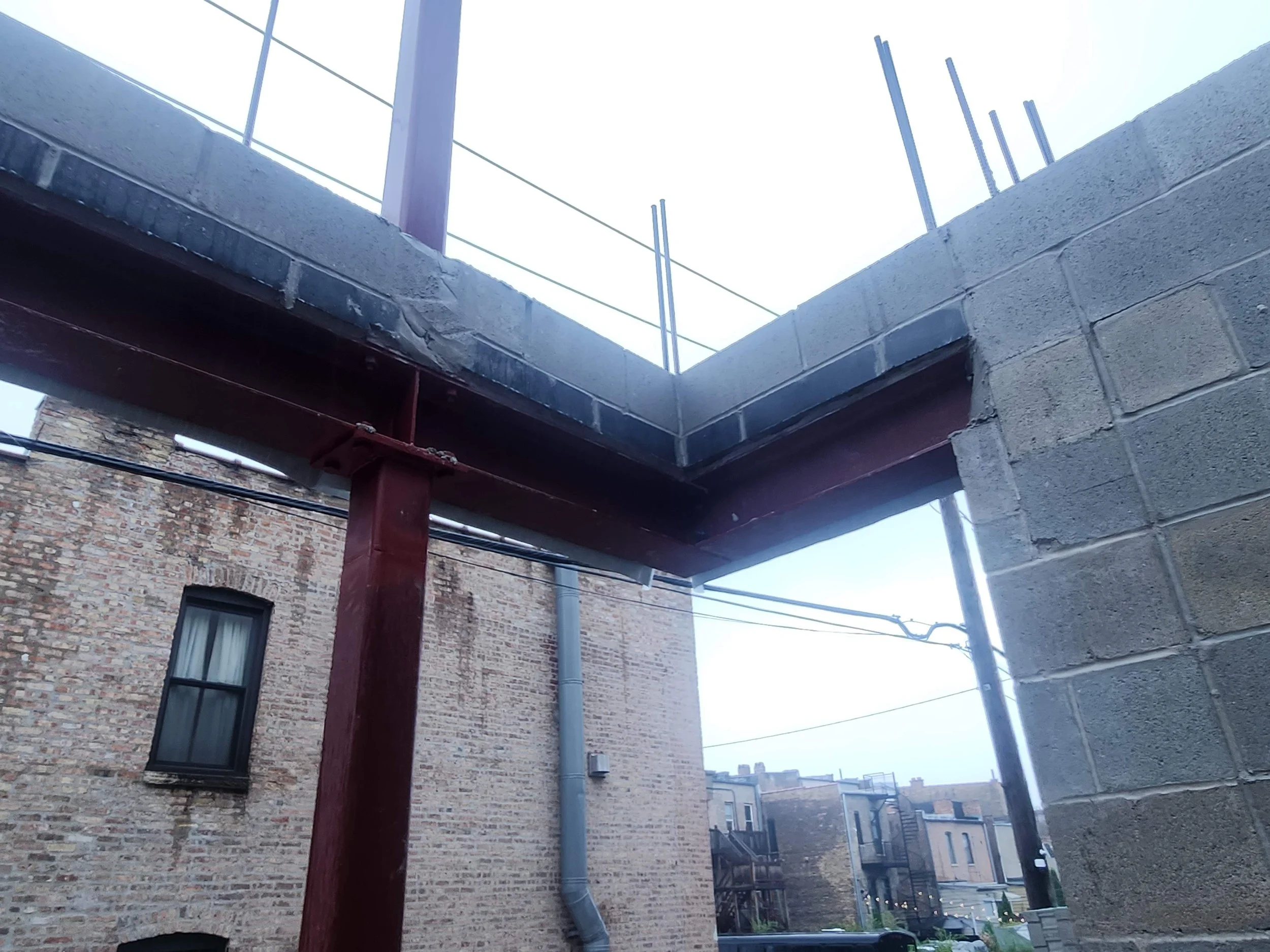
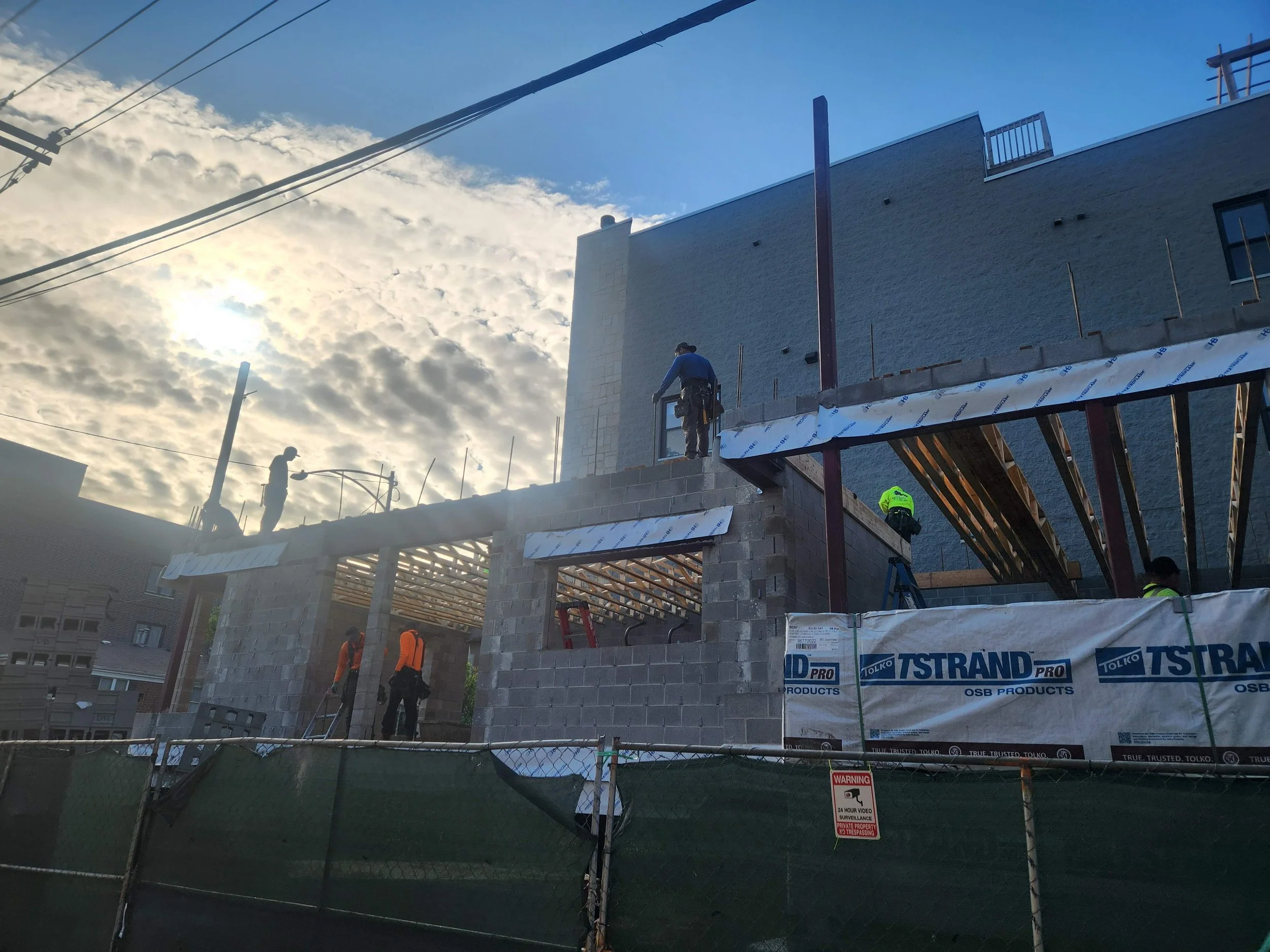

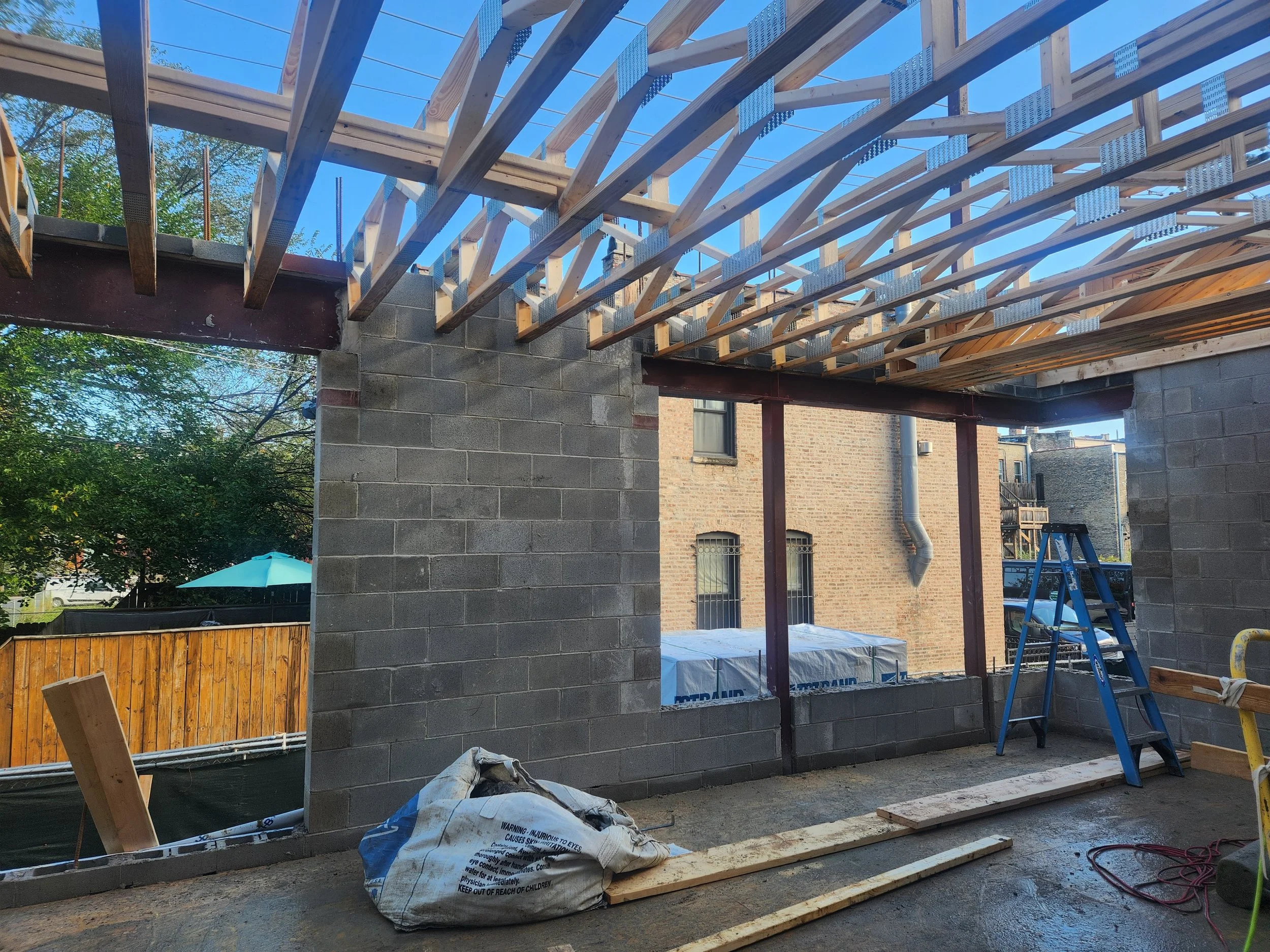
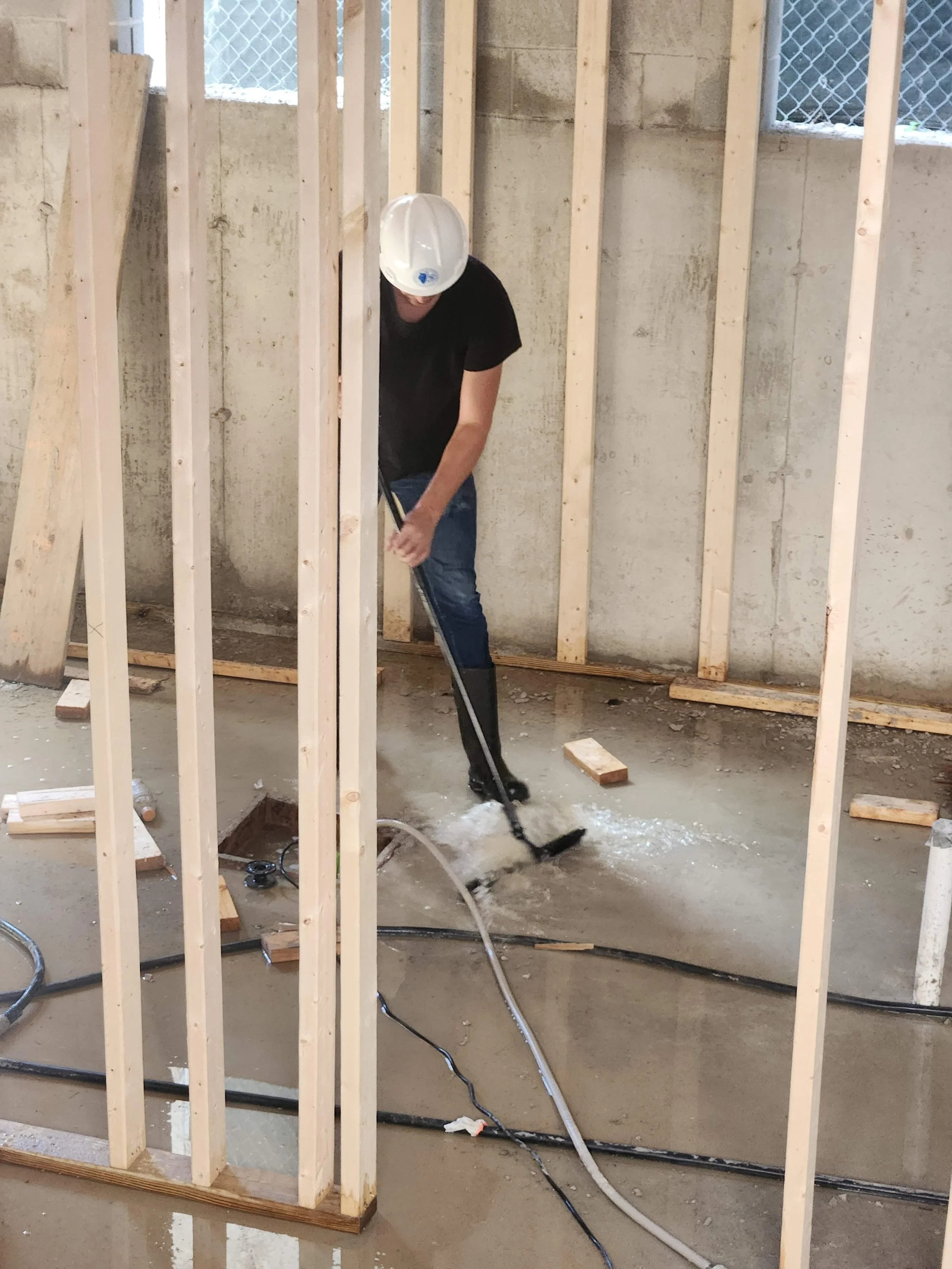
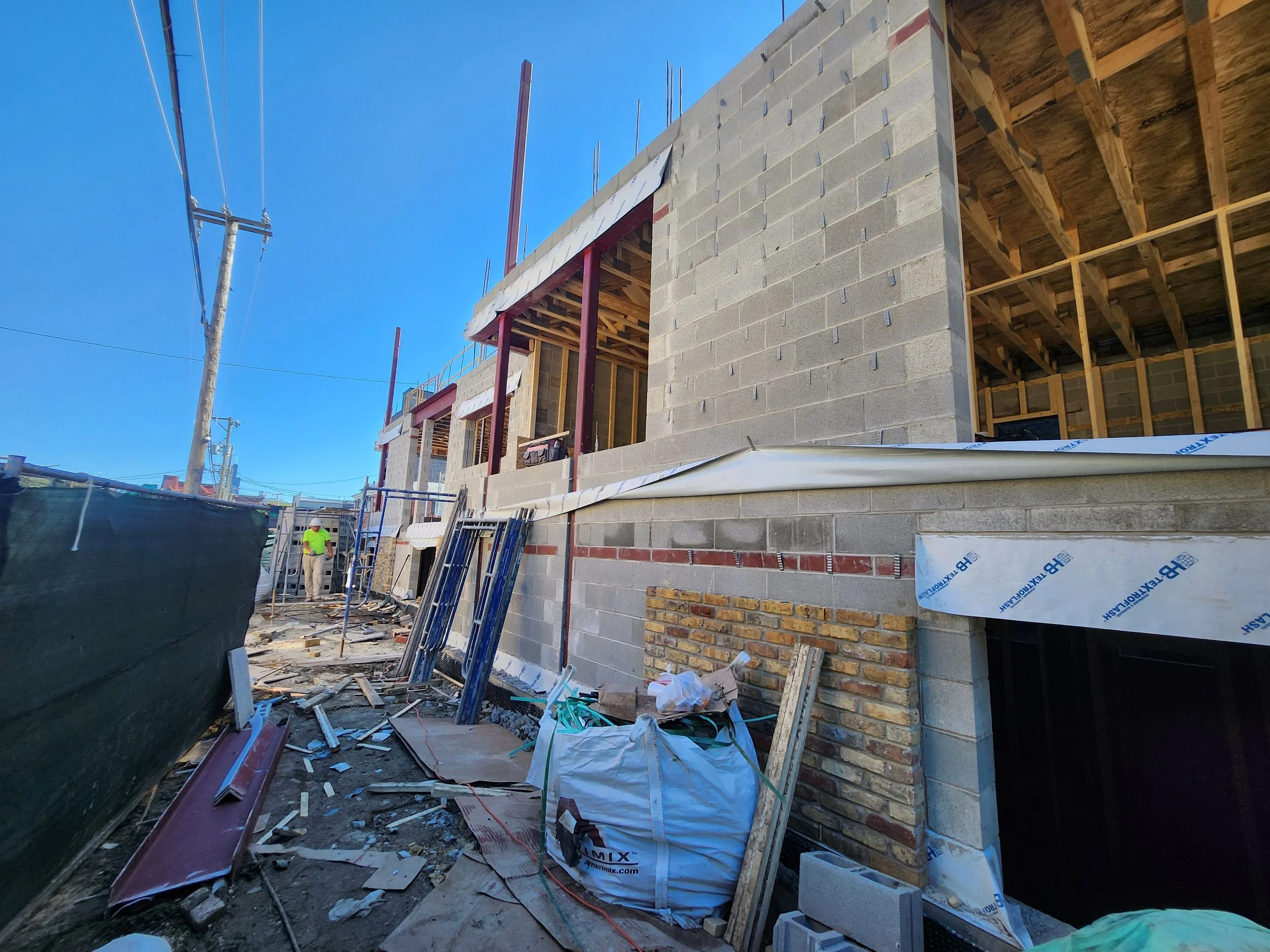
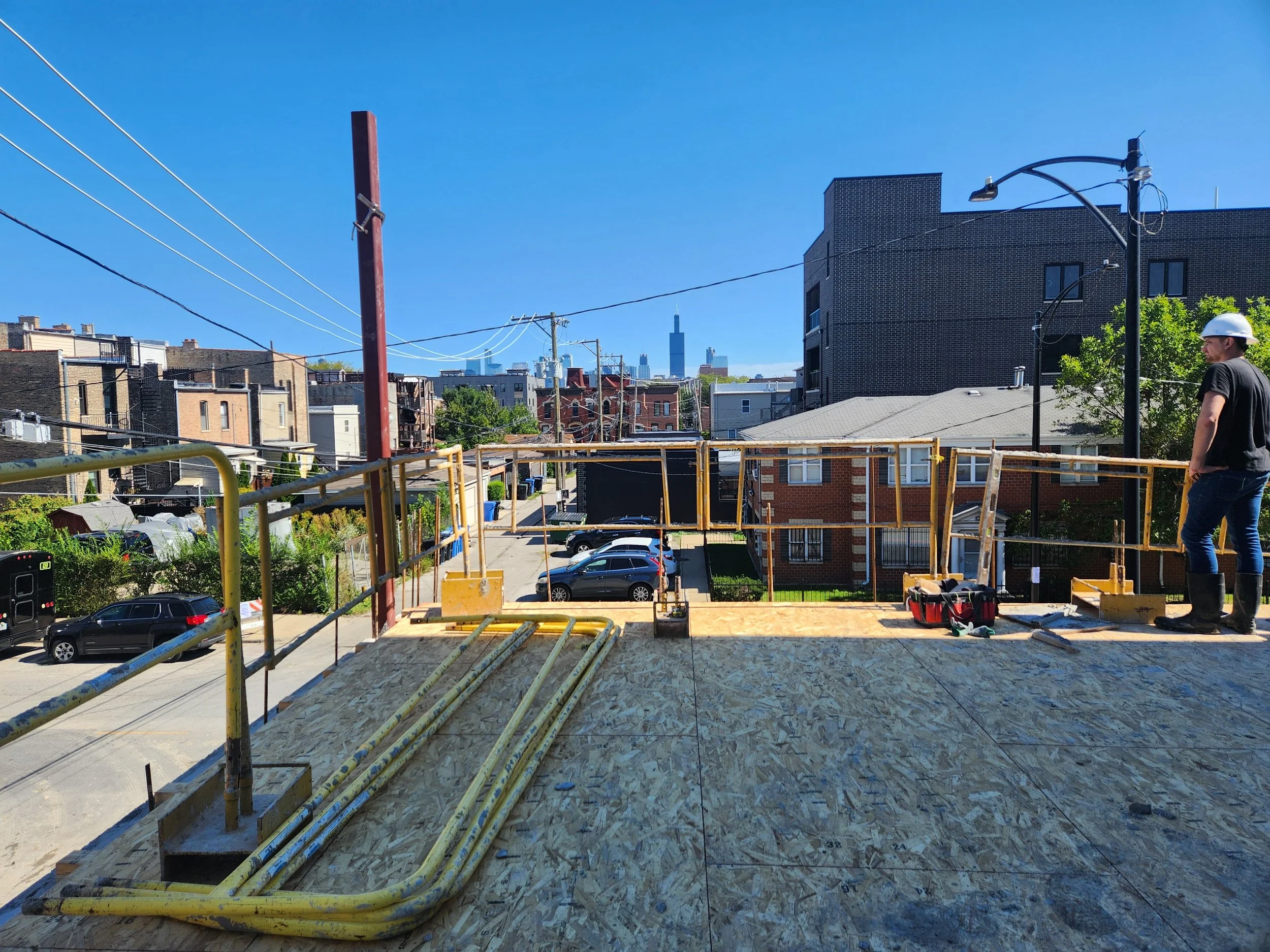
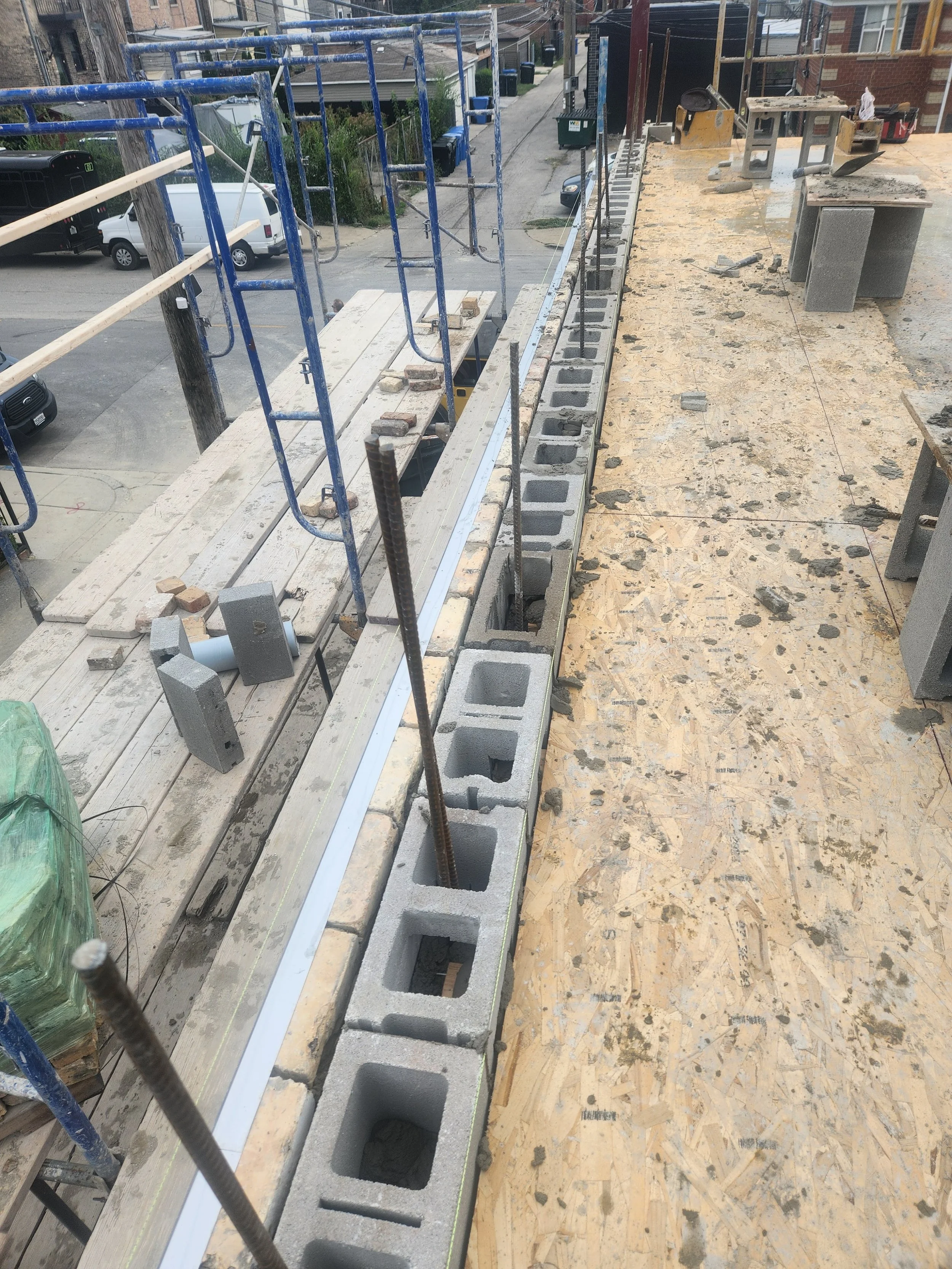
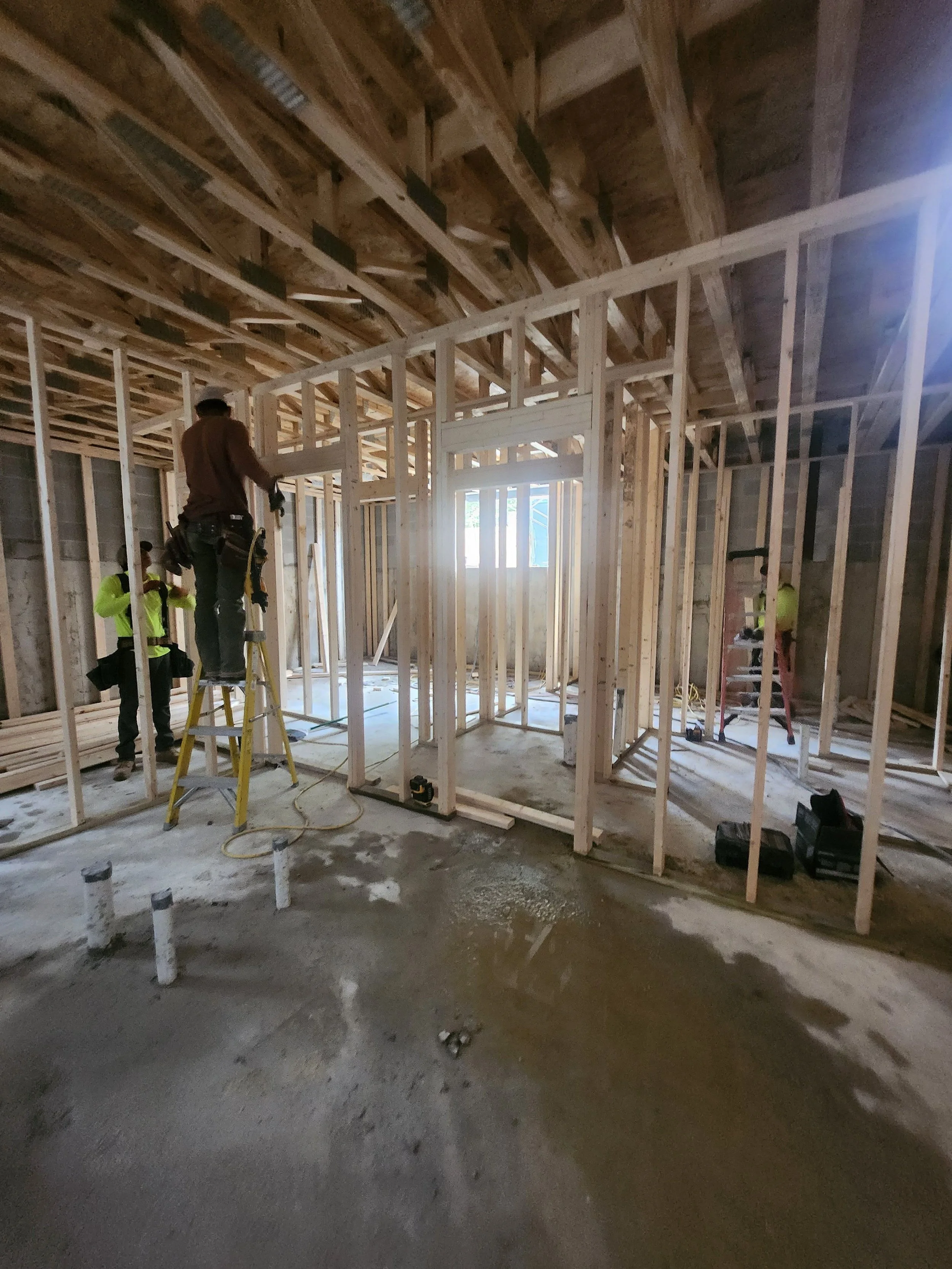
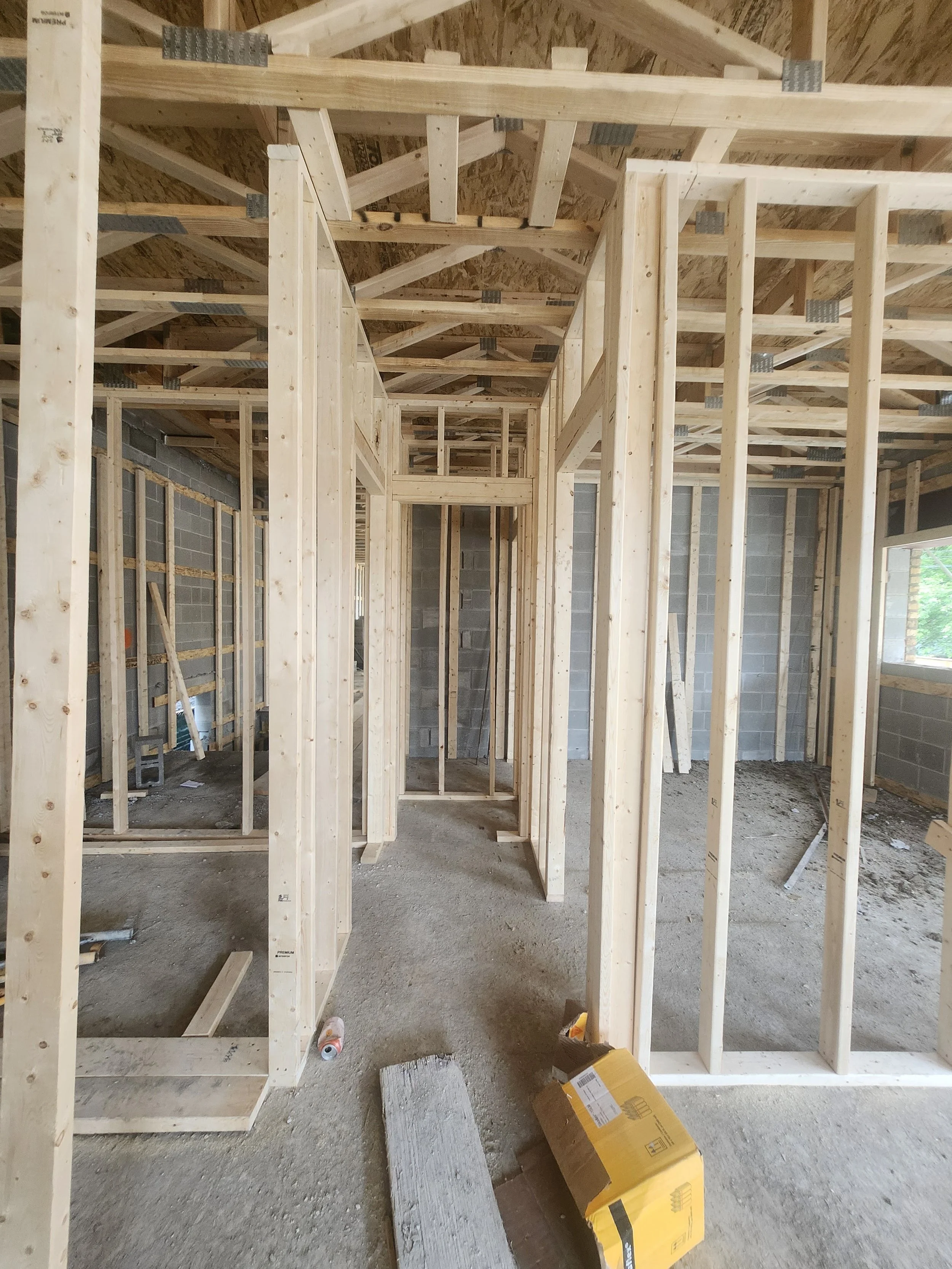

9/23/24
Things are moving quickly — first floor walls are up and almost ready for the second deck. Water connection to the city is complete. Interior framing in the basement has begun.


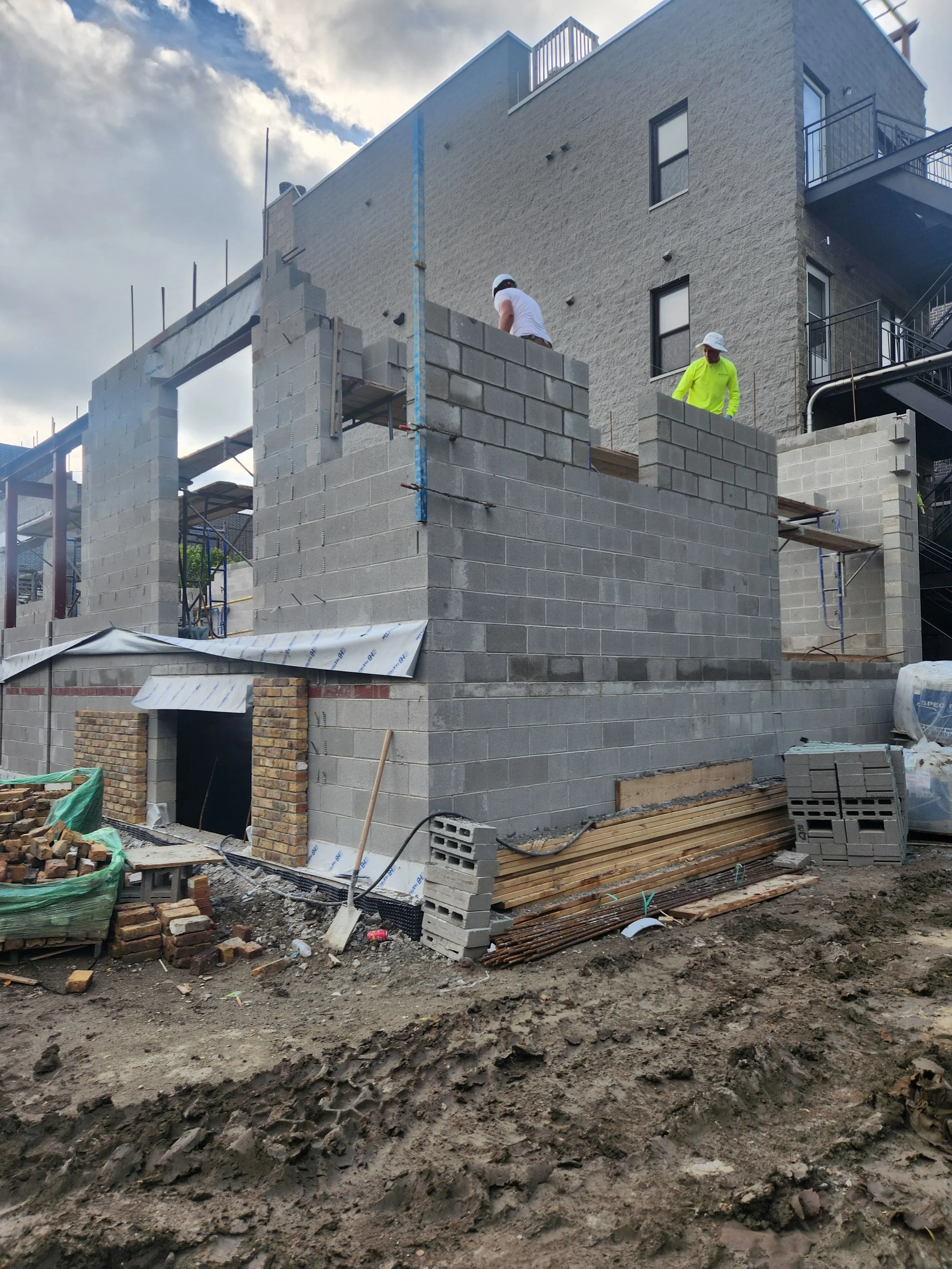



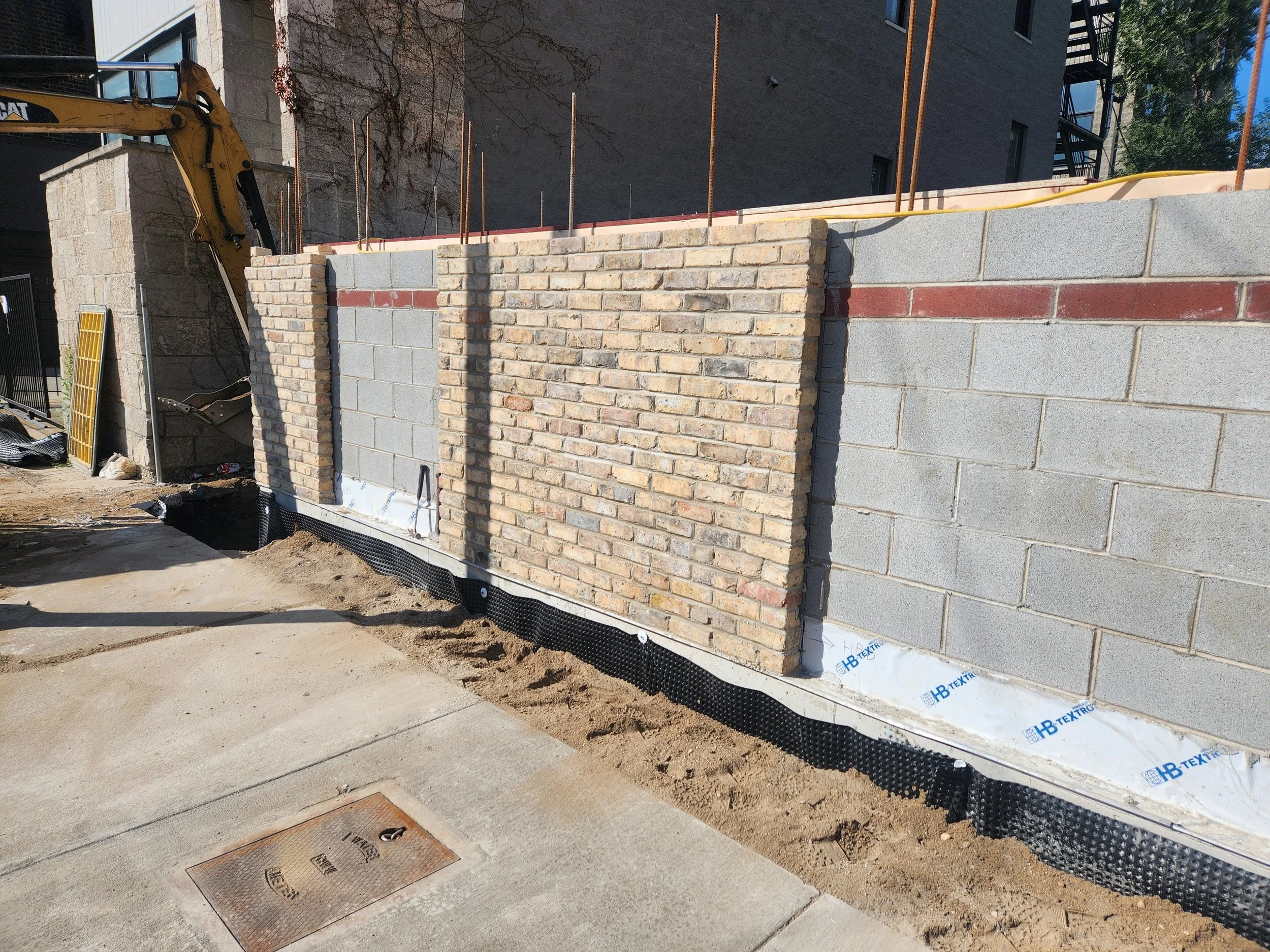
9/13/24
We’ve made a lot of progress this week! The walls are up to the first floor level, and the first floor trusses are installed. The masons have started installing our brick that we saved during demolition and it looks beautiful!

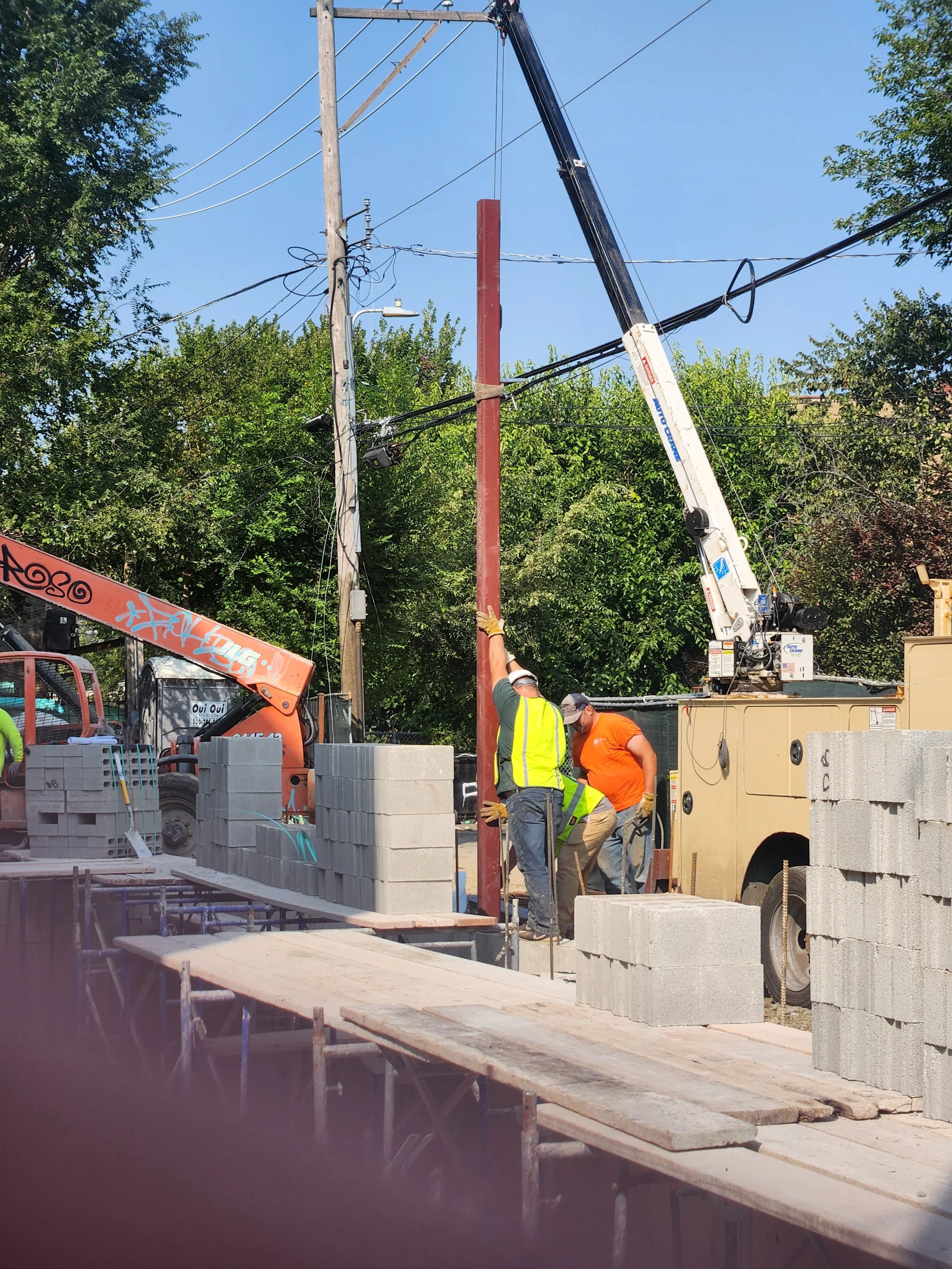
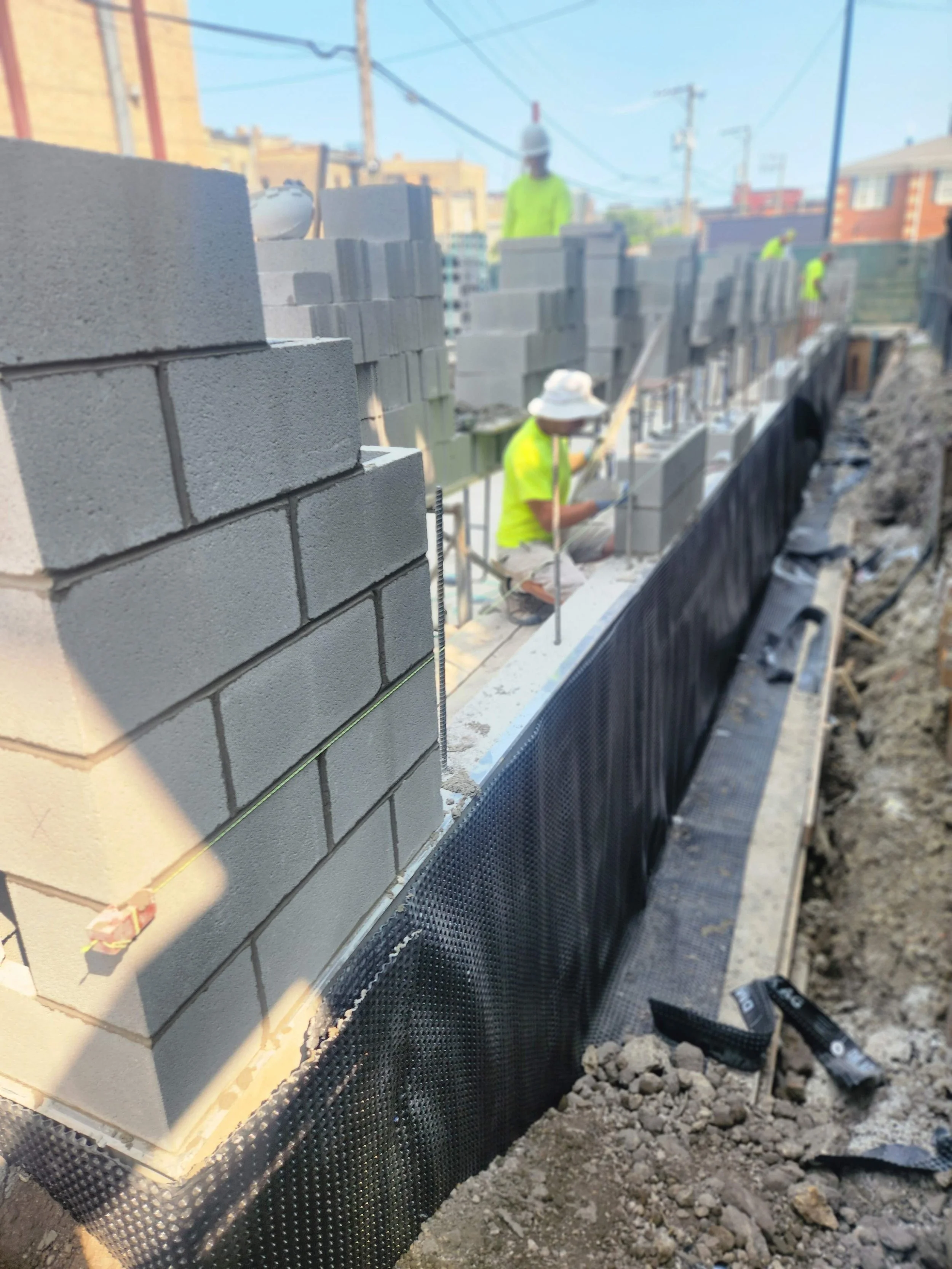
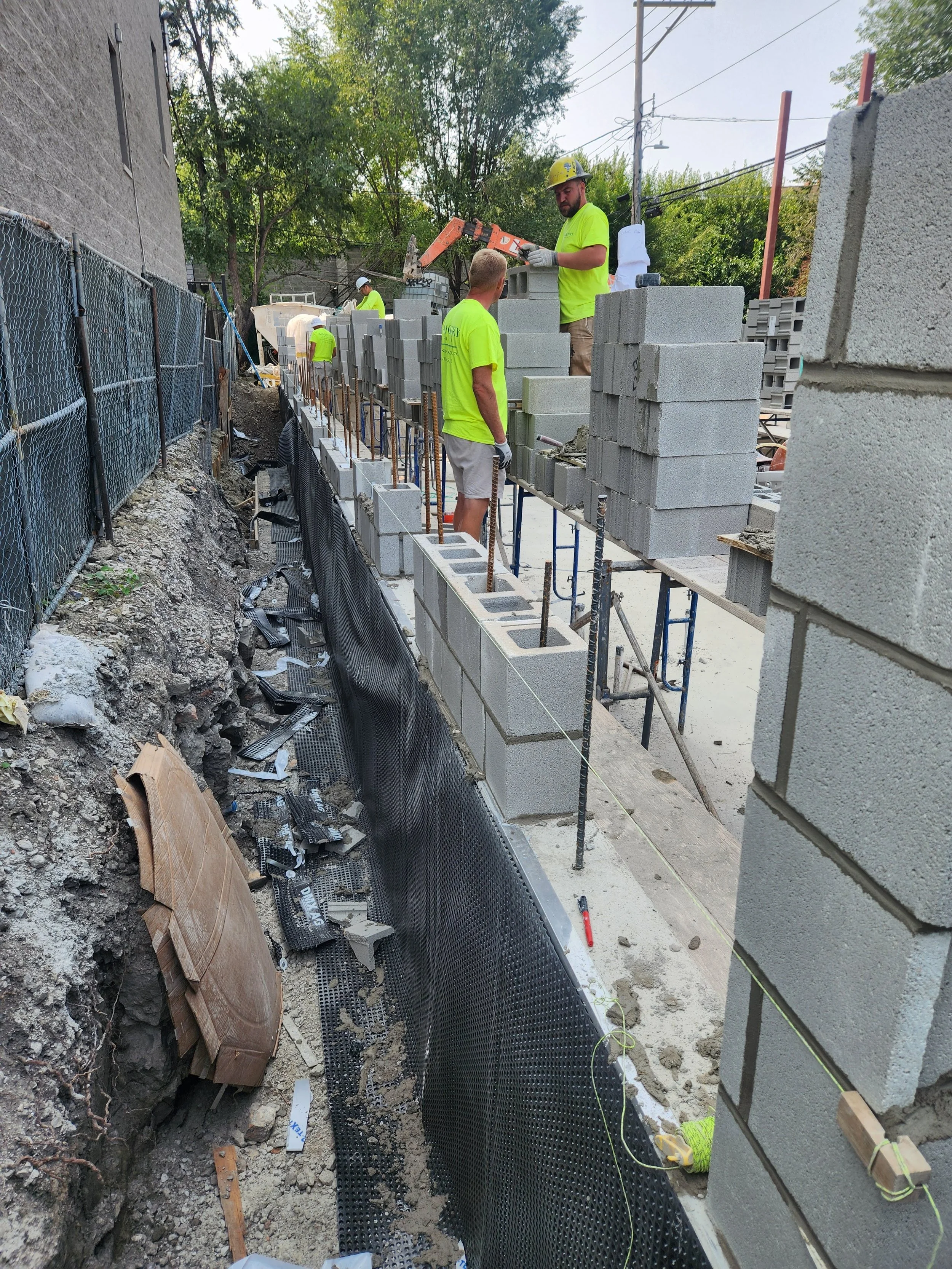
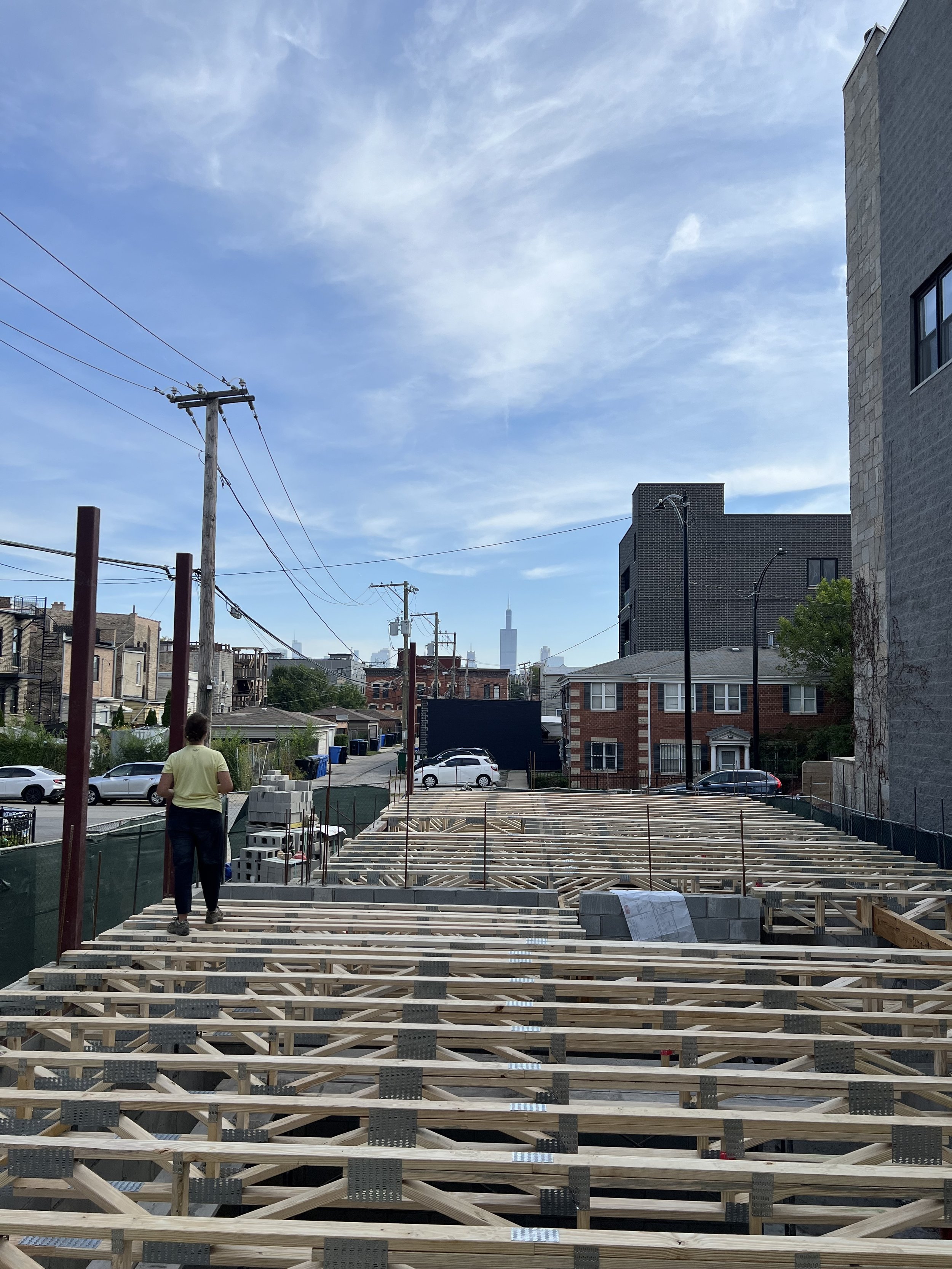


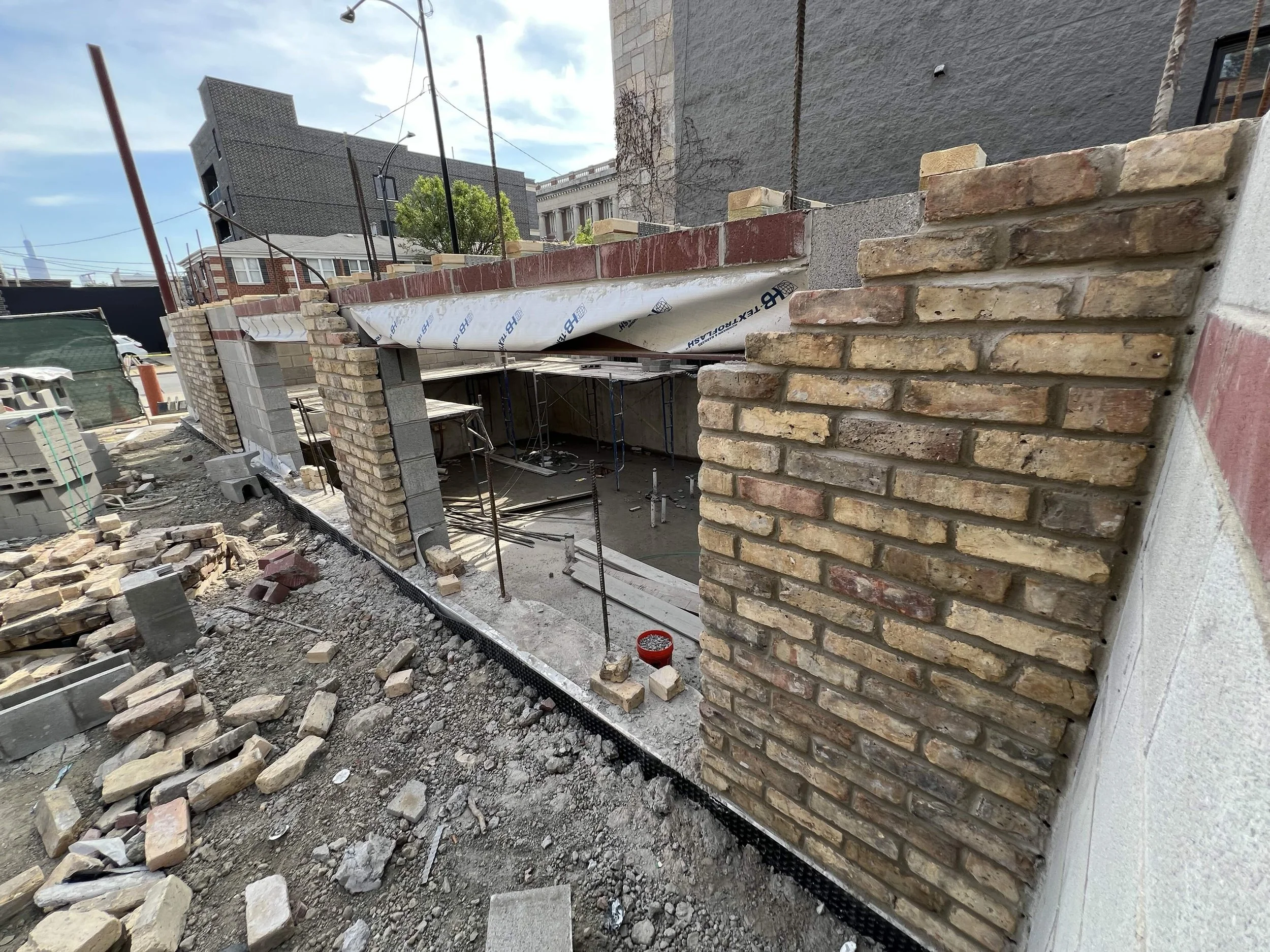
9/3/24
Rode our bikes to the site to inspect our beautiful foundation walls.


8/30/24
Formwork installation is completed and the concrete for the walls is poured today!
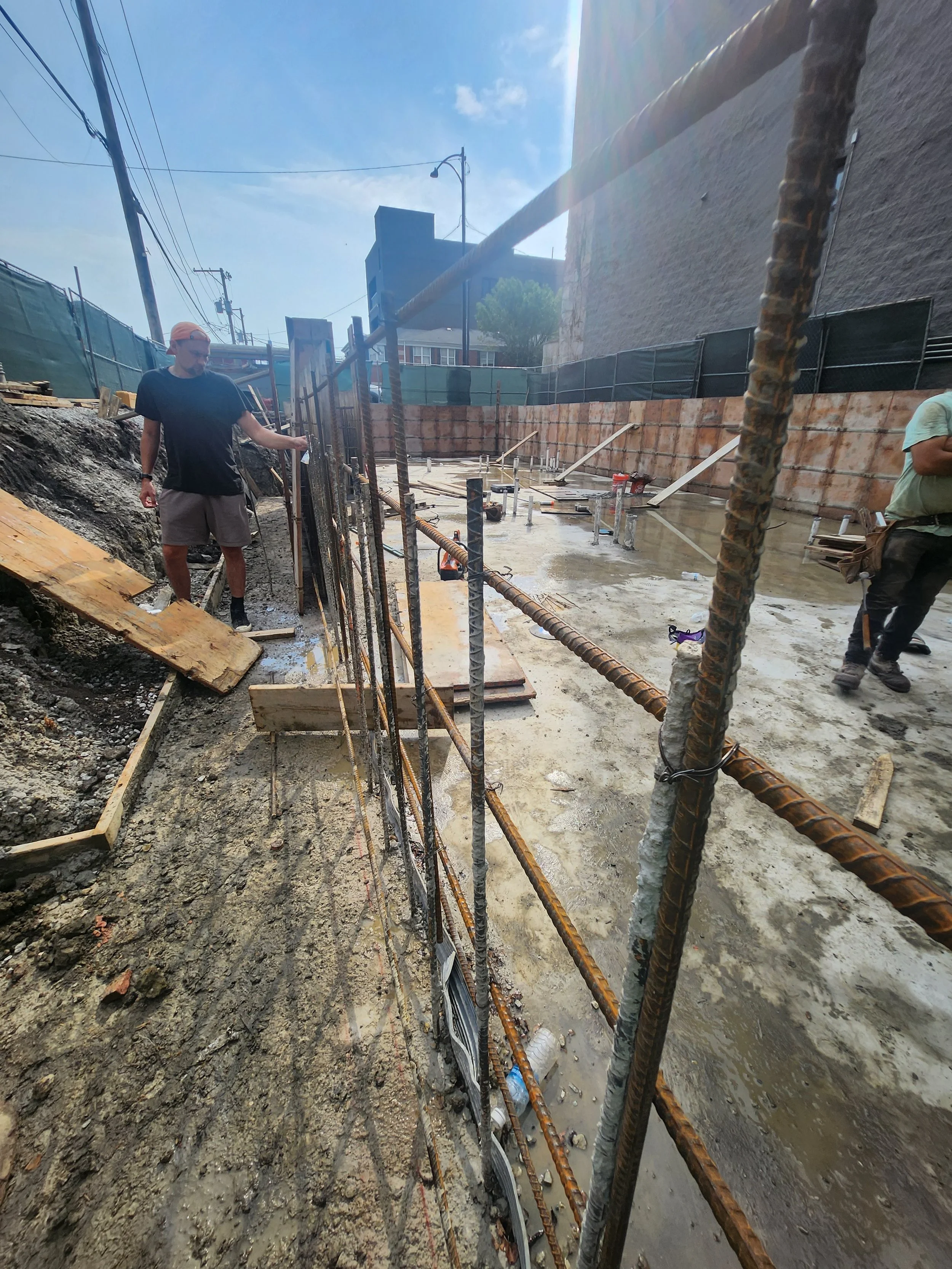





8/28/24
The 14” thick mat foundation was poured and left to cure. A rubber gasket was embedded in the mat while still wet to prevent water ingress. Now the concrete contractors begin to place rebar for the foundation walls and build the formwork






8/24/24
Rebar installation is complete!
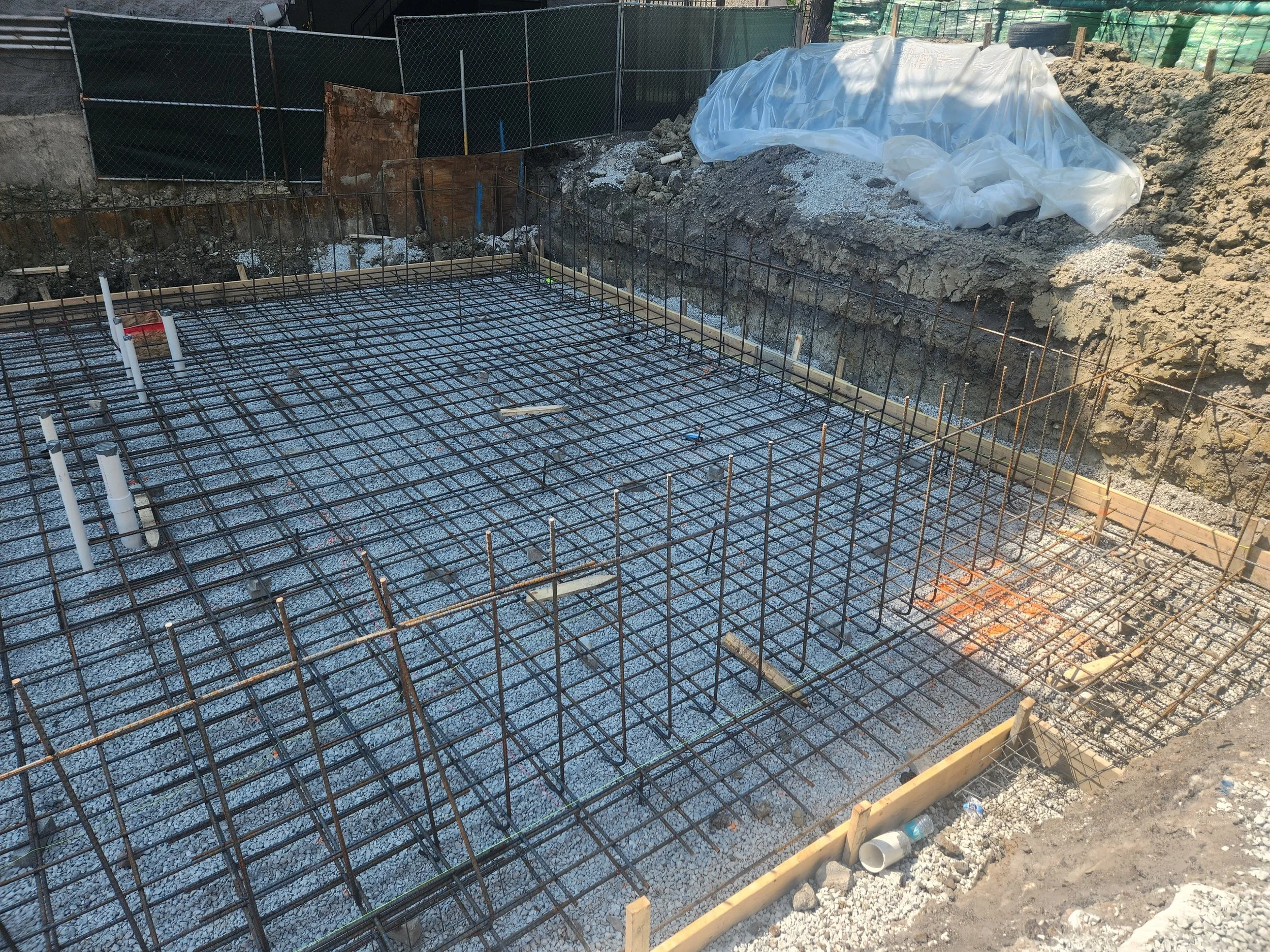
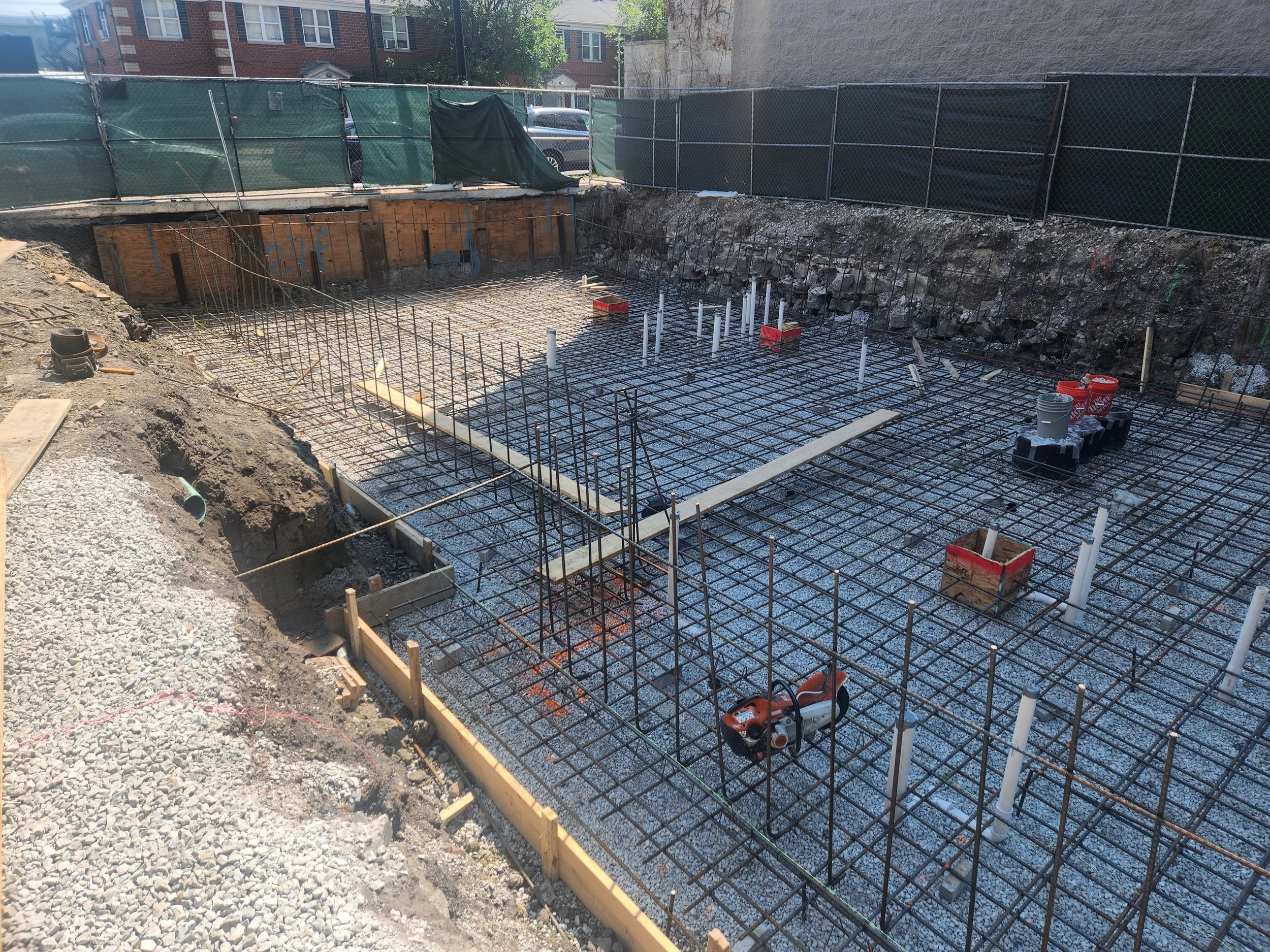

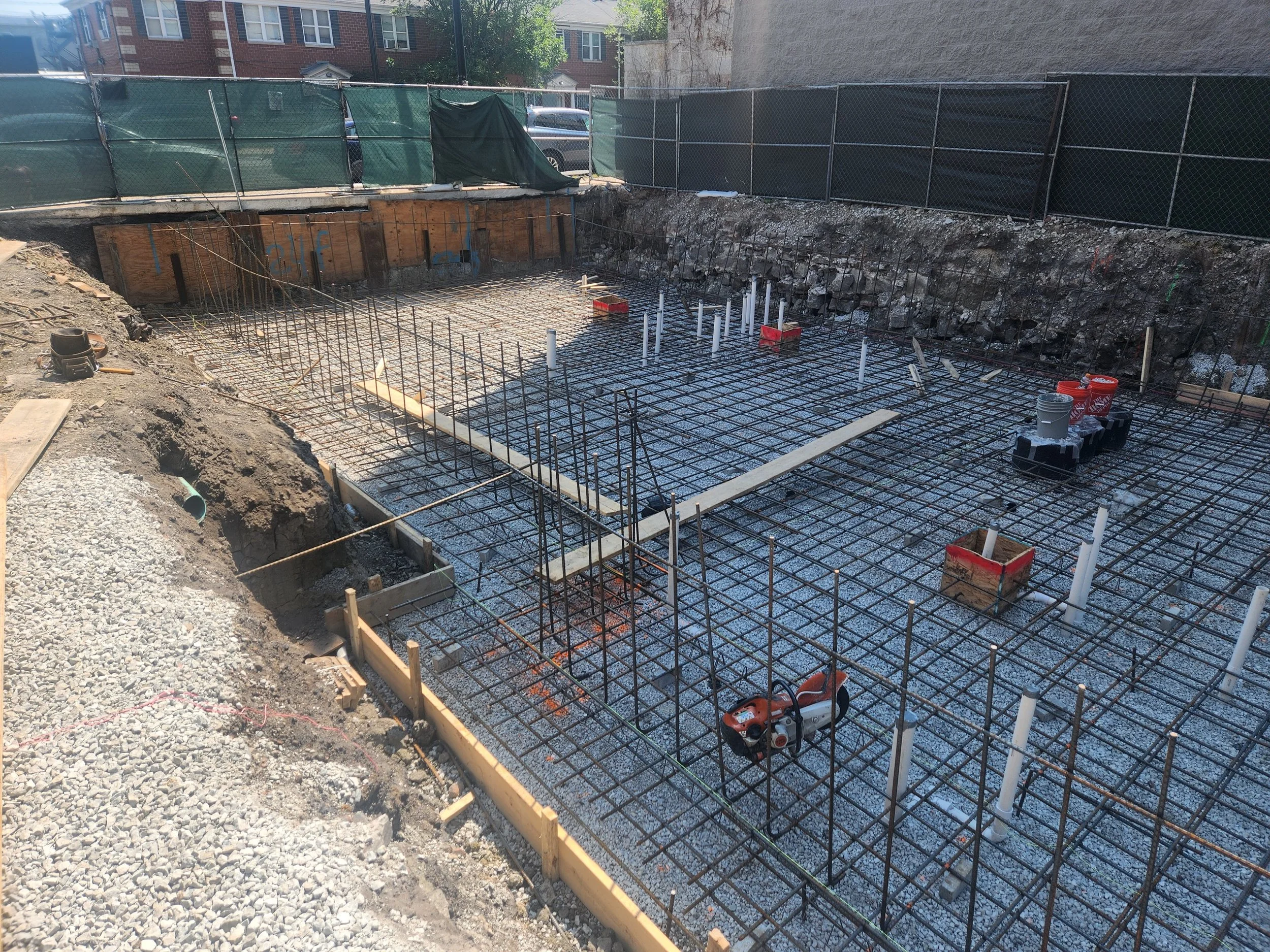
8/21/24
Another layer of rebar is added to finalize the grid structure. Additionally, upright rebar is being placed to tie the future foundation walls to the mat. We inspected the rebar and verified locations of the underground plumbing in relation to the perimeter of the mat.



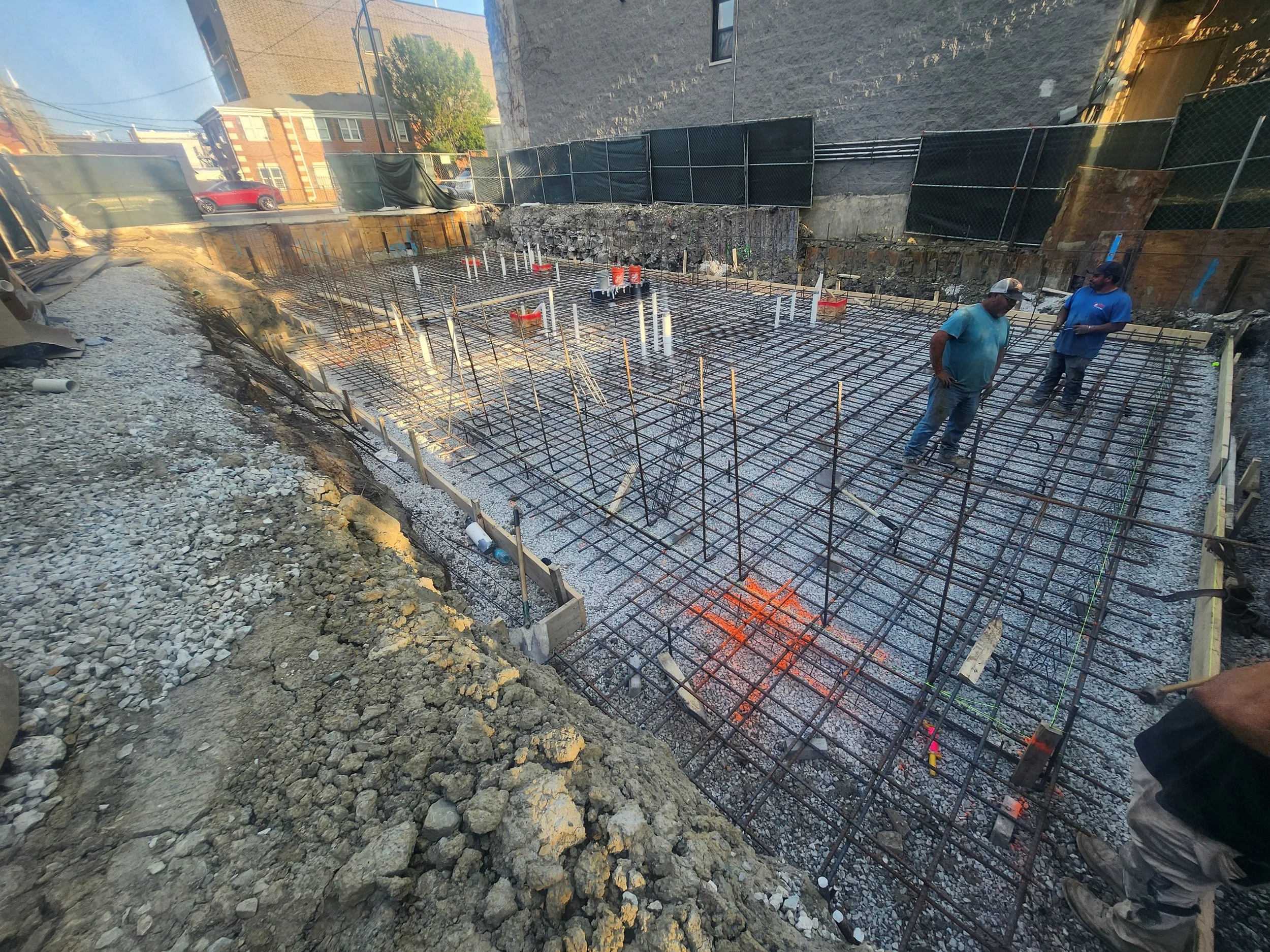
8/17/24
The prep work required before pouring the mat foundation continues with the formwork and the first layer of rebar.



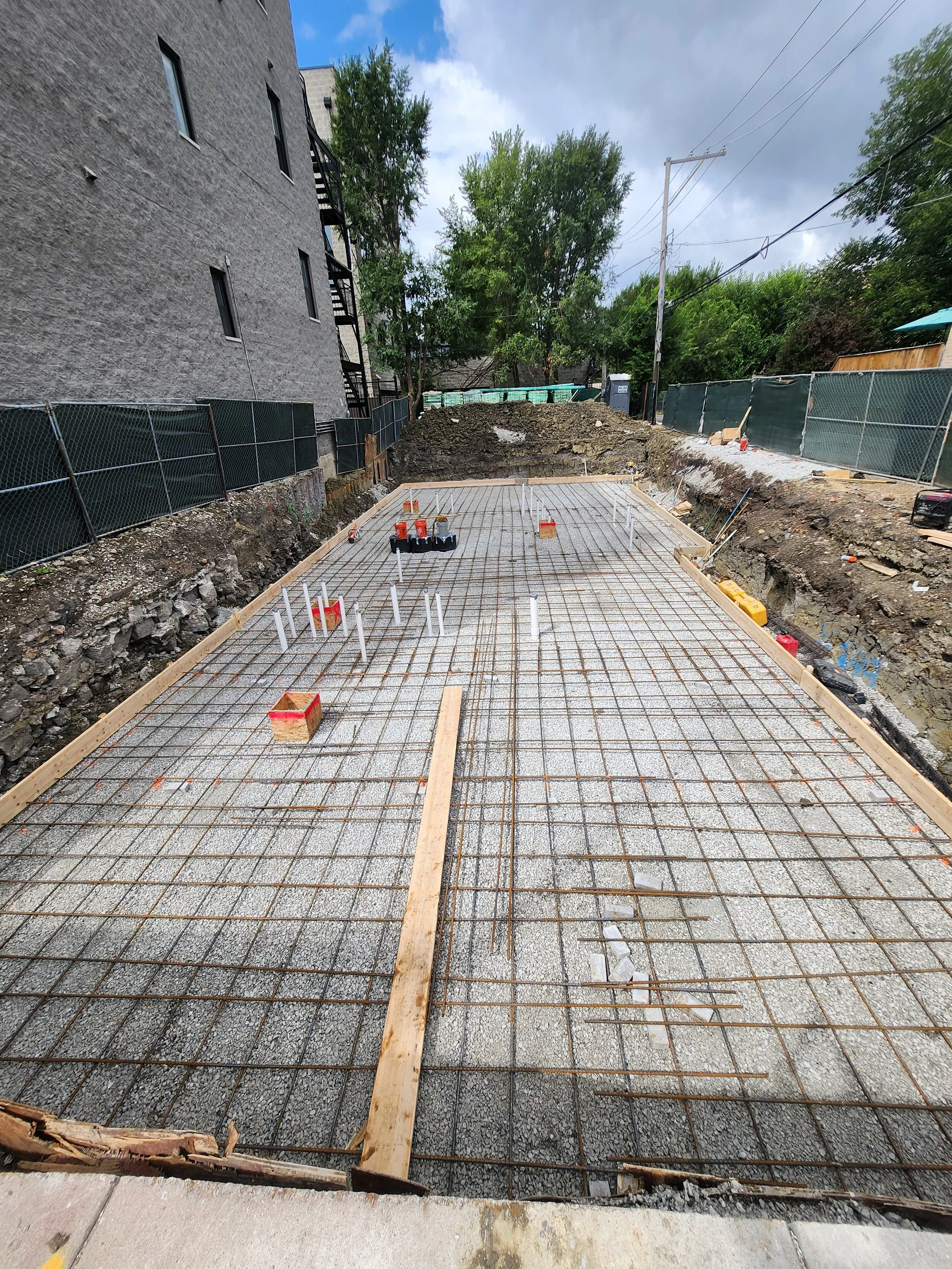
8/16/24
Underground plumbing inspection PASSED!
8/14/24
With the foundation issue sorted, we were able to move forward with the underground plumbing.
Our plumbing team was able to get everything installed in a day!

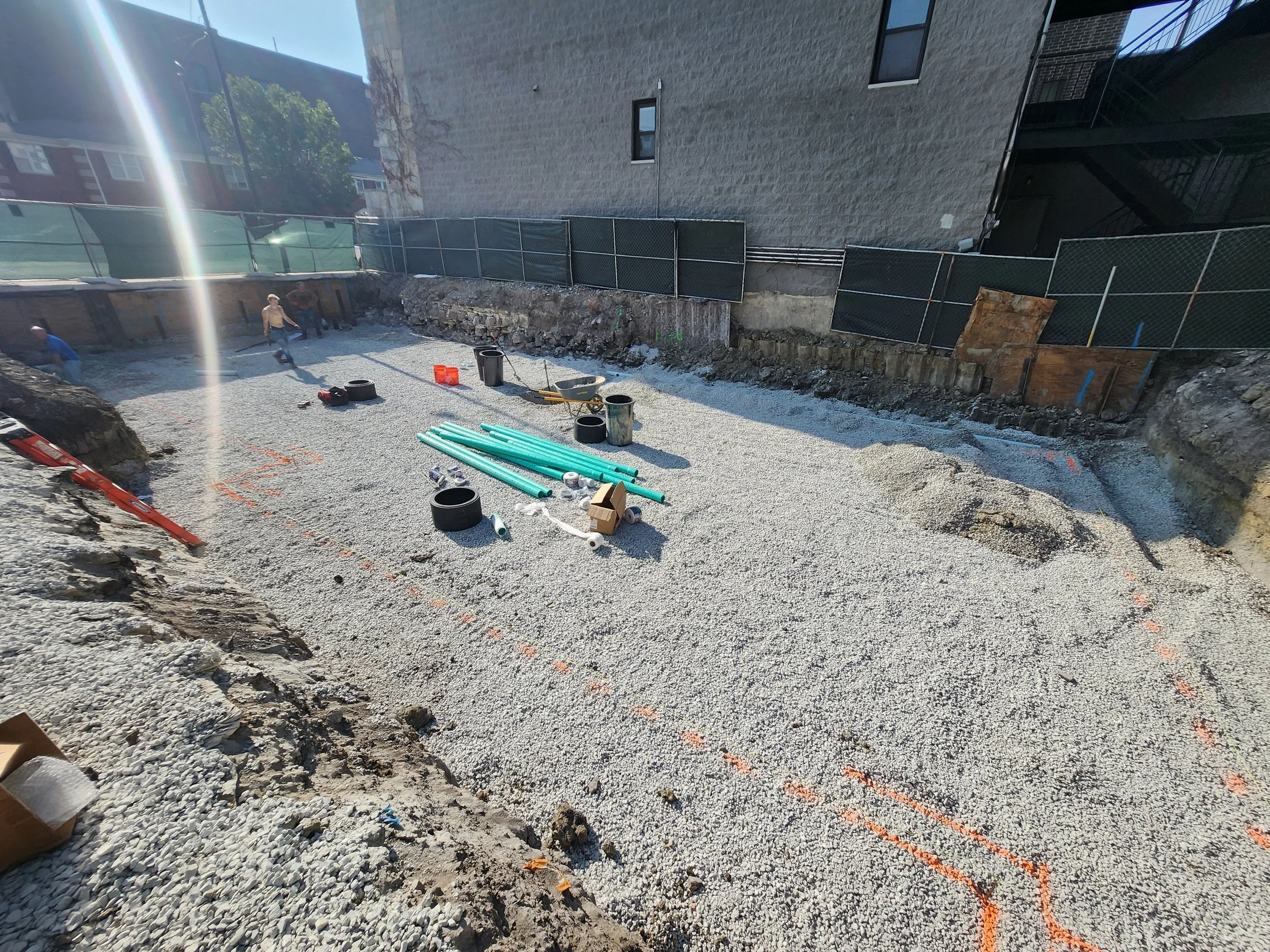

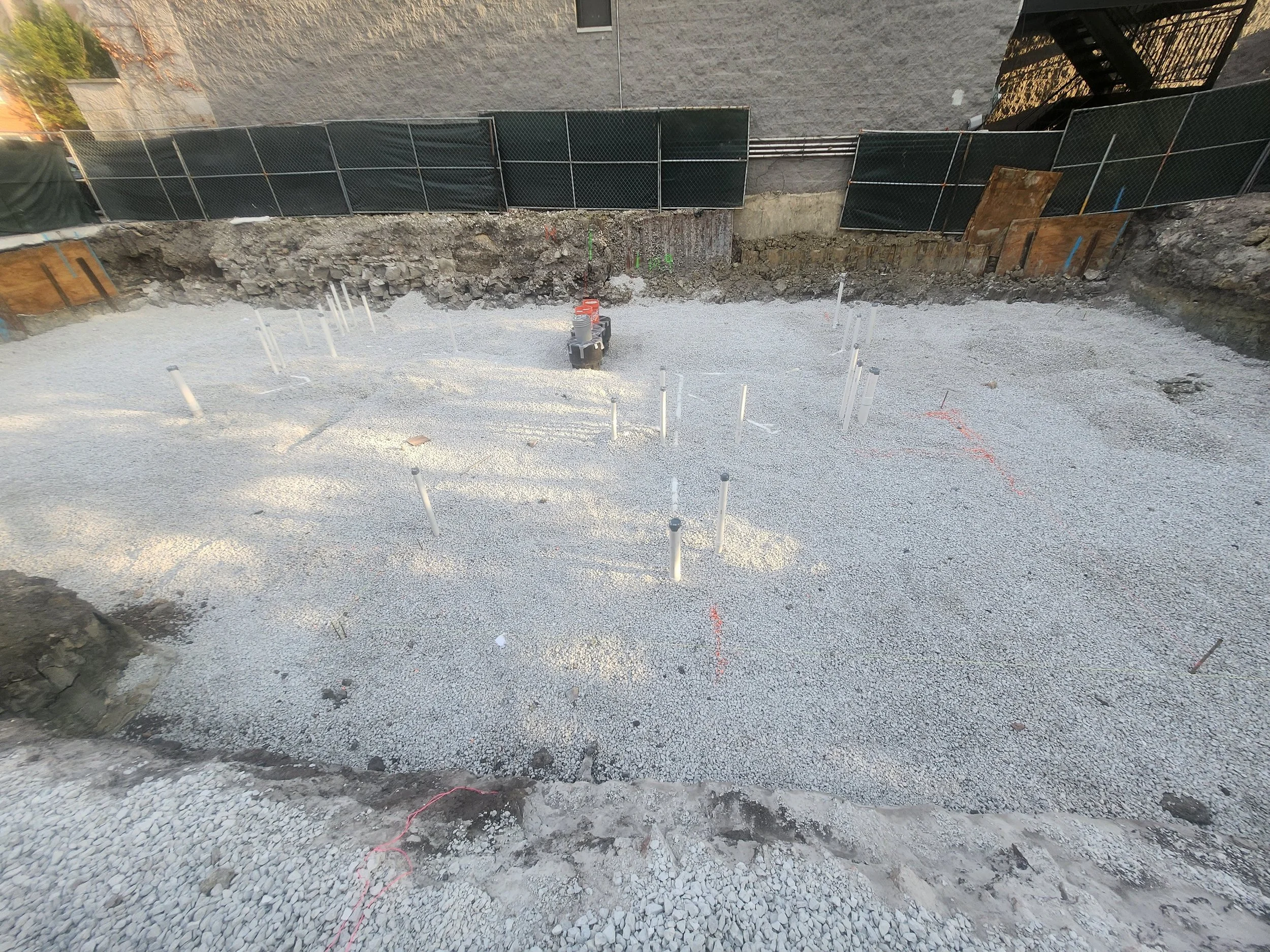
8/14/24
We have some exciting news to share about the area surrounding 222 S Oakley — introducing the 1901 Project!
A transformative $7 billion private investment on Chicago’s West Side celebrating Chicago’s unique spirit. Spearheaded by the Reinsdorf and Wirtz families, The 1901 Project will transform the West Side with a jolt of new development, bridging neighborhoods and enhancing opportunities for residents, businesses and all of Chicago.
The vision features a more than 10-acre elevated urban design strategy. The public park aims to establish new open space that connects the community to nature, furthering the legacy of iconic public spaces throughout the city and includes a walking path that will celebrate the West Side and Chicago’s rich history of sports and music.
This impressive development will be a 10-minute walk from our project site and will greatly enhance the surrounding neighborhood, pushing economic development westward.
For more detailed information, visit: https://www.the1901projectchicago.com


8/5/24
The current phase of the project involves ground work and preparation for pouring the foundation. We’ve found that we have soil thats a bit weaker than anticipated, so our team is modifying the foundation design to compensate. This critical step sets the stage for the construction of the new building, providing a solid and secure base for all future work.
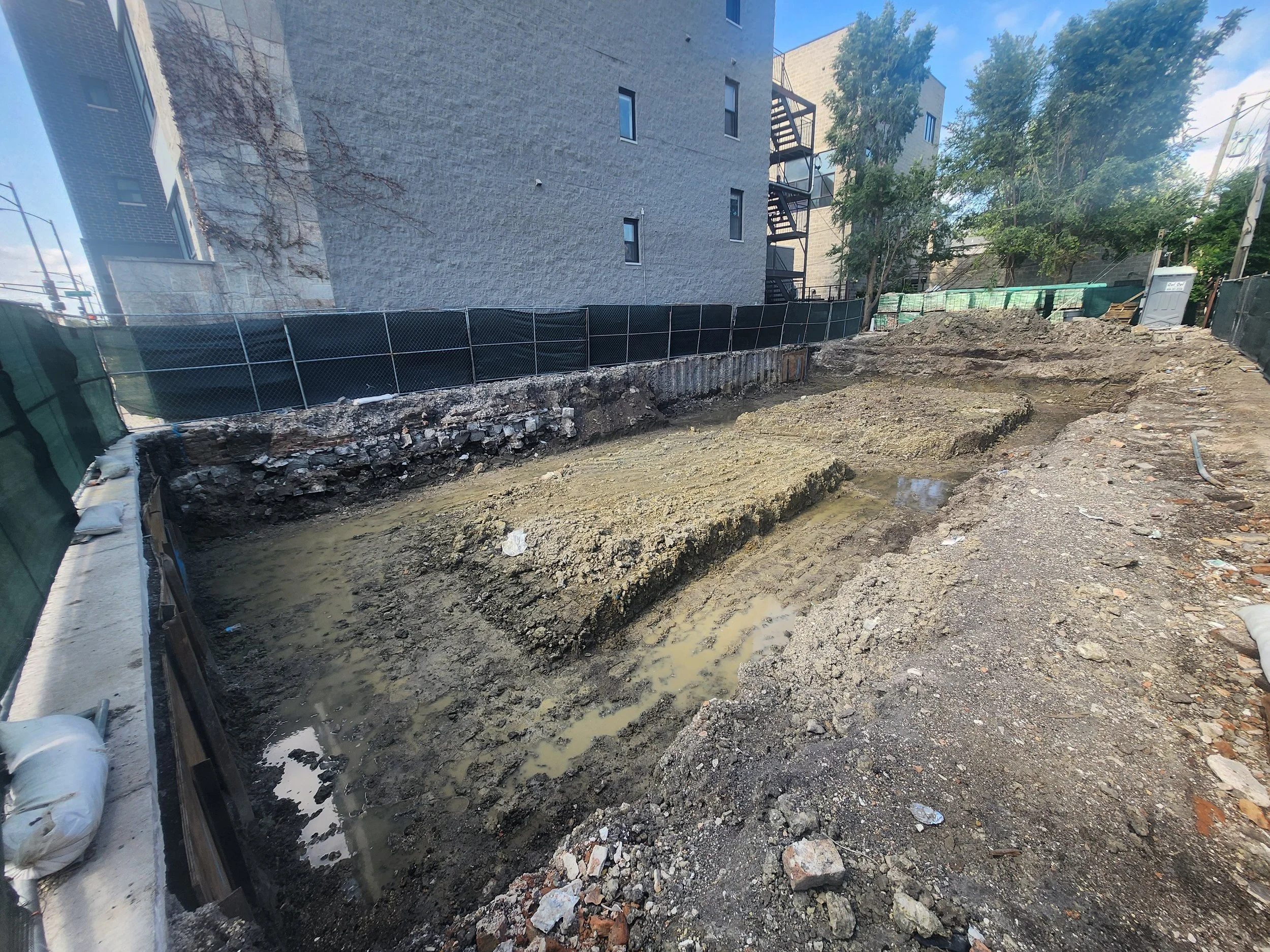
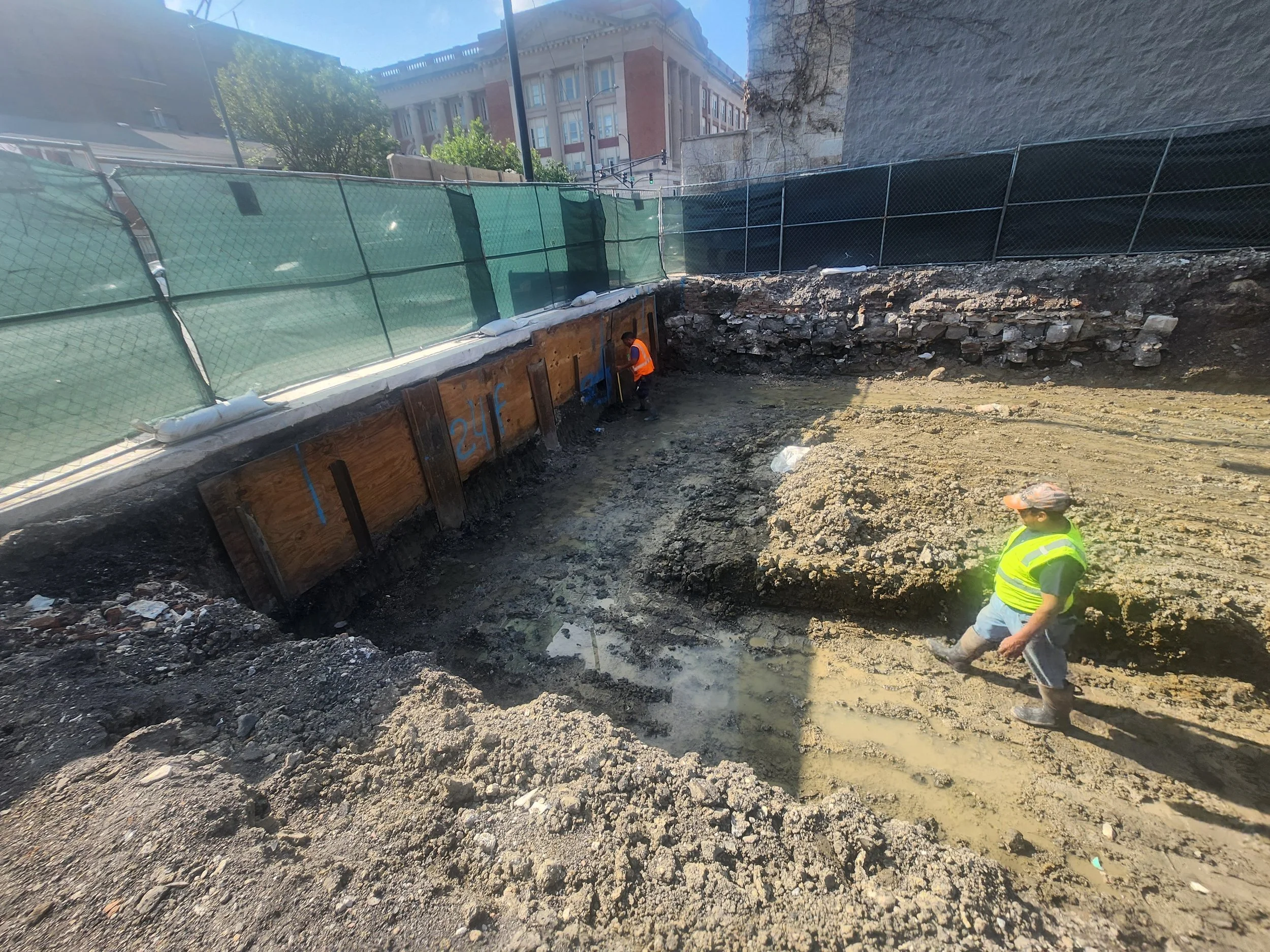

6/5/24
It’s gone!

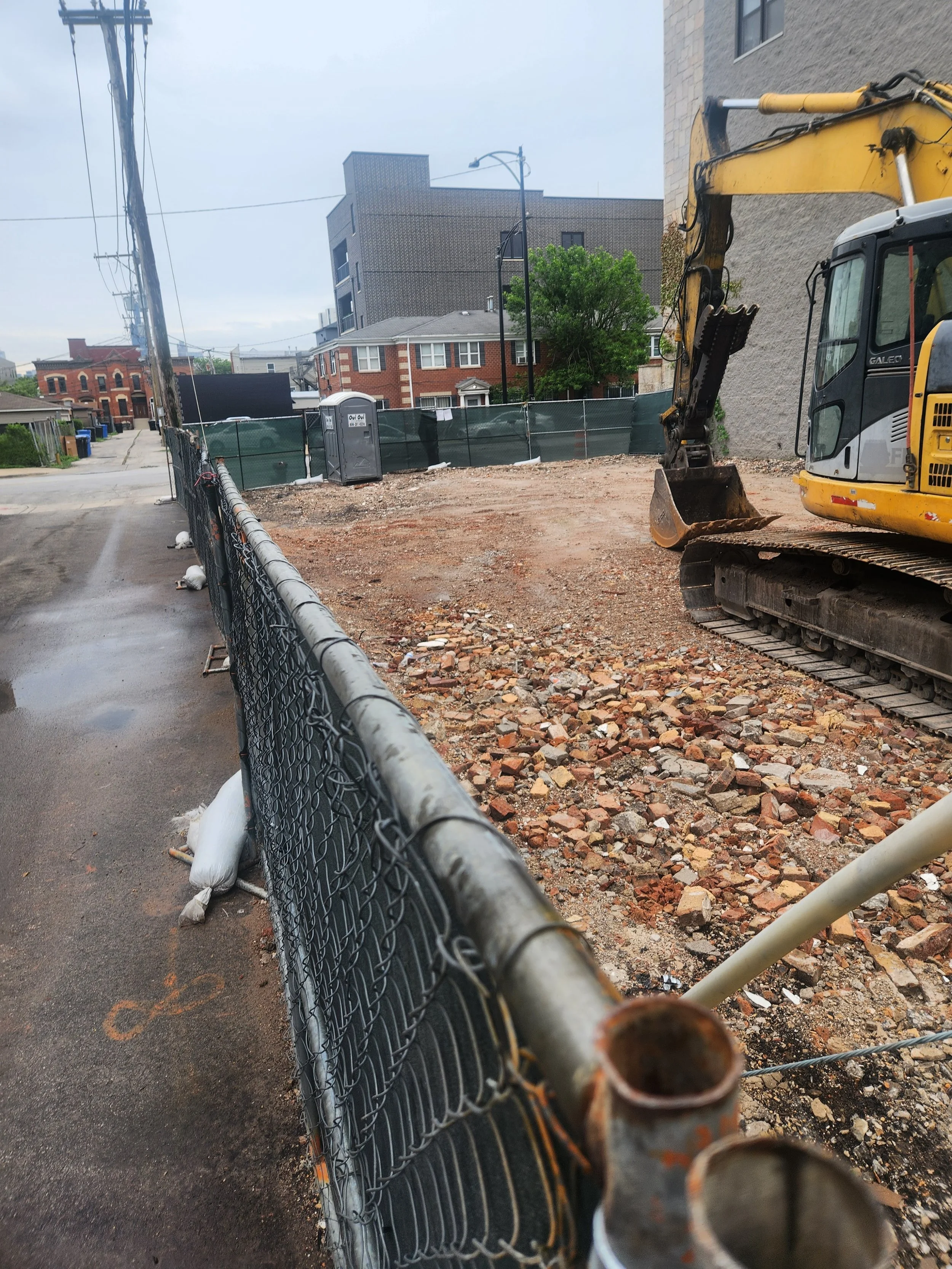
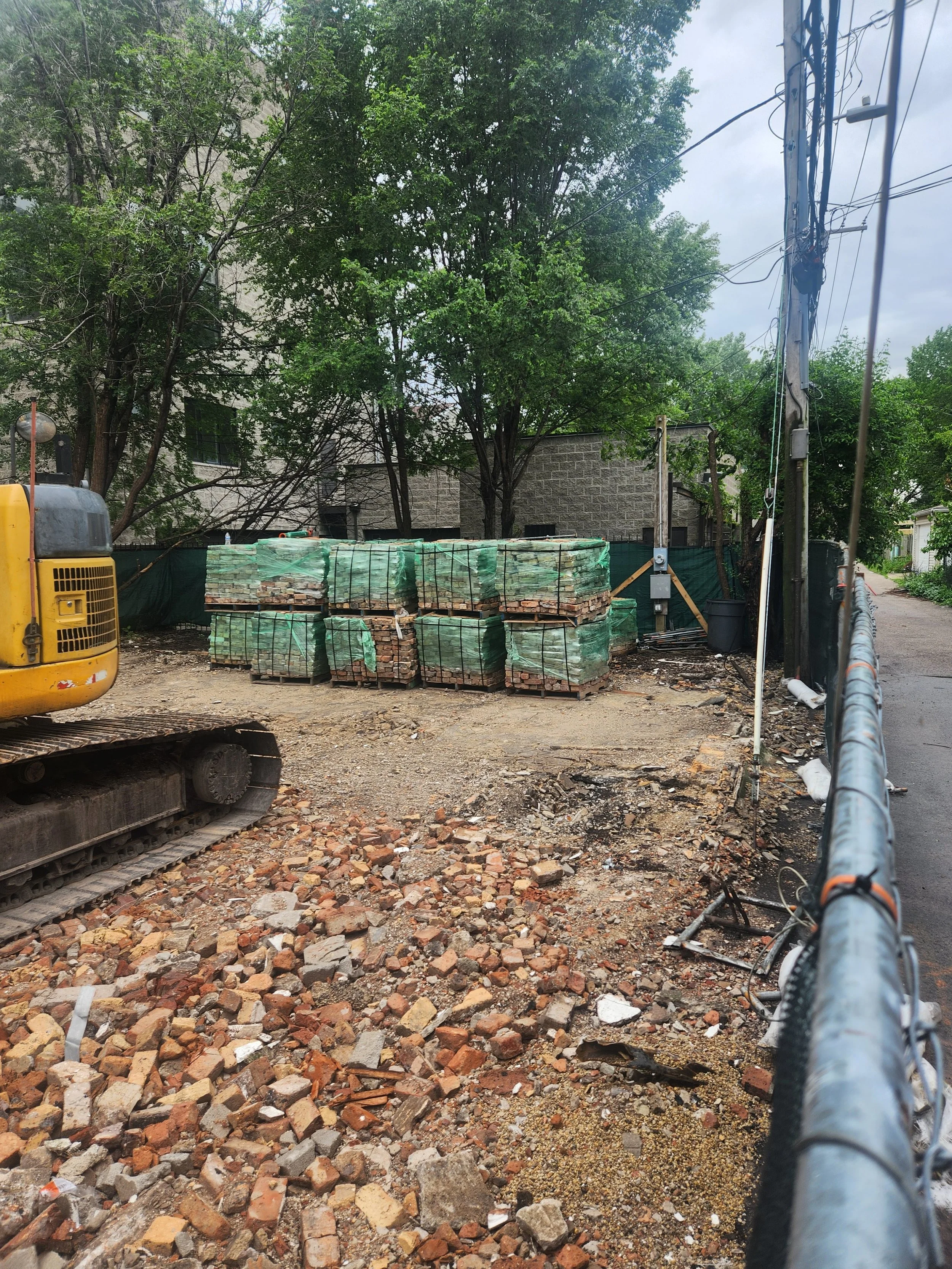
5/31/24
Today the sorted bricks are being palletized so the masons can easily move them around the site.
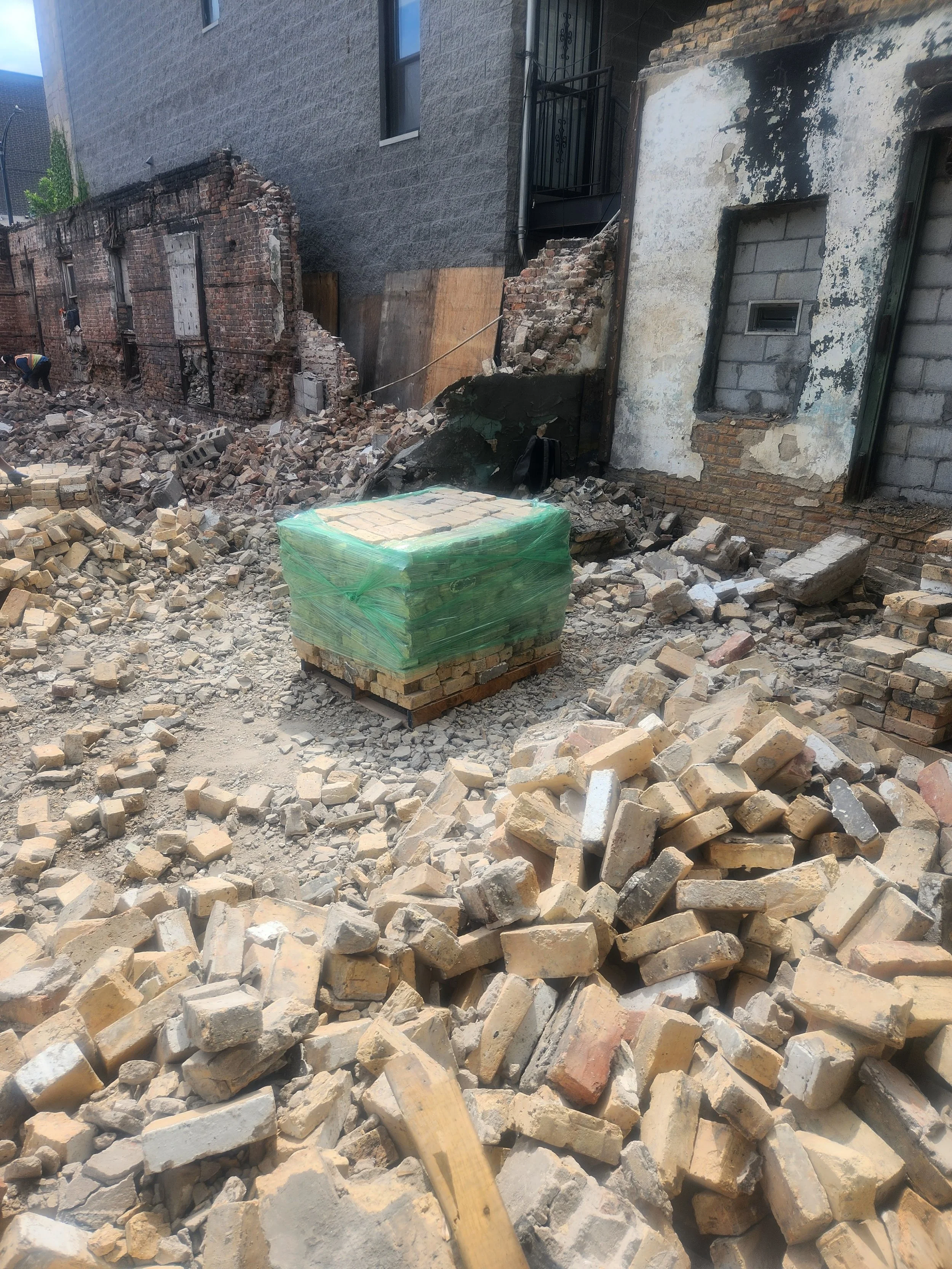
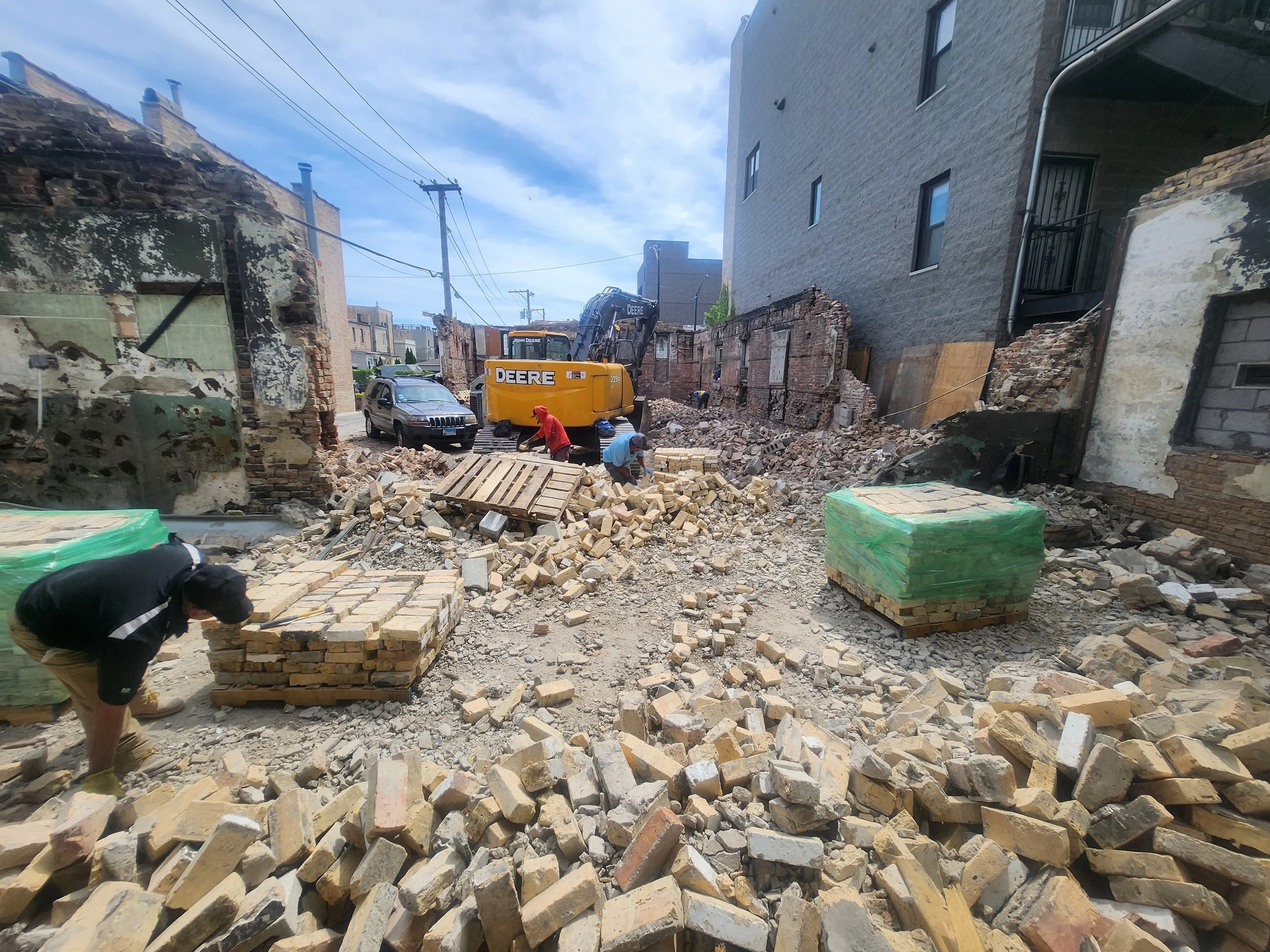
5/30/24
Day Two was spent sorting through the debris and removing scrap metal and lumber. The old “Chicago Common” bricks are highly coveted — they will be salvaged and reused for the new building facade.



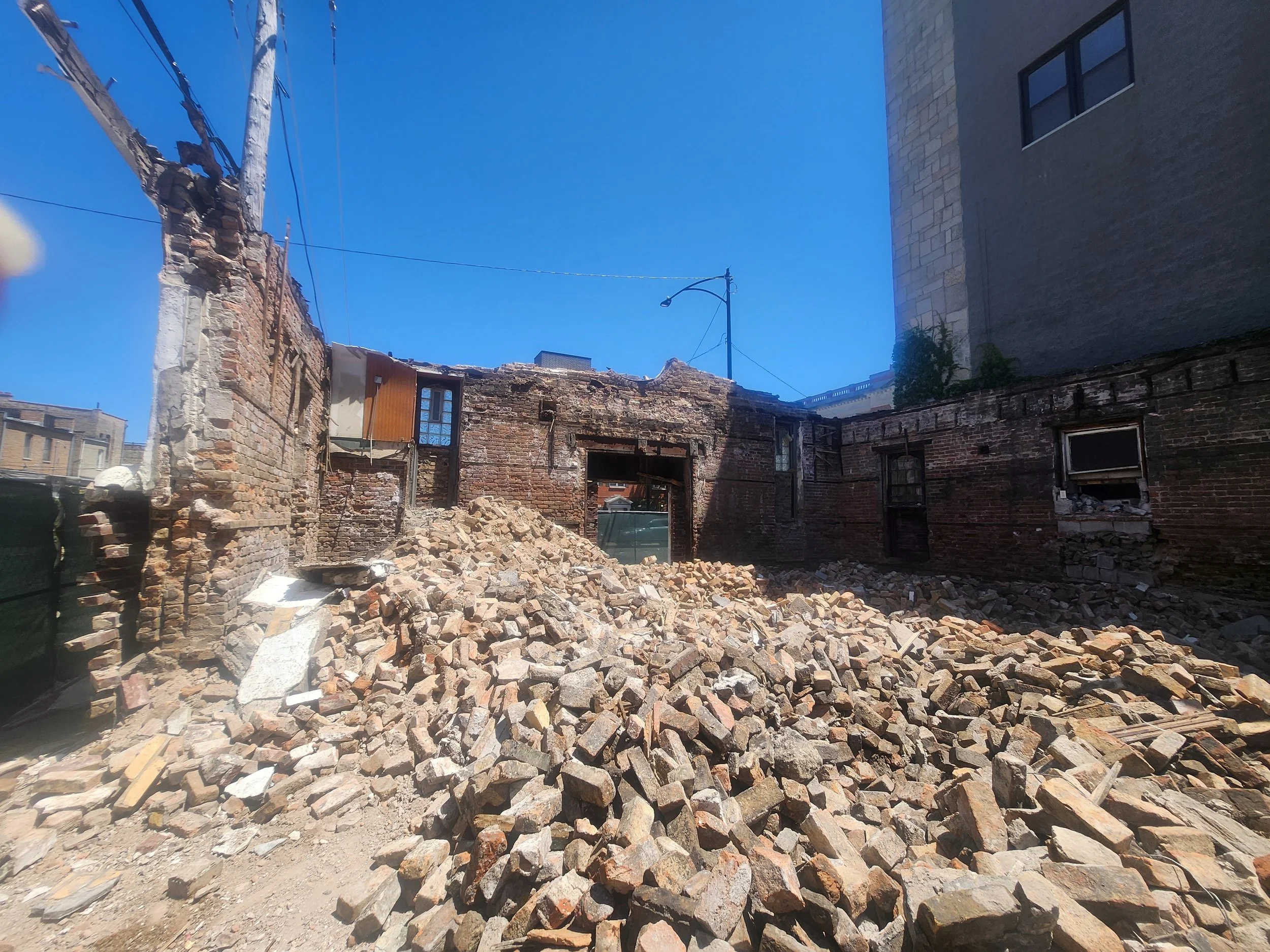
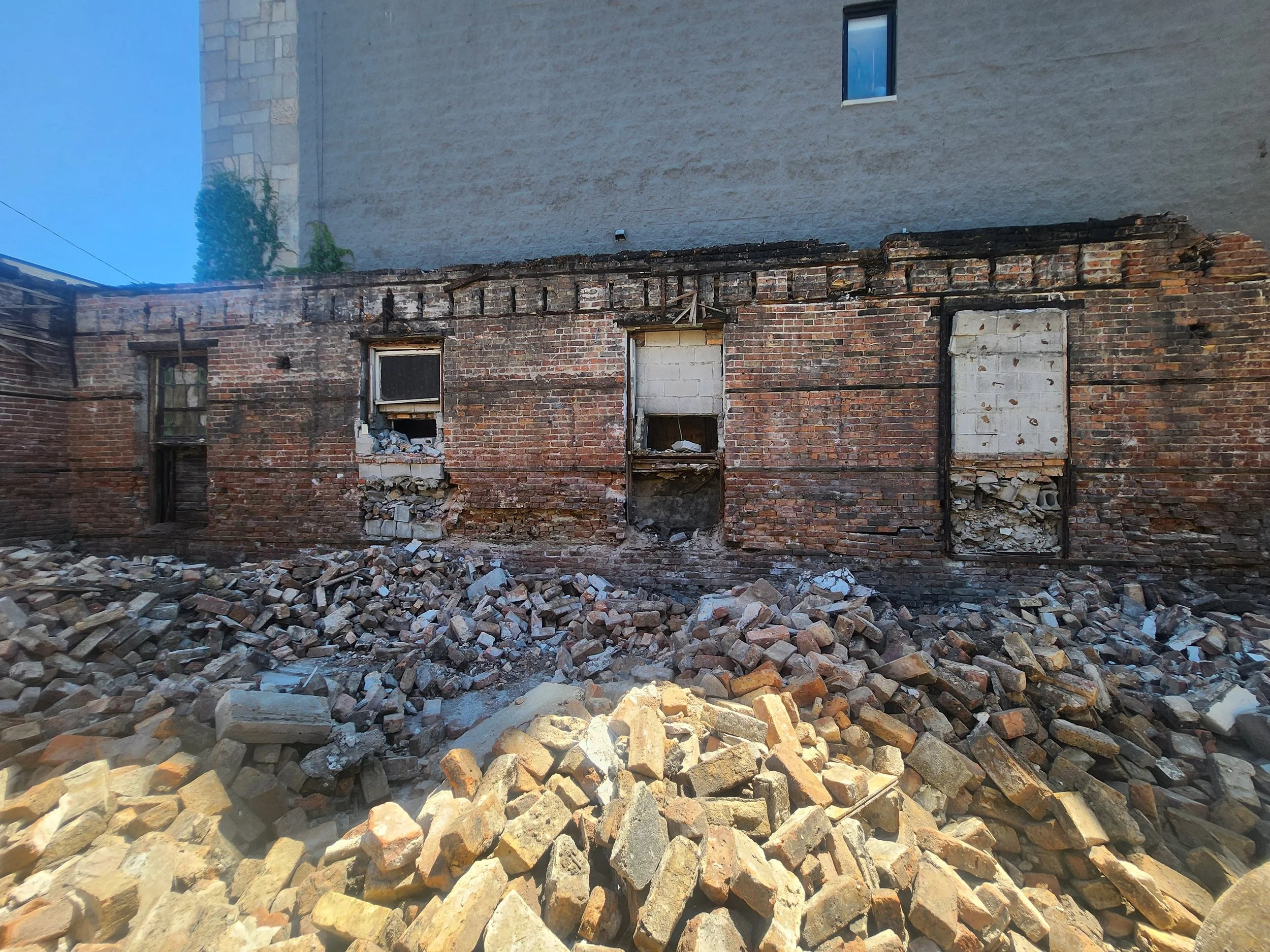
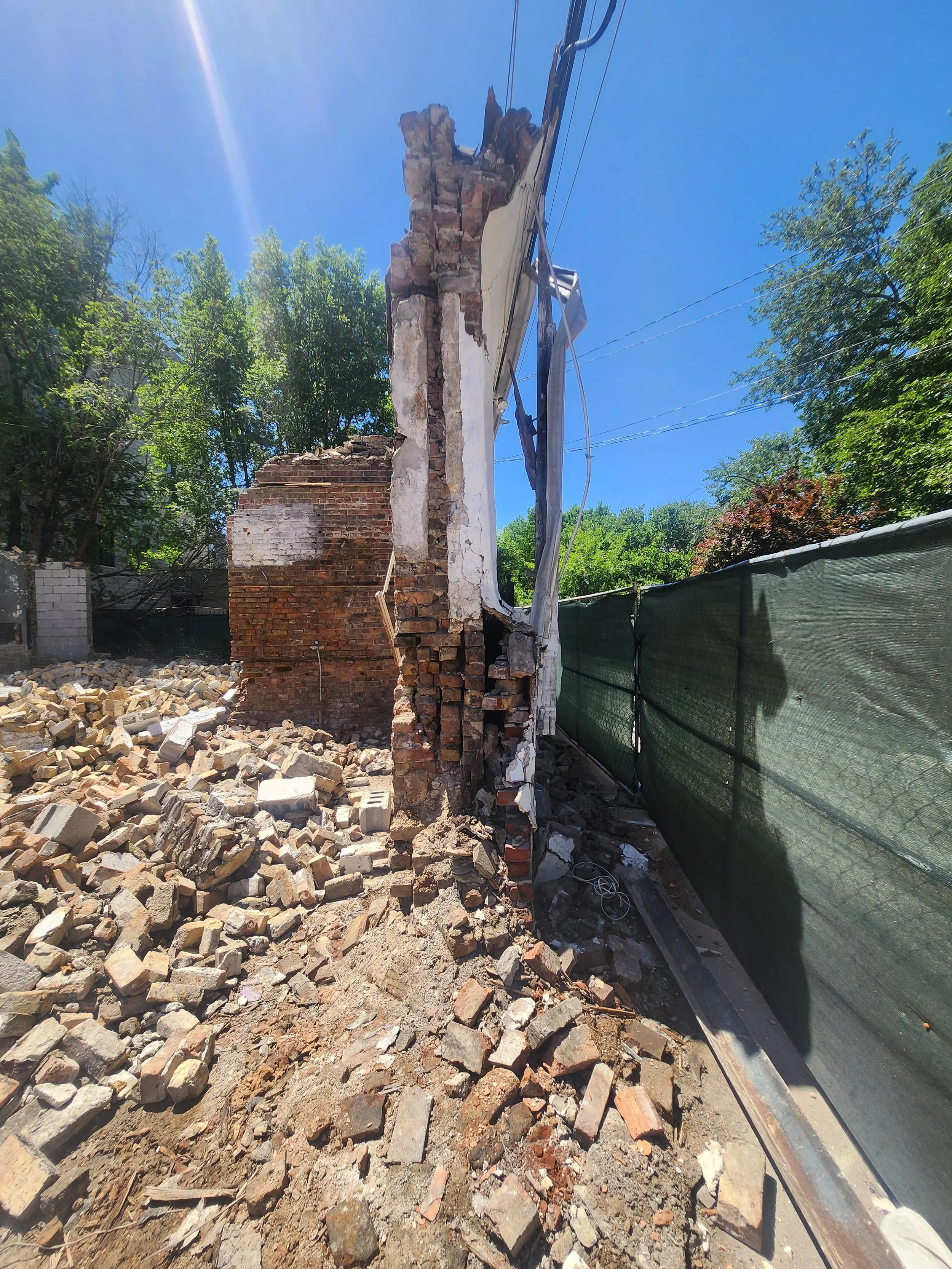
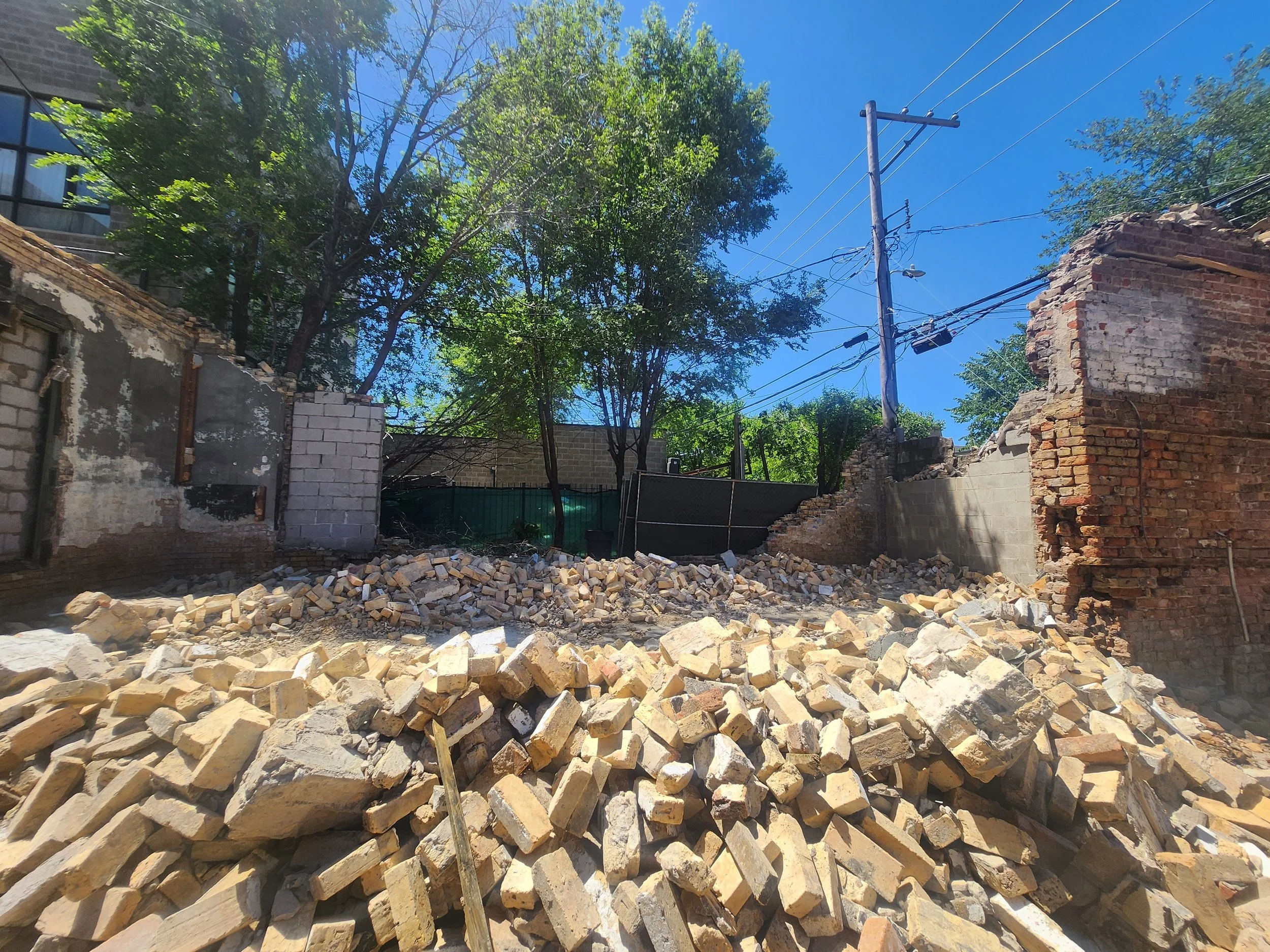

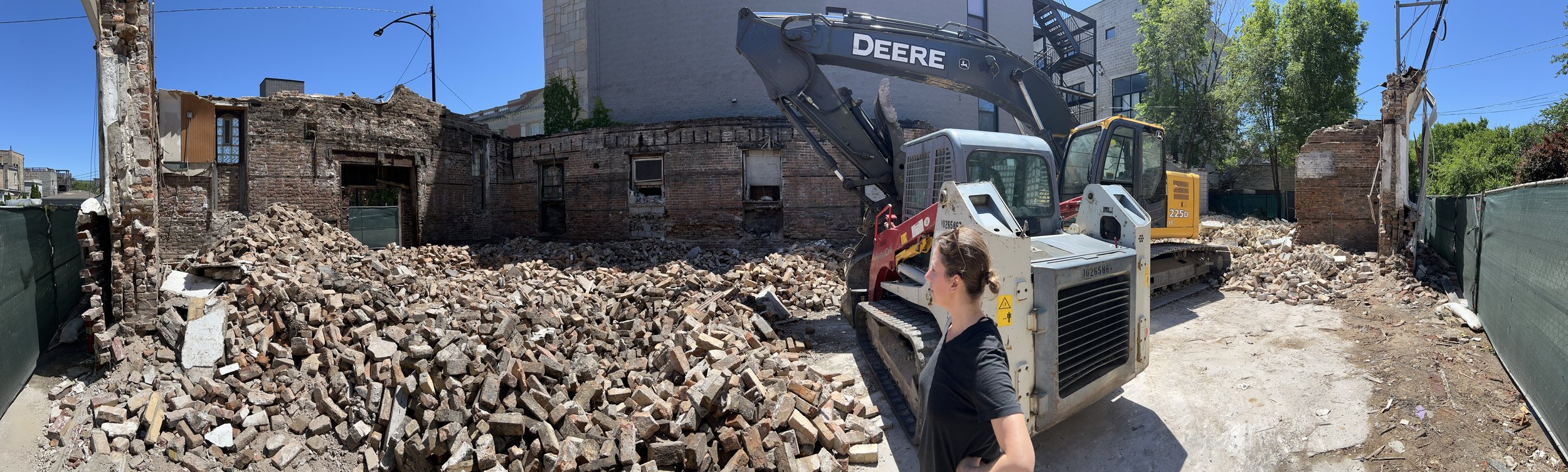

5/28/24
After weeks of navigating the bureaucratic permitting process, we finally secured the coveted demolition permit. We watched in awe as Carlos of Carlos Group skillfully piloted his demolition equipment. It was very cool to see in person. We were surprised at the amount of material he was able to remove on the first day and it made us hopeful the process might wrap up sooner than expected.
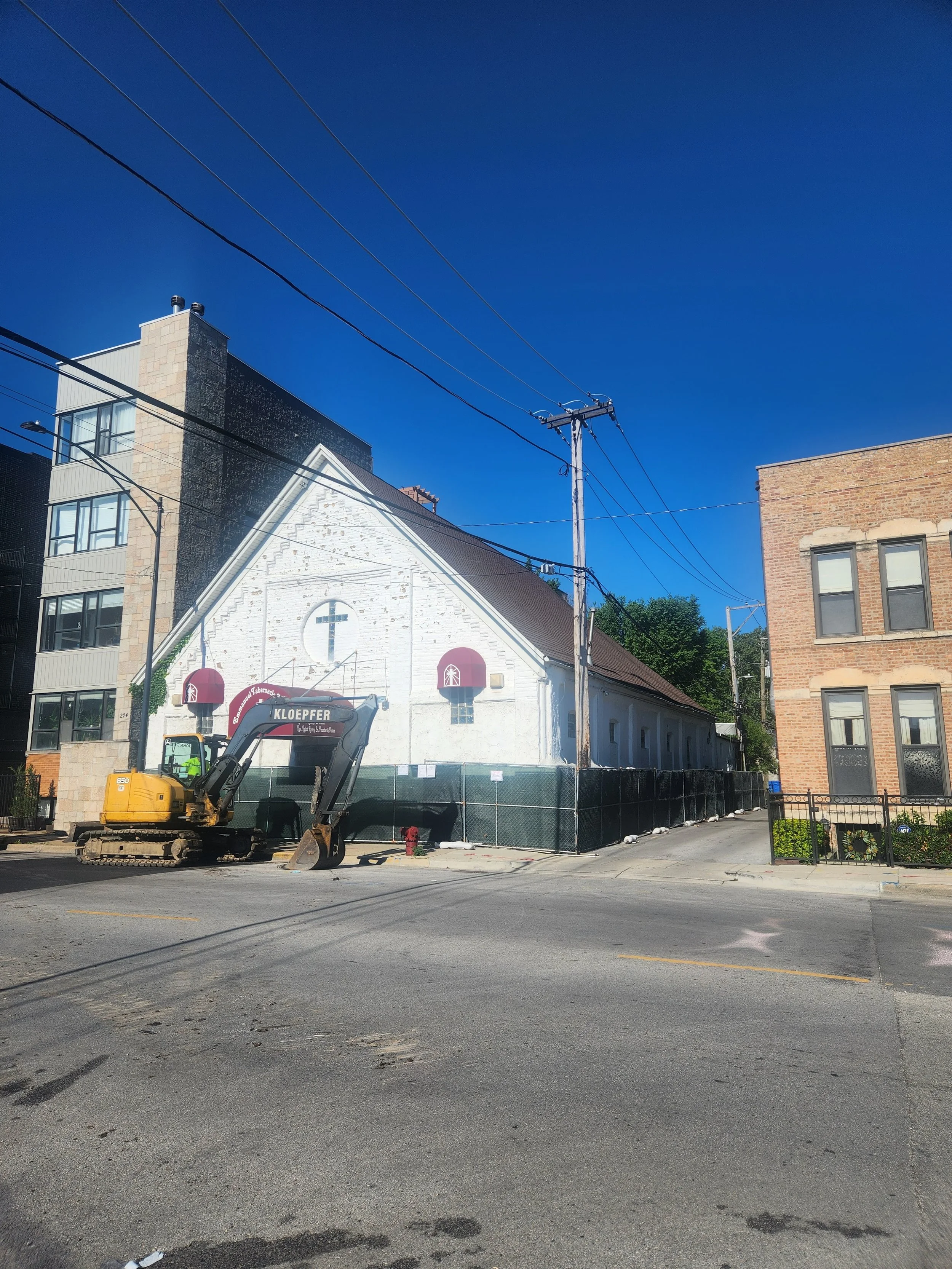
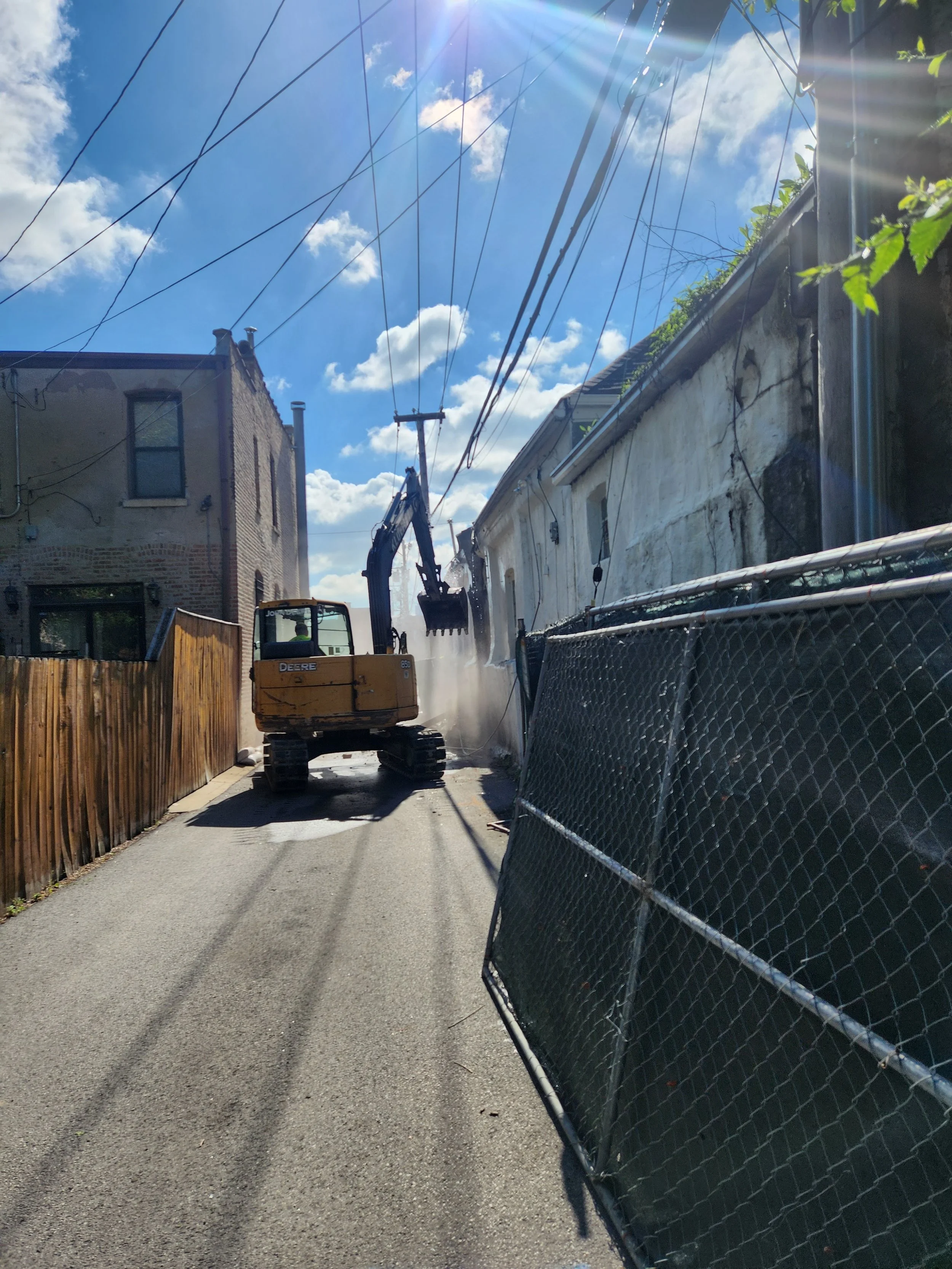
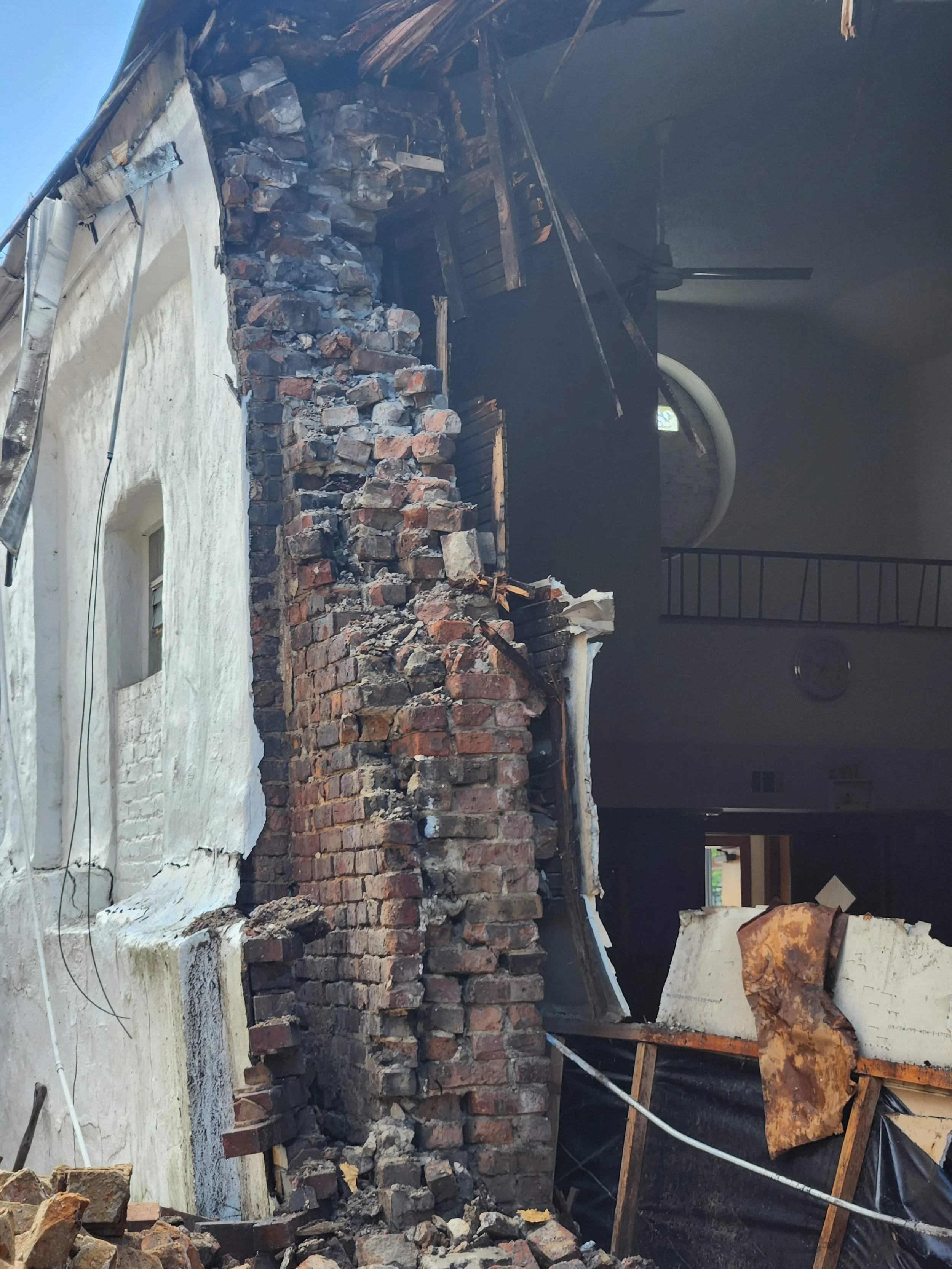
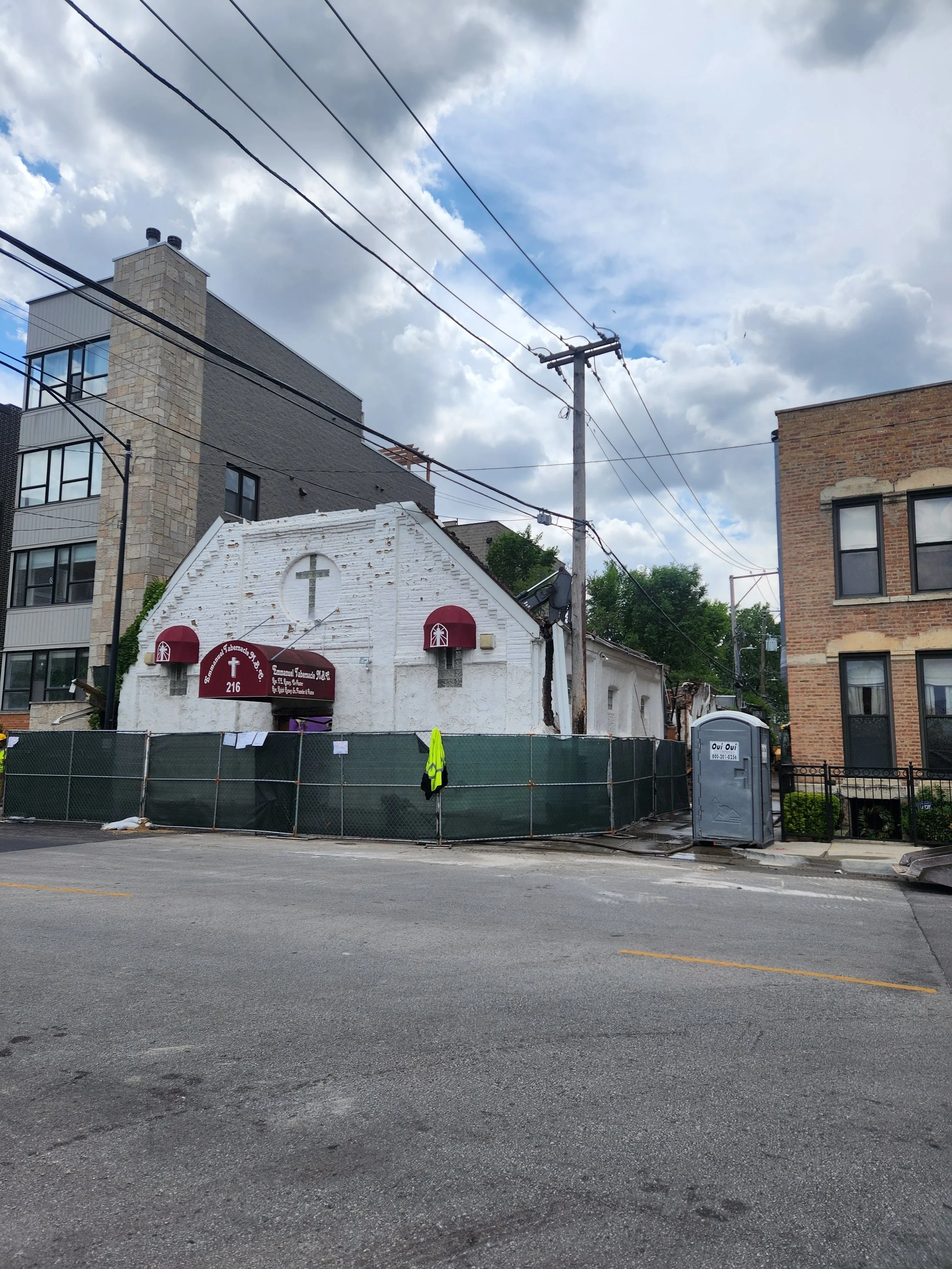


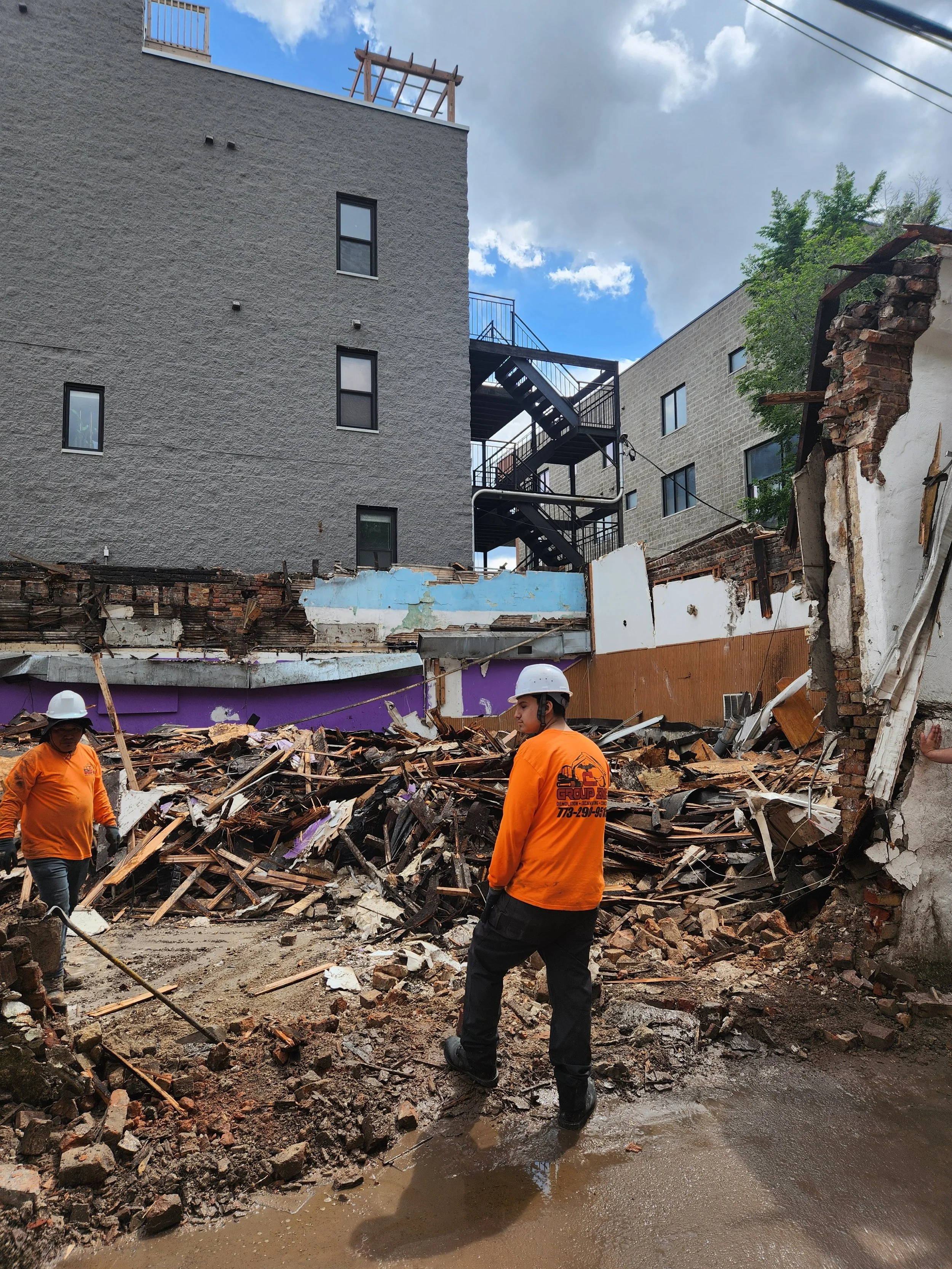
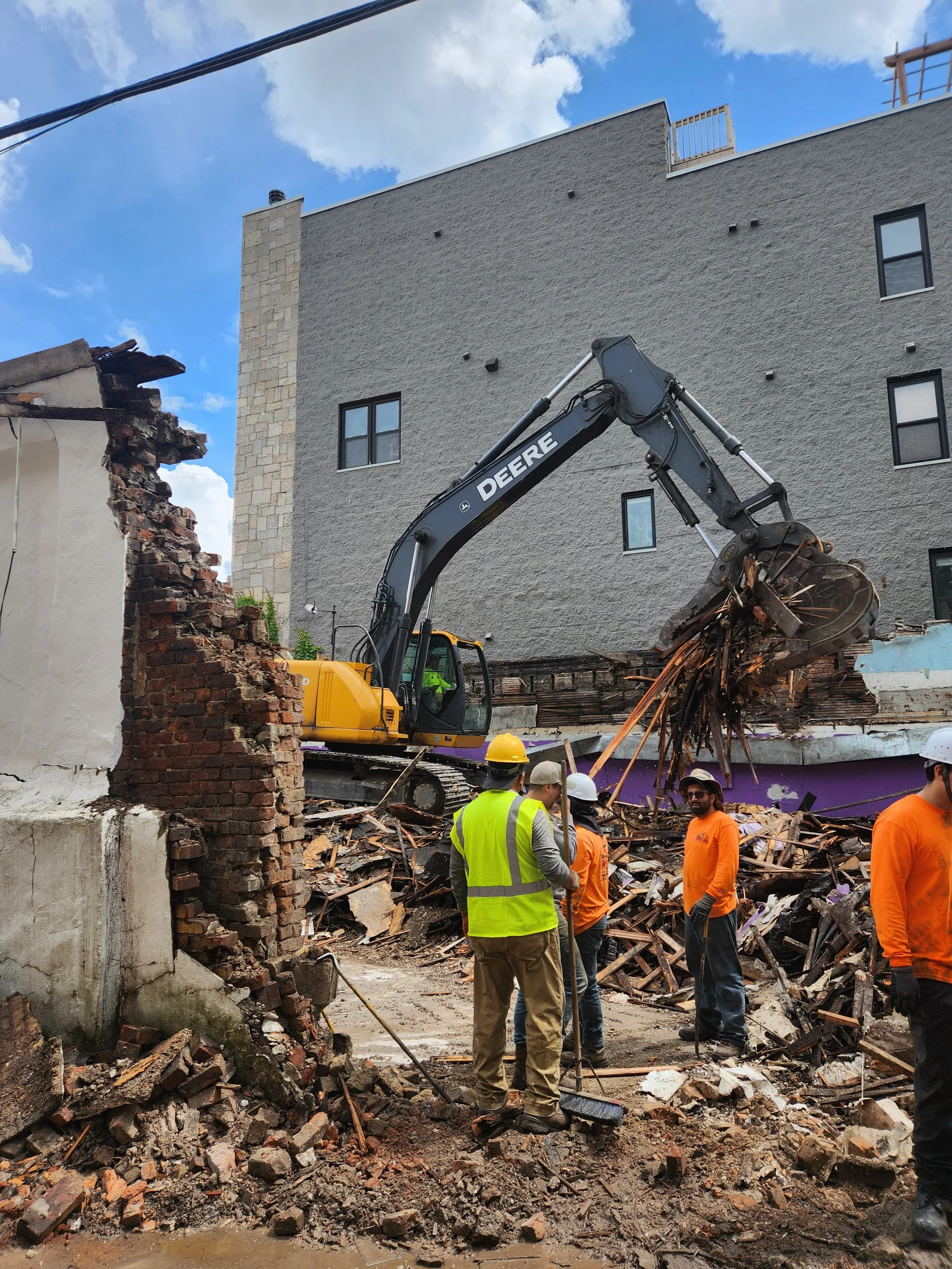
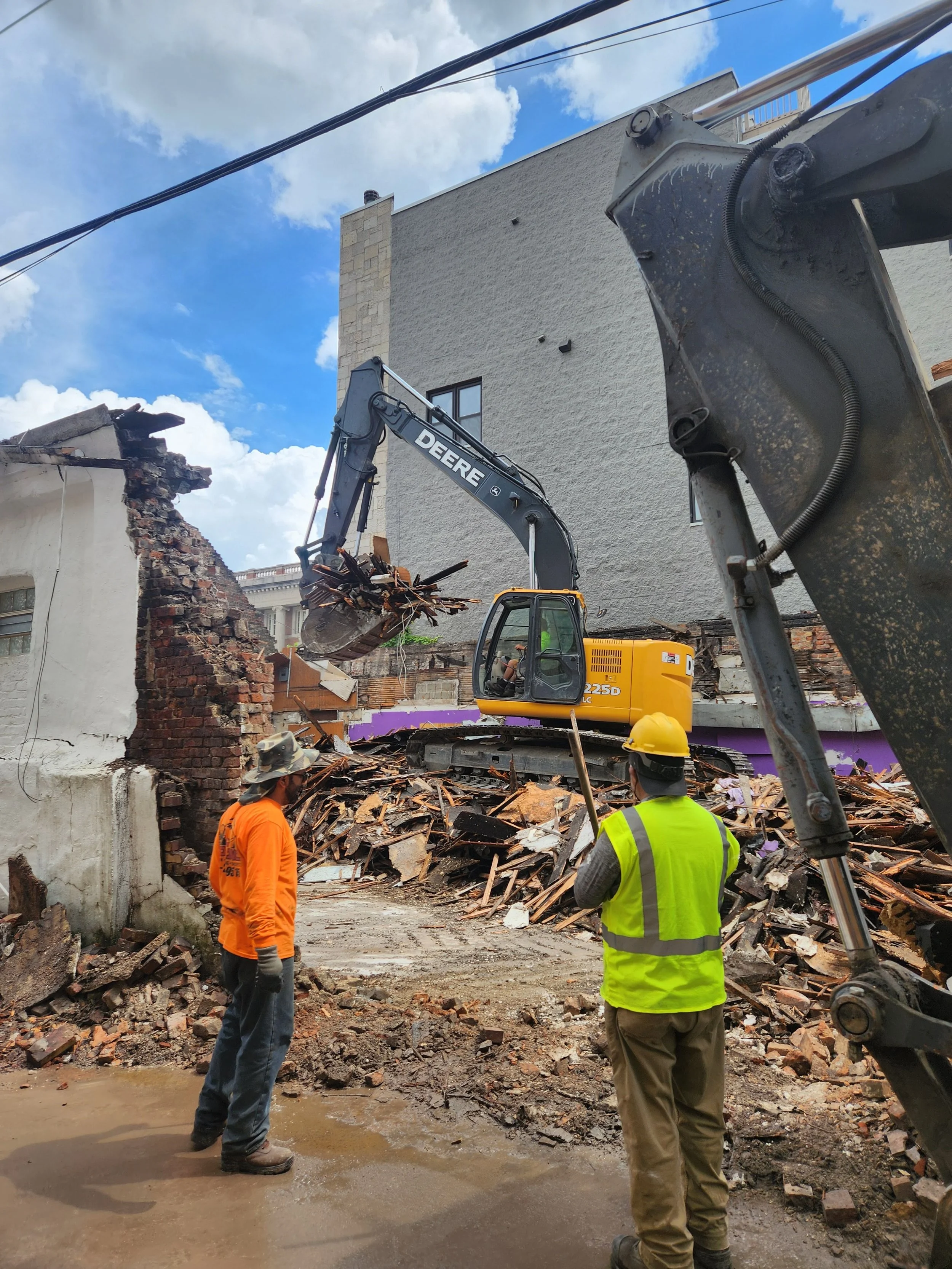
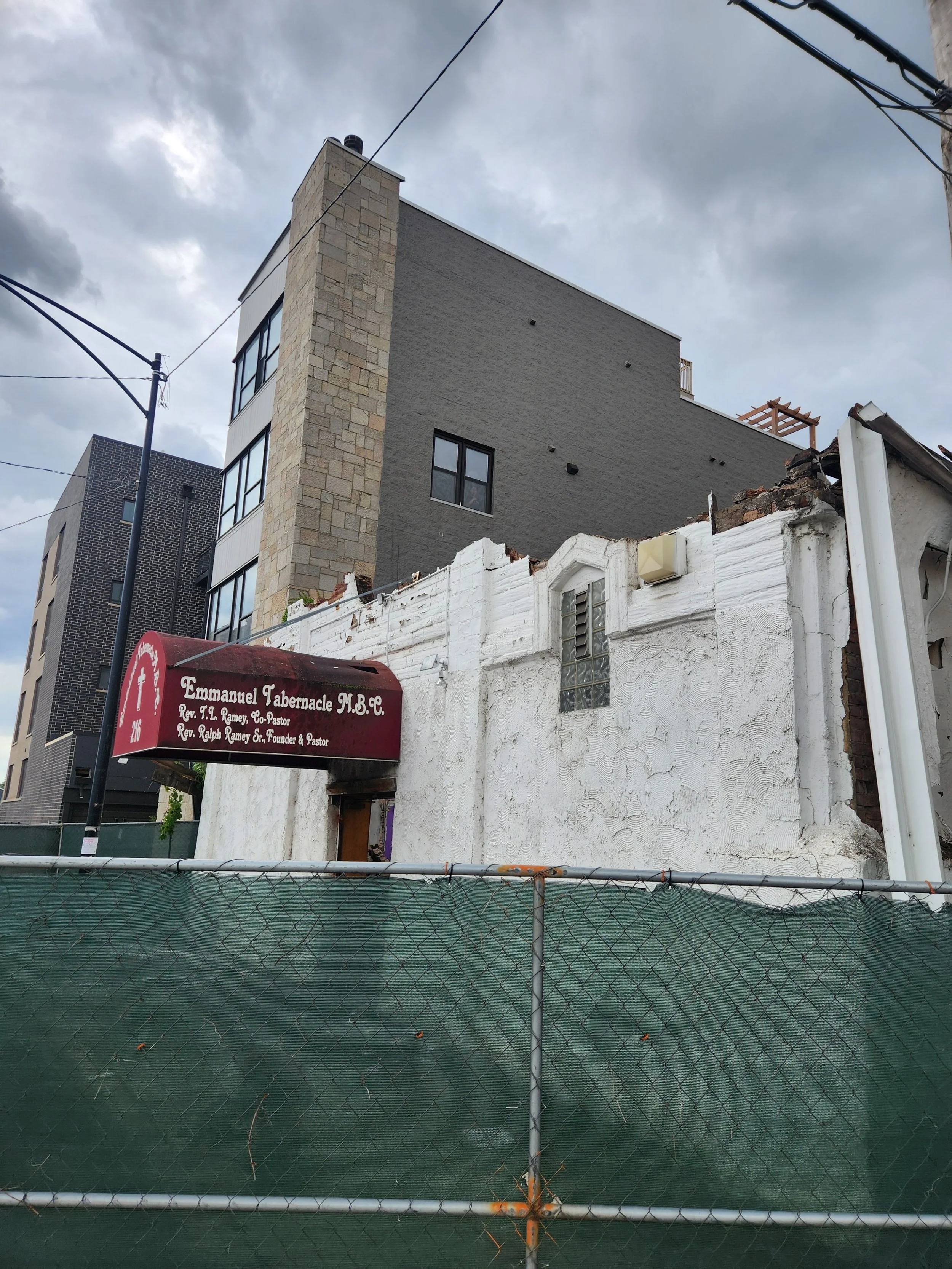
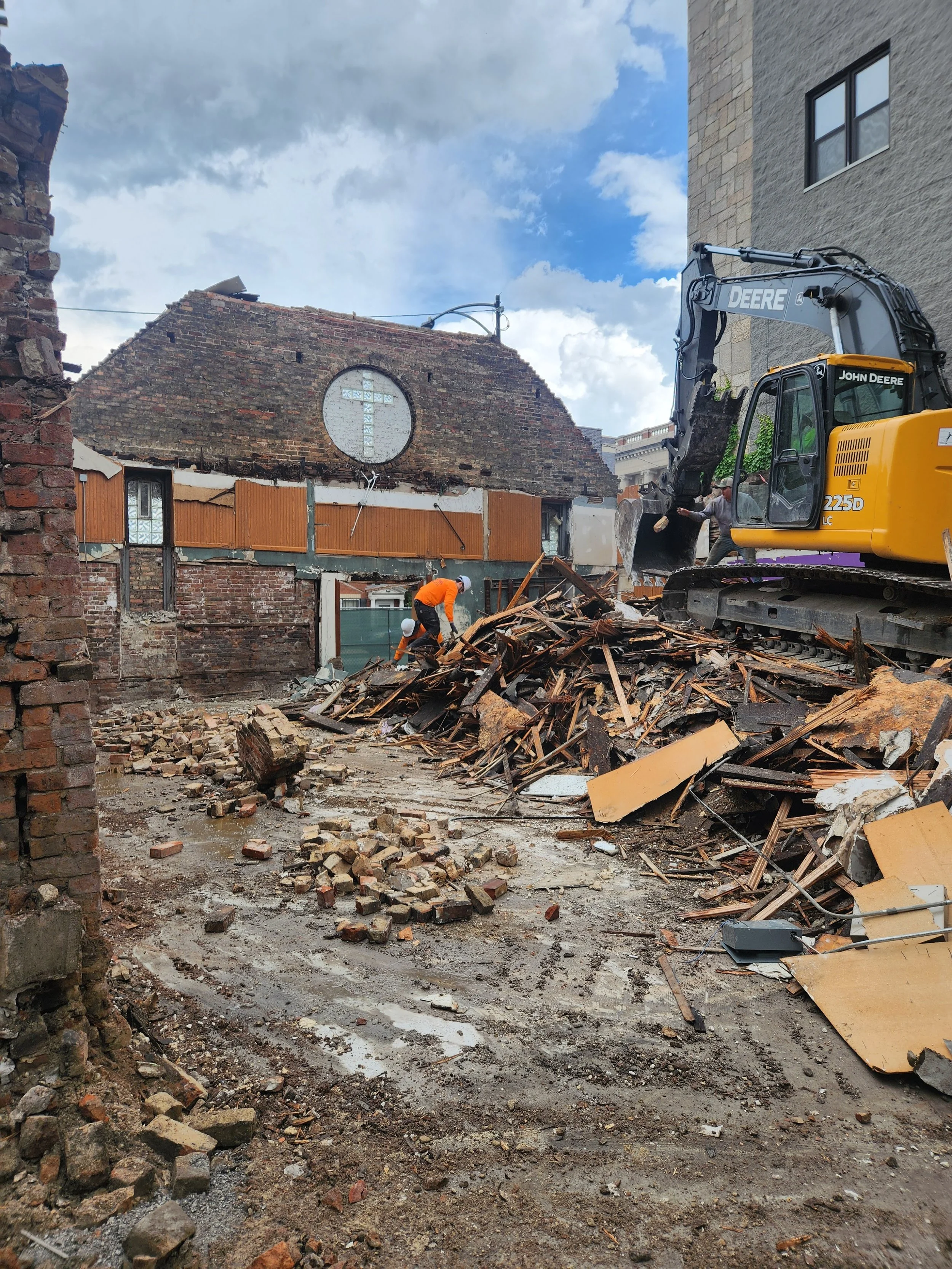